Al momento, questa pagina non è disponibile nella lingua scelta. È possibile visualizzare una traduzione automatica realizzata con Google Translate. Renishaw declina qualsiasi responsabilità relativa alla fornitura di tale servizio e specifica di non avere controllato la traduzione.
È possibile contattarci per richiedere ulteriore assistenza.
Defence & telecommunications supplier 'would not operate a machine without probes'
Tom Forsyth, managing director of Mekall's Machining Division (previously named Fortec), cannot understand why anyone would buy a CNC machine tool without Renishaw probes. He has 12 HAAS machines, all fitted with spindle mounted probes for part setting, and feels well equipped to expand Mekall's subcontract work.
When touch probes were first introduced total machining cycle times were reduced, with setting times cut dramatically and the whole process made highly repeatable. Simultaneously process development times were significantly reduced. As Tom Forsyth comments, “We've brought in time-served skilled engineers who've never seen probing before and left them goggle-eyed!”
Now a key supplier to a growing number of clients in the defence, aerospace, medical and telecommunications markets, Mekall is also the manufacturing partner and supplier to sister company Teknek, a world leader in contact sheet cleaning and web cleaning machinery, with over 15,000 installations worldwide, including many of the world's leading manufacturing facilities. Teknek systems improve yields substantially in manufacturing applications such as surface-mount technology (SMT), printed circuit board (PCB), automotive glass, solar energy and converting/printing. A recent installation is at one of Sony's European plants where it manufactures surface-mount technology (SMT) boards for various Sony flat screen televisions.
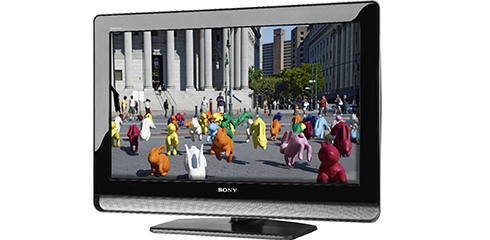
The main benefit is the certainty
Mekall use Renishaw touch probes on its HAAS machines to control the process. As Mr Forsyth says, “It gives us consistency and takes out the chance of human error. Scrap reduction is not even an issue we have to consider.” When parts are loaded for machining the probe is used to measure the position of datum features in a matter of seconds. Machining can start immediately with no manual setting.
Mekall know how important the repeatability of the probing process can be. Before fitting the first touch probe systems to machine tools, they had big problems on a very accurate job for Thales. The position of machined features could vary by up to 0.1mm over the course of a shift, which was all down to operator error.
Automation of manual tasks
“Probes are critical when machining castings”, says Mr Forsyth. “We've done jobs that if set manually would have added a day's work. The casting for a BAe Systems Challenger tank needed us to use a skewing function to rotate the whole coordinate system, using the positioning data gathered with the probe. The thin walls on the casting meant that you had to pick up on the feature itself, and with 50 datum features to check it would have been a huge manual task.”
The data the touch probe provides can also be used to provide feedback so that the machine makes ‘intelligent decisions'. Mekall use routines that check for mis-load by finding the position of certain features. The program will not run if it detects a surface in the wrong place or cannot find a feature.
It gives us consistency and takes out the chance of human error. Scrap reduction is not even an issue we have to consider.
Mekall (UK)
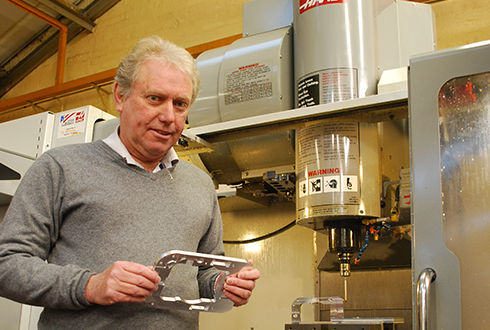
Rapid process development
Mr Forsyth continues, “Knowing you have the probe shortens the development time considerably, removing the need to design and develop fixtures, since you don't need to position the part accurately. Simple clamping is used and an approximate location is all that is needed for the probe to find and set the part. We've been able to standardise the work-holding system across all the machines.
He adds, “The probe moves are very quick and easy to program. We add single lines of NC macro commands into the programs produced by our CAM system.” Mekall use a Solidworks CAD/CAM system, importing drawings and CAD models in the various formats their customers supply ready to plan the machining routines, then quickly adding the probe moves afterwards.
HAAS machines – “capable and easy to use”
Mekall use HAAS machine tools exclusively, with 10 VMCs and 2 turning centres. There are several reasons for this, firstly that Tom Forsyth wanted to standardise on the HAAS control, which he finds very capable and easy to use. Another critical requirement was maintenance, which Mekall does in-house.
Explains Mr Forsyth, “Support can all be done over the phone. Our engineers fit replacement parts, make adjustments and downtime is kept to an absolute minimum. In 15 years we've not had a single issue.”
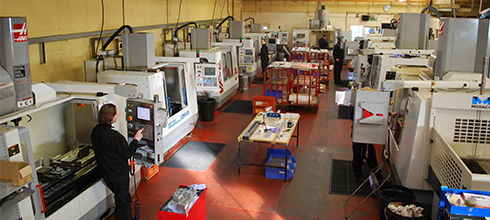