Tato stránka není v současné době k dispozici ve vašem jazyce. Automatizovaný překlad můžete zobrazit pomocí nástroje Google Translate. Neodpovídáme za poskytování této služby a výsledky překladu jsme nekontrolovali.
Potřebujete-li další pomoc, kontaktujte nás.
Taking precision to new heights - air bearing stages with Renishaw optical encoders
Background
Air bearings are a widely used technology in precision equipment across various high-end industries, such as semiconductor, photovoltaics and precision machining.
By using air or other gases as a lubricant to support non-contact surfaces through an air cushion, these bearings enable the slider to move in a floating state within motion stages. When combined with linear motors and optical encoders, these stages achieve outstanding levels of performance.
In this regard, TOYO Nano System Corporation is at the forefront of innovation, having developed motion stages that utilise a coplanar patented mechanism design and Renishaw's high-precision optical encoders as the position feedback system. Their advanced solutions provide micro and nano-level motion stage capabilities while maximising cost-effectiveness for the industry.
Air bearing principles and advantages
Air bearings in the market can generally be divided into two types: static pressure and dynamic pressure. Static pressure air bearings are commonly used in motion stages. The working principle is to inject compressed air (or other gases such as nitrogen, argon, or carbon dioxide) from the outside. The air passes through a throttle and enters the air gap between the slider bottom and the guide rails of the granite base.
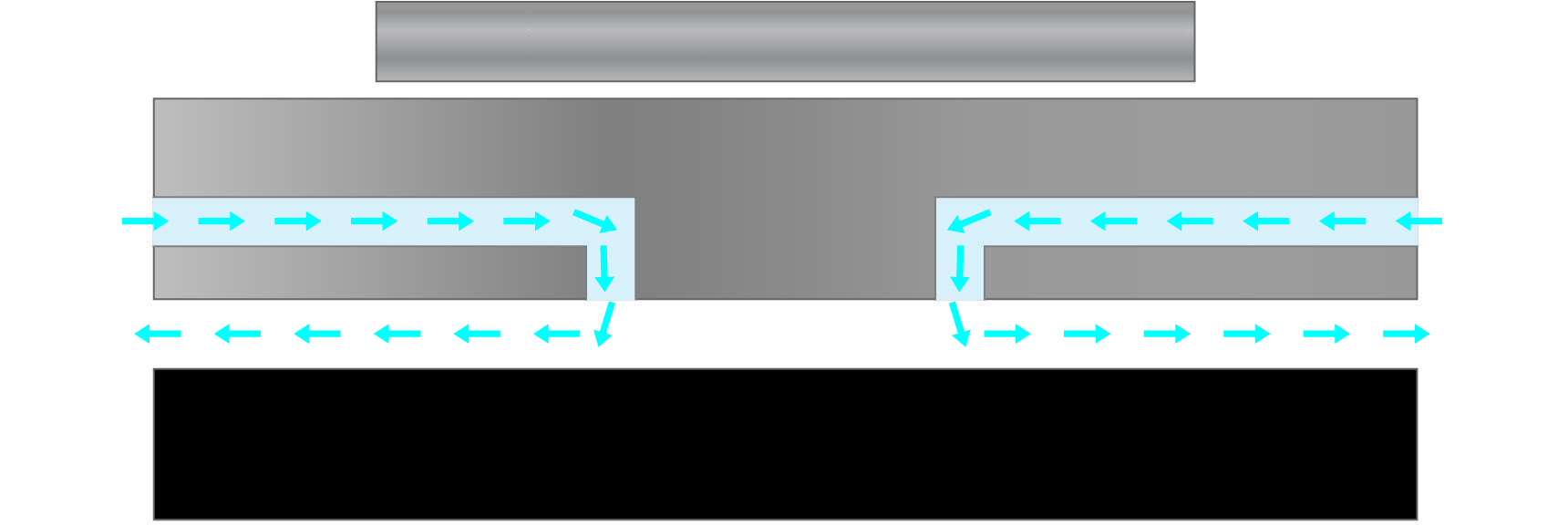
Structure of TOYO's air bearing stage
A static pressure air film is formed in the gap that supports the load and suspends the slider over the guide rails. The thickness of the air film (working air gap) depends on the stage design and the surface finish accuracy of the motion pair, generally around 5 to 10 µm.
Challenge
Application of Renishaw optical encoders in TOYO's air bearing motion stages
The throttle is a crucial component in air bearings. When the load increases, the air film is compressed, affecting rigidity. In response to load changes that maintain air film thickness and bearing stiffness, the throttle adjusts the flow rate and flow velocity of compressed air into the gap.
