La tecnologia AM di Renishaw contribuisce al successo in Formula SAE dell'auto elettrica Swinburne
Le tecnologie Renishaw di stampa 3D in metallo hanno aiutato un gruppo di studenti australiani della Swinburne University of Technology di Melbourne a ottenere il miglior piazzamento di sempre nelle gare di Formula SAE.
Il team ha conquistato il sesto posto finale, che rappresenta il risultato migliore mai raggiunto dagli studenti di questa università, inoltre durante le prove in pista l'auto ha fatto registrare alcuni dei tempi migliori in assoluto.
Background
La Formula SAE è una competizione organizzata dalla sezione australiana della Society of Automotive Engineers e prevede che gruppi di studenti producano un prototipo di monoposto da presentare a un'ipotetica azienda per la realizzazione. Successivamente, le auto vengono portate in pista e sottoposte a una serie di test. Oltre che per le caratteristiche tecniche, le auto vengono giudicate anche in base al design, al rapporto costo/efficienza e a una presentazione di marketing relativa al progetto.
Il programma non serve solo a fornire agli studenti esperienza pratica, ma offre anche l'opportunità di partecipare a un lavoro di gruppo, all'interno di un team multidisciplinare, con l'obiettivo di produrre una vettura da gara quanto più competitiva possibile. Le capacità delle squadre vengono testate fino al limite perché sono richiesti metodi di lavorazione innovativi e affidabili.
Il team di Swinburne è composto da studenti di ingegneria, design ed economia, che collaborano alle fasi di progettazione, costruzione, marketing e guida del veicolo creato.Nel 2010, l'università è stata la prima a presentare un veicolo elettrico. Da quell'anno in poi, tutte le vetture portate in gara hanno sfruttato motori elettrici.
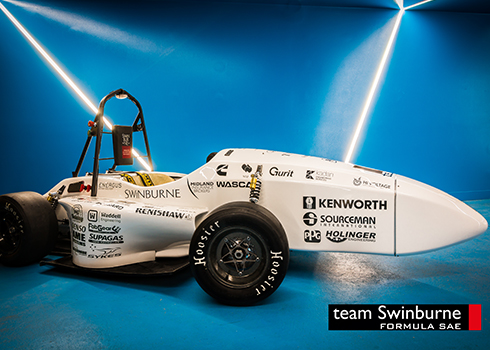
La sfida
Il problema principale che si affronta quando si porta un'auto elettrica a competere contro vetture a benzina è il peso delle batterie. Per compensare questo svantaggio e rendere la monoposto competitiva, è indispensabile ridurre al minimo il peso di tutti gli altri componenti. Per tale ragione, il Team Swinburne è alla costante ricerca di soluzioni creative per alleggerire la struttura ed è una delle poche squadre ad utilizzare un telaio in fibra di carbonio, costruito direttamente all’interno dell'università.
Dopo la competizione del 2015, il team ha svolto una serie di calcoli dettagliati per determinare l'energia consumata dalla vettura durante le varie prove.
Una delle scoperte più interessanti riguardava il fatto che l'inerzia di rotazione delle ruote durante le fasi di accelerazione e frenata richiedeva più energia del previsto.
A Ryan Wise, il responsabile della divisione Dynamics del Team Swinburne, venne quindi affidato l'incarico di ridurre il peso delle ruote e, di conseguenza, l'inerzia di rotazione. Inoltre, ruote più leggere avrebbero migliorato le prestazioni in accelerazione e frenata e la risposta delle sospensioni. Ryan aveva già fatto parte del team nelle competizioni del 2014 e 2015 e per la vettura del 2016 aveva ricevuto il compito di occuparsi di sospensioni, ruote, freni e volante.
Una delle cose che ho apprezzato di più dei macchinari AM Renishaw è stata la possibilità di aumentare gradualmente la complessità del mio progetto.
Swinburne University of Technology - Formula SAE (Australia)
Soluzione
L'idea di ricorrere all’additive manufacturing venne proposta all'interno del Team Swinburne da un collega di Ryan che aveva effettuato una ricerca sui nuovi materiali e sulle tecnologie innovative utilizzate nel campionato di Formula Student europeo. Dopo aver notato che alcuni team europei si erano affidati alle tecnologie Renishaw, il collega suggerì di contattare l'azienda.
Ryan si presentò quindi nella sede australiana di Renishaw con una ruota presa dal modello del 2015, che includeva un centro ruota e una fascia in lega di alluminio. Ryan produsse quindi una serie di progetti, sostituendo i centri ruota in alluminio con parti più piccole in lega di titanio, prodotte tramite lavorazione additiva.
Il nuovo progetto prevedeva anche l'uso di una fascia in fibra di carbonio al posto del precedente pezzo in alluminio, per ridurre ulteriormente il peso complessivo.
