Deze pagina is momenteel niet beschikbaar in uw taal. U kunt met behulp van Google Translate een automatische vertaling bekijken. Wij zijn niet verantwoordelijk voor deze dienstverlening en het vertaalresultaat is niet door ons gecontroleerd.
Heeft u meer hulp nodig, neemt u dan contact met ons op.
How to prosper as a UK machining sub-contractor
The directors of Castle Precision have embraced the latest technology in every discipline, but not for the sake of it – this is technology applied so effectively that in some cases ‘wasteful' operations have been reduced by over 80%. As an example, Renishaw probe systems on Castle's CNC lathes have reduced inspection times from about 35 minutes to less than 6 minutes.
Build quality in; don't inspect to achieve it
Renishaw has become involved with Castle, and has closely supported them, for over 20 years. Chairman Marcus Tiefenbrun comments “I firmly believe in the principle of building quality in, not inspecting to achieve it. Renishaw probing is central to that manufacturing philosophy and throughout our use of CNC machines we have had a close relationship with Renishaw – the flexibility and willingness to assist has always been outstanding.”
In 1984 a Mori Seiki 6-pallet machining centre was delivered fitted with Renishaw spindle probing. Although the software was limited at that point, the probe proved extremely useful for datuming all jobs – Castle had no doubts in fitting every new machine, from that point on, with probing retrofitted by Renishaw as standard.
Spindle probing is well accepted on machining centres but Castle have also demonstrated how effectively it can be used on CNC lathes for set-up and inspection tasks. Director of Engineering Alex Skinner, who, together with Marcus Tiefenbrun, has provided the inspiration behind the drive for technology, explains why this process in particular demonstrates how efficiency gains can be made.
“On one component we used to spend 35 minutes on in-process inspection – this had to be improved. It was manually loaded and had to stay in place, effectively part of the machining cycle, so the machine was stopped, not producing parts, for the whole of the in-cycle inspection. The inspectors would measure a particular thin-walled feature, decide whether or not it met specifications, pass or fail the part, and then not even record the measurements they had taken! We replaced this with a probe cycle, reducing the inspection cycle to about 6 minutes. The measurements taken are recorded in an SPC package and kept on record. We can tell instantly the measured dimensions of every part we have made over the last 5 years!”
Intelligent decisions with probing systems
That's not the end of the story – Alex Skinner continues “We decided to use the probe to make intelligent decisions. The measurements the probe takes are used to update offsets, these offset changes are downloaded and recorded to monitor and control the process. We have been able to significantly reduce human intervention, such that now each operator often runs two machines instead of one.”
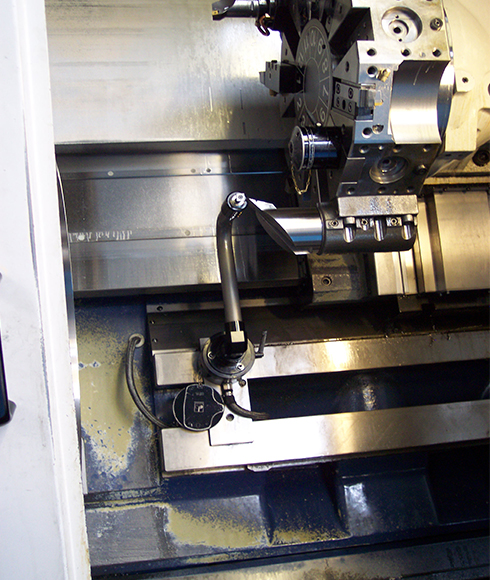
Changing control systems to integrate probing
All machines in Castle's workshop must have probe systems; in fact it is so important that some machines have had to have the control system replaced to accommodate probing. Probe systems have been adapted to 4-axis machines, even to the extent of detailed examination of the mounting brackets to maximise accuracy. Two new vertical turning lathes will be fitted with probing systems.
Marcus Tiefenbrun has no doubts about the impact of the probe systems on his business. “The biggest benefit is the reduction… no, it would be more appropriate to say total elimination, of all offset problems. The second biggest is the de-skilling of the operations. We have also found that when our customers look closely at the processes we employ they are very impressed, going away with the confidence that the process is under control.
Quality and tight control are essential because our business is mostly ‘high-end'; we don't usually get involved with low-cost parts. We have learnt to specialise, for example in titanium parts for a whole variety of industries, and not even attempt to compete on mundane parts with developing countries.”
Skilled staff and training are the key
One vital element to running a process like this is having the skilled staff to run it. Marcus Tiefenbrun's father ran the company before him, and believed in a strong apprenticeship scheme. When Marcus took over in 1994, he invested heavily in the latest machinery and control systems, but never forgot the importance of skilled people to run them, with up to 20 people at a time in training, supplemented by their college grounding. The importance of this is further emphasised by the central role played by the project staff, all of whom have been trained internally.
Marcus explains “Expansion is limited by how many skilled people can be recruited. Colleges need to, and in some cases now do, invest in the latest equipment. Success is down to the entire process working well together i.e. fully integrated liaison between us and the college.”
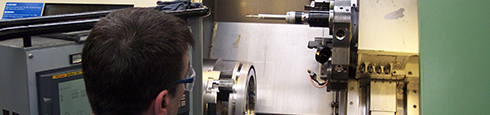
Integration of the entire company computer system
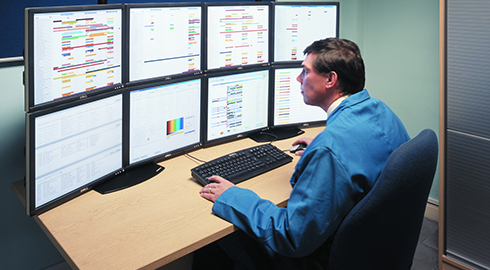
Castle's computer system has to be seen to be believed! ‘System' is the correct word to use, because every company application is integrated into one program. This system can be accessed live from any other terminal (of which there are many dotted around the company) by a real-time biometric fingerprint recognition system. Employees have access to the information they require from the system, which includes CAD/CAM functions, production scheduling, time recording, inspection reports, invoicing, sales databases, even personnel records!This access to information brings
multiple benefits which contribute to the efficient running of the organisation.