No momento esta página não está disponível em seu idioma. Você pode ver uma tradução automatizada utilizando o Google Translate. Não somos responsáveis pelo fornecimento deste serviço e não podemos verificar os resultados.
Se você necessitar mais ajuda fale conosco.
A Swift transition to digital dentistry
The Artemision Bronze is an ancient Greek sculpture that was recovered from the sea off Cape Artemision. It represents either Zeus or Poseidon and is slightly over life-size. Despite the uncertainty about what the statue represents, it is known that it was made using a process called lost-wax casting.
The process of lost-wax casting is still used today and hasn't changed much since ancient Greece. Commonly used in jewellery making, it is also a common manufacturing method in dentistry.
Albeit a time-honoured process, Swift Dental Group recently sourced a more accurate and efficient manufacturing method to use at its facility in Bolton, UK with the help of global engineering and scientific technologies company, Renishaw.
Background
Established in 1984 by Roy McGillivary and Mark Stevenson, Swift Dental Group started out as a small, family run business. Over the last 30 years, the company has become the UK's leading dental laboratories with an onsite teaching and training facility, fully equipped dental surgery and seminar and conference facility.
Swift manufactures implants, crowns and bridges, prosthetics, chrome work and orthodontics, all of which are based on patient impressions taken at dental surgeries across the UK. Before working with Renishaw, Swift used lost-wax casting to create its metal frameworks.
As Swift's volume of work increased, the company started to consider the potential of digital design and manufacturing to increase production efficiency without the loss of accuracy. Business development manager, Paul Perkins was tasked with investigating potential manufacturing solutions.
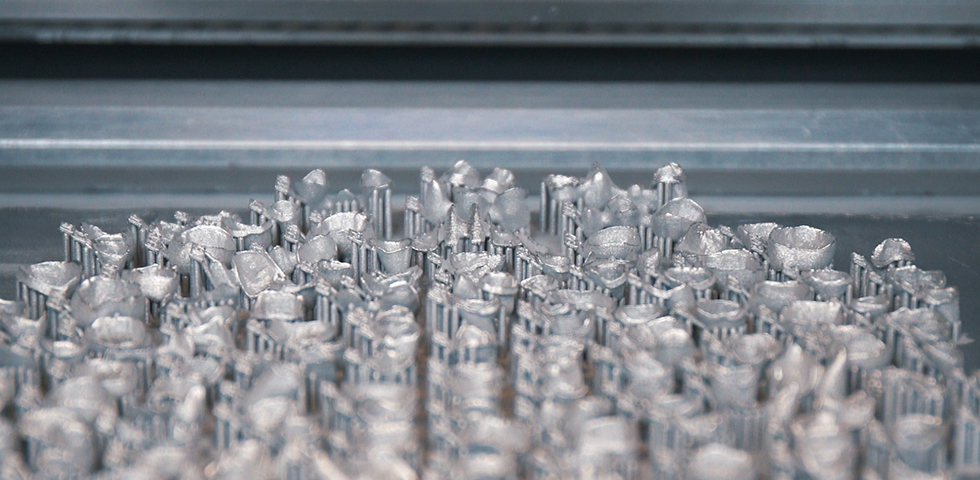
"Before meeting Renishaw, Swift began working with a German company to try and develop a digital manufacturing process that was completely new to the dental industry. We sent designs and prototypes back and forth, but soon realised that we needed to take a different approach."
Swift Dental Group (UK)
Challenges
Naturally, castings need to be extremely accurate in the dental industry — the tolerance limits of a dental casting are approximately half the thickness of a human hair. Achieving this level of accuracy with lost-wax casting can be difficult and often frameworks need rework after being sent to the dentist and fitted to the patient.
