3D metaalprinten verlegt de grenzen in Moto2™ met uitdagende innovaties
In de dynamische wereld van de MotoGP™ motorraces hebben technische verbeteringen veel effect. Het races winnende team TransFIORmers zet de hypermoderne additieve productietechniek (3D metaalprinten) in voor een onconventionele voorwielophanging die een aanzienlijke voorsprong op de tegenstanders geeft.
Achtergrond
De motorfietsen waarmee gereden wordt in de MotoGP wereldkampioenschappen zijn speciaal. Het publiek kan ze niet kopen en ze zijn niet op de openbare weg te gebruiken. Als prototype-racemotoren worden ze op maat gebouwd om hun rivalen te verslaan en maximale prestaties op het circuit te leveren.
Moto2, de tweede van de drie MotoGP klassen, werd gestart in 2010. De officiële motor is een 600 cc viertakt productiemotor, momenteel van Honda. Het Franse Moto2 team TransFIORmers, met als thuisbasis Perigueux in Zuidwest-Frankrijk, ontwierp een revolutionaire voorwielophanging om de andere deelnemers voor te blijven.
TransFIORmers wordt geleid door voormalig coureur in het 250 cc wereldkampioenschap Christian Boudinot, en het onconventionele ophangingsysteem van het team was geïnspireerd op voorafgaand werk van de legendarische Franse motorfietsontwerper Claude Fior.
Fior, indertijd vriend en mentor van Boudinot, herkende de winst die te behalen was door de voorwielophanging te isoleren van de stuurkrachten. Het ontwerp pakt het 'duiken' bij remmen aan en maakt zo later remmen in de bocht en sneller er uit accelereren mogelijk.
In plaats van wielophanging met een traditionele telescopische voorvork maakt de motorfiets van TransFIORmers gebruik van een starre voorvork die via twee driehoekige armen van het frame gescheiden is.
Om het innovatieve ontwerp nog geavanceerder te maken, benaderde TransFIORmers het bedrijf I3D Concept, expert van wereldklasse in ontwerp en uitvoering van additief produceren in metaal.
Met gebruik van het Renishaw AM250 additief productiesysteem werkte I3D Concept als partner samen met het TransFIORmers team om het ontwerp te optimaliseren van de bovenste driehoekige arm, één van de twee waarmee de voorvork vastzit aan het frame en een kritisch onderdeel voor de besturing van de motor.
Uitdaging
Bij het ontwikkelen van nieuwe onderdelen voor een Moto2 motorfiets is gewichtsbesparing een prioriteit. Vooral het terugbrengen van het 'onafgeveerde gewicht' van de motor is een belangrijke overweging. Hoe lager het onafgeveerde gewicht, des te beter is de wielophanging wat betreft trillingbeheersing en responsiviteit op remmen en accelereren.
Net zo belangrijk is de snelheid waarmee het ontwerp van een nieuw onderdeel kan worden gewijzigd, en hoe lang het duurt om het opnieuw te fabriceren. Perfectie bereiken in een zeer competitieve omgeving vereist snelle nauwkeurige constante kwaliteit.
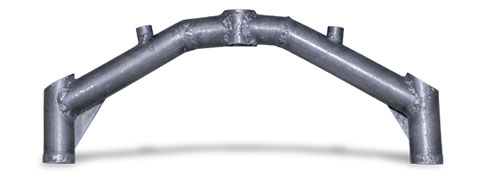
Oorspronkelijk twaalfdelig onderdeel
In een omgeving van hoge betrouwbaarheid is ook mechanische sterkte een voorname overweging. De driehoekige arm van TransFIORmers moet de hoogst mogelijke starheid garanderen, en daarbij behoorlijk hoge dynamische stuurkrachten kunnen weerstaan.
"Om de algehele prestaties van de motorfiets te verbeteren, is het essentieel om het gewicht van alle onderdelen voorbij de schokdempers te verlagen. Als je de gewichten van de onderdelen niet optimaliseert, kan dat nadelig uitwerken op trillingen, remmen en accelereren, dus gewichtsverlaging heeft echt hoge prioriteit", vertelt Jérôme Aldeguer van TransFIORmers.
