Innovation Matters 2022: Dalla nostra officina
Alla scoperta dei segreti per ottimizzare la produzione di piccoli lotti.
Benvenuti nel nostro mondo. In questa intervista, alcuni esperti dei reparti produttivi Renishaw vi racconteranno i loro segreti del mestiere. Steve Jay ed Antony Spill lavorano in due strutture produttive Renishaw d’eccellenza nel Regno Unito. Sono specializzati nel migliorare i processi produttivi, trovando soluzioni innovative per ridurre i tempi di sviluppo associati alle produzioni in piccoli lotti.
Steve Jay
Qualifica: Responsabile del gruppo Low Volume Production
Sede Renishaw: Miskin
Mansione: Produrre nel minor tempo possibile piccoli lotti di pezzi, facendo ricorso a metodologie diverse, dalla lavorazione di componenti con dimensioni che vanno dai 4 mm ai 4 m , alla realizzazione di pezzi metallici stampati in 3D. Definire processi di lavorazione dei nuovi prodotti ricorrendo a soluzioni innovative.
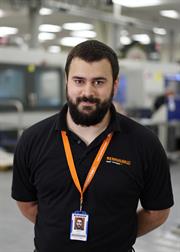
Antony Spill
Qualifica: Responsabile del gruppo Low Volume Production
Sede Renishaw: Stonehouse
Mansione: Gestire l'introduzione di nuovi processi di lavorazione CNC con tempi di consegna ristretti. Ottimizzare i processi in essere e implementare metodologie efficienti per centrare gli obiettivi di produzione e qualità. Le produzioni in piccoli lotti possono arrivare a un massimo di 300 pezzi all'anno e riguardano anche i prodotti personalizzati che realizziamo su misura.
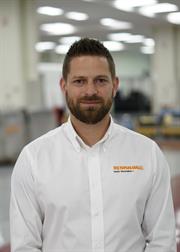
Parlaci dell'approccio Renishaw alle lavorazioni in piccoli lotti e alla produzione di pezzi singoli.
Antony Spill: Il nostro obiettivo principale è la messa a punto di processi efficienti per ottenere "alta qualità a basso costo". Il dipartimento Low Volume è un'entità separata rispetto al reparto produttivo principale e si dedica allo sviluppo di nuovi processi per la realizzazione di prodotti unici o in piccoli lotti, destinati a una grande varietà di settori.
I tecnici del gruppo Low Volume Production (LVP) si occupano dell'intero processo di lavorazione, dal progetto CAM all'impostazione, alla messa in funzione delle macchine.In genere, un nuovo processo viene creato durante un singolo turno di otto ore e include la realizzazione del programma mediante software CAM, l'impostazione della macchina e la lavorazione dei pezzi, nel rispetto dei limiti di tempo previsti. Per realizzare processi efficienti con tempi di consegna rapidi, dobbiamo essere sicuri che le macchine siano in condizioni perfette e, per questo motivo, svolgiamo frequenti verifiche dello stato, utilizzando i sistemi ballbar QC20‑W Renishaw. Utilizziamo spessissimo i prodotti Renishaw per mantenere le macchine in condizioni ottimali e avere la certezza di produrre sempre componenti perfetti al primo tentativo.
Quando lavoriamo a un nuovo componente, non ci concentriamo tanto sullo sviluppo dei singoli processi a livello di programmazione, quanto su procedure che ci diano la certezza che le macchine utensili siano abbastanza precise da produrre pezzi sempre corretti.
Steve Jay: Nel 2018 il reparto Low Volume è stato spostato nella sede di Miskin, nel sud del Galles ed è stato potenziato per rispondere in modo adeguato all'aumento della domanda di componenti di grandi dimensioni e di prodotti speciali e personalizzati, spesso realizzati tramite stampa 3D in metallo.
Come mantenere una macchina in buono stato
Un investimento in soluzioni per il controllo delle condizioni della macchina può aiutare a ridurre i tempi di sviluppo e di implementazione dei pezzi.
- Valutazione delle prestazioni: calibrazione della macchina, tramite il kit ballbar QC20-W(processi multipli)
- Procedura di controllo delle condizioni: mediante un tastatore pezzo OMP400 (su fresa verticale)
- Origini pezzo con mappatura degli errori: utilizzando un tastatore pezzo OMP400 (su processo di tornitura/fresatura)
- Calibrazione utensile da torretta a torretta: con un gruppo composto da sonda OLP40 e stilo (su processo di tornitura/fresatura)
Quali sono oggi le tre sfide principali per le aziende?
Aumentare l'efficienza
AS: Introdurre soluzioni innovative per migliorare l'efficienza dei reparti.
Ridurre il costo della qualità
AS: Ridurre il costo della qualità, soprattutto cercando di eliminare gli scarti e arrivando ad avere un rapporto ottimale fra pezzi fabbricati e pezzi utilizzabili.
SJ: Questo è un aspetto particolarmente delicato qui a Miskin, dove spesso produciamo pezzi grandi e costosi, che richiedono lavorazioni molto lunghe. Il costo della qualità è un tema su cui continuiamo a lavorare, ricorrendo a varie soluzioni tecniche, fra cui la verifica dei pezzi durante il ciclo.
