Ta strona nie jest obecnie dostępna w Twoim języku. Możesz zapoznać się z tłumaczeniem automatycznym, korzystając z usługi Google Translate. Nie jesteśmy odpowiedzialni za świadczenie tej usługi, ani też wyniki tłumaczenia nie były przez nas sprawdzane.
Jeżeli chciałbyś uzyskać więcej pomocy skontaktuj się z nami.
Using machine tool probes for precision metrology in the manufacturing of forged wheel and car chassis
The automotive industry is fiercely competitive. Tier-one car manufacturers are constantly looking for breakthroughs in areas such as performance, safety and innovative design, all of which places ever stricter requirements on the processing of metal components.
SuperAlloy Industrial Company Ltd. (SAI) is a supplier of high-quality lightweight forged metal products. The forged wheel and car chassis components SAI produce are used by the world's top car manufacturers that demand specialised technologies and services, including some of the world's top-tier car makers such as BMW, Mercedes-Benz, VW, Porsche, Ferrari, Ducati, Bentley, Audi, Rolls Royce, Jaguar, Land Rover, Ford, Chrysler, Toyota, GM and Honda, thanks to the company's insistence on premium quality and precision manufacturing. Renishaw machine tool probe systems, including the OLP40, RMP60, OMP60, and the NC4, are a perfect match for SAI, allowing SAI, assisted by Renishaw, to make great progress on the route to high end precision manufacturing.
SAI's relationship with Renishaw began with CMM measurement. SAI, explains: “When we entered the European market in 2008, we realised that our high-end car manufacturer clients' quality, dimensional stability and precision requirements for metal products were extremely high. While our equipment at the time was able to meet their volume requirements, we needed to enhance product quality and reduce the amount of rework and corrections during processing so as to achieve high quality levels.
Through Renishaw, we discovered machine tool probe measurement solutions that could deliver in-process measurement control and real-time data feedback on our existing CNC machines, thereby providing effective precision manufacturing control. This was a massive help in terms of increasing production efficiency and precision.”
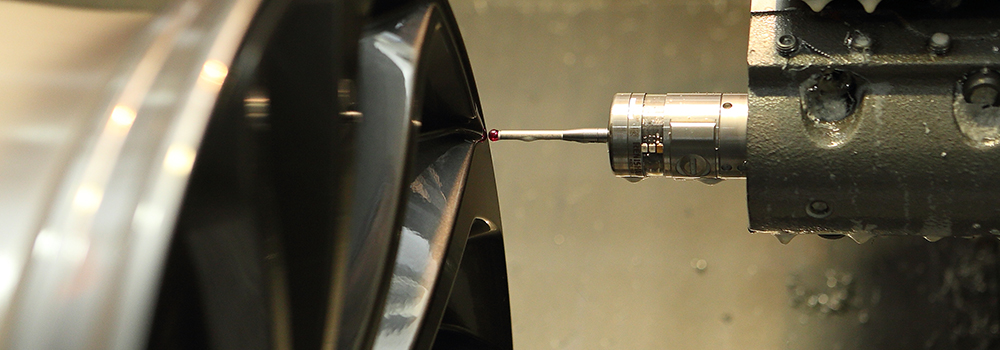
The production of aluminium forged wheel rims
The forged wheel production process is complex, particularly for low-volume, high-diversity production. SAI produces more than 200 types of wheel which requires the utmost production flexibility. Strict standards are applied to workpiece setting, reference measurements and key dimension detection during metal processing, as the precision requirements for machining wheel mounting surfaces exceed the requirements of even the aerospace industry. SAI currently has 600 CNC machine tools working on wheel rim production, including 150 Victor Taichung lathes and 450 YCM milling machines. All these machine tools are engaged in production on a three shift process five days per week.
In order to increase production precision and reduce scrap, SAI equipped the relevant lathes with Renishaw OLP40 touch probes, which use optical signal transmission and are adapted for turning processes. The CNC milling machines were equipped with RMP60 machine tool probes which use wireless radio transmission to measure workpiece position and reference height, as well as providing in-line key dimension detection, thereby increasing production performance.
Mr. Y. C. Kao, Director of SAI, explains: “The automated workpiece setup enabled by Renishaw machine tool probes allows us to ensure that the cutting dimensions remain stable and consistent when we are producing wheel rims, as well as effectively reducing human error. For example, the air valve hole cutting thickness Process Capability Index (CPK) rose from 0.71-1.13 to 1.35-1.43 when using Renishaw machine tool probes.”
