Al momento, questa pagina non è disponibile nella lingua scelta. È possibile visualizzare una traduzione automatica realizzata con Google Translate. Renishaw declina qualsiasi responsabilità relativa alla fornitura di tale servizio e specifica di non avere controllato la traduzione.
È possibile contattarci per richiedere ulteriore assistenza.
Project MARCH builds exoskeleton to aid mobility for people with spinal cord injuries
Background
Worldwide, between 250,000 and 500,000 people suffer a spinal cord injury every year. A spinal cord injury (SCI) typically causes paralysis in either the lower extremities (paraplegia) or throughout the body (quadriplegia). People with a spinal cord injury often use a wheelchair as an assistive device for mobility.
Project MARCH is a non-profit, multi-disciplinary student team from the Delft University of Technology in the Netherlands. Its goal is to develop and build advanced prototype exoskeletons that enable people with SCI to stand up and walk.
The team also compete in a quadrennial sporting competition for bionic para-athletes called the ‘Cybathlon' and a smaller annual spin-off event called the ‘Cybathlon Experience'. The purpose of these international competitions is to accelerate the development of human prosthetics, advanced wheelchairs and exoskeleton technology, in order to improve the daily lives of people with physical disabilities.
Martine Keulen, Partnerships & PR for Project March, explains: “Every year, a new multi-disciplinary team of students pause their studies for a year to design their own prototype exoskeleton. We do this in collaboration with a ‘pilot'—someone who has a complete spinal cord injury (paraplegia)— who controls the exoskeleton. The pilot is a wheelchair user, but once they are in the exoskeleton, they can control the exoskeleton to stand up, walk and tackle other kinds of obstacles.”
“The Cybathlon is a competition for para-athletes who use technical assistive devices. Participants compete in an event such as a power-wheelchair race or a mind-control competition. We [Project MARCH] compete in the powered exoskeleton race which is an obstacle course where there are six obstacles lined up, one behind the other, and you must complete all the obstacles and do it as fast as possible in under 10 minutes.”
Renishaw and RLS, a Renishaw associate company, have sponsored Project MARCH since the team was founded in 2015 and provide RLS magnetic encoders for joint motor position feedback.
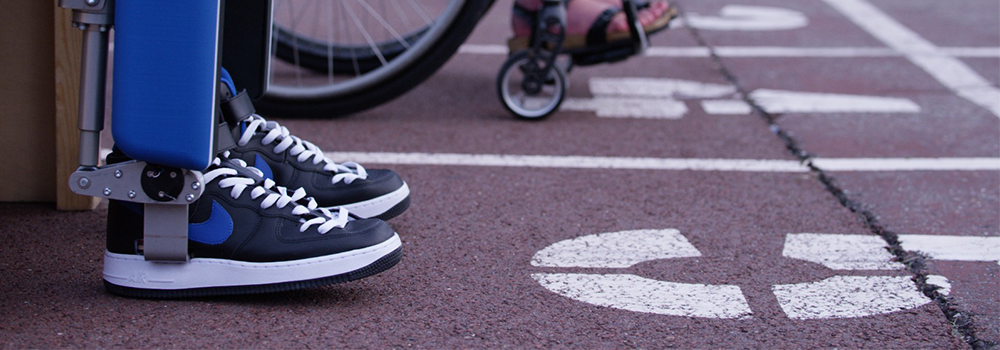
Project MARCH IVc exoskeleton and conventional wheelchair on the starting line
Challenge
Exoskeletons, designed to assist people with their mobility, are in close contact with the body and their performance is influenced by many factors, including mechanical structure, actuators and feedback devices, as well as the human-machine interaction.
Control laws for such a complex system are difficult to devise. In this case, a closed loop system, consisting of the pilot and exoskeleton, is used to track controller-generated joint reference trajectories. Project MARCH initially experimented with standard proportional-integral-derivative (PID) controllers as Björn Minderman, team 2019-2020 Embedded Systems Engineer, explains:
“At the beginning of our year, we were using a standard PID controller for the position of the joints. Over time, we saw that it did not give the results we desired. So, our control engineers decided to switch to a torque-based control. The hard part of the control is that for different walking patterns or gaits, you must use a different tuning of your PID controller. For example: when you walk up the stairs, you must deliver a lot of torque; therefore, you need stiff servo control and a high P [proportional] value. Whereas, when you are sitting down on a sofa, a high controller P-value will result in an unstable system. That is a big challenge.”