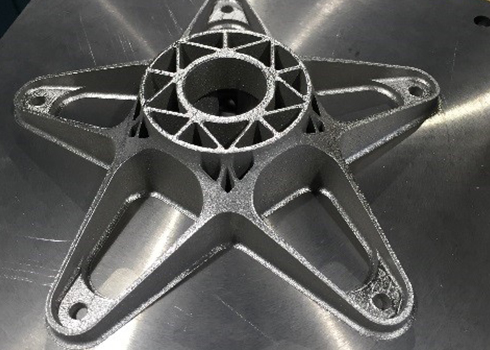
Lo staff di Renishaw fornì una serie di consigli per l'ottimizzazione del design in funzione della lavorazione additiva, fino ad arrivare a un progetto finale che mise tutti d'accordo.
Durante la fase di sviluppo vennero eseguite diverse simulazioni FEA (finite element analysis) per avere un'idea delle prestazioni del nuovo componente e per valutare a fondo tutti i possibili vantaggi.
"Una delle cose che ho più apprezzato dei macchinari AM di Renishaw è stata la possibilità di aumentare gradualmente la complessità del mio progetto", ha dichiarato Ryan.
"In precedenza avevo progettato pezzi da produrre con metodi di lavorazione tradizionale e in quei casi dovevo prestare molta attenzione alle dimensioni e alle forme degli utensili da taglio disponibili, nonché ai tempi aggiuntivi di lavorazione richiesti da alcuni elementi particolari del progetto. Grazie alla stampa 3D in metallo, ho potuto aggiungere alle ruote una serie di dettagli che difficilmente sarebbero stati ottenibili con lavorazioni sottrattive, senza incidere in alcun modo sul tempo ciclo".
Una volta finalizzato il progetto, Renishaw Oceania ha prodotto nove centri ruote, in modo da fornire al Team Swinburne due treni completi più una ruota supplementare per i test. Il gruppo ruota è stato progettato in modo che i componenti in titanio richiedessero un intervento di post-processing minimo. Dopo la loro rimozione dal sistema AM, i pezzi sono stati messi in un forno a vuoto per ridurre le tensioni residue e quindi estratti dalla piastra di costruzione mediante elettroerosione a filo e successivamente sottoposti a sabbiatura. Non sono state necessarie ulteriori operazioni di post-processing o lavorazione.
Risultati
Il nuovo design, con i componenti in titanio in sostituzione di quelli in alluminio e una fascia più larga in fibra di carbonio, hanno permesso di alleggerire ciascuna ruota del 20%, portando a una riduzione del 75% dell'inerzia di rotazione e a prestazioni in accelerazione e frenata decisamente superiori. I centri ruota prodotti tramite AM hanno inoltre contribuito ad alleggerire il peso di ogni ruota di 1 kg, senza compromettere la stabilità e la sicurezza del veicolo, come dimostrato dalle prove su pista.
Un vantaggio importante dato dall'utilizzo di tecnologie di stampa 3D Renishaw è stata la possibilità di produrre pezzi in titanio. "La quantità di materiale necessario per la billetta, i tempi necessari per la lavorazione e il livello di esperienza richiesto ci avevano impedito di utilizzare questo metallo con i metodi produttivi tradizionali" ha spiegato Ryan.
"La stampa dei componenti non ha richiesto un grande sforzo e i tempi di produzione sono stati decisamente inferiori rispetto ai centri ruota che avevamo creato in precedenza. Sono rimasto sorpreso per la qualità delle finiture delle superfici e per il fatto che i pezzi non hanno richiesto alcuna operazione di finitura dopo la lavorazione".
"Sono convinto che più di una persona avesse forti dubbi, perché i componenti erano incredibilmente sottili" ha aggiunto. "Ammetto che dopo aver assistito alla rottura di un centro ruota di un'altra squadra ho iniziato a temere il peggio. Invece, i nostri pezzi hanno resistito magnificamente a tutti i test. Devo dare credito a Renishaw per aver sfruttato al meglio le proprietà di questo materiale".
Oltre a fornire un valido contributo alla squadra, la cooperazione con Renishaw ha rappresentato un momento di crescita personale per Ryan. "All'inizio dell'anno non sapevo praticamente nulla delle tecnologie di produzione additiva in metallo" ha ammesso. "Non ci ho messo molto a capire che, come in tutte le tecniche produttive, anche in questo caso è indispensabile prendere in considerazione le capacità del processo durante la fase di design.
Dopo alcune sessioni di formazione presso Renishaw ho imparato in che modo funziona questa tecnologia e quali sono i problemi che si possono incontrare lungo la strada e ho iniziato a disegnare progetti facilmente attuabili.