The load capacity and performance characteristics of an air bearing are closely related to the throttle technology adopted, and each manufacturer develops its own throttle technology to optimise performance.
According to Mr. Deng Gui Dun, Vice President of TOYO, the throttle component designed by TOYO is directly embedded in the granite structure inside the air bearing stage, which is structurally simpler, easy to assemble, has high rigidity and good load-carrying capacity, unlike the typical air bearing stages that have an external throttle body.
TOYO's air bearing stages offer a repeatability of 0.3 μm (per 300 mm stroke), providing high accuracy in six degrees of freedom. The XY stage adopts a co-planar structure design, sharing the same reference plane, to solve the problem of error accumulation caused by designs that stack the X and Y axes in the horizontal and vertical planes.
The acceleration of some stage models can reach up to 10 g which is sufficient to meet most high-end application requirements, including semiconductor, flat panel display, PCB, laser exposure and automated optical inspection (AOI) equipment— with AOI applications accounting for the largest proportion. Since AOI needs to scan and image the object under inspection, it requires stable velocity control.
Solution
Benefitting from the almost zero friction of its air bearings, the motion stage can make very small displacements. The air film in the air bearing motion platform has an averaging effect on the surface error of the stage base, slider, and other components, leading to better flatness and straightness, and enabling excellent speed stability.
However, precise position feedback still relies on optical encoders. Taking one of TOYO's high-performance air bearing gantry stages as an example, it uses RESOLUTE™ absolute optical encoders with RELA ZeroMet™ low expansion scales.
The stage's repeatability is better than 1 μm, the crossbeam's yaw angle is less than 3 arc seconds, the maximum speed is up to 1 m/s, and the X and Y axis travels are 350 mm and 1200 mm, respectively.
The RESOLUTE encoder features 50 nm resolution and is connected to the controller via the BiSS C communication protocol. This stage has low velocity ripple, making it suitable for applications that require high-speed and stable movement, such as PCB printing or direct imaging (DI) exposure machines.
Mr. Deng said, “Renishaw's optical encoder products are very diverse, including the RESOLUTE absolute encoder series, as well as VIONiC™, QUANTiC™ and ATOM™ incremental optical encoder series, which are applied to TOYO's air bearing gantry stages of different specifications.
In fact, different industries have different specifications for motion platform positioning systems, and Renishaw can provide corresponding optical encoder products in the vast majority of cases. Since using Renishaw optical encoders, we have not received any reports of encoder failures from customers, so the reliability of their optical encoders is good.”