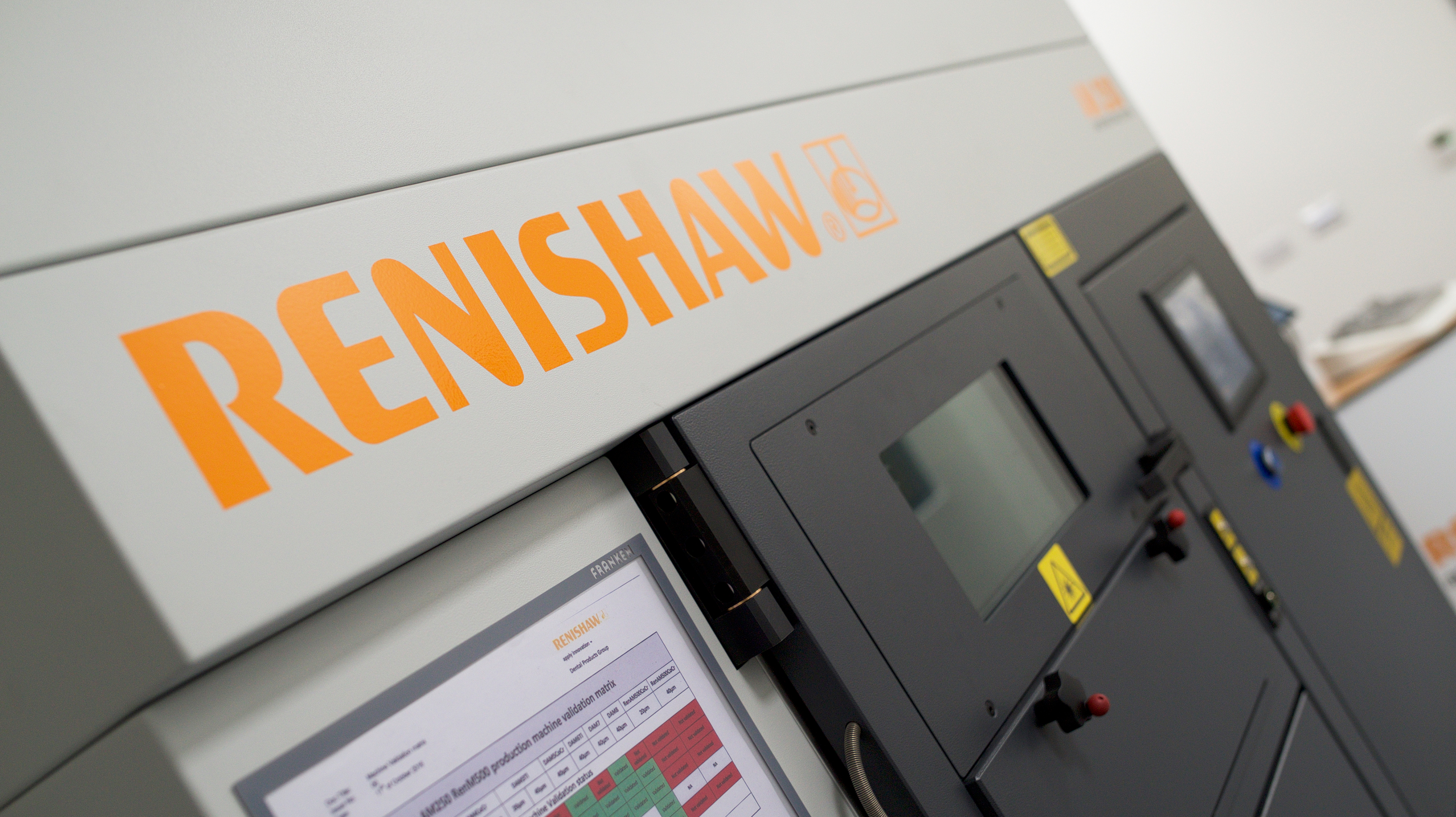

Solution
A partnership with Renishaw saw the introduction of additive manufacturing to Swift, fitting seamlessly into a newly implemented digital workflow. Renishaw supplied an AM250 system, which uses a high-powered ytterbium fibre laser to fuse fine metallic powders together to create a final three-dimensional structure.
The AM250 is coupled with Renishaw's DS30 blue light scanner, which creates a digital copy of a dental impression or model. The dental frameworks are designed in Renishaw Dental Studio (RDS) and exported as 3D CAD data. These digital files are then sent to the AM250 and are produced from 40 micron layers of CE-marked cobalt chrome powder. Up to 300 dental frameworks, each with a unique ID tag, can be printed within eight to twelve hours.
During the first two weeks of production, Renishaw mirrored Swift's production line at its site in Gloucestershire. This gave Swift Dental the confidence that, if there were any initial problems with the system, there would be back-up products manufactured at Renishaw's site.
"The fact that Renishaw offered us the mirrored production line during set-up gave us the assurance that there would be no loss of production or downtime during the initial machinery changeover," explained Perkins.
"The installation process was managed excellently by Renishaw, which enabled a smooth transition for our staff. The machine was delivered in mid-February and, within two weeks, we were up and running. Our staff embraced the digitalisation of the process and it gave our younger members of staff the chance to showcase their skills."
Not only is the company's technology on the cutting edge of the global manufacturing industry, but its technical support and customer service is first class.
Swift Dental Group (UK)
Results
In 2016, Swift Dental Laboratory won the Laboratory Award's categories; Best Dental Laboratory and Best Digital Dental Laboratory. The nationwide award scheme aims to recognise and reward outstanding work carried out by laboratories in the UK. Perkins directly attributes the award win to the successful implementation of Renishaw's technology.
"Renishaw's manufacturing expertise is one of the best kept secrets in the UK," continued Perkins. "Not only is the company's technology on the cutting edge of the global manufacturing industry, but its technical support and customer service is first class.