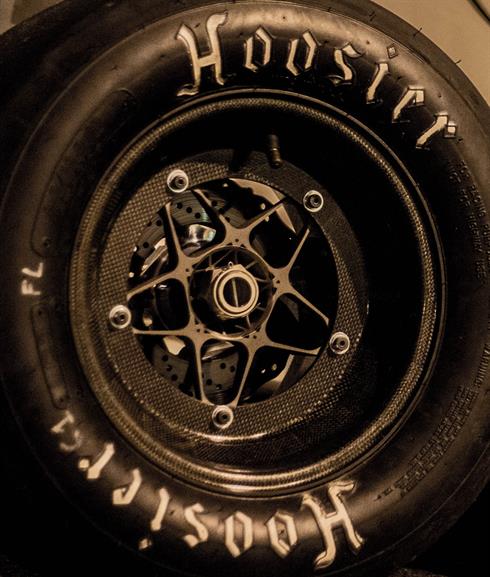
Abbiamo escogitato una serie di trucchi interessanti, come ad esempio la stampa di pellicole intorno a una struttura di lattice, in modo da ridurre il peso e limitare le sollecitazioni termiche. Una volta acquisita familiarità con il processo, la fase progettuale è risultata sorprendentemente semplice e sono riuscito a definire senza problemi un design che assicurasse leggerezza e facilità di stampa".
Ryan prevede che altri team ricorreranno alle produzioni additive durante la gara. "Ho perso il conto del numero di persone che hanno visitato il nostro box, solo per la curiosità di vedere le nostre ruote",” ha commentato. "Hanno un aspetto davvero fantastico e non ci hanno creato nessun problema. Penso che molti visitatori siano rimasti sbalorditi".
La stampa dei componenti non ha richiesto un grande sforzo e i tempi di produzione sono stati decisamente inferiori rispetto ai centri ruota che avevamo creato in precedenza. Sono rimasto sorpreso per la qualità delle finiture delle superfici e per il fatto che i pezzi non hanno richiesto alcuna operazione di finitura dopo la lavorazione.
Swinburne University of Technology - Formula SAE (Australia)
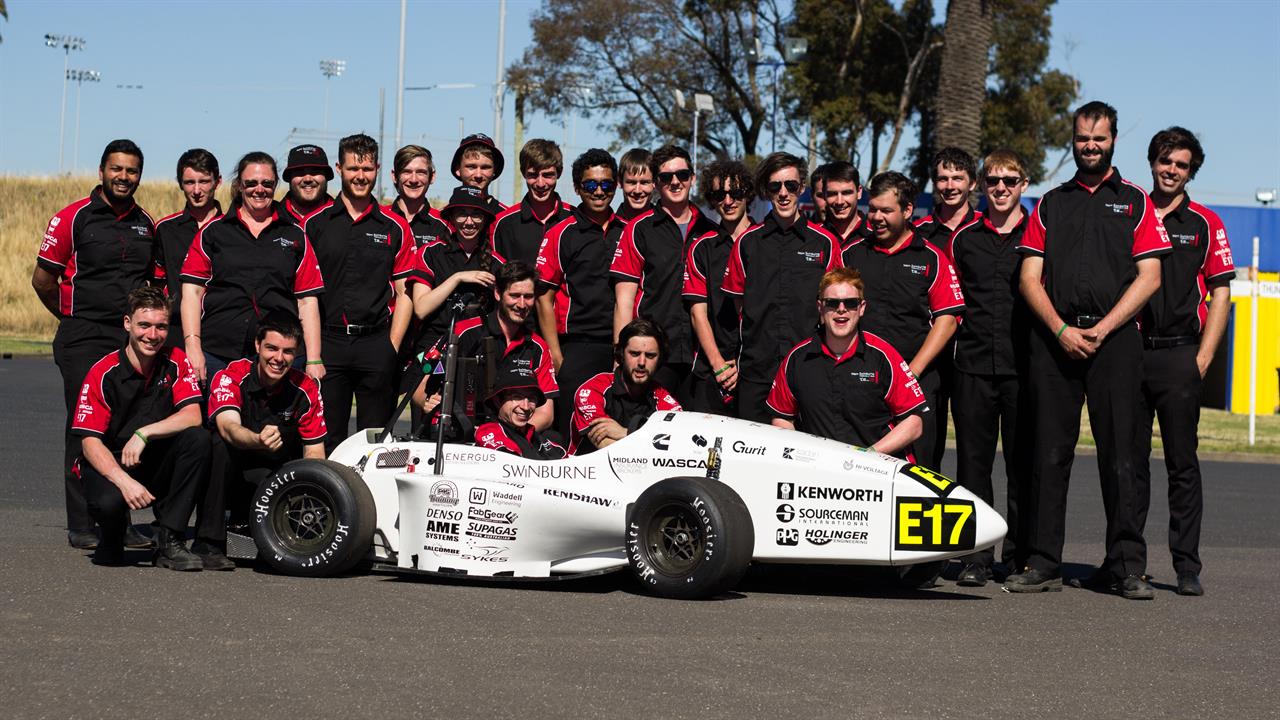