I sistemi d’ispezione per macchine utensili aumentano la produttività di un’officina australiana
L’officina australiana Hammond Engineering, avendo constatato che l’impostazione manuale dei pezzi comportava un notevole dispendio di tempo ed era difficilmente ripetibile, ha valutato le potenzialità dell’ispezione in macchina. Da quando utilizza la sonda a trasmissione ottica OMP40-2 di Renishaw, l’azienda ha rilevato tempi di impostazione più rapidi e livelli di produttività più elevati.
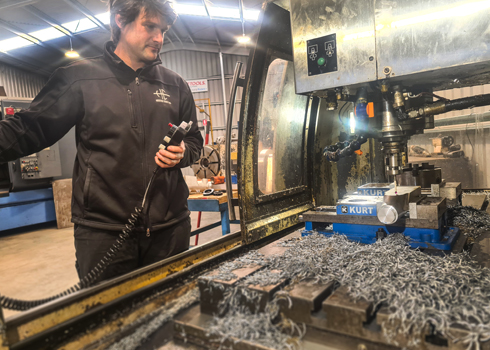
Travis Hammond, fondatore di Hammond Engineering
Background
Hammond Engineering è un’officina meccanica con sede a Bairnsdale. I suoi servizi includono la progettazione CAD, la fresatura e la tornitura per volumi di produzione che vanno dalla prototipazione alle grandi serie industriali.
“Ho fondato la Hammond Engineering per coniugare la mia passione per la lavorazione dei metalli con l’amore per l’informatica”, ha spiegato il fondatore Travis Hammond. “Dopo aver completato il mio corso avanzato da operatore CNC, mi sono procurato un tornio a controllo numerico di seconda mano e ho iniziato da lì. Oggi siamo un team di tre persone che lavorano per offrire un servizio tecnologicamente più avanzato rispetto al passato”.
L’azienda si rivolge principalmente ai clienti del settore alimentare e dei ricambi automobilistici aftermarket, ma offre anche produzione e riparazioni generali per industrie locali.
Il tempo impiegato per fare dei cambiamenti, come allineare un fissaggio o impostare un pezzo, equivale a tempo in cui la macchina non lavora. Per una ditta piccola come la nostra perdere tempo significa perdere denaro, così abbiamo cercato un modo per aumentare la produttività, ridurre i tempi di consegna e minimizzare l’errore umano.
Hammond Engineering (Australia)
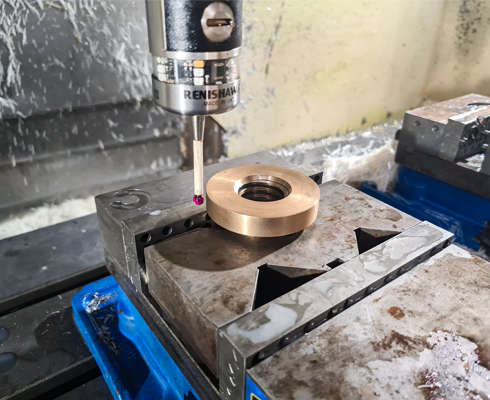
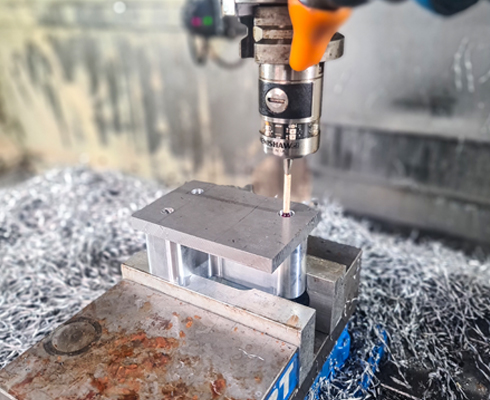
Impostazione e ispezione dei pezzi con la sonda a trasmissione ottica OMP40-2 di Renishaw
La sfida
“Quando eseguiamo un lavoro generico dobbiamo cambiare le impostazioni delle macchine diverse volte durante il giorno”, ha affermato Hammond. “Il tempo impiegato per fare dei cambiamenti, come allineare un fissaggio o impostare un pezzo, equivale a tempo in cui la macchina non lavora. Per una ditta piccola come la nostra perdere tempo significa perdere denaro, così abbiamo cercato un modo per aumentare la produttività, ridurre i tempi di consegna e minimizzare l’errore umano”.
La soluzione
“Essendo un’impresa di dimensioni molto piccole che cerca di ridurre i costi, spesso compriamo macchine di seconda mano”, ha aggiunto Hammond. “Quando abbiamo acquistato il nostro ultimo centro di lavoro, questo era dotato di una sonda Renishaw, così abbiamo iniziato a usarla per l’impostazione dei pezzi, cercando di capire se potevamo migliorare la precisione e la produttività”.
Il centro di lavoro della Hammond Engineering era dotato di una sonda OMP40-2. Questa sonda a contatto 3D ultracompatta a trasmissione ottica del segnale è utilizzata principalmente per l’impostazione e l’ispezione dei pezzi nei centri di lavoro. Ci permette di ridurre fino al 90% i tempi di impostazione, di limitare i costi di fissaggio e la quantità di scarti prodotti.
I risultati
Grazie all’utilizzo della sonda OMP40-2, Hammond Engineering ha ottenuto tempi di impostazione molto più brevi. Prima di utilizzare questo sistema, ad esempio, l’allineamento di un fissaggio richiedeva cinque minuti circa; con la nostra sonda Renishaw questa operazione richiede meno di un minuto. I benefici si sommano nel tempo, infatti l’utilizzo della sonda per le operazioni giornaliere di allineamento dei pezzi si traduce in un risparmio di ben 17 ore annue. L’uso della sonda riduce anche l’impatto dell’errore umano sulla produzione, perché può calcolare gli angoli senza l’intervento di un operatore.
“Non posso credere che mi ci sia voluto così tanto tempo per capire l’importanza dell’ispezione automatica nella mia officina” ha dichiarato Hammond. “Ora che so quanto sia accurata e semplice da usare la sonda OMP40-2, difficilmente mi lascerei convincere a utilizzare qualcos’altro”.
Hammond Engineering prevede di utilizzare la sonda OMP40-2 in futuro per la misurazione in-process, con l’obiettivo di garantirne il corretto posizionamento e allineamento dei pezzi. Inoltre, l’officina ha in programma di avvalersi della verifica dell’integrità degli utensili per migliorare l’affidabilità e la sicurezza dei processi.