Il sistema di calibrazione multi-asse XM-60 riduce notevolmente il tempo richiesto per misurare gli errori di precisione volumetrica
Background
Ci sono molti elementi di cui tenere conto per misurare gli errori di precisione volumetrica e misurarli tutti richiederebbe molto tempo. Ad esempio, ci sono sistemi di misura della precisione volumetrica con tracker dove, al crescere delle dimensioni della macchina, il tempo richiesto per la misura cresce in maniera esponenziale.
Il Volumetric Accuracy Research Institute Co. Ltd. (VARI) è specializzato in servizi di analisi delle misure di precisione e di miglioramento dell’accuratezza di lavorazione per le linee di produzione, con un focus particolare sulla misura dell’accuratezza delle macchine utensili e sulla creazione dei relativi parametri di correzione. Tramite una collaborazione di ricerca con DMG Mori Seiki Co., Ltd. e l’Università di Kyoto, il VARI contribuisce allo sviluppo delle macchine utensili del futuro. L’istituto offre anche un servizio mirato al miglioramento dell'accuratezza delle macchine utensili tramite parametri di correzione calcolati tramite appositi algoritmi brevettati. Migliorare l’accuratezza significa migliorare il processo produttivo e quindi ridurre la necessità di rilavorazioni.
Il VARI ha come obiettivo un’accuratezza spaziale diversa dall’accuratezza geometrica convenzionale. Tradizionalmente, per valutare una macchina utensile si utilizza l’accuratezza di movimento in termini di posizionamento lineare e di rettilineità. Esistono standard per l’accuratezza di movimento, come ISO 230-1 e JIS B 6190-1, che vengono utilizzati da molti produttori di macchine utensili per verificare l'accuratezza prima della consegna della macchina. Tuttavia, poiché gli errori di movimento interagiscono tra loro, non è facile ipotizzare l’effettiva deviazione di posizionamento della punta dell’utensile in base all’accuratezza di movimento. Per questo il VARI ha sviluppato l’idea di accuratezza spaziale, che valuta direttamente la deviazione tridimensionale di posizione rispetto a ogni posizione della punta dell’utensile.
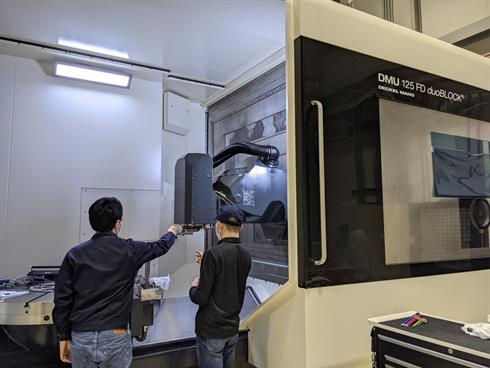
Centro di lavoro per la misura dell'accuratezza
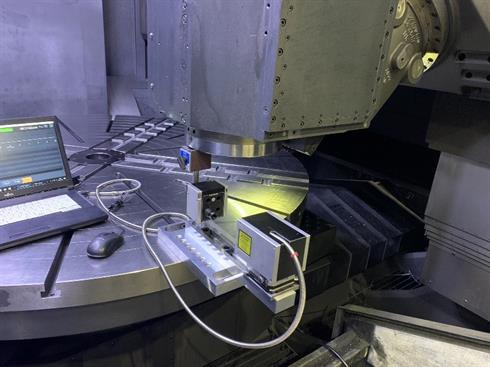
Misura dell’accuratezza di una macchina utensile con il sistema di calibrazione multi-asse XM -60
Per valutare le capacità di lavorazione di una macchina utensile, è necessario misurare gli errori su tutti gli assi della macchina. La posizione di un oggetto nello spazio è definita da sei gradi di libertà, analogamente alla relazione fra l’utensile da taglio e il pezzo da lavorare in macchina utensile. Per misurare direttamente e contemporaneamente tutti gli errori, il VARI ha introdotto nei propri processi il sistema di calibrazione multi-asse XM-60. Questo ci ha consentito di ridurre i costi di manodopera e di valutare accuratamente le prestazioni di una macchina.