De gewichtsbesparing die 3D metaalprinten ons bracht in onze driehoekige arm stelde ons in staat om de traditionele gewichtsverplaatsing en de problemen die ontstaan door 'duiken' bij het remmen te vermijden. Het is ons zelfs gelukt om een onderdeel te ontwerpen dat niet alleen lichter is maar ook een veel hogere stijfheid heeft.
TransFIORmers (Frankrijk)
Oplossing
De originele driehoekige arm van TransFIORmers was met de hand gemaakt van staal en bevatte bij elkaar twaalf apart bewerkte en gelaste onderdelen. I3D Concept paste het ontwerp aan naar één enkel onderdeel, waardoor de assemblagetijd enorm verkort werd.
Het bedrijf maakte de 3D metaalgeprinte driehoekige arm met behulp van een Renishaw AM250 additief productiesysteem; eerst als prototype in roestvast staal (rvs) en uiteindelijk als lichtgewicht onderdeel van titanium.
Een sleutelrol in het nieuwe 3D productontwerp speelde een iteratief proces van topologische optimalisatie, waarin het armontwerp in software gerationaliseerd werd binnen krappe ruimtelijke beperkingen om een aantal voorgedefinieerde situaties van voorvorkbelasting te kunnen weerstaan.
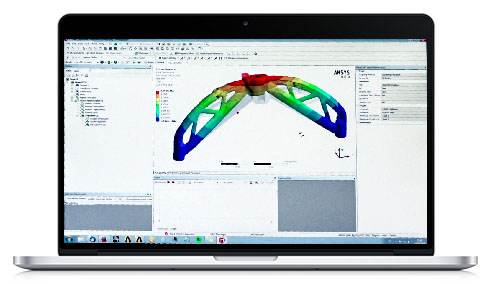
CAD-software
Nadat het uiteindelijke productontwerp gevalideerd was met behulp van CAD-software, werd offline het bestand voor de bouwvoorbereiding gemaakt en vervolgens geëxporteerd naar het additief productiesysteem.
Met de CAD-software kon I3D Concept vaststellen of de parameters vooraf effectief waren bepaald of nog wijzigingen nodig hadden om te passen bij de specifieke eigenschappen van het metaalpoeder en bij de complexe geometrie die de TransFIORmers arm moest krijgen.
Belangrijk was ook dat I3D Concept met de speciale optische controlesoftware (OCS) van de AM250 in staat was om de laser zeer nauwkeurig te sturen, wat meehielp om de precisie, detaildefinitie en oppervlaktekwaliteit te verbeteren.
Resultaten
Door een Moto2 motorfietsontwerp te benaderen vanuit additief produceren, is TransFIORmers erin geslaagd om het gewicht van de driehoekige arm die kritisch is binnen de voorwielophanging te verlagen met maar liefst 40%. Vergeleken met de oorspronkelijke gelaste stalen versie weegt het titanium onderdeel uit één stuk 600 gram minder.
3D metaalgeprint titanium onderdeel uit één stuk
3D metaalprinten gaf TransFIORmers ook een veel fijnere controle over de toleranties van onderdelen en de flexibiliteit om armgeometrieën zeer snel te produceren voor specifieke frame- en kinematische eisen.
"De gewichtsbesparing die 3D metaalprinten ons bracht in onze driehoekige arm stelde ons in staat om de traditionele gewichtsverplaatsing en de problemen die ontstaan door 'duiken' bij het remmen te vermijden. Het is ons zelfs gelukt om een onderdeel te ontwerpen dat niet alleen lichter is maar ook een veel hogere stijfheid heeft", legt Jérôme Aldeguer van TransFIORmers uit.
Met een treksterkte van meer dan 1100 MPa bij verwerking voor additief produceren en een vrijwel perfecte dichtheid van 99,7% heeft de gebruikte Ti6AI4V titaniumlegering een totaal nieuwe driehoekige arm opgeleverd, die een veel hogere stijfheid biedt dan het oorspronkelijke uit meerdere delen handmatig samengestelde stalen onderdeel.
Dankzij additieve productie is de ontwikkeling van een prototype-arm door TransFIORmers een uiterst efficiënt proces met lagere kosten geworden. Uitgebreide bewerkingen en extra tijd voor het monteren zijn niet meer nodig, en ontwerpiteraties en productie zijn vele malen sneller geworden.
In juni 2016 won het team bij de CEV races in Barcelona zijn allereerste Moto2 GP race.