Al momento, questa pagina non è disponibile nella lingua scelta. È possibile visualizzare una traduzione automatica realizzata con Google Translate. Renishaw declina qualsiasi responsabilità relativa alla fornitura di tale servizio e specifica di non avere controllato la traduzione.
È possibile contattarci per richiedere ulteriore assistenza.
Additive manufacturing crosses the finishing line
Formula Student is Europe's most established educational motorsport competition, bringing together industry leaders, high profile engineers, universities and students from around the continent.
The aim is to design and build a single-seater car which races on a course normally reserved for Formula 1. Formula Student is also a place where innovation is very much at home, particularly when it comes to new manufacturing methods and design engineering.
For the 2015 Formula Society of Automotive Engineers (FSAE) race, Swansea University worked closely with global engineering company and additive manufacturing expert Renishaw to redesign the intercooler of its race car and manufacture it on a Renishaw AM250 additive manufacturing system.
The history of the FSAE goes back to 1981, when it was first set up in the United States. Over the years, the competition has become more and more popular with the academic and engineering communities around the world. Each year, innovative designs are submitted, often pushing the boundaries of traditional automotive sports.
A place for additive manufacturing
Swansea University Race Engineering is one of the Formula Student teams that has been at the forefront of the competition since 2001, experimenting with new designs and technologies. The team is made up of engineering students from across different disciplines and levels of study, who work alongside experts from the Materials Advanced Characterisation Centre (MACH1) and the ASTUTE project based at Swansea University, and funded by the Welsh Government and Welsh European Funding Office, respectively.
The Swansea University team focuses on developing different aspects of the car, including suspension, engine, chassis and heat transfer. The students' approach to innovation is pragmatic: if you take a car apart, improve each component and then put all the parts back together, the whole will be greater than the sum of the parts.
One of the components that was given a radical make-over this year was the car's intercooler. The aim was to redesign the component to make it lighter and more compact than its old counterpart.
A combination of these factors was expected to improve the car's speed. To achieve the objective, the team looked towards additive manufacturing, more specifically, metal powder bed fusion.
Metal powder bed fusion uses a powerful high precision laser to fuse fine metallic powders in order to form highly complex functional components. The design of the parts is optimised using 3D computer-aided design (CAD) and the components themselves can be built from a wide range of metal powders melted in a tightly controlled inert atmosphere, in layers with a thickness ranging from 20 μm to 100 μm.
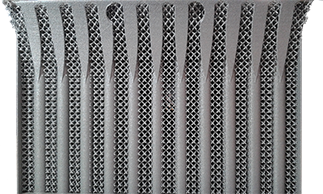
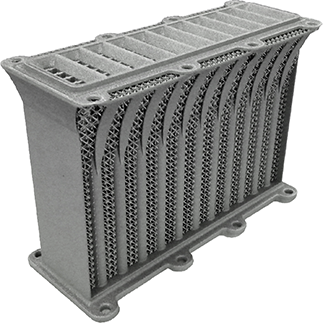
Why an intercooler?
Turbochargers and intercoolers are used in the automotive industry to increase the density of the air flowing into an internal combustion engine. This allows for a larger quantity of fuel to be combusted per stroke, while still maintaining the same air-to-fuel ratio. In turn, this increase in the quantity of combusted fuel produces a higher pressure in the cylinder head, allowing the engine to provide more power. Essentially, turbochargers and intercoolers allow cars to accelerate faster and achieve higher speeds than they would otherwise.
A turbocharger is made up of a turbine linked to a compressor, with the turbine connected to the exhaust pipe of the engine. The hot exhaust gas flows over the turbine making it spin. This increases the pressure of air into the engine - also known as boost pressure. An undesirable result of compressing the air is an increase in temperature of the air entering the engine. The hot air occupies a greater volume.
This is where the intercooler comes in; placed between the outlet from the turbocharger's compressor and the engine intake plenum, it removes heat from the air flowing into the engine and transfers it to the surrounding atmosphere. This further increases the density of air flowing into the engine, developing more power.
The project wouldn't have been as successful without Renishaw's constant support. Additive manufacturing is a complex process, so it always helps to be able to consult an expert whenever you run into any hurdles. Luckily, Renishaw was never more than a phone call away, so their team helped us in the design, testing and manufacturing stage.
Swansea University (UK)
Part requirements
Clearly, the location of the intercooler is essential because the part requires flowing ambient air to cool the boost air into the engine. Commonly, intercoolers are located behind the front grill of a vehicle, but due to their weight, it's not always the best option for race cars. In fact, in the Swansea University formula student car, location was one of the challenges. The intercooler is situated behind the driver, above the engine – not an optimum position in terms of heat transfer.
The new high performing heat exchanger needed to have excellent heat transfer and low pressure drop through the system. The wider range of geometries made available by additive manufacturing meant the team could experiment with more innovative designs that allowed better airflow. Interestingly, although additive manufacturing has previously been used in Formula 1, the current project is unique due to the large scale and cross flow nature of a car intercooler.
Overcoming design challenges
The main hurdles of the project came from design, material and software challenges. The team's objectives were to ensure a high density of boost air for the engine, while still maintaining a good mass flow rate of air. This intercooler also needed to be as light as possible, to improve acceleration.