"In-house laboratory processes are much smoother and more efficient than ever before, and the level of accuracy that we are able to achieve with the additive manufacturing processes has helped position us ahead of our competition. Previously, around two products in every ten would need a rework after the end-customer's first fitting. The AM250 has helped reduce this drastically. This reduction in reworks is a particular benefit for dentists as it helps reduce the amount of appointments needed for each customer, which has a significant effect on the revenue of the practice.
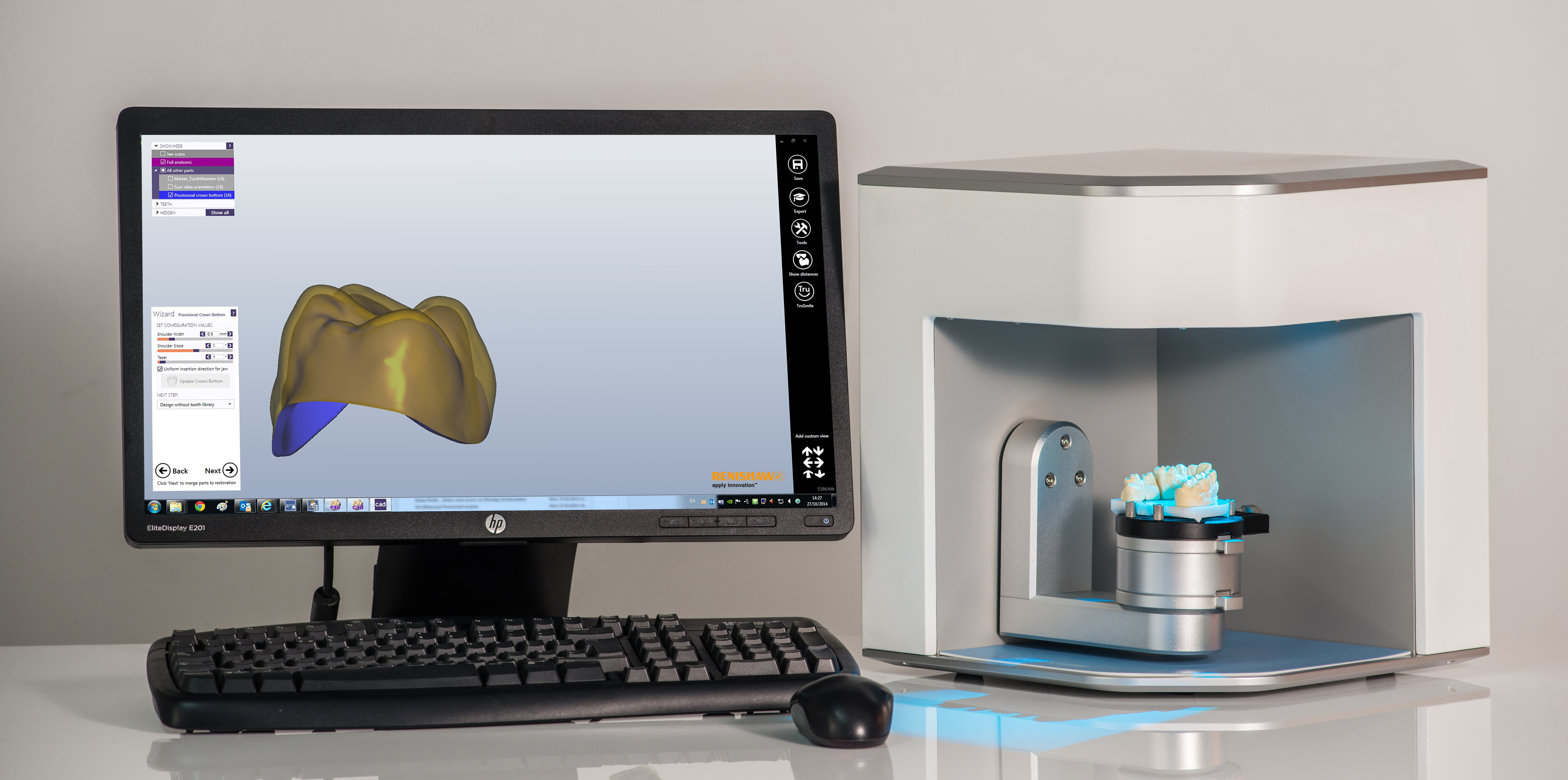
“In the future, Swift is planning to purchase another additive manufacturing system from Renishaw to further increase our production levels. We are also hoping to develop the manufacturing process of our other products, specifically our chrome removable partial dentures. Production levels currently sit at around 1000 [chromes] per month — designing and manufacturing these products using a digital process gives us the opportunity to increase our capacity, leading to job creation within the business.”