Scania – miejsce, gdzie konserwacja obrabiarki stanowi inwestycję, a nie koszt
Dynamate AB, firma zajmująca się obsługą techniczną instalacji dla wiodącego w świecie producenta ciężarówek Scania, wdrożyła jedną z najbardziej wszechstronnych i najlepiej zaplanowanych strategii konserwacji w swej dziedzinie.
Scania chce produkować jak najwięcej części jak to tylko możliwe "wewnętrzenie". Fabryka silników Södertälje zaopatruje Szwecję, Holandię, Francję, Brazylię i Argentynę.
Karl Orton, kierownik działu obsługi technicznej produkcji firmy Dynamate, z zadowoleniem wypowiada się krytycznie o nowych obrabiarkach – “Przyprawiamy o ból głowy producentów obrabiarek. Jak wykazały nasze testy, tylko 3 z 34 nowych obrabiarek zakupionych ostatnio spełnia standardy ISO! Scania zgadza się więc zapłacić nam abyśmy pojechali do dostawcy obrabiarki zanim zostanie ona do nich przewieziona, i wykonali testy aby ją poprawnie ustawić. Koniec końców jest to bardziej korzystne dla dostawców gdyż mając mniej zgłoszeń serwisowych mogą poświęcić więcej na ulepszanie swoich produktów i technologii."
Regularne, 20-minutowe testy
Przynajmniej jeden raz w roku, a w niektórych przypadkach częściej, każda z 500 obrabiarek CNC w zakładach w Södertälje jest poddawana kilku testom, które łącznie zajmują godzinę na każdą obrabiarkę. Około 20 minut z tego czasu jest poświęcane na wykonanie testów sprawdzających parametry pozycjonowania obrabiarek, za pomocą zestawu QC10 ballbar. Ich wyniki pozwalają od razu zidentyfikować możliwe do wprowadzenia ulepszenia, takie jak dostosowanie ustawień oprogramowania lub wskazują miejsca, gdzie należałoby zaplanować bardziej podstawowe prace konserwacyjne, na przykład wymianę pewnych części.
Wyniki każdego testu wykonanego przy użyciu systemu z prętem kinematycznym kulkowym (ballbar) są zapisywane w kartach historii, zapewniając rejestrowanie zmian stanu technicznego maszyny następujących z upływem czasu. Pozwala to firmie Dynamate przewidzieć, kiedy konieczne będzie przeprowadzenie zadań konserwacyjnych, zamiast „gasić pożary” w sytuacjach, gdy zły stan techniczny obrabiarki powoduje produkowanie braków.
Test z użyciem systemu ballbar polega na uruchomieniu na obrabiarce programu CNC, który zrealizuje ruch po okrągu o określonym promieniu. System ballbar jest montowany pomiędzy wrzecionem obrabiarki i łożem wykorzystując specjalne magnetyczne uchwyty. W trakcie gdy obrabiarka wykreśla zaprogramowany okrąg, system ballbar monitoruje promień okręgu, a wszelskie odchylenia od "idealnego" okręgu są zapisywane przez oprogramowanie QC10 ballbar.
Dokładność z jaką obrabiarka porusza się po okręgu jest wskazówką odnośnie dokłądności pozycjonowania, a oprogramowanie Renishaw jest w stanie zidentyfikować 21 oddzielnych czynników i obliczyć dokładnie ile procent danego błędu stanowi każdy czynnik.
Ten 20 minutowy test, który jest dokładnie taki sam dla wszystkich inżynierów gdziekolwiek się znajdują, jest idealny zarówno dla centrów obróbkowych jak i tokarek. Dynamate stara się opracować taki sam test dla szlifierek i obrabiarek do kół zębatych.
