Stran trenutno ni na voljo v vašem jeziku. Lahko si ogledate strojni prevod, ustvarjen s storitvijo Google Translate. Te storitve ne zagotavljamo mi in rezultatov prevoda nismo preverili.
Za dodatno pomoč se lahko obrnete na nas.
Additive manufacturing for serial production of orthopaedic implants
Croom Precision Medical has chosen Renishaw as their additive manufacturing (AM) and metrology partner, utilising Renishaw technology throughout the production and validation of their ISO13485 certified medical devices.
The company has found that using Renishaw's AM technology allows them to incorporate complex features into their implant design at a commercially viable cost. They also report that Renishaw's built-in AM software, used in combination with Renishaw's metrology solutions, allows them to maintain traceability throughout their manufacturing process, which is essential in a heavily regulated environment.
Orthopaedic implants
Background
Croom Precision Medical (CPM) sits at the heart of Ireland's thriving medical device industry. Founded in 1984, CPM has been supplying Class I, II and III medical devices to the orthopaedic market for over 35 years. Because these devices will ultimately end up impacting people's lives, it is essential that rigorous quality procedures are applied to help achieve safety and effectiveness of the device, both during and following implantation.
“We want to achieve consistency and reliability in the products that we make. CPM has a vision of becoming a centre of excellence for additive manufacturing in Ireland”, explains Patrick Byrnes, Research and Development Manager at CPM.
CPM operates an Integrated Management System (IMS) which encompasses ISO 9001, ISO 13485 and ISO 14001 accreditation. In order to demonstrate compliance with the standards, CPM must maintain transparency and traceability at each stage of the manufacturing process.
We've managed to gain a new market share in international markets, in East Asia and North America, that were not feasible for us before. It's only the last two years that these markets have opened. We chose Renishaw as a development partner, not just as a product, whereby we see the next few years being a strategic partnership with Renishaw in growing our additive manufacturing base here in Ireland.
Croom Precision Medical (Ireland)
Challenge
Medical implant designs are advancing rapidly. Manufacturers are increasingly incorporating novel and complex structures into implant designs, with the aim of improving implant performance and longevity. Making such structures with traditional manufacturing techniques can be challenging and is not always economically feasible.
In order to assess the quality of parts, CPM carries out a series of offline tests to check the chemical, mechanical and morphological properties of the implant. Whilst these tests are essential to measure mechanical and chemical consistency of the implants, they can be time consuming and add to the overall cost per part. CPM's ambition is to transform their production so that it sees more of the monitoring taking place during the manufacturing process.
“We're looking for a red light or a green light, whether the part is good or bad. At the moment there's a lot of offline testing that we do, and we want to get away from that in order to reduce our cost of goods. We've done a lot of work on that over the last couple of years, there's still a bit to go, but we feel that we're ahead of some of our competitors in the area of in-process monitoring”, explained Byrnes.
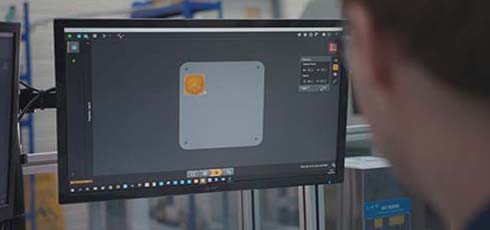
3D print file generated using QuantAM build preparation software
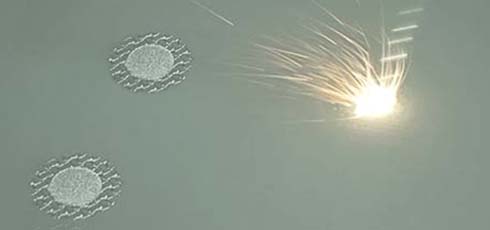
Acetabular cup build in progress on RenAM 500M AM system
Solution
Born out of the aerospace sector, Renishaw has a proven track record of supplying solutions to help achieve manufacturing efficiency and part safety in highly regulated environments. CPM are applying Renishaw's technology to the same end in the medical sector.
CPM has invested in a RenAM 500M additive manufacturing system, which they use to 3D print medical devices in titanium. Renishaw's AM technology can produce complex structures in one manufacturing operation. As an example, CPM has begun assessing the use of gyroid lattices on acetabular cups, a design feature which would not have been economically feasible to produce before their investment in AM. The resulting implants have stood up to rigorous quality testing, and CPM report notably good density and Young's modulus values.
In addition to the advanced manufacturing capabilities of AM, according to Byrnes it is the inline process monitoring that really sets Renishaw's technology apart and gives CPM a competitive edge:
“The Renishaw software provides us with all the necessary information to stand over the quality of our parts, from build reports to post-processing, so we can have traceability of our parts from start to finish.”
To promote quality and consistency in their parts, CPM has also chosen Renishaw as their partner in precision metrology equipment, employing Renishaw's technology at various stages in their testing and part validation. The team had long been familiar with Renishaw's reputation for producing reliable, robust metrology equipment: “When you go around to the multinational companies, and you see all the Renishaw products on the shop floor, they have a name for being repeatable and reliable and well able to operate in harsh environments consistently”, commented Byrnes. CPM exemplifies how Renishaw can supply an end-to-end solution, with technology to aid the manufacturing of technically ambitious parts as well as the quality verification.
Results
CPM report an increased market share, which they directly attribute to their investment in AM technology. “We've managed to gain a new market share in international markets, in East Asia and North America, that were not feasible for us before. It's only the last two years that these markets have opened. We chose Renishaw as a development partner, not just as a product, whereby we see the next few years being a strategic partnership with Renishaw in growing our additive manufacturing base here in Ireland.”
Healthcare is one of the industries at the forefront of AM development. Whilst a lot of progress has already taken place, there's still room to grow. CPM sees Renishaw as a strategic partner in driving the advances in AM technology. Byrnes adds: “Approaching AM for us has been a journey, it's a completely different way of thinking. It's much more of a laboratory environment, more of a cognitive way of approaching a process, rather than conventional engineering.”
Over the next few years, CPM will continue to apply the knowledge they have gained from their rigorous development programs, as well as work closely with customers and regulatory bodies, to carry additive manufacturing technology forward and support advances in healthcare.