The exoskeleton pilot must preselect the type of movement required for each task via a human-machine-interface (HMI) embedded in a crutch. These movement patterns are created offline (by movement engineers in the team) and customised for each obstacle. Precise control of joint angle is required to ensure pilot stability and safety, and this is achieved by using position feedback from high quality rotary encoders.
“Another challenge is that we measure near to motors and this can generate electrical noise. The motors used in our exoskeleton create strong magnetic fields that come close to the electronics. If you have wires in their vicinity, signal noise can occur. It is a challenge to reliably transfer the data from an encoder to the CPU, without losing any data,” Mr Minderman adds.
Solution
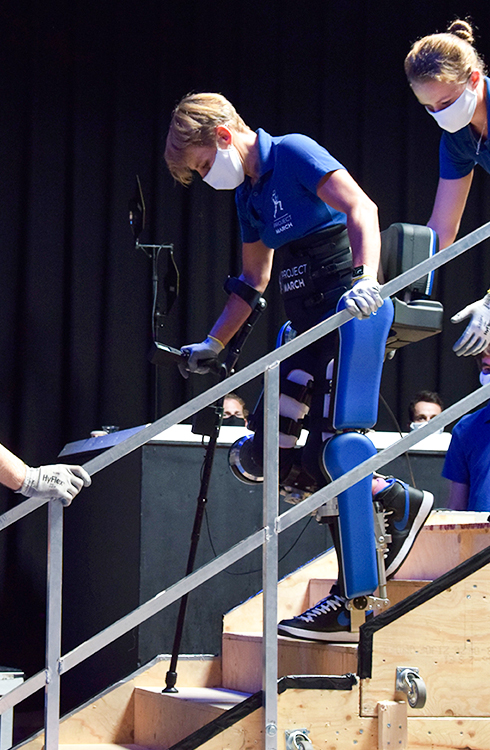
Project MARCH competes in the run-up to Cybathlon 2020
In August 2020, the team launched its latest ‘MARCH IVc' exoskeleton which uses both rotational joints in the hips and knees, and four linear joints (linear-rotary joints) in the hips and ankles. This combination of powered joints mimics a human musculoskeletal system and provides additional degrees of freedom that enable the implementation of more advanced gaits.
Mr Minderman highlights the important role of position encoders in this system:
“We have eight joints in our exoskeleton. We have one for each ankle, one for each knee and two for each of the hips. And each joint makes use of two encoders. So, the joint motor spins and, through a reduction gear, the spinning of the motor is converted into a joint angle. We use absolute encoders to measure the joint angles directly, so we always know the joint position at start-up without having to perform a calibration sequence. It is essential that we are sure that each joint is in the right position and follows the trajectory designed by our movement engineers.”
“We also have another encoder on the motor and, because the motor is spinning faster than the joints, this gives us a higher resolution which is good for control purposes. The motor encoder is mainly used in the control loop and the joint encoder is used as an extra safety measure. The encoder resolution is important for control and we previously had some issues computing the speed from the position. Since you differentiate the encoder signal, you will amplify the position measurement errors and that is why a high resolution is required.”, continues Mr Minderman.
The MARCH IVc exoskeleton integrates the new RLS AksIM‑2 absolute encoder for high-resolution (17-bit) rotational joint feedback and the miniature RLS RM08 absolute rotary encoder for linear joint feedback.
Renishaw and RLS did not try to sell us something we did not need. They thought about what it is that we needed and how they could help us with that. That level of interest in our project is, for me, what makes this collaboration so great.
Project MARCH (The Netherlands)
Results
The continued support of Renishaw and RLS has enabled successive Project MARCH teams to build new prototype exoskeletons that push the boundaries of what is possible. But how will this exciting technology evolve in the run-up to Cybathlon 2024?