Możliwość uzyskania natychmiastowej poprawy
Kjell Norstedt, inżynier ds. konserwacji z Dynamate jest w stanie udowodnić że bardzo często obrabiarka sama w sobie powoduje problemy, w co operatorzy często nie chcą wierzyć. Pierwszy test jaki wykonuje na obrabiarce często ukazuje błędy o których wcześniej nie wiedziano. Już na tym etapie jest w stanie zaprezentować dramatyczne ulepszenia. Pan Norstedt wyjaśnia typowy przykład -
“W przypadku jednej z obrabiarek produkujących przekładnie konieczne było ręczne wprowadzanie poprawek ustawień oprogramowania co kilka godzin w okresie ostatnich kilku lat, aby zapewnić utrzymywanie wymiarów części w granicach tolerancji. Wykonałem test z użyciem systemu ballbar trwający kilka minut i stwierdziłem występowanie odchyłki okrągłości równej 948 mikrometrów! Wykorzystując wartości uzyskane z programu analizy systemu ballbar mogłem natychmiast zmienić ustawienia kompensacji luzu zwrotnego i zredukować błąd kołowości do wartości niższej niż 400 mikronów. Po wymianie silników zniknie większość pozostałych błędów i już nie będą musieli zmieniać wartości ustawień programu.”
Dodaje, “Dawniej, pomiar jakości był wykonywany po wyprodukowaniu przedmiotu, bardzo niewielu wykonuje pomiary przed produkcją, aby analizować stan techniczny maszyn. Przynajmniej ktoś rozumie, o czym mówimy – musiałem czekać 20 lat, aż ktoś to usłyszy.”
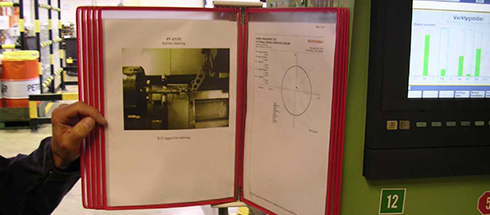
Znając stan każdej obrabiarki
Firma Dynamate poprosiła inżynierów ds. planowania produkcji w Scanii, aby sklasyfikowali wszystkie obrabiarki jako A, B lub C, zgodnie z pięcioma różnymi wytycznymi:
- bezpieczeństwo (kwestie BHP)
- krytyczne cechy wysokiego ryzyka
- duża ilość / czas poświęcony na skrawanie
- redukcja
- planowane wykorzystanie w przyszłości
Dzięki tym kategoriom, firma Dynamate może zaplanować częstotliwość i zakres programów konserwacyjnych i dostarcza Scanii informacje gdzie obrabiarki są nadużywane i gdzie jest duże prawdopodobieństwo wystąpienia błędów. System QC10 ballbar jest niezbędny aby zrozumieć, które obrabiarki mają krytyczne znaczenie w kwestii produktywności i występowania opóźnień.
Analizowanych jest wiele aspektów związanych z każdą obrabiarką, w tym struktura i dynamika, a wszystko by móc poinformować Scanię jak długo dana obrabiarka będzie produkować dobre części, które maszyny wymagają napraw, a które wymiany. Wiele obrabiarek może produkować bardziej odpowiednie części przez dłuższy czas ponieważ rozwiązywane są problemy u samej podstawy, a nie oznaki części zezłomowanych.
Mocne strony Dynamate
Dynamate jest jednostką całkowicie należącą do Scanii, ale działającą jako niezależna firma. Obrót wzrósł z 30 millionów euro w roku 1997 do 130 millionów euro w roku 2004, przy zatrudnieniu 720 osób. Przedstawiając siebie jako " zwolennika konserwacji" uzyskali wiele nowych kontraktów, w szczególnowści bardzo dobry, 5 letni kontrakt z firną metalurgiczną. Jak podsumowuje pan Orton "Największym wyzwaniem jest przekonanie ludzi, że kontrolowanie wydajności obrabiarek jest inwestycją, a nie kosztem."
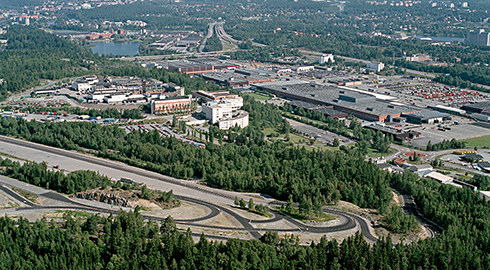