3D appearance modelling for forged wheel
Wheel styling design has moved from flatter surfaces towards more 3D effects in recent years, causing wheel rims to become ever larger, and placing increasingly stringent demands on processing precision. Until 2011, SAI's acceptable tolerances for wheel rim production (with the flatter designs used at the time) were 0.05-0.10mm. However, the tighter tolerance requirements of the current 3D designs has gradually increased cutting times and processing; wheel rim appearance processing takes as long as 180 to 240 minutes, with the result that any rework imposes considerable pressures in terms of both production time and cost.
OLP40 probes allow SAI to carry out in-process measurement control to achieve tolerance of less than .0.02 mm, and can replace human measurements and updates to workpiece coordinates. This greatly improves cutting and efficiency for surface precision processing after coating. Even more importantly, it reduces rework by 80%, as before the introduction of in-line measurement systems wheel production generally had to be processed twice to achieve the necessary precision. When combined with Renishaw software, the probes not only play a role in guidance during production, but also provide in-process control and real-time feedback, immediately updating and correcting data during metal cutting, and efficiently monitoring and controlling dimensions and deformations.
Renishaw machine tool probe systems have allowed SAI to increase production precision and product quality, while also reducing scrap from 2-3% to 0%, and improving production efficiency.
Renishaw has an excellent reputation in manufacturing industries, and also provides service for different industries, so it doesn't just offer a product or a solution, but also shares with us its experience, expertise and the industry's best practices. Renishaw is also meticulous in terms of its technical support, the Renishaw team reacts quickly to solve problems; this is particularly impressive to us.
SAI (Taiwan)
Precision processing for car chassis
The automotive industry has already evolved from focusing on basic safety requirements and performance towards enhanced driving comfort, improved fuel efficiency and reduced emissions. The safety and stability of lighter vehicles moving at high speed is closely connected to the manufacturing of the car chassis. The higher the precision of chassis produced with aluminium alloys, the safer and more stable the car is when travelling at speeds as high as 200 km/h, and the more comfortable the driving experience. The lighter the chassis, the lower the fuel consumption, and thus the easier it is for the vehicle to meet environmental requirements.
SAI has continually improved its forging and mechanical processing technology. The company moved into the processing and production of precision car chassis in 2011. SAI now has 38 Tongtai high end five-axis CNC machine tools, all of which are equipped with Renishaw OMP60 optical machine tool probes and NC4 non-contact laser tool setters.
Unlike wheel rim production, chassis production tends to involve high volume and lower diversity, but nevertheless still requires high-precision metal cutting and processing. Renishaw OMP60 optical machine tool touch probes use advanced modulated optical transmission to provide 360° signal transmission. The probe simplifies measurement and calibration processes, thereby achieving high-precision measurement for workpieces with complex profiles. The NC4 uses innovative laser technology to perform high-speed, high-precision measurement of cutting tools as small as 0.2 mm, and to perform tool breakage detection on cutting tools as small as 0.1 mm. Its non-contact method avoids the potential for causing wear or damage of cutting tools.
Production times for car chassis are relatively short, and can generally be kept within 20-25 minutes. Renishaw machine tool probe systems provide the operator with turnkey solutions for real-time positioning and measurement, and in-process control measurement, helping to further automate production processes.
Trusted brand, thoughtful service
SAI chose Renishaw because of the company's trust in the Renishaw brand. SAI explains: “When we choose suppliers, we don't just look at the price of the product; we also attach a great deal of value to their R&D capabilities and service. Renishaw has an excellent reputation in manufacturing industries, and also provides service for different industries, so it doesn't just offer a product or a solution, but also shares with us its experience, expertise and the industry's best practices. Renishaw is also meticulous in terms of its technical support, and the Renishaw team reacts quickly to solve problems; this is particularly impressive to us.”
SAI's trust in Renishaw began with the use of CMM probes. The company now has 10 CMMs fitted with Renishaw probes. For machine tool performance checks, SAI has also fitted its machining centres with Renishaw QC20-W telescopic ballbar measuring instruments for the most comprehensive diagnostic testing and verification functions.
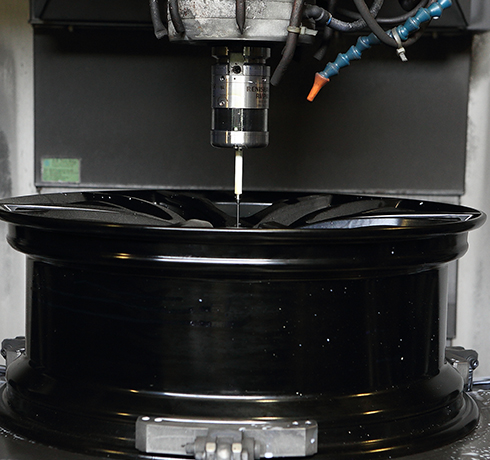