Ducati vertrouwt op gereedschapbreukdetectie bij productie van unieke nokkenassen.
Ducati realiseert zich dat het bewerken van kostbare componenten voor zijn desmodromische motoren zorgvuldig gestuurd moet worden. In de loop van een jaar worden verschillende gereedschappen honderdduizenden keren gebruikt, waarbij voortdurend het risico bestaat dat uit het magazijn een beschadigd of gebroken gereedschap wordt gehaald met alle ernstige gevolgen van dien. Een Renishaw detectiesysteem voor gereedschapbreuk op basis van innovatieve contactloze lasertechnologie biedt hier de oplossing.
De belangrijkste stap in het productieproces van Ducati’s desmodromische nokkenas wordt uitgevoerd op twee Stama bewerkingscentra. De machines bewerken non-stop het hele jaar door nokkenassen voor alle verschillende Ducati motoren.
Fulvio Abbondi, specialist in productietechnologie bij Ducati Motor, geeft uitleg: “De fabricage van deze assen vraagt om grote precisie, en het nogal langdurige bewerkingsproces voeren we volledig in eigen huis uit. Dit is een heel dure component. De as wordt gemaakt van een speciale staallegering en is al kostbaar als hij na het eerste ruwdraaien bij de machine aankomt.”
Gereedschapbreuk tijdens de nokkenasproductie zou een ernstige zaak zijn, die kan leiden tot uitval, kostbare herstelbewerkingen en tijdverspilling. Daarnaast zou aan de machinespindel schade kunnen ontstaan die, samen met de kosten voor het speciaalgereedschap zelf, duizenden euro’s kan bedragen.
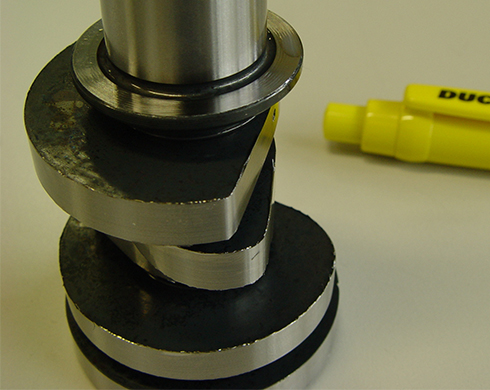
Controle inbouwen
Abbondi licht de rol toe die gereedschapbreukdetectie speelt: “Controles uitvoeren op het werk dat de machines verrichten is essentieel. Op twee bewerkingscentra hebben we een Renishaw NC4 systeem geïnstalleerd. Direct na plaatsing in de spindel om gebruikt te gaan worden doorkruist elk gereedschap de laserbundel op een bepaalde hoogte. Als de snijtip gebroken is en bijvoorbeeld in plaats van 100 mm nog maar 97 mm lang is, dan geeft het lasersysteem een alarmmelding. Ieder gereedschap heeft natuurlijk zijn eigen lengte en diameter, en het systeem houdt daar rekening mee wanneer het gereedschap door de controlebundel gaat.”
En hij voegt toe: “De NC4 maakt het ook mogelijk om klein gereedschap op breuk te controleren. Dat gebruiken we om spiegleuven en andere referentiepunten in de nok te maken, die van vitaal belang zijn voor een goede motorloop. Zonder het Renishaw systeem zou de machine bijvoorbeeld gewoon kunnen doorgaan met een gebroken snijtip, met rampzalige gevolgen. Bovendien kan één operator nu gemakkelijk twee machines bedienen, aangezien de controle op gereedschapsbreuk automatisch gaat. Hij hoeft alleen maar de producten te plaatsen en te controleren of alles soepel verloopt.
Procesbesturing is kritieke factor bij machinale bewerking
“Eerst hebben we een systeem geïnstalleerd dat de machinefabrikant ons leverde”, beschrijft Abbondi. “Dat controleert het vermogen dat de spindelmotor opneemt. Zo bepaalt het systeem de mate van slijtage van de grotere boorbits, gebruikt voor de diepste gaten waarin de spanning tijdens bewerken het meest blijkt. Als het koppel toeneemt, wijst dat erop dat het gereedschap versleten is en volgt een alarmmelding. Maar daarnaast wilden we snel en betrouwbaar het breken van gereedschap detecteren, zelfs bij de kleinste die er vaak in slagen aan detectiesystemen te ontkomen.”
