ATOM™ encoders allow rapid, high-accuracy FPD inspection and repair
South Korean flat-panel display (FPD) process equipment manufacturers have held a market-leading position for some time and are the driving force behind many of the recent advances seen in the manufacture of organic light emitting diode (OLED) and active-matrix light emitting diode (AMOLED) displays.
TPC Motion (TPC), a well-known Korean manufacturer of motion-control components, has developed a laser aperture stop (optical slit) assembly that employs Renishaw's miniature ATOM linear encoder system on multiple X and Y axes. The aperture stop offers a compact and precise aperture-control solution for the laser repair of FPD assemblies and metal photomasks.
The FPD manufacturing process involves a number of complex stages that build one patterned layer at a time. Each additional layer to the FPD assembly must pass through inspection to identify any defects likely to impact display quality. Laser irradiation, by a neodymium-doped yttrium aluminium garnet (Nd: YAG) laser or similar, is often used in the repair of a defect, before progression to the next stage in the process.
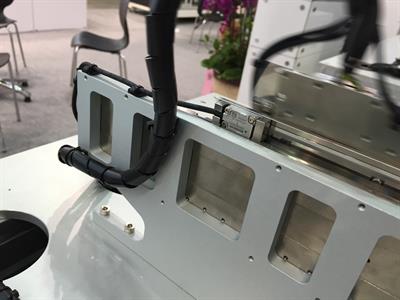
The ATOM series meets all of our main requirements for a high-performance, low-noise and light-weight miniature encoder system. Direct comparison with competing brands has demonstrated beyond doubt that ATOM is indeed best-in-class. Renishaw's delivery lead-times and after-sales support have also proven to be excellent.
TPC Motion (TPC) (South Korea)
Panel defect repair
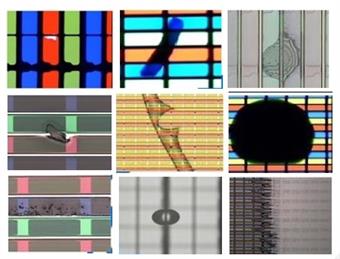
As modern FPD manufacturing techniques become more complex and difficult, panel defects are increasingly likely. Robust inspection and repair procedures have been developed to ensure that errors, where they do occur, have minimal effect on display quality. Processes needing repair operations in liquid crystal display (LCD) manufacturing, for instance, include those involving thin film transistor (TFT) substrates, colour filter (CF) substrates and TFT / CF alignment (cell assembly).
Damage to any one of the millions of transistors within the LCD panel may leave a sub-pixel permanently on or off, creating a tiny dark or bright spot on the display. Broken or shorted TFT data lines are often the cause of bright / black line defects. Repair structures integrated into the TFT layer allow white pixel defects to be turned to ‘black' or ‘dull' by irradiation with a laser. The laser is used in ablation / welding and is focused on the defect to either vaporize it or to create new contacts in the case of TFT repair. The spot-size (diameter) of the laser beam needs to be carefully controlled so as to encompass the defect but leave the normal substrate around it undamaged. Precise manipulation of the laser aperture, in the range of 5 – 50 microns (µm) in diameter, is vital to ensure successful panel repair and improved process yield.
Laser beam shaping
In the FPD repair process, the precise position of the laser beam on a panel substrate is controlled by a scanning mirror, or similar, while the substrate sits on an XY air-bearing stage. The aperture stop lies between the laser source and the intended target. Depending on the application, changes may be made to the laser beam shape, spread (divergence) or even intensity in order to meet process requirements. TPC's variable aperture stop design is novel for FPD repair as objective-lens systems are typical in this application. One advantage of a mechanically adjusted aperture is that laser spot sizes can be precisely controlled to within 1 µm or less, the typical feature size of 10th generation devices, which allows very accurate control of the beam spread.
Mr Hyun-Joo Hwang, director of TPC Motion, explains: “The laser aperture stop consists of four moving vanes arranged in crossed pairs. Each vane is driven by an individual voice coil motor with a maximum travel of only 2 mm.

All four voice coil motors are equipped with an ATOM encoder system for position feedback control. For this application, we selected the ATOM encoder with 50 nm resolution and RTLF tape scale. The accuracy of ATOM allows us to precisely control aperture sizes ranging from 5 x 5 µm to 50 x 50 µm. Before attempting to repair a defect, the aperture size is pre-set and then remains unchanged until the next repair operation."
Miniaturised design
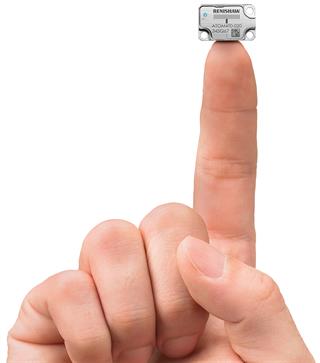
TPC designed its aperture stop assembly to be as compact as possible, in order to fit inside a small imposed footprint. Clearly, consideration of the physical size of the chosen encoder system was essential to meet this criterion.
Mr Hwang continues: “The laser repair tool rapidly tracks back and forth across the panel to the location of every defect, which necessitates a light weight design to maximise throughput. The aperture assembly accommodates four voice coil motors, each with an ATOM encoder, all enclosed within an area of approx. 100 mm square. ATOM's best-in-class feedback performance provides improvements in aperture control, whilst the low mass (<4 g) of the readhead ensures that overall design weight remains uncompromised.”
ATOM's miniature readhead is only 7.3 mm x 20.5 mm x 12.7 mm (FPC cable variant) and is ideal for applications with limited space.
High-repeatability and high-stability
During defect repair with a laser, the size of the laser aperture must be fixed and stable between adjustments by the operator. This requires that the encoder outputs have minimal noise, such that each vane holds its position, without wander, once in place.
TPC requires that aperture stop repeatability be maintained in the ±0.5 µm range, in order to limit unintentional damage to the surrounding substrate.
Mr Hwang concludes: "The ATOM series meets all of our main requirements for a high-performance, low-noise and light weight miniature encoder system. Direct comparison with competing brands has demonstrated beyond doubt that ATOM is indeed best-in-class. Renishaw's delivery lead-times and after-sales support have also proven to be excellent.”
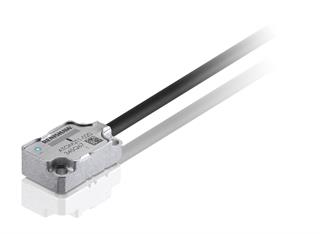
TPC's confidence is reflected by its recent development of a precision miniature linear motion stage which also incorporates the ATOM encoder. Potential applications of this new stage will include: semiconductor, FPD and others characterised by flexible, high-precision and compact production equipment.
About TPC
Tanhay Pneumatic Engineering Company (TPC) was founded in 1973 and is Korea's largest manufacturer of pneumatic equipment. TPC established its motion control division (TPC Motion) in 2009, specializing in the development of motion control-related products; including linear stage motors, servo motors, Cartesian coordinate robots, 3D printers, and other optical components. Customers include those in the semiconductor, FPD and printed circuit board (PCB) industries. In addition to the ATOM series, TPC employs Renishaw's TONiC™ optical encoder series and XL-80 laser interferometer for quality checks.