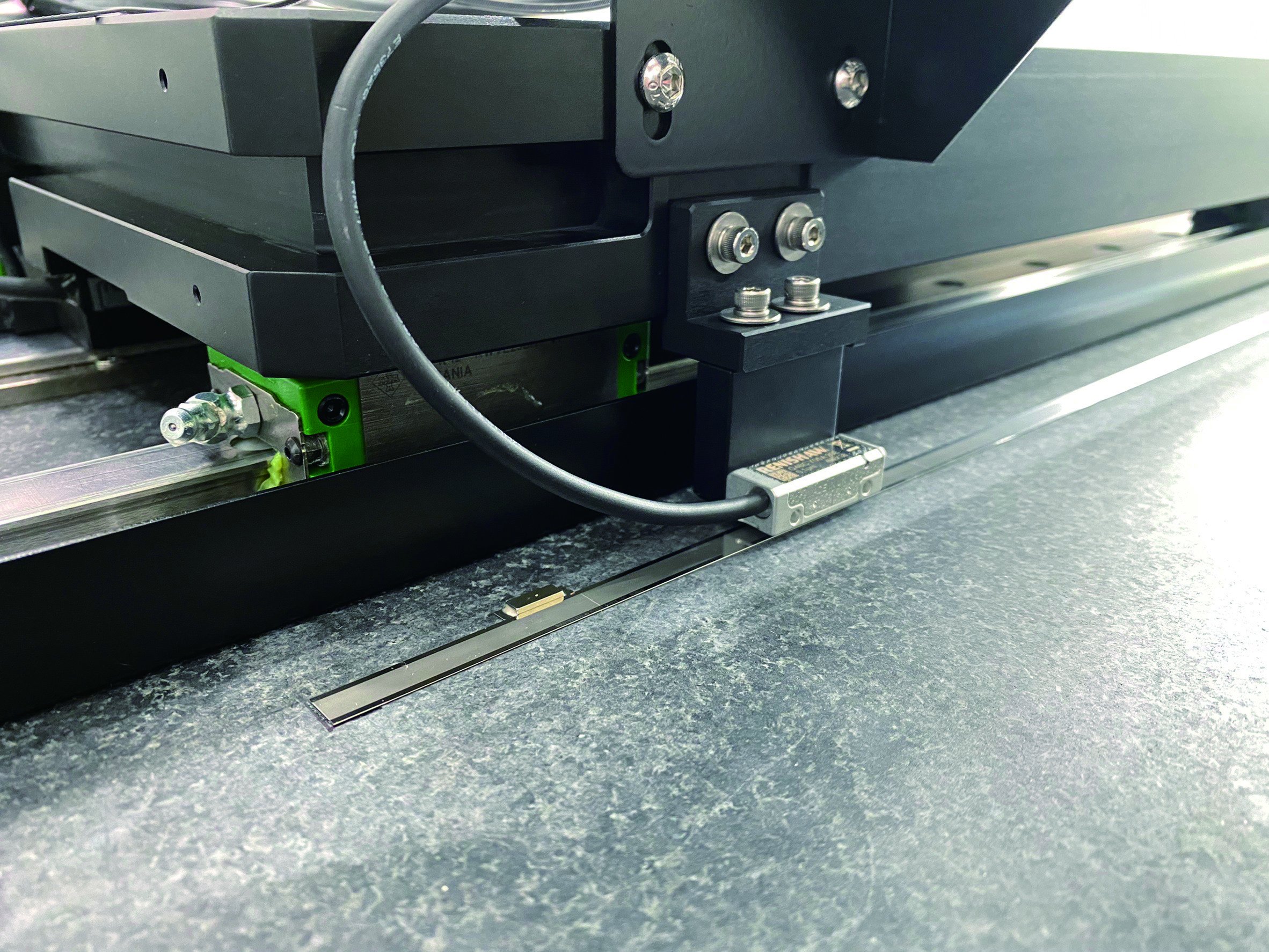
How do optical encoders affect the performance of air bearing gantry stages?
Air bearings have many advantages, including sealing from dust, low noise and non-contact characteristics which enables higher platform accelerations.
However, high-precision optical encoders are required to create high-performance motion platforms. When selecting optical encoders, a range of environmental and application requirements need to be considered, such as temperature, Sub-Divisional Error and jitter.
Temperature – temperature changes can cause thermal expansion and contraction of the optical encoder scale, affecting its accuracy, especially when micron or even nanometre-level positioning accuracy is required. Therefore, air bearing stages mostly use materials that are not sensitive to temperature changes, such as granite substrates and Invar® scales with a thermal expansion coefficient close to zero.
Sub-Divisional Error (SDE) – Sub-Divisional Error directly affects the smoothness of the axis motion, and low SDE also reduces velocity ripple. AOI inspection and printing applications, for example, require low SDE. Renishaw RESOLUTE and VIONiC encoders have SDE values less than 30 nm and 10 nm respectively, which can meet most requirements.
Jitter – all encoders have inherent uncertainties associated with internal electronics and jitter is the measure of this uncertainty which is seen as positional noise output by the encoder when it is not moving. This can contribute to motion stability of the stage when trying to hold a fixed position. The jitter of VIONiC encoders is only 1.6 nm RMS, making it suitable for applications where position stability is critical.
Collaboration with Renishaw
TOYO's air bearing motion stages are mainly targeted at the high-end production market, with major sales regions including Taiwan, China, Korea, Japan, USA, and South-east Asia.
TOYO's product line includes electric cylinders, linear motor modules and servo drives, among other products. Over 95% of the linear motor products use Renishaw QUANTiC series optical encoders, which provide 1 μm, 0.1 μm and 0.5 μm resolution, with travel ranges from 80 mm to 8 metres and thrusts from 30 N to 1000 N.
Rather than perform quality control through sampling, TOYO adopts a full inspection approach. Each motion platform undergoes testing and calibration with Renishaw's XL-80 laser interferometer before leaving the factory, and a report is generated for the customer. Some large platforms will undergo additional calibration with the XL-80 laser system after arriving at the customer's site to ensure accuracy.
TOYO first became acquainted with Renishaw after using its iconic CMM measuring probe products, and later became a customer of Renishaw's optical encoders and laser interferometers. Renishaw was chosen for the excellent reputation of its products, their ease of installation, product quality, and outstanding technical support.
