I sistemi di diagnostica ballbar semplificano i processi produttivi in campo aeronautico
In mancanza di interventi periodici di verifica e manutenzione, le macchine CNC possono perdere accuratezza di posizionamento, introducendo errori nel processo produttivo. BAE Systems ha scelto di introdurre un sistema ballbar wireless nella propria linea per la lavorazione di componenti complessi dedicati al settore aeronautico, in modo da ottenere dati diagnostici per massimizzare la qualità e la produttività delle proprie macchine utensili.
Background
La produzione di componenti per le cellule dei moderni velivoli richiede la massima precisione e uniformità. I componenti degli aerei hanno un'aspettativa di vita molto lunga e pertanto la qualità e l'affidabilità sono fattori determinanti nei processi di lavorazione dei pezzi in metallo e compositi.
BAE Systems è un'azienda internazionale, specializzata nei settori aerospaziale e difesa: produce componenti fondamentali per le cellule dell'Eurofighter Typhoon, l’aereo bimotore per uso militare con ala principale a delta e alette laterali a configurazione canard. Questo agilissimo velivolo è operativo dal 2003 e viene utilizzato dai corpi di aviazione militare di molti paesi in tutto il mondo.
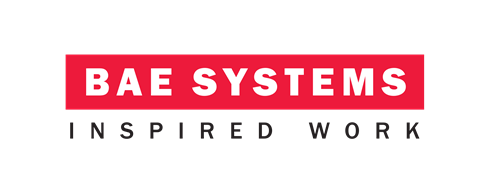
Nel modernissimo stabilimento britannico di Samlesbury Aerodrome, presso Blackburn, BAE Systems utilizza più di 80 macchine CNC per produrre un'ampia gamma di costosi componenti per cellule destinati al Typhoon e ad altri modelli di aerei.
Una delle principali responsabilità dello staff tecnico dell'azienda consiste nel massimizzare le prestazioni e la produttività delle macchine a 5 assi, in modo da garantire una qualità uniforme dei pezzi, ridurre al minimo gli scarti e accrescere al massimo l'efficienza.
In quest'ottica, le ispezioni e le calibrazioni periodiche delle macchine CNC diventano aspetti fondamentali del processo di lavorazione. In precedenza, BAE Systems aveva già utilizzato i sistemi ballbar QC10 di Renishaw per eseguire la diagnostica delle macchine e ha successivamente deciso di investire nell'acquisto di sistemi wireless di seconda generazione, che garantiscono maggiore flessibilità e facilità d'utilizzo.
Sistema ballbar QC20-W
In una macchina CNC con prestazioni di posizionamento perfette, l'interpolazione circolare, in qualsiasi combinazione di due assi, corrisponderebbe con precisione a un percorso circolare programmato. Con il sistema ballbar wireless QC20-W è possibile confrontare il percorso programmato e quello effettivo, per determinare la presenza di errori.
Il ballbar telescopico include un trasduttore lineare ad elevata accuratezza e viene posizionato fra due supporti magnetici di precisione posti uno sulla tavola della macchina, l'altro nel mandrino. Con questa configurazione, il ballbar può misurare variazioni minime del raggio mentre la macchina CNC esegue un percorso circolare programmato.
L'elaborazione del segnale viene eseguita all'interno del ballbar e i dati sono trasmessi ad un PC tramite una connessione wireless. I dati raccolti consentono di calcolare le prestazioni complessive in termini di accuratezza del posizionamento (circolarità e deviazione circolare), in conformità agli standard internazionali oppure ai report di analisi redatti da Renishaw.
Per semplificare ulteriormente la diagnosi degli errori della macchina utensile, i dati del ballbar vengono visualizzati in formato grafico e numerico. Il kit ballbar include barre di prolunga da 50, 150 e 300 mm che consentono di eseguire test diagnostici su una grandissima varietà di macchine CNC.
