Deze pagina is momenteel niet beschikbaar in uw taal. U kunt met behulp van Google Translate een automatische vertaling bekijken. Wij zijn niet verantwoordelijk voor deze dienstverlening en het vertaalresultaat is niet door ons gecontroleerd.
Heeft u meer hulp nodig, neemt u dan contact met ons op.
Renishaw AM technology helps Swinburne electric car to best-ever Formula SAE result
Metal additive manufacturing technology from Renishaw has helped a team of students from Swinburne University of Technology in Melbourne, Australia, to the University's highest overall score in the latest Formula SAE competition.
As well as being placed sixth overall, the highest position for a team from the University, the car recorded some of the fastest times in the speed trial part of the competition.
Background
Formula SAE is a competition organised by the Australian branch of the Society of Automotive Engineers in which teams of students produce a prototype for a single-seat racing car and present it to a hypothetical firm for manufacture. The cars compete in a series of track tests. In addition, the teams are judged on the design and cost-efficiency of the car, and on a marketing presentation about their project.
Along with the practical experience gained, the programme gives students the opportunity to work together in a dedicated, multi-disciplinary team to produce an impressive vehicle for the competition. The skills of the team are pushed to the limit to ensure that the design and the manufacturing methods used are innovative and robust.
The team from Swinburne is made up of students in engineering, design and commerce, who work together to design, build, market and race their car.
In 2010, the University was one of the first to enter an electric car in the competition. It has continued to race electric cars in subsequent years.
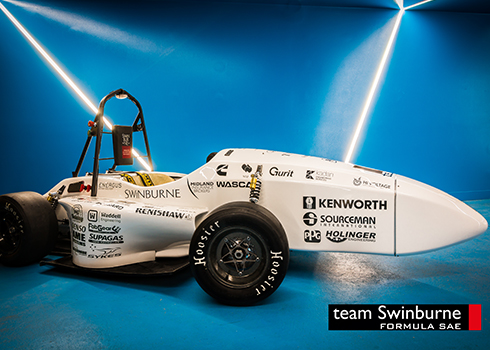
Challenge
The fundamental problem in racing an electric car against petrol competition is the weight of the batteries. This means that the weight of all the other components must be minimised to make the car competitive. Team Swinburne is always looking for ways to reduce weight, including being one of only a few teams to base its car on a carbon fibre chassis, which is built at the University.
Following the 2015 competition, the team undertook a detailed calculation of the energy used by the car in the various trials.
One of the findings of this analysis was that the rotational inertia of the wheels during acceleration and braking was using much more energy than expected.
Ryan Wise, the Dynamics Section Leader for Team Swinburne, was given the brief to reduce the weight of the wheels and so cut their rotational inertia. Lighter wheels would, in addition, improve the acceleration and braking performance, and enhance the responsiveness of the suspension. Ryan had been associated with the Team for the 2014 and 2015 competitions, and had been given responsibility for the suspension, wheels, brakes and steering for the 2016 car.
One of the things that I loved about using the Renishaw additive manufacturing equipment was the ability to increase the complexity of my design.
Swinburne University of Technology - Formula SAE (Australia)
Solution
The use of additive manufacturing was suggested by one of Ryan's colleagues in Team Swinburne following a general search of new materials and technologies being used by teams in the equivalent European competition, Formula Student. He had found examples of the use of the Renishaw technology by these teams and suggested that Ryan should contact the company.
Ryan approached Renishaw's office in Australia with a wheel from the 2015 car comprising a centre machined from an aluminium alloy, and a band also made from aluminium. Ryan worked through several design iterations, replacing the aluminium wheel centres with smaller ones made from titanium alloy by additive manufacturing.
The new design also used a carbon fibre band in place of the aluminium one to give the maximum weight savings.
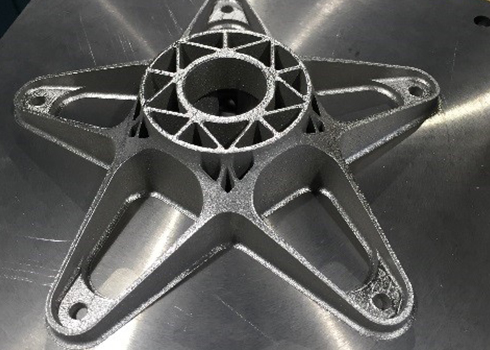
Guidance in design optimisation for additive manufacturing was provided by Renishaw staff to reach an alternative design with which everyone involved was happy.
Iterative FEA (finite element analysis) simulations were performed throughout the design process in order to predict the behaviour of the new component and to evaluate the benefits that could be gained.
“One of the things that I loved about using the Renishaw additive manufacturing equipment was the ability to increase the complexity of my design,” said Ryan.
“With parts that I had designed for traditional manufacturing methods, I had to be very aware of the size and shape of the cutting tools that were available as well as the added machining time that would be required by certain design features. By 3D printing the wheel centres, I was able to add in fine features that would be difficult to achieve using traditional methods and it cost nothing in extra build time.”
Once the design had been finalised, Renishaw Oceania manufactured nine wheel centres to provide Team Swinburne with two full sets of wheels and an extra wheel for testing. The wheel assembly was designed so that each of the titanium components would require minimal post-processing. On removal from the AM equipment, the parts were stress-relieved in a vacuum furnace, removed from the build plate with wire EDM and bead-blasted. No further post-processing or machining was required.
Results
The new design, with the titanium parts replacing the machined aluminium centres, and the broader carbon fibre band, reduced the weight of each wheel by 20%, resulting in a significant 75% reduction in rotational inertia, leading to measurable improvements in acceleration and braking performance. The additively manufactured wheel centres also contributed to an overall weight reduction of 1 kg per wheel, whilst also maintaining safety, leading to an overall improvement in the car's performance that was evident in the results on the track.
