Stran trenutno ni na voljo v vašem jeziku. Lahko si ogledate strojni prevod, ustvarjen s storitvijo Google Translate. Te storitve ne zagotavljamo mi in rezultatov prevoda nismo preverili.
Za dodatno pomoč se lahko obrnete na nas.
ASTRiA™ inductive rotary absolute encoders
Fast, efficient, robust inductive encoder
The ASTRiA inductive rotary absolute encoder achieves an impressive total system accuracy of ±40 arc seconds and 23 bit resolution (for a Ø100 mm size), which is made possible by using a multi-track scale, robust mechanical design and advanced signal processing.
Other encoder features include:
- Built-in alignment flexures to ensure hassle-free installation. Whether for the initial setup or subsequent mounting operations, the ASTRiA encoder self-centres the rotor — significantly reducing installation time and effort.
- State-of-the-art electronics optimised for low current consumption. By minimising energy usage, customers benefit from reduced system running costs and an overall low cost of ownership.
- Carefully designed mechanical features on both the rotor and stator that enhance stability across a wide range of operating speeds and temperatures. Thermal expansion and high speeds do not compromise system operation.
- Standard RS485 serial communication, offering the BiSS® C (unidirectional) open serial interface. Baud rate of up to 10 MHz and request rates up to 32 kHz cater for even the most demanding customer applications.
ASTRiA encoders thrive in demanding environments. Their electromagnetic induction technology detects absolute angular position without requiring direct line-of-sight between the stator and rotor. Contaminants like dirt and oils are invisible to the position detector.
Furthermore, eccentricity errors during installation are significantly minimised. The built-in alignment flexures ensure low eccentricity of the rotor mounting, and the encoder measures position information over the full 360 degrees of the scale which further minimises measurement errors.
Watch our introduction to ASTRiA™ inductive rotary absolute encoders
Key benefits
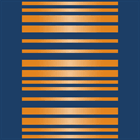
System accuracy
ASTRiA encoders offer excellent system accuracy due to advanced signal processing and self-centring mounting flexures on the rotor.
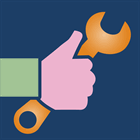
Easy installation
The encoder features a self-centring rotor that reduces installation time and effort whilst maintaining excellent installed accuracy. No calibration is required.
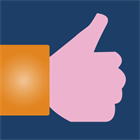
Robust position measurement
Mechanical features on the rotor and stator give the encoder excellent mechanical stability across a wide range of operating speeds and temperatures.
What is an inductive encoder?
An inductive absolute encoder is a type of position sensor that uses electromagnetic induction to measure the position or motion of an axis. Applications include gimbals, medical devices, general automation, unmanned aerial vehicles (UAVs), robots and servo motors.
There are two main parts to an inductive rotary encoder: the stator (stationary part) and rotor (moving part). Each is constructed as a PCB with circular conductive coils and circular arrays of conductive segments called scale tracks.
The stator features a circular excitation coil and several receiving coils. The rotor is unpowered (passive) and features two or more scale tracks.
1. Excitation coil
2. Incremental coils
3. Vernier 1 coils
4. Vernier 2 coils
5. Incremental track
6. Vernier 1 track
7. Vernier 2 track
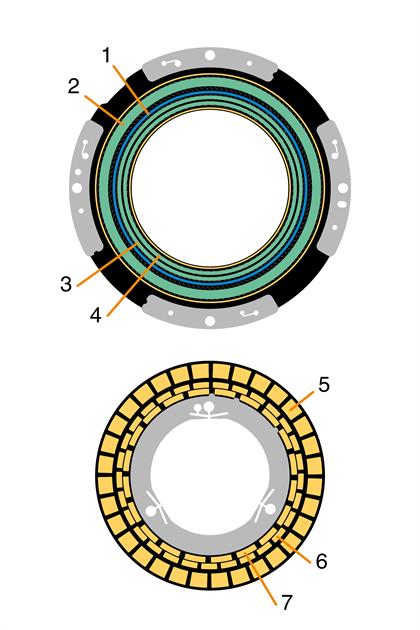
How an inductive encoder works
1. Electromagnetic field generation
- A fixed frequency carrier sine wave is sent through the excitation coil, which generates an alternating electromagnetic field.
- This induces eddy currents on the surface of the segments in the scale tracks of the rotor.
2. Sensing position
- The eddy currents generate an electromagnetic field, which is picked up as sine and cosine amplitude-modulated waveform voltages in the receiver coils on the stator, with period matching the features on the scale tracks.