“I hope that, by then, we will have begun to balance our exoskeleton without the need for crutches. This means that we are going to look for another form of input that will enable the exoskeleton to autonomously detect obstacles such as the stairs, and even measure the riser height to adapt its walking gait accordingly. These are difficult challenges that I would personally find interesting to tackle, but every year a new Project MARCH team is assembled, and it will be up to the teams to decide what developments take place. We shall have to see how far we get in the coming years. These are our aims and we hope to make as much progress as we can,” says Mr Minderman.
RLS and Renishaw collaborate directly with customers to offer the best metrology solutions for their applications as Ms Keulen observed:
“At the beginning of the year, we had a meeting with Renishaw's sales engineer, Rene Van der Slot, and Björn and the rest of the electrical department. Rene did not simply bring us the encoders and say ‘well, you should use this or that'. Instead, he thought about our application and asked about how our exoskeleton worked and what we needed. So, Renishaw and RLS did not try to sell us something we did not need. They thought about what it was that we needed and how they could help us with that. This level of interest in our project is, for me, what makes this collaboration so great. We know that Renishaw and RLS will think further than just the encoders; they will think about the whole design and how the encoders fit into that.”
In a tribute to the successful collaboration between Renishaw, RLS and Project MARCH; the team featured on Renishaw's Precisiebeurs 2019 trade stand in the Netherlands. During this trade fair, members of Project MARCH showcased an older prototype of the MARCH exoskeletons demonstrating a real-world application of the RLS magnetic encoders.
Renishaw and RLS look forward to supporting the triumphs of future Project MARCH teams in the Cybathlon competitions. As technology evolves, exoskeletons and other wearable robotic prostheses promise to revolutionise the lives of millions of people with disabilities.
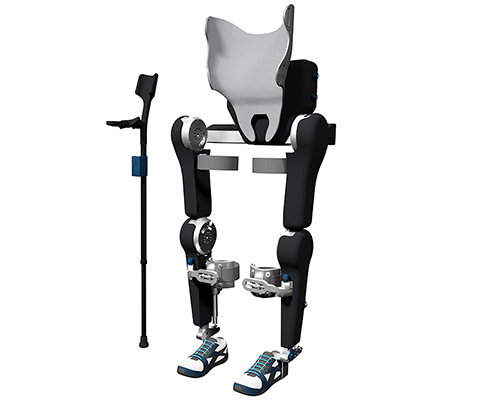
Render of March IV exoskeleton
About Project MARCH
Project MARCH is a student team from the Delft University of Technology, the Netherlands, that develops innovative and versatile exoskeletons to enable people with a spinal cord injury to stand up and walk. The current sixth team of Project MARCH consists of 26 students and continues to build on the pioneering work of its predecessors.
Every year, Project MARCH competes in the Cybathlon Experience—a competition for bionic para-athletes representing academic and commercial teams from around the world.
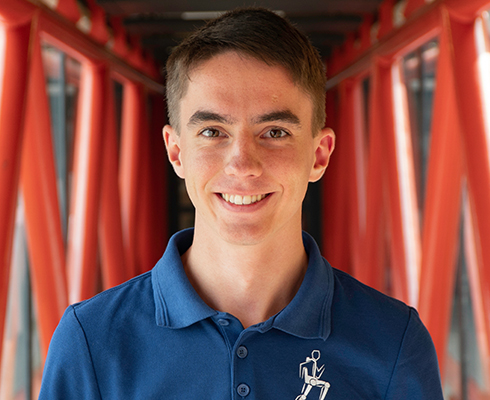
Björn Minderman, team 2019-2020 Embedded Systems Engineer
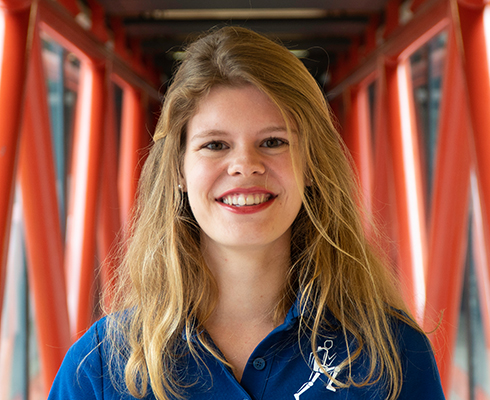
Martine Keulen, Partnerships & PR for Project MARCH
Downloads
Video courtesy of Project MARCH