Al momento, questa pagina non è disponibile nella lingua scelta. È possibile visualizzare una traduzione automatica realizzata con Google Translate. Renishaw declina qualsiasi responsabilità relativa alla fornitura di tale servizio e specifica di non avere controllato la traduzione.
È possibile contattarci per richiedere ulteriore assistenza.
Streamlining additive manufacturing for spinal implants
Global engineering company, Renishaw, collaborated with two innovative technology companies to demonstrate the capability of metal additive manufacturing (AM) technology to produce lightweight spinal implants that mimic the mechanical properties of bone. As part of the project, manufacturing research organisation Irish Manufacturing Research (IMR) designed and manufactured a series of representative spinal implants. IMR designed the implants using software from nTopology and produced them on a Renishaw RenAM 500M metal AM system.
Background
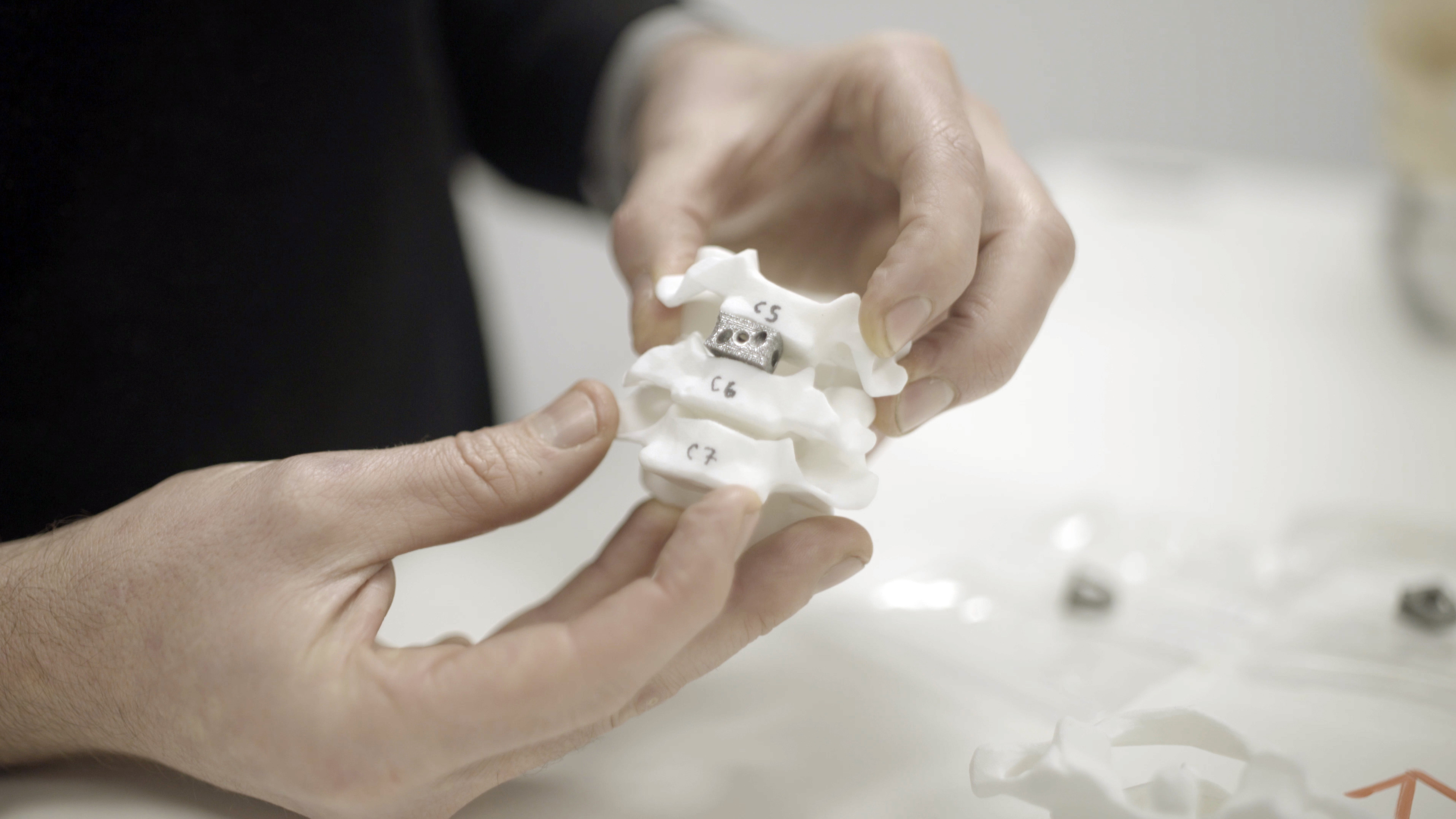
IMR, based in Dublin, provides Irish manufacturing companies with the support they need to become ready for the next generation of digital manufacturing. Medical device production is a prevalent industry in Ireland and IMR works with a variety of companies to investigate what can be achieved with 3D printed medical devices.
nTopology is an industry leading generative design company based in New York and has developed next generation design engineering software for advanced manufacturing. nTopology's unique software platform enables the creation of complex, performance-driven designs that fully exploit the capabilities of additive manufacturing.