Results
Mr Deng summarised, “Renishaw's laser interferometer is highly regarded in the industry, and the test reports give confidence to customers. As we produce a large quantity of stages, we have purchased five XL-80 laser interferometers, which are being used continuously every day. In addition, we have also seen a demonstration of Renishaw's XM-60 multi-axis calibrator system, which can greatly improve the testing efficiency of motion stages, especially for precision stages that require calibration in all six degrees of freedom. In the future, TOYO will invest more resources in the development of new products, including standard air bearing modules and direct drive rotary motors using air bearings, to meet the development needs of emerging technologies such as microLED displays.”
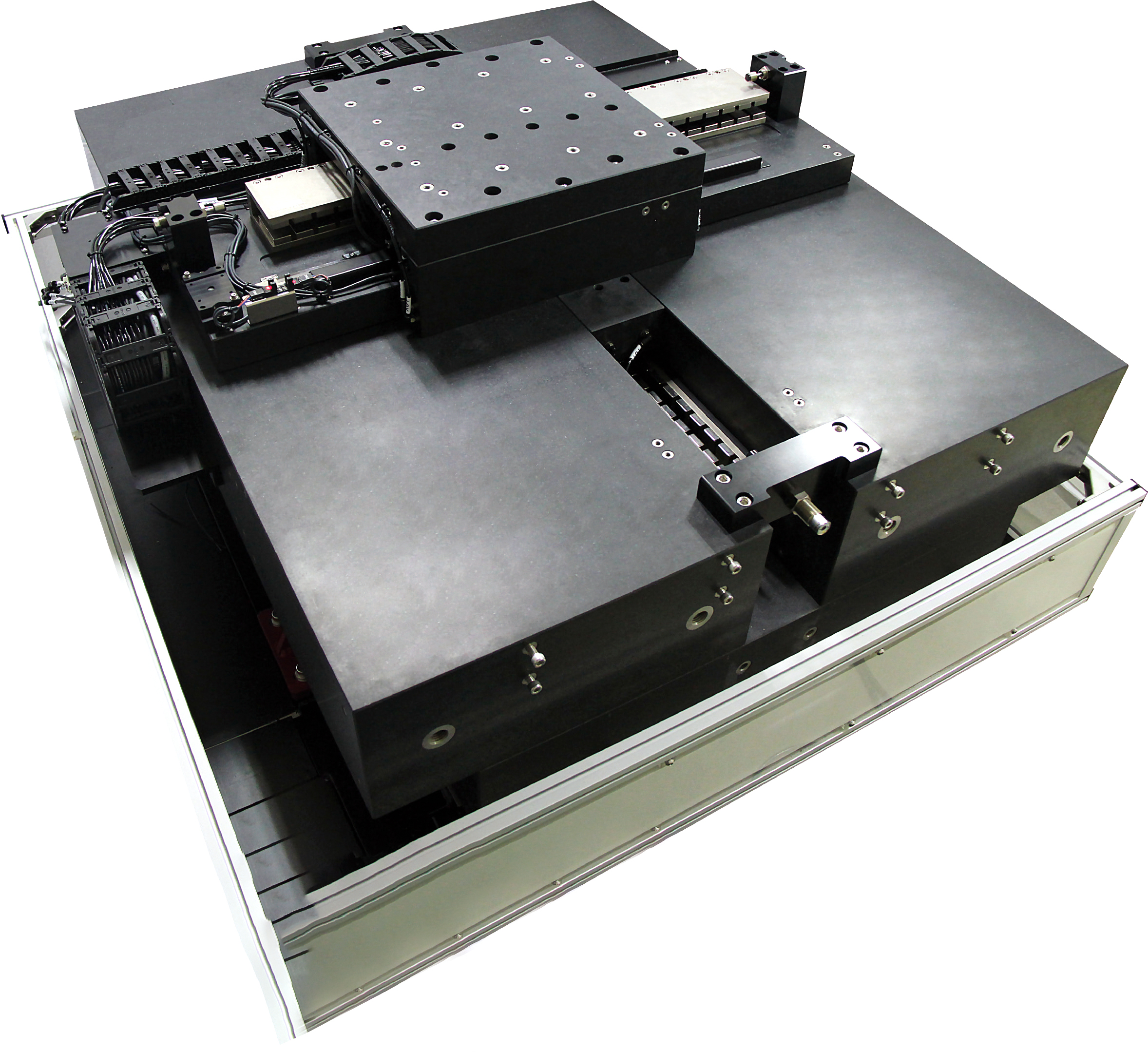
Linear XY air bearing stage