Ta strona nie jest obecnie dostępna w Twoim języku. Możesz zapoznać się z tłumaczeniem automatycznym, korzystając z usługi Google Translate. Nie jesteśmy odpowiedzialni za świadczenie tej usługi, ani też wyniki tłumaczenia nie były przez nas sprawdzane.
Jeżeli chciałbyś uzyskać więcej pomocy skontaktuj się z nami.
Of robot mice and men
International ‘Micromouse' competitions inspire the engineers of the future with ever more sophisticated electronic designs, including the latest Renishaw magnetic encoders.
What is so interesting about a competition to design, build and program a robotic ‘mouse' that finds its own way to the centre of a 16 x 16 maze in the shortest possible time? Micromouse events have fascinated the cleverest time-served engineers, but also captured the imagination of students, demonstrating the exciting possibilities of an engineering career to young minds. The competitions are entered by everyone from school children to engineers at blue-chip computer companies and top universities.
Designing a Micromouse to win
A Micromouse has to find its own way through a maze, with a different and un-predictable layout every time, between the start point in one corner and the centre point. It has several runs, with the competition scored through a combination of total time and the time for the fastest run.
At the top levels the competition is fierce, with a delicate balance to be struck in the design between on-board processing power, speed and manoeuvrability, and minimising weight to the last gram. Derek Hall, current UK champion, designs his mouse with complex SMT electronics and custom designed boards. However it is the latest addition, Renishaw magnetic encoders, that provide the servo feedback on the drive system, which has made a real difference to performance. Mr Hall uses the chip version of the Renishaw magnetic encoder, while his long time rival and previous champion, Alan Dibley, uses the on-board version.
Renishaw magnetic encoders are unrivalled
Explaining the reasons behind his decision to use the Renishaw encoder, Mr Dibley says, “The AM256 comes on a small board which is very easy to connect and fit to such a small complex machine. The robust nature of the magnetic encoder is very important – optical encoders don't work because of dust ingress, and sealed optical encoders are too expensive. The fact that the Renishaw magnetic encoders are non-contact, introducing no extra friction into the drive system, is critical – there are no other encoders like this on the market.”
He continues, “I have been very pleased with how easy it was to interface with the encoders, the signal goes straight into the PIC chip I use, to provide feedback on distance travelled by each wheel. The on-board program needs to know how far the mouse has travelled to work out where it is at all times. Coupled with the signals from the sensors it can work out where the walls are, usually when it has reached a dead end or passed the end of a wall to the side of the mouse.”
I have been very pleased with how easy it was to interface with the encoders, the signal goes straight into the PIC chip I use, to provide feedback on distance travelled by each wheel.
Micromouse (UK)
From basic processors to the latest technology
UK MicroMouse competitions started in 1980 using ZX80 computers, when Nick Smith created the first mouse to find its way through a maze on its own. Interest in the idea rapidly increased, with television appearances on shows such as Johnny Ball's ‘Think of a number' in 1983.
Currently competition contenders use a 2-wheel drive ‘wheelchair' construction with pads front and back to aid balance, and infra-red wall-sensors on the front and sometimes the back. Stepper motors are very powerful, but to improve acceleration DC motors and encoders are used. The wheels have special rubber to improve grip, allowing the motors to drive the mouse at more than 1G of acceleration. Mice must be no bigger than 25 cm (w) x 25 cm (l), and whilst there are no limits to height or overall weight, heavier components reduce performance and battery life.
Clearly the programming of the mouse is critical to the performance. The maze-exploration logic takes into account how far the mouse travels and all the turns it makes, and whether it has passed the end of a wall or is approaching a wall; all to build and memorise a map of the un-known maze layout from the starting corner. Once it works out that it has travelled enough grid blocks forward and to the right, in other words reached the centre of the maze, it comes back to the start to attempt a faster and shorter route, remembering exactly where it made choices before. The fewer runs it takes to find the optimum route the better, so the logic employed can make all the difference.
The competitions have very clear rules, with mazes laid out with randomly different routes to the centre, on an 18 cm grid pattern, with walls no thicker than 12 mm and 5 cm high. Before the maze is unveiled, the mice must be accepted and ‘caged' by the contest officials. A mouse handler is given 1 minute, from the moment the mouse is taken out of the cage, to make any adjustments (if any) to the mouse sensors, but no selection of strategies must be made and no information on the maze configuration entered or captured into the memory.
Inspiring tomorrow's engineers
The concept can run at many levels, with, for example, MicroMouse used as the basis for final year projects for university students, or in simplified school competitions. Kits are available for schools with 2 options – wall following or line following robots (which use no walls).
Micromouse embodies so many aspects of engineering that it is easy to see how it appeals to education - mechanical and electronic design, programming, and a real possibility of using the latest technology to improve on previous designs.
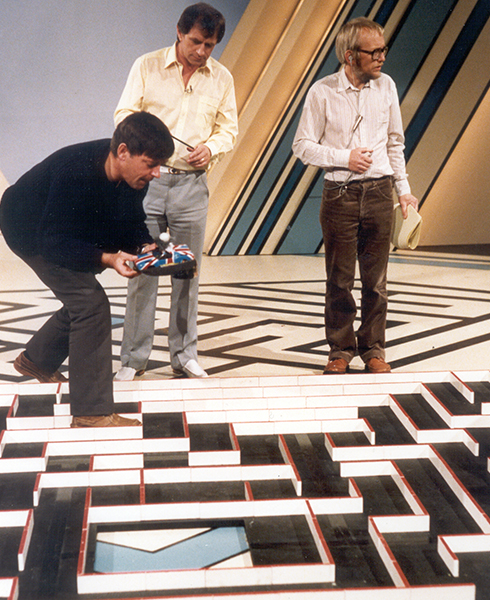