- The ratios between the three sine and cosine signals are unique for each angle of rotation, allowing a single segment of the outer incremental scale track to be identified.
3. Signal processing
- All scale track signals are optimised using advanced signal processing technology to achieve very high signal purity.
- The incremental track signal is then interpolated and combined with the segment position to determine the absolute rotary position to a resolution of 23 bits per revolution.
4. Output
- This absolute position is checked against a continual count of the rotation of the incremental scale segments, which helps to ensure that the controller receives dependable position feedback.
- The position can be output at up to 32,000 times per second, using the BiSS® C serial communications interface with a baud rate up to 10 MHz.
Renishaw's ASTRiA inductive encoders are fit-and-forget solutions that provide accurate and robust position measurements in demanding operating environments.
Resistance to contamination
ASTRiA encoders make use of electromagnetic induction to detect the absolute angular position of the scale rotor by sensing a peripheral copper incremental track and two concentric vernier tracks on the rotor. Unlike optical encoders which require a clear line-of-sight between stator and rotor, this sensing technology is highly immune to contamination such as dirt and oils.
Easy installation
The ASTRiA encoder minimises installation error with built-in alignment flexures that self-centre the rotor. These features significantly reduce installation time and effort, without sacrificing excellent installed accuracy. No calibration is required.
What makes Renishaw inductive encoders reliable and dependable?
Every ASTRiA encoder is built to last. We subject our inductive encoders to rigorous tests that exceed normal operating conditions. For instance, the ASTRiA encoder undergoes humidity testing, temperature testing, speed tests up to 9,000 rpm, maximum acceleration tests up to 500 m/s2, shock tests and vibration tests. During the assembly process, every ASTRiA encoder has a comprehensive final check to guarantee reliability.
Signal processing
ASTRiA encoders feature dynamic signal conditioning including Auto Balance Control (ABC), Auto Offset Control (AOC) and Auto Phase Control (APC) for enhanced Sub-Divisional Error (SDE) performance even when the encoder is misaligned.
Durable materials
ASTRiA encoders are built from robust FR4 composite combined with stainless steel mounting points and can withstand 30 g shocks during operation, ensuring resilience and longevity. This makes them suitable for demanding applications in harsh environments where reliability is critical.
Increased noise immunity
The ASTRiA encoder series comfortably exceeds the noise immunity requirements for CE certification, which helps prevent errors under harsh radio frequency interference (RFI) conditions.
Contamination immunity
These encoders thrive in demanding environments. Their electromagnetic induction technology detects absolute angular position without requiring direct line-of-sight between the stator and rotor. Contaminants like dirt and oils are invisible to the detector which ensures accurate performance even in harsh conditions.
ISO 9001 Quality Management System
All key manufacturing stages, from PCB assembly to final testing, are conducted in-house. This allows us to maintain strict quality control at every step, ensuring that each ASTRiA encoder meets our high standards.
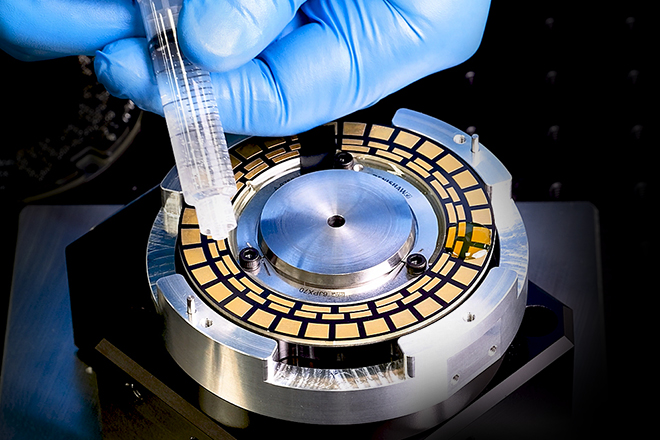
Comprehensive warranty
In the unlikely event of a failure, Renishaw offers full support through a global network of wholly owned sales offices. Technical support teams can help with in-field fault finding, potentially saving time, and reducing installation and maintenance costs. If an ASTRiA encoder needs replacing, Renishaw will send a replacement immediately, then investigate the failure and send you a comprehensive report into exactly what happened, why it happened and what has been done to prevent recurrence.
Discover our range of open and enclosed optical, magnetic and laser encoders designed to meet your industrial automation needs.