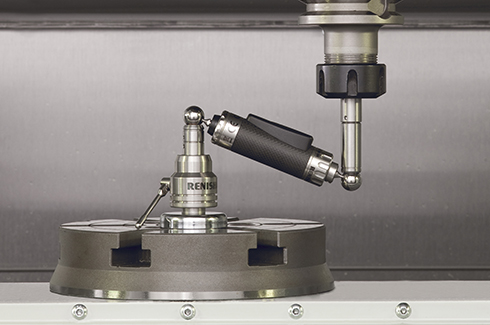
Con l'ausilio delle diagnostiche ballbar di Renishaw, una macchina CNC ritenuta inutilizzabile è stata riportata alla piena operatività e BAE Systems ha potuto trarre vantaggio dal considerevole aumento della produttività della propria officina e dalla conformità ai requisiti di QA.
BAE Systems (Regno Unito)
La sfida
A prescindere dal tipo, dalle specifiche, dal carico di lavoro e dal duty cycle, anche la migliore macchina CNC al mondo con il tempo tende a perdere accuratezza di posizionamento e a introdurre errori, a meno che non sia sottoposta a interventi regolari di manutenzione. Tanti fattori, tra cui usura, danni causati da collisioni, installazioni non corrette, presenza di vibrazioni nella base di appoggio e temperatura ambientale, possono incidere negativamente sulle prestazioni delle macchine utensili.
Scoprire la presenza di un problema solo dopo che i componenti sono stati lavorati può causare perdite economiche significative. Nel caso delle cellule per velivoli prodotte da BAE Systems, un'alta percentuale di componenti è prodotta in titanio. Questo metallo è molto resistente e leggero, con buone capacità di resistenza alle alte temperature e alla corrosione, ma sta diventando sempre più raro e prezioso e spesso le scorte vanno ordinate anche con un anno di anticipo.
Ai costi supplementari causati dagli scarti si aggiunge il tempo di lavorazione sprecato e che non può più essere recuperato.
Per la costruzione di un componente complesso in titanio sono mediamente necessarie 40 ore di lavorazione in macchina. La produzione ripetuta di pezzi sbagliati può avere un impatto molto gravoso sulla produttività della macchina.
Gli ingegneri di BAE Systems erano alle prese con una macchina utensile che nel tempo aveva perso accuratezza e stava creando molti problemi alla produzione. Preso atto dell'impossibilità di ottenere pezzi conformi alle specifiche, i tecnici stavano pensando di smantellarla e dirottare il carico di lavoro sulle altre macchine dell'officina.
Di fronte a problematiche di questa portata, è importante che le macchine CNC vengano controllate con regolarità. L'accuratezza di posizionamento è un fattore vitale per mantenere elevati i livelli di qualità e produttività.
Soluzione
Al fine di velocizzare le operazioni di diagnostica periodica delle macchine CNC, BAE Systems si avvaleva già di un sistema ballbar QC10 di Renishaw che consentiva l'identificazione di specifici errori prestazionali.
L'azienda ha successivamente deciso di adottare un ballbar wireless QC20-W di seconda generazione per dare vita a un programma di manutenzione preventiva, con controlli settimanali, mensili e annuali, che avrebbe coinvolto tutte le 60 macchine CNC dell'officina.
Grazie ai dati diagnostici prodotti dal QC20-W è stato possibile produrre un'interpretazione dettagliata dei trend che ha permesso a BAE Systems di definire un benchmark attendibile di situazioni di tipo OK/Errore, al fine di controllare velocemente le prestazioni delle macchine. Tutti gli errori di circolarità superiori a 30 µm nell'accuratezza di posizionamento di una macchina fanno scattare immediatamente un'indagine accurata.
Gli operatori addestrati all'uso del sistema ballbar QC20-W riescono a svolgere i test diagnostici in modo molto efficiente, riducendo al minimo gli errori durante il processo di produzione dei pezzi.
È stato inoltre determinato il rapporto ottimale fra kit per test ballbar e macchine CNC. Il valore ideale è stato calcolato come 1:15, tenendo in considerazione anche la necessità di sottoporre i sistemi ballbar a calibrazioni annuali e la possibilità di eseguire controlli ballbar simultanei su più macchine dell'officina.
Dopo aver acquisito esperienza nell'utilizzo del ballbar QC20-W intervenendo su un'ampia gamma di macchine diverse fra loro, BAE Systems ha rivolto l'attenzione alla macchina utensile che dava problemi e che di fatto era stata messa fuori uso.