“Design had a massive impact on the end product, even more so than the material, which is something we didn't originally expect,” explained Dr. Nicholas Lavery, director of the Materials Advanced Characterisation Centre (MACH1) at Swansea University. “Although our students had to go back to the drawing board many times, they were very pleased with the end product. It's also interesting when results are unexpected; it either means you've muddled up your calculations or you're on to something good. Luckily, in this case, it was the latter.”
To identify the best alternative, students tested four intercooler core designs. The different iterations reflected the design principles and capabilities of different manufacturing methods. The first core design, used as a benchmark, was a conventionally manufactured aluminium alloy, AlSi10Mg core with a simple vertical design on the ambient side and a sine wave shape on the boost side.
The second core was designed from 316L stainless steel using metal powder bed fusion. The design was identical to the first one, but was used to test how the added surface roughness available with additive manufacturing impacted heat transfer and pressure drop.
The real benefit of additive manufacturing came when the students started experimenting with the design freedom of the technology. The third intercooler core had a lattice of three dimensional star shapes to form the mesh – a design only made possible by additive manufacturing machines. The mesh was generated using additive manufacturing software and although it took several iterations, the team knew that they were on to a winner.
The fourth and final core used the same three dimensional star lattice structure used in the mesh core, but also made the strut cross-section finer, which meant a higher surface area and density.
Although superior to casting, the surface finish was not as smooth as a manufactured surface. The tests found that the higher surface roughness of additively manufactured intercoolers outperformed conventional counterparts.
This counter intuitive result could be due to better air mixing, altered flow conditions or a combination of both. A good example is shark skin which is rough but very efficient. Recently, biomimicry, the study and emulation of nature in engineering, has become topical. Additive manufacturing could play a role in creating and researching novel shapes.
Mastering material and software challenges
After the students identified the most efficient design, the question of what material they should use came into the spotlight. They originally tried titanium Ti6Al4V, a lighter alternative to stainless steel, but with lower thermal conductivity.
At this stage, Renishaw stepped in and offered to manufacture the part using aluminium alloy AISi10Mg, a material considered ideal due to its high thermal conductivity and light weight. Renishaw used the students' designs to manufacture the intercooler.
Handling the designs was actually one of the most complex aspects of the project, mostly due to their large size. However, it was the computer-aided design (CAD) functions that allowed the most efficient positioning of the lattices to allow maximum heat efficiency, thus increasing the capabilities of the intercooler.
“The project wouldn't have been as successful without Renishaw's constant support,” added Lavery. “Additive manufacturing is a complex process, so it always helps to be able to consult an expert whenever you run into any hurdles. Luckily, Renishaw was never more than a phone call away, so their team helped us in the design, testing and manufacturing stage.”
“To collaborate with Renishaw is a fantastic opportunity for the students,” added Davide Deganello, faculty advisor for the Swansea FS team. “It allows us to foster the links between Swansea University, its students and the industry.”
The project clearly shows the benefits and opportunities of using additive manufacturing for intercoolers used in the automotive sector and the motorsports subsector. Both industries are moving towards the use of smaller, turbocharged engines that mean reduced carbon emissions, while increasing power outputs.
In fact, Formula 1 recently undertook one of the biggest transformations in its history, when in 2014, the engines were changed from a 2.4 litre naturally aspired engine to a 1.6 litre turbocharged unit with a small electric motor for added power.
The relentless requirements of race cars have been known to spark revolutionary driving innovations, like smarter tyres, carbon fibre chassis and traction control.
Who's to say that additively manufactured parts won't be the next big thing for the automotive industry?
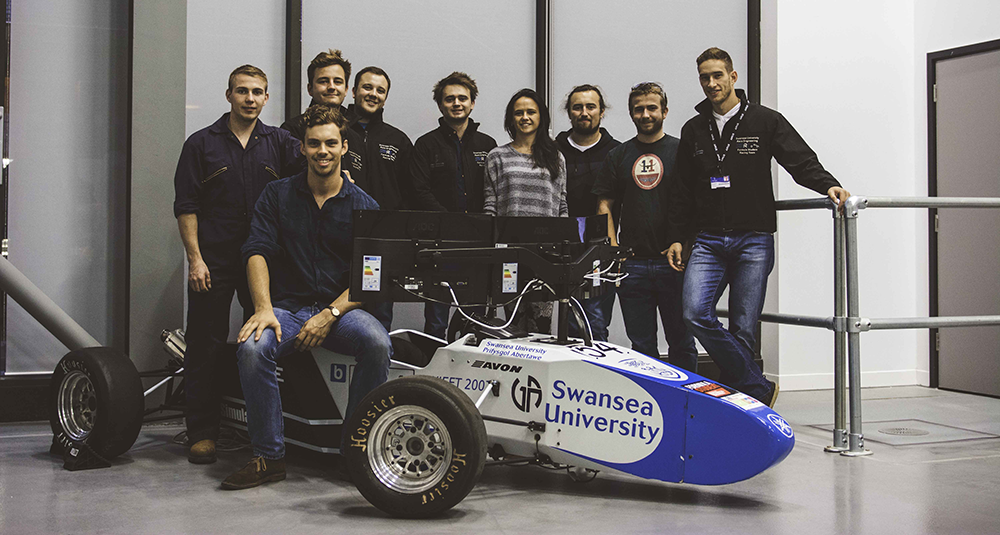