Conventionele contact makende systemen hebben enkele nadelen en zijn meestal ongeschikt voor klein gereedschap. Het gereedschap raakt een knop of staaf, die het systeem activeert. Het gevaar bestaat dat door dit contact het gereedschap breekt of beschadigd raakt. Controleren is dus alleen mogelijk met lage snelheden, wat het proces afremt en de cyclustijden aanzienlijk verlengt. Verder moeten de systemen dikwijls in het werkgebied ingepast worden, waar ze kostbare ruimte in beslag nemen, een botsrisico vormen én nog eens minder betrouwbaar zijn omdat ze vast kunnen zitten. Daarom werd het Renishaw systeem in gebruik genomen ter vervanging van deze systemen.
Controleren met licht
Ontwikkelingen in de lasertechnologie hebben contactloze detectiesystemen mogelijk gemaakt die zelfs kleine gereedschappen veilig kunnen meten. Een laserbundel bevindt zich tussen een zender en een ontvanger, die zodanig op de machinetafel of aan weerszijden daarvan zijn aangebracht dat de bundel door het werkgebied loopt. Wanneer het gereedschap in de bundel komt, vangt de ontvanger een kleinere hoeveelheid licht op en ontstaat een puls. Indien de hoeveelheid licht niet vermindert, dat meldt het systeem een gereedschapbreuk.
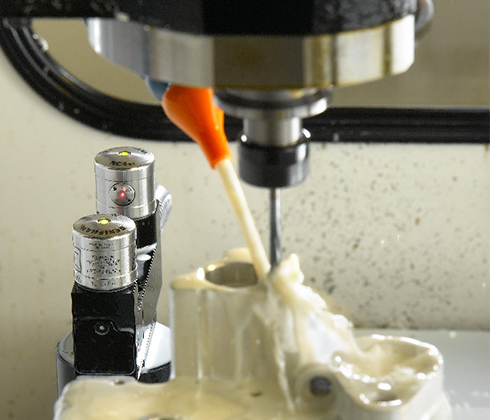
Het desmodromisch systeem
Vrijwel alle motorfabrikanten in de wereld gebruiken klepveren in hun motoren om de in- en uitlaatkleppen te sluiten. Deze veren duwen de kleppen terug in hun uitgangspositie nadat ze geopend werden. De enige uitzondering hierop is Ducati, dat grote voordelen haalt uit het minder conventionele desmodromische systeem. Desmodromische kleppenbediening werkt bij hoge toerentallen betrouwbaarder, omdat er geen massatraagheid van veren is en zo’n 30% minder wrijving optreedt. In theorie kan de motor gemakkelijk 20.000 tpm bereiken.
Desmodromisch houdt in dat de kleppen op mechanische wijze worden gesloten, een concept van Amerikaanse oorsprong dat later werd verlaten vanwege de hoge kosten. De beroemde fabrikant uit Bologna dacht daar echter anders over en nam in 1972 desmodromische kleppenbediening op in zijn tweecilindermotoren, die al decennia lang winnaars zijn. De kleppen worden gesloten door een speciale nok in plaats van een veer, zodat er altijd een directe verbinding is tussen de klep en zijn bediening. De term desmodromisch komt dan ook van het Griekse woord “desmòs” dat “verbinding” betekent.
Het desmodromisch systeem maakt het ontwerpen en produceren van componenten als nokkenassen aanzienlijk gecompliceerder. De nokken zien er niet uit zoals gebruikelijk, maar zijn voorzien van speciale vormen voor het heffen. Het ontwerpteam van Ducati heeft de vormen zorgvuldig vastgesteld op basis van de vereiste acceleratie en topsnelheid. Precisie is alles. Zo wordt de speling tussen klepsteel en nok tijdens het samenbouwen uiterst nauwkeurig met de hand ingesteld. Zoals Abbondi vertelt: “Het is niet mogelijk de speling te bepalen met hydraulische klepstoters zoals bij auto’s. Wij passen een vulplaatje onderaan toe en een bovenaan, en dat moet buitengewoon precies gebeuren.”