A big advantage of using Renishaw's additive manufacturing technology was the ability to use titanium. “The amount of material for the initial billet, together with the machining time and experience that would be needed, had ruled out using titanium with traditional manufacturing methods,” explained Ryan.
“Printing the parts required very little effort on our behalf and they were manufactured much more quickly than the last set of wheel centres that we made. I was surprised at the quality of the surface finish and that we required no finish machining.”
“I think there were a few people who were quietly sceptical on seeing how thin they were,” added Ryan. “I'll admit that I was feeling nervous after the team next to us broke a wheel centre on the track. However, in the end, we gave them a good testing and they held strong. So it's a credit to Renishaw to be able to achieve the material properties required.”
As well as contributing to the team's success, Ryan gained personally from working with Renishaw. “At the start of the year, I knew next to nothing about additive manufacturing of metals,” he admitted. “I soon learnt that, as with any other manufacturing technique, you need to consider the capabilities of the process during the design stage.
After a few educational sessions from Renishaw on how the 3D printing system worked and where the issues might arise, I was soon able to adjust the design to be more achievable.
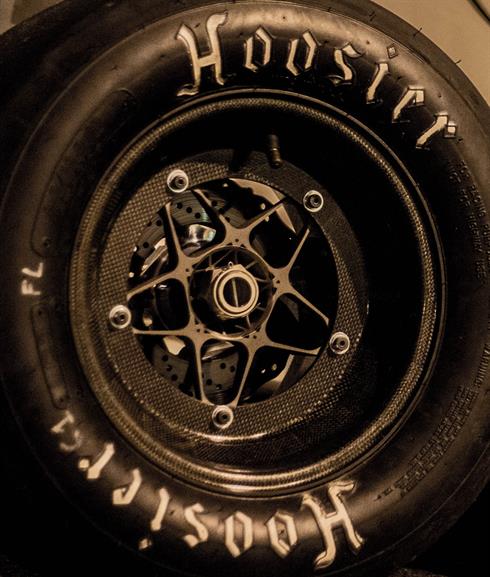
We looked into some unique tricks, such as printing skins around an internal lattice to reduce weight and to keep the thermal stresses down. Once I understood the process, I found it surprisingly easy to come up with a design that was both light-weight and printable."
Ryan expects to see more teams using metal additive manufacturing in this year's competition. "I lost count of the number of people that came into our pits, just to check out the new wheels," he commented. "They looked incredible and we had no issues with them at all. A lot of people will have gone home impressed."
Printing the parts required very little effort on our behalf and they were manufactured much more quickly than the last set of wheel centres that we made. I was surprised at the quality of the surface finish and that we required no finish machining.
Swinburne University of Technology - Formula SAE (Australia)
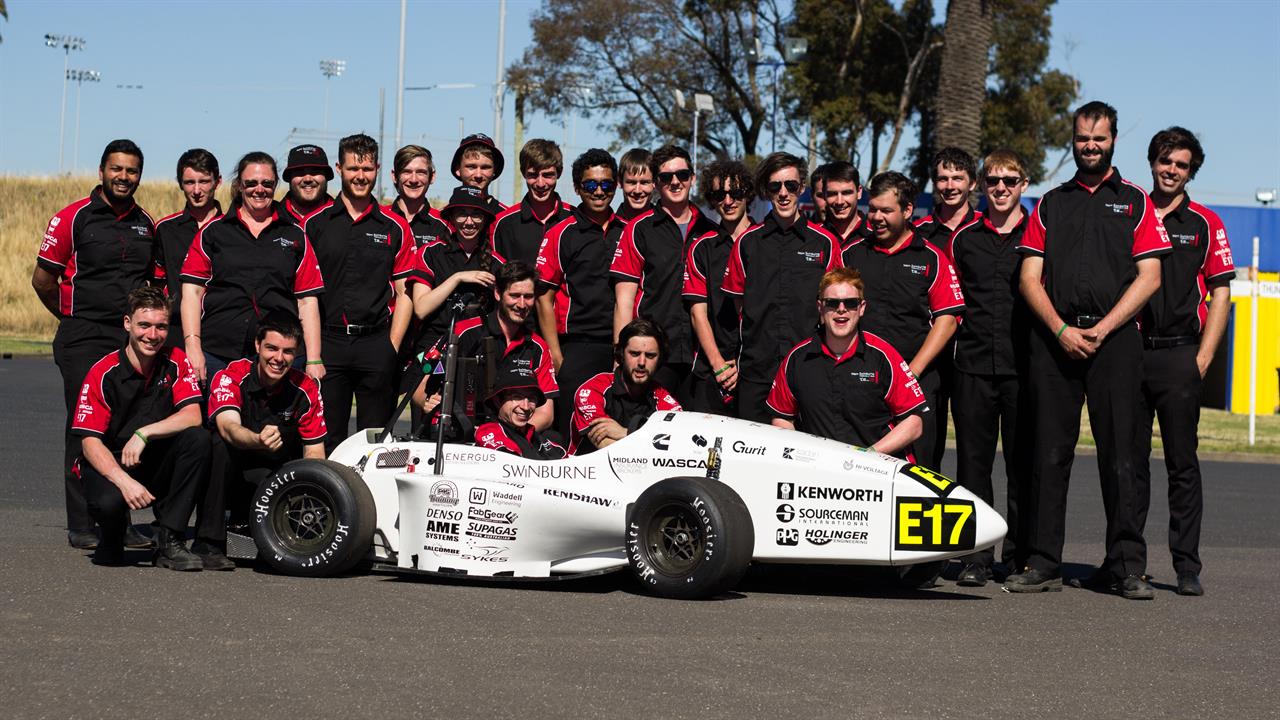