Con ballbar si è riscontrato un errore di circolarità XY di 200 μm. Grazie al software diagnostico è stato possibile individuare una mancata corrispondenza dei servomotori, seguita da un gioco significativo. La mancata corrispondenza dei servomotori è stata rettificata dai tecnici della manutenzione di BAE Systems che hanno ottimizzato i parametri di guida dell'asse X, utilizzando il ballbar come strumento di verifica per quantificare i miglioramenti ottenuti con le varie regolazioni.
Anche dopo l'eliminazione della mancata corrispondenza dei servomotori, l'errore rilevato continuava ad essere significativo e il ballbar, utilizzato insieme a calibri di tipo tradizionale, ha permesso di capire che la vite a sfera dell'asse X era usurata. Una volta ripristinata la vite e reimpostata la compensazione per il gioco, la macchina ha soddisfatto il requisito di circolarità XY di 30 μm ed è stata reintegrata nella linea produttiva.
Jim Walsh, Specialist Manufacturing Engineer di BAE Systems, ha commentato: "L'integrazione dei test ballbar nei controlli di routine delle macchine ci ha aiutato a garantire la conformità dei pezzi e ci ha permesso di rimettere in servizio una macchina che ritenevamo irrecuperabile".
Ha poi continuato: "L'uso del software diagnostico del ballbar per l'interpretazione automatica dei risultati e la diagnosi degli errori libera gli operatori dal calcolare il significato dei dati, permettendo di individuare l'origine del problema agevolmente e trovando una soluzione idonea in tempi brevi. Tutto questo si traduce in un immenso risparmio di tempo che può essere dedicato ad attività produttive".
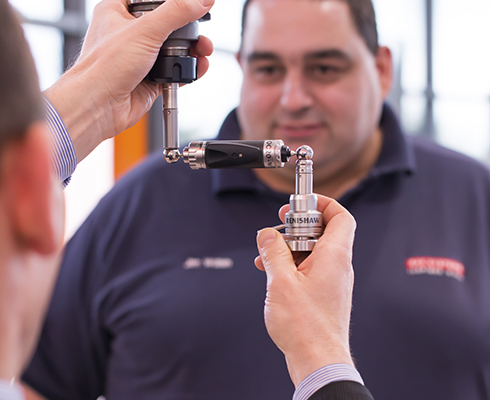
Risultati
L'introduzione del sistema ballbar wireless QC20-W in un programma di manutenzione preventiva per macchine CNC ha aiutato BAE Systems a risolvere alla radice una delle molte sfide rappresentate dalla lavorazione di piccoli lotti di componenti di alto valore, destinati al settore aeronautico.
Grazie alle nuove diagnostiche del ballbar, l'azienda ha potuto intensificare il suo approccio proattivo per la riduzione degli scarti e per l'aumento della produttività. Le cause alla base degli errori della macchina CNC vengono identificati molto prima che possano causare problemi significativi e vengono risolte tempestivamente.
Da BAE Systems la diagnosi degli errori macchina viene effettuata in modo quasi istantaneo. I tempi di inattività delle macchine, a seguito di lunghi e costosi interventi di ispezione e riparazione, sono stati ridotti drasticamente e il produttore della macchina non è più l'unico punto di riferimento per ottenere informazioni e assistenza tecnica.Con l'ausilio delle diagnostiche ballbar di Renishaw, una macchina CNC ritenuta inutilizzabile è stata riportata alla piena operatività e BAE Systems ha potuto trarre vantaggio dal considerevole aumento della produttività della propria officina e dalla conformità ai requisiti di QA.
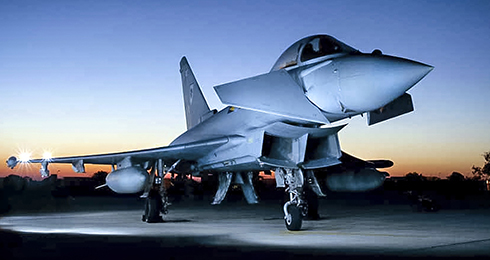