Scodix chooses TONiC™ encoders for its Ultra™ series of digital enhancement printing presses
Background
Scodix Ultra™ digital presses are the most productive in the series and enable commercial printers and converters to produce tangible enhancements for a wide variety of applications, such as marketing literature, stationery items, book covers, boxes, premium packages and greeting cards. On-demand printing capabilities ensure a high-degree of flexibility for the end-user. These presses meet the exacting requirements of an ever more demanding industry and provide new levels of speed, quality, and efficiency. Ultra series capabilities include elevated features as high as 250 microns, high gloss printing to 99 Gloss Units (GU), hot foil stamping and embossing. Patented technologies include overprinting systems and unique foil processes such as PAS™ (Pin Activate Secure).
A key feature of the Scodix Ultra digital press is the wide range of compatible substrates from paper and cardboard to PVC and laminates. This requires a novel type of conveyor system capable of precise positioning control. Scodix's RSP™ (Rotate Scale Position) technology combines very precise positioning of a substrate under four CCD cameras with sophisticated algorithms for optimal image-to-image registration. Renishaw's TONiC optical incremental encoder system was chosen by Scodix for the machine's linear feed (X) axis after in-house testing proved the suitability of TONiC for this demanding motion control application.
After reviewing several alternatives, we found the TONiC optical linear encoder to answer our needs. The main decision factors were accuracy, repeatability and quality.
Scodix (Israel)
Challenge
The Scodix Ultra series comprises several different stages including: a substrate loading stage, an alignment stage, a print stage and an unloading stage. Rather than using a traditional belt conveyor, the Scodix system employs a pair of rigid platforms (platens) that operate continuously. Each platen is mounted side-by-side and moves both vertically and horizontally. Accurate determination of both the position of the substrate on the platen and the platen itself is essential for high quality printing. Any misalignment between the substrate and printhead needs to be compensated. In this case, registration markers on each corner of the substrate are captured by CCD cameras and used to determine compensation adjustments to correct for positional offsets. Four movable CCD cameras are fixed over each of the four corners of the substrate. Once the corners are recognized and based upon a predetermined ideal orientation programmed into the machine by the operator, the system calculates and stores any misalignments (offsets) and transmits this information to the printing and curing modules. Offsets are then directly applied to the digital image files to fully compensate for errors. Corrections may be for linear shift (X-Y axes), angular shift, size shift or any combination thereof.
The position of each of the platens needs to be known at all times because the position of each carrier affects the timing of the loading of the substrate, the position and speed of the substrate in the print module and the timing of the curing and unloading operations.
Fixed printheads eliminate the scan motion across the substrate and allow single pass printing. However, to avoid error in the printing process and ensure precise, high-quality, image reproduction it is essential that the position and speed of the platen be measured system outputs. This requires high-performance linear encoders on the platen transportation system for the provision of high-gain feedback control.
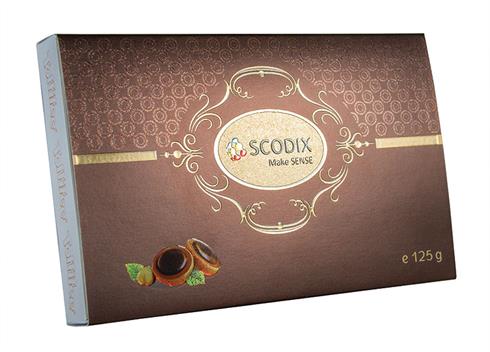
Scodix chocolate box example - the label text has been printed in relief inside an embossed gold background pattern
Solution
The challenge was to find a high precision, high signal-stability encoder capable of meeting the diverse and demanding requirements of printing machines; to have immunity to possible contaminants such as grease, dust particles and scratches and to run reliably with minimal maintenance. Scodix chose a 5 nm resolution TONiC readhead with a self-adhesive scale for each individual platen, mounted on both sides of the machine and thermally mastered to the substrate with end-clamps. This scale is ideal for the printing industry, offering increased corrosion resistance and ease of cleaning. LM10 linear magnetic encoders with MS10 scales, from RLS (a Renishaw associate company), are also employed on the machine's Y-axis to enable some degree of lateral alignment control of each platen.
Gur Shapira, R & D project manager at Scodix Ltd, explains: “After reviewing several alternatives, we found the TONiC optical linear encoder to answer our needs. The main decision factors were accuracy, repeatability and quality. We conducted accuracy tests using a profilometer and comparator to ensure that the system performance was within spec. The TONiC encoder was shown to have excellent metrology performance. Every stage of the testing and integration of the Scodix Ultra was done in cooperation and collaboration with Renishaw's local technical support team.”
Mr Shapira concludes: “We see Renishaw as an invaluable strategic supplier to Scodix, ensuring product quality and reliability to the benefit of our customers.”
Results
Renishaw's TONiC encoder has provided Scodix with an off-the-shelf solution to enable automatic feedback control of the Scodix Ultra series' patented substrate transportation system. The leading-edge performance of the TONiC encoder range, combined with Renishaw's excellent worldwide technical support, has allowed Scodix to create truly ground-breaking technology. Renishaw and Scodix share a successful, high-value, collaboration that fosters innovation across both companies.
About Scodix Ltd
Scodix Ltd, headquarted in Rosh Ha'ayin, Israel, is a leading provider of digital print enhancement presses for the graphic arts industry, offering print service providers (PSPs) and folding-carton converters the ability to add value to the products they provide to their customers. The company's digital enhancement presses with Scodix SENSE™ technology offer high-quality enhancement capabilities designed to increase the impact of graphic-communications content.
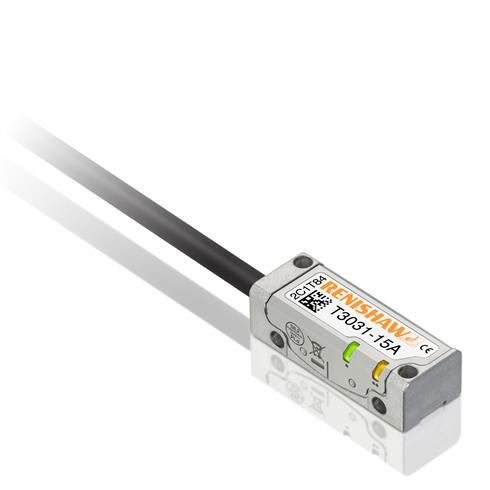
Renishaw would like to thank the R & D project manager of Scodix Ltd, Gur Shapira, for his contribution.