Volumetric Accuracy Research Institute Co., Ltd. (Giappone)
La sfida
Gli sforzi mirati all’aumento dell’efficienza di lavorazione, alla riduzione degli scarti e alla minimizzazione dei costi rendono sempre più necessaria una migliore comprensione dei processi di lavorazione. Conoscere le prestazioni di taglio di una macchina prima della lavorazione è fondamentale per la produzione.
Quando si tratta di valutare l’accuratezza di una macchina, gli interferometri laser sono ampiamente utilizzati per la loro elevata precisione. Tuttavia, l’asse in movimento di una macchina può presentare errori non solo in termini di posizione, ma anche in termini di allineamento verticale e di rettilineità. Misurare ciascuno di questi errori presi singolarmente può richiedere molto tempo. Dal momento in cui sia le macchine che i pezzi prodotti diventano sempre più complessi, non basta più misurare le prestazioni di posizionamento ed è per questo richiesta maggiore attenzione alla fase di controllo preliminare. Durante il movimento del mandrino, gli errori di allineamento verticale e di rettilineità si verificano a causa dell'attrito e di altre influenze sulla struttura del mandrino, determinando una differenza tra la posizione indicata e quella effettiva della punta dell’utensile. Questo può causare notevoli errori in termini di posizione delle caratteristiche e conseguenti deviazioni sui contorni e sulle superfici, che rendono i pezzi prodotti fuori tolleranza.
Con il verificarsi di deviazioni sui pezzi lavorati a causa degli errori su ogni asse della macchina, è necessario misurare tutti gli errori su ogni asse per valutarne le capacità di lavorazione. La posizione di un oggetto nello spazio viene definita da sei gradi di libertà, analogamente alla relazione fra l’utensile da taglio e il pezzo da lavorare nella macchina utensile. Misurare tutti gli errori direttamente e contemporaneamente consente di ridurre il tempo di lavorazione e valutare in modo accurato le prestazioni della macchina.
Soluzione
Il sistema di calibrazione multi-asse XM-60 di Renishaw ha introdotto un concetto assolutamente innovativo per il VARI, consentendo la misurazione dei sei gradi di libertà in un unico set-up, a prescindere dalla direzione assiale. L’accuratezza della macchina utensile viene solitamente identificata misurando 21 diversi errori di movimento. Tuttavia, poiché gli errori di movimento interagiscono tra loro, non è sempre facile determinare l’effettiva deviazione della punta dell’utensile in base all’accuratezza di movimento. Una soluzione può essere quella di utilizzare la mappa degli errori di accuratezza spaziale per visualizzare la distribuzione dell’accuratezza nello spazio di lavorazione. Il Volumetric Accuracy Research Institute offre un servizio indipendente che misura l’accuratezza spaziale delle macchine utensili per creare una mappa degli errori da utilizzare per migliorare l’accuratezza complessiva.
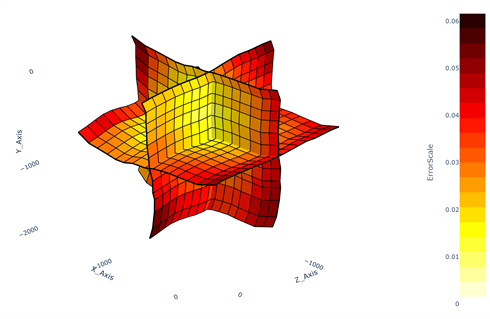
Mappa degli errori spaziali
Risultati
Utilizzare il sistema di calibrazione multi-asse XM-60 ha consentito al VARI di ridurre sostanzialmente i tempi di misura dell'accuratezza spaziale, specialmente nelle macchine più grandi. Come spiega un utilizzatore diretto, “è possibile selezionare i dati delle misure passate da un elenco e confrontare con facilità più risultati.”