Garantire la soddisfazione del cliente
AS: Il nostro obiettivo primario è fare felice il cliente, che sia l'utente finale o semplicemente il successivo gruppo di lavoro nella catena di assemblaggio.
SJ: Quando realizziamo un pezzo speciale o personalizzato per la prima volta, cerchiamo di produrre un "pezzo buono al primo tentativo".
Perché è così importante evitare che il primo pezzo prodotto sia da scartare, soprattutto nel caso di pezzi grandi?
AS: Si tratta di un insieme di fattori che riguardano l'efficienza e la riduzione del costo della qualità. Possiamo usare tecnologie di ispezione che ci permettono di trovare la posizione degli elementi per essere certi di lavorarli in modo accurato. La lavorazione dei pezzi più grandi può richiedere diverse ore e l'impiego di più reparti. Essere costretti a scartare un componente perché un elemento risulta fuori posizione o perché ha misure non corrette rappresenta uno spreco in termini economici e di efficienza. L'impiego di semplici cicli di ispezione ci permette di tenere sotto controllo le caratteristiche chiave ed evitare imprevisti spiacevoli.
SJ: Il tempo è denaro. La varietà dei componenti e dei metodi di lavorazione continua a crescere e il concetto di "Productive Process Pyramid" sviluppato da Renishaw si dimostra sempre più utile ed efficace. La capacità di migliorare in modo costante e consapevole ogni fase del processo produttivo ci permette di ottimizzare l'efficienza e il costo della qualità.
Com'è lavorare in un'officina Renishaw?
AS: Posso considerarmi fortunato, perché ho avuto l'opportunità di ricoprire ruoli diversi all'interno dell'officina Renishaw. Senza l'esperienza acquisita svolgendo tante mansioni diverse, oggi non sarei certamente in grado di fare la differenza e di mettere le mie competenze al servizio dei colleghi. Questa è la filosofia della nostra officina, dove tutti sanno quanto sia importante il lavoro di squadra e la condivisione delle conoscenze. Qui da noi, i successi del singolo sono anche i successi del gruppo.
Seguendo la strategia della nostra officina, cerchiamo di allineare le piattaforme utilizzate. L'uso di tante macchine diverse può portare a una dispersione delle competenze e creare colli di bottiglia nei processi, con conseguenti problemi a livello di risorse e forniture. La standardizzazione di macchine e processi ci permette di avere la flessibilità necessaria per sfruttare al meglio le nostre risorse e competenze. In questo modo diventa più semplice per i reparti raggiungere i propri obiettivi e il personale può passare da un'area a un'altra senza particolari problemi.
Quali sono le tecnologie Renishaw che utilizzi con più soddisfazione?
AS: Adoro le sfide e mi piace trovare problemi che possono essere risolti solo con la partecipazione dell'intero gruppo. Il nostro compito è trovare soluzioni e questo dev'essere ben chiaro a tutti i membri del team. La ricerca di strade nuove e innovative per migliorare il lavoro del dipartimento tramite i prodotti Renishaw è una sfida costante e avvincente. Bisogna dire comunque che la possibilità di avere queste straordinarie tecnologie a nostra disposizione è una grande fortuna.
Un esempio recente, che probabilmente è stato anche il progetto che a oggi mi ha dato maggiore soddisfazione, riguarda una macchina che era ormai considerata da buttare. Abbiamo sfruttato la tecnologia Renishaw per individuare tutti i problemi e implementare una soluzione mirata che ha regalato alla macchina una seconda vita.
SJ: La nostra tecnologia di stampa 3D è davvero eccezionale. Stimola l'immaginazione dei progettisti e il modo in cui l’abbiamo integrata nel dipartimento come unità produttiva è semplicemente fantastico.
Qual è il segreto per una buona produzione in piccoli volumi?
AS: Quando si lavora con scadenze strette, è indispensabile adottare processi rapidi dal primo all'ultimo momento. Questo significa anche scegliere metodi di programmazione che diano la certezza che la macchina utensile lavori in modo accurato.
Ho mappato gli errori delle macchine per essere sicuro di realizzare componenti buoni al primo tentativo senza allungare i tempi di sviluppo del processo iniziale. Un esempio del nostro modo di lavorare riguarda una macchina con prestazioni ben al di sotto dello standard minimo.
- Centro di tornitura/fresatura complesso e di grandi dimensioni, con asse B e torretta.
- Questo problema causava molti errori di posizione nella macchina
- e riduceva le sue prestazioni durante le lavorazioni di piccoli lotti che potevano durare mediamente otto ore per serie, e spesso anche di più.
- La scarsa efficienza del centro di lavoro creava costantemente problemi di approvvigionamento.
- Grazie all'implementazione di un tastatore pezzo OMP400 Renishaw, siamo riusciti a individuare gli errori di posizione fra gli assi della macchina e abbiamo studiato una procedura per mapparli.
- Il controllo viene effettuato due volte a settimana per garantire che gli errori di posizione vengano individuati e salvati nelle macro che, a loro volta, vengono richiamate in tutti i nuovi setup della macchina e incorporate mediate le origini pezzo.
- Questo processo, unito alla calibrazione da torretta a torretta, consente di ottenere una perfetta accuratezza in tutti gli assi della macchina e di eseguire la mappatura degli errori della stessa.
- Così, siamo riusciti a dimezzare i tempi di impostazione