Diese Seite steht derzeit nicht in Ihrer Sprache zur Verfügung. Mittels der
Übersetzungsfunktion
von Google kann Ihnen eine automatische Übersetzung angezeigt werden. Bitte beachten Sie jedoch, dass wir keinerlei Verantwortung für diese
Dienstleistung tragen und die Übersetzung auch nicht von uns geprüft wurde.
Wenn Sie weitere Unterstützung benötigen,
kontaktieren Sie uns bitte.
Renishaw on high with Airbus A380 Superjumbo
By virtually every measure of comparison, the Airbus A380 Superjumbo is the largest commercial aircraft in the world.
Able to accommodate 555 passengers, and with a wingspan in excess of 260 feet, building the giant double-decker calls for some highly-innovative assembly techniques. One such technique is the use of several wing-panel assembly machines that depend upon Renishaw's RG4 linear encoder systems (not recommended for new designs, alternative upgrade: QUANTiC™ encoders with RKLC40 scales) for positioning accuracy. The four machines incorporate over 1 km of 40 micron scale tape, to determine the precise position of travelling ‘yokes'. These massive four-storey-high, 80 tonne structures straddle each skin panel in order to drill, tap and rivet stringers along the entire span.
Ground-breaking system
Electroimpact Inc, based in the US, has played a significant role in providing Europe's Airbus Industrie with ground-breaking equipment for wing assemblies. These range from the early Airbus A320 family, through to the four-engine A340, and now for the huge A380 wings currently under build.
Since supplying the original machinery to Airbus to mount wing skins onto structural members for the two earlier models, Electroimpact's Airbus work grew until it made up nearly 90% of its 2002 revenue. Electroimpact sourced Renishaw's encoder systems for use with its original A320 equipment and has been happy to stay with Renishaw at each succeeding stage of growth. This is thanks to Renishaw offering proven global support, and the fact that the tape scale used in the RG4 linear encoder system is available in continuous roll form.
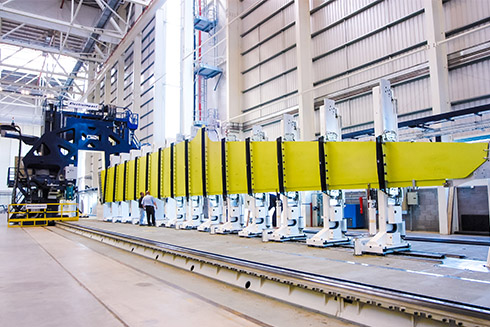
Thousands of holes drilled
Designated LVERs (low voltage electro-magnetic riveters), the huge twin-towered yokes run on beds capable of supporting all 16 of the wing panels involved. Each head must drill thousands of holes and apply all the rivets and bolts as it traverses the stringer/skin combinations, with their support columns. The heads must always be perpendicular to the skin surface and so have to adjust to match any combination of camber, aerofoil contour, dihedral, taper and sweepback, anywhere along the wing.
Fundamental to the process is the complex CNC riveting/drilling head and this in turn depends upon the linear accuracy, span-wise, of the whole yoke structure as it picks up signals from the RG4 linear encoder system.
Electroimpact's president and founder, Peter Zieve, said of the original Renishaw application, “It's absolutely amazing. It gives us a highly repeatable process. The guys here don't even know it's there. We are now designing all our machines with Renishaw linear encoder systems in mind”.
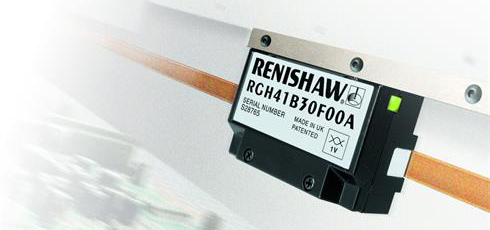
Electroimpact Inc (USA)
Unseen and undemanding
An open, non-contact, optical linear encoder, the RG4 system has a range of compact readheads offering resolutions from 10 micron to 0.1 micron, speeds in excess of 10 metres/second, industry standard outputs, and compatibility with Renishaw's novel ‘RGS40' tape scale. Supplied on a reel, the self-adhesive, flexible scale was simply cut to the length required and fitted in-situ along the full traversing distance of the 160 m-long machine. It is protected against the ingress of dirt, liquids etc and, once installed, is largely unseen and undemanding. The four Electroimpact lines in the initial ‘Stage Zero' wing-panel assembly stations each have one LVER already installed, with second units on each machine in the course of construction, to bring the total number up to eight.
Space, time and labour-saving
The automated fastening cells represent a vast improvement on earlier riveting systems. They offer a 40% space reduction for a start and save an enormous amount of time and labour by eliminating the need to first manually tack components and then split them for deburring, before re-tacking.
Speaking of the new A380 project, Zieve is on record as saying, “They (Airbus) came to us and said, ‘You guys did such a nice job for us making panels, why don't you build the jig for the entire wing?' That took our contract and put it on steroids as it went from big to totally gigantic.”