Deze pagina is momenteel niet beschikbaar in uw taal. U kunt met behulp van Google Translate een automatische vertaling bekijken. Wij zijn niet verantwoordelijk voor deze dienstverlening en het vertaalresultaat is niet door ons gecontroleerd.
Heeft u meer hulp nodig, neemt u dan contact met ons op.
AksIM™ supports Universal Robots for smart factory automation
Industrial robots usually operate in safety zones and are used for heavy, highly hazardous and repetitive tasks in aerospace, automotive assembly, handling, painting, coating and other applications. Conventional industrial robots are typically gigantic and bulky, they occupy a large area and the programming processes are usually time-consuming.
Factory automation is becoming more and more diverse in terms of manufacturing requirements and new technologies, and with the introduction of smart factory concepts a number of new robot manufacturers have been established in recent years, especially in China. Robotic applications have expanded gradually from conventional heavy industries to light industries, such as 3C product assembly (computing, communication and consumer) and other automatic production lines, where robots with high-precision and high-flexibility are necessary.
The use of collaborative robots is becoming a fast growing trend in today's industrial automation. They are designed to work with people to help finish scheduled tasks in production by simple and quick programming or even self-learning processes. Robots are no longer an exclusive solution for large enterprises; SMEs (small and medium-sized enterprises) can also benefit from the use of robots.
Denmark-based company Universal Robots (UR) is one of the most successful, high-profile robot manufacturers in the market. Their multi-axis collaborative robots employ the AksIM series magnetic rotary absolute encoder which offers outstanding performance, system safety and stability.
No matter how excellent the design, a robot still relies on the components used in order to maximise its functionality and efficiency. A robot usually consists of a main body (skeleton), a servo-driven system, a reducer and a control system. Requiring position feedback for real time position tracking of each joint to the controller, an encoder is also a critical component to ensure the robot's accuracy.
UR robots achieve a significant enhancement in overall performance by using an RLS' AksIM series magnetic rotary encoder, supplied by Renishaw's associate company RLS. The encoder is attached to the reducer's end to directly monitor the actual rotating angle of the robot's joint. Compared to some of the robot designs where the encoder is attached to the reducer's front, this approach eliminates system error, resulting in a robot repeatability of ±0.1 mm, which is sufficient to meet the majority of market needs.
AksIM is a true absolute encoder without the need of a battery backup - absolute position is determined immediately upon power-on.
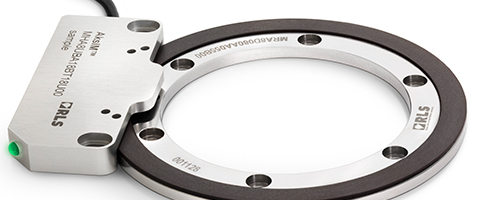
The encoder has multiple built-in self-monitoring functions, which supports the UR robots operational safety. The encoder and ring have been specifically designed in compact form for integration onto the reducer, and it increases the joint's thickness by just 7 mm. The hollow ring allows cable to be fed through it, simplifying cable management and allowing customers to have more flexibility in system design. Furthermore, the lightweight encoder has also significantly reduced loading on the joints, resulting in lower energy consumption.
The AksIM encoder has an outstanding performance specification to satisfy the most demanding robotic application requirements. Resolution is up to 20 bit, with system accuracy up to +/-0.1° and repeatability better than the unit of resolution. It features excellent dirt immunity with a IP64 rating to allow operation in harsh industrial environments.
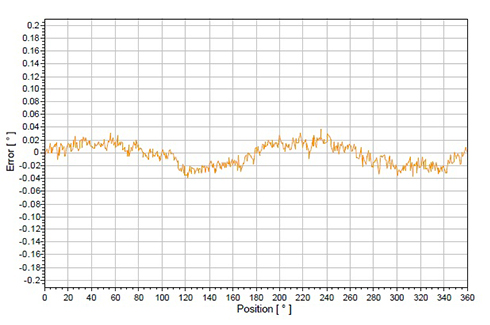
The UR collaborative robot is believed to be unique in the current market, concurrently achieving characteristics of simplicity, flexibility and safety. UR is cooperating with many well known companies to develop more flexible production processes and provide a healthy and safe working environment.
The innovative PolyScope Robot System software enables someone with no technical background or limited experience to conduct programming and debugging of the robot. Installation takes less than 3 hours, enabling the UR robots to be deployed at any time on different production lines to run for new operations, providing unlimited possibilities for the flexible conversion of production lines.
Moreover, the lightweight UR robot can be fitted anywhere on a table, device or even on the ceiling, giving manufacturers flexibility in different applications. UR robots' unique force sensing and force control features ensure the safety of employees, so that the robots can collaborate with workers without guard fences. When a person contacts the robot beyond a defined force limit, UR robots will stop automatically.