These advanced designs can be created in minutes instead of hours or days. nTopology's platform enables engineering workflows, manufacturing processes and knowledge to be captured within the software to enable users to create custom workflows to meet their exact requirements.
Spinal implants are needed to restore intervertebral height in patients with a range of medical conditions including degenerative disc disease, herniated disc, spondylolisthesis, spinal stenosis and osteoporosis.
Thanks to all the support we have received from Renishaw developing spinal implants as well as working on other projects, we have up-skilled our staff and are now well established in the AM space.
Renishaw worked tirelessly with us on improving the AM process for producing the spinal implants. Together, we designed a set of experiments that yield the most appropriate parameter settings for the product. As a result, we reduced the amount of post-processing required on key features by a factor of ten.
Irish Manufacturing Research (IMR) (Republic of Ireland)
Challenge
Conventional manufacturing techniques are unable to produce spinal implants with a lattice structure, which offers a high surface area to encourage migration of osteoblasts into the implant and the ability to optimise the mechanical properties of a porous volume to meet the required loading conditions.
IMR identified metal AM as a suitable method to manufacture lattice structures optimised for osseointegration. However, the most suitable design software and AM machines had to be identified.
“The capabilities of AM hardware have developed fast and are now outpacing traditional design tool capabilities,” explained Duann Scott, nTopology's Director of Business Development and Partnerships. “nTopology was established in 2015 when the founder realised there was no software that could design the complex geometries AM was capable of producing.
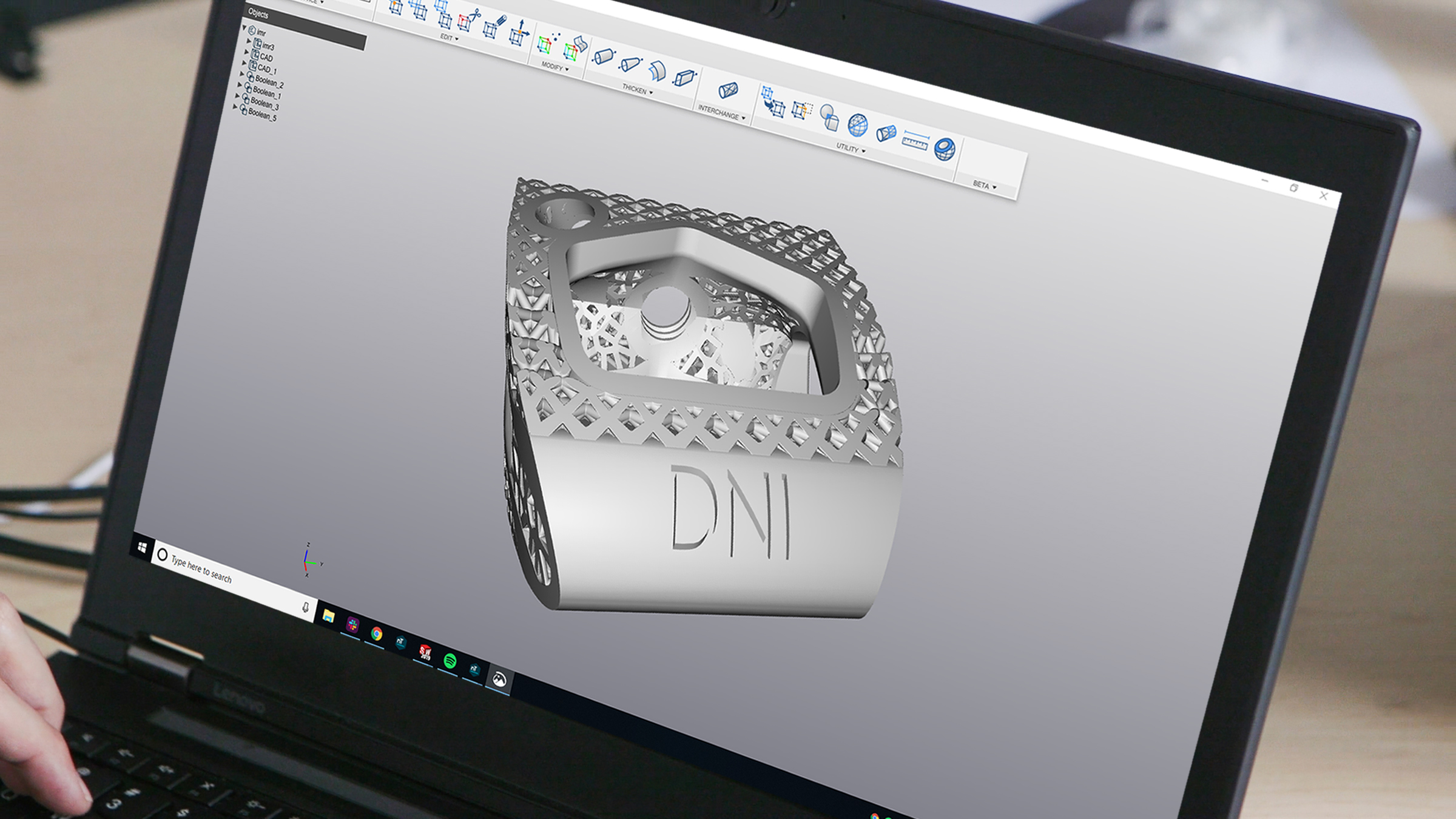
“To allow a smooth AM workflow from design to manufacture, hardware and design software need to communicate effectively,” Scott continued. “Easy translation from design software to an AM machine is especially important when producing spinal implants, because intermediary stages and information transfer provide opportunities for errors and inconsistencies to occur.”
Solution
Renishaw, IMR and nTopology joined forces to produce implants for the cervical spine (c spine) that incorporate lattice structures using AM. The project name for the implant type being Anterior, Cervical, Interbody Device, or ACID.
First, IMR created a design envelope to identify the unique opportunities presented by AM to improve patient outcomes. nTopology then provided the software needed to design the complex geometry of the spinal implants and Renishaw's RenAM 500M machine was used to manufacture the implants using AM.
IMR conducted extensive research to identify the appropriate dimensions for the specified case and the loading conditions the implants must withstand in day to day life. And also in extreme situations such as running or jumping. This data was combined with the known material properties of bone in patients with diseases known to create the need for a spinal implant. The three companies then worked together to design the mechanical characteristics of the device, which are largely a function of the geometry of the unit cells used in the lattice structure, to achieve mechanical properties closer to those of human bone and to optimise the porous lattice for osseointegration.
Once the design parameters for the implants were decided, IMR produced the design files using nTop Platform. nTopology and Renishaw worked together closely to ensure their products were compatible, so that a design could be seamlessly translated from the nTop Platform to the RenAM 500M.
IMR then used the RenAM 500M to produce prototypes from grade 23 titanium (Ti 6Al-4V ELI).
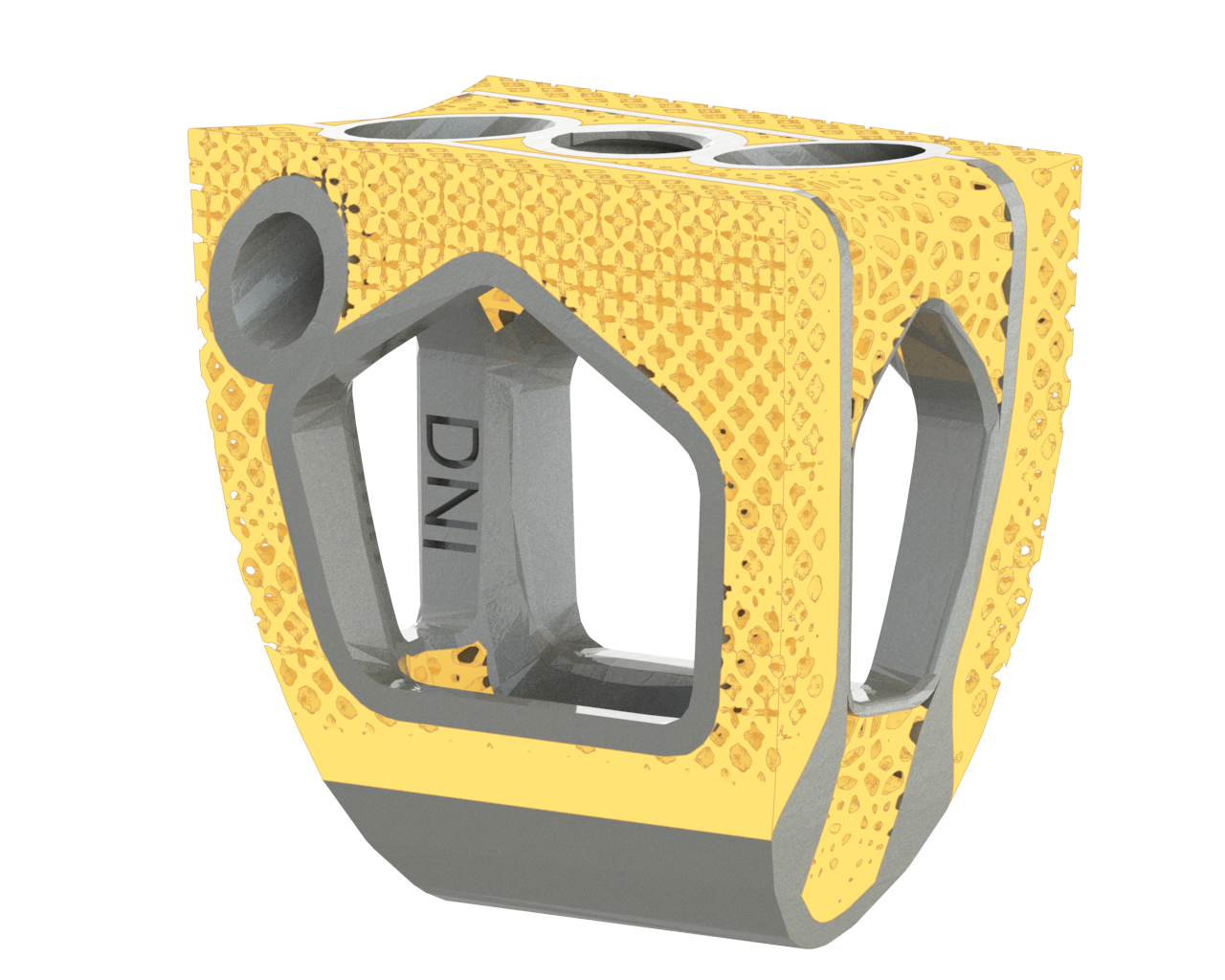
The company performed a series of tests to demonstrate the device met the most relevant elements of the standard specifications required by the FDA. Chemical properties were tested to ensure they met ASTM F136 and ASTM F3302, the standard specification for wrought grade 23 titanium to be used in orthopaedic implants and the standard specification for the additive manufacturing of titanium alloys by powder bed fusion respectively. The mechanical properties of the porous structure were characterised per ISO 13314, a test method used to determine the compressive properties and failure mode of a porous metallic material. Finally, testing ensured compliance with ASTM 1104 and ASTM 1147, standard test methods to demonstrate that porous structures do not delaminate from the solid faces of the device.
“To demonstrate proof of concept, we built witness coupons on the RenAM 500M build plate and performed destructive testing of the coupons,” explained Sean McConnell, Senior Research Engineer at IMR. “We did this to ascertain the chemical, metallurgical, and mechanical properties of the implants.”
Results
This proof of concept study demonstrated that AM can be used to produce spinal implants with characteristics that are not possible to achieve with conventional manufacturing methods. The RenAM 500M was used for manufacturing both the prototypes and the final implants, so the procedure did not have to be translated for different machines. This streamlined workflow will result in considerable cost and time savings for medical device manufacturers.
“Two years ago, AM in IMR was non-existent,” explained McConnell. “Thanks to all the support we have received from Renishaw developing spinal implants as well as working on other projects, we have up-skilled our staff and are now well established in the AM space.
“We have been able to pass the knowledge about AM gained from Renishaw to our customers,” added McConnell. “We are working with companies who were previously fearful of the risks associated with the AM knowledge gap but are now building their confidence using AM equipment.
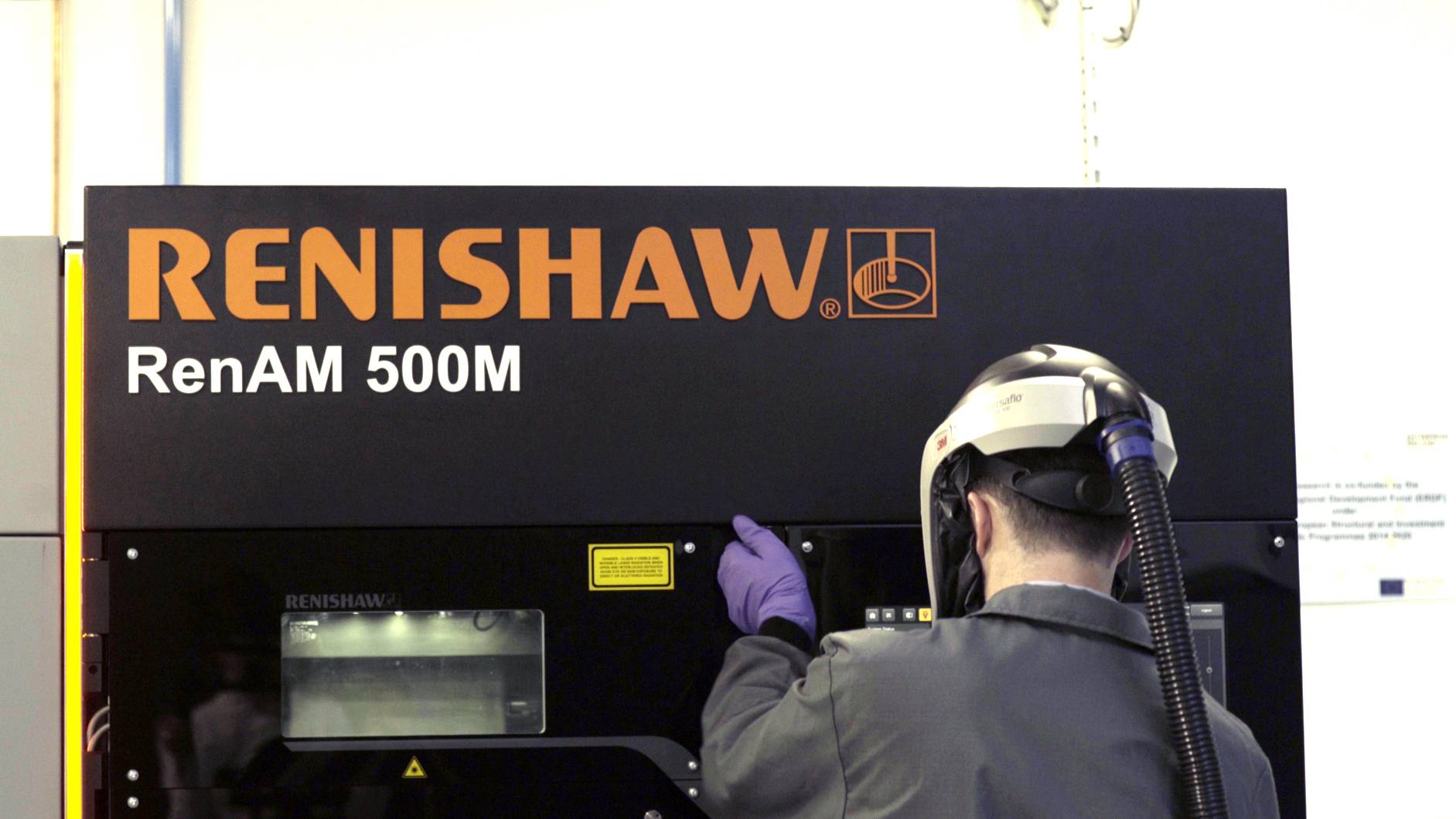
“Renishaw worked tirelessly with us on improving the AM process for producing the spinal implants,” continued McConnell. “Together, we designed a set of experiments that yield the most appropriate parameter settings for the product. As a result, we reduced the amount of post-processing required on key features by a factor of ten.”
“IMR is instrumental in bringing advanced manufacturing technology to the Irish industry,” explained Ed Littlewood, Marketing Manager of Renishaw's Medical and Dental Products Division. “The company's design expertise and research rigour enabled the production of representative spinal implants that demonstrate the potential of AM to transform healthcare.”
As well as demonstrating the ability of AM to produce spinal implants, this study shows that by considering design for additive manufacturing (DfAM) at the early stages it is possible to reduce reliance on supports and hence reduce finishing operations.
“The spinal implants project allowed us to develop our understanding of medical device production and the capabilities of AM machines,” explained Scott. “This enabled us to develop our design software so that it can be used to drive the use of advanced manufacturing technology for medical devices.
“There was a considerable amount of trial and error involved in adapting the software to align with the requirements of the RenAM 500M,” added Scott. “However, Renishaw's engineers made the entire process smooth and efficient. Projects like this usually take years, but the excellent collaboration between nTopology, Renishaw and IMR meant that we could complete the study in a matter of months.
“We will continue to work closely with Renishaw to ensure companies can access AM technology. We want to encourage wider collaboration in the advanced manufacturing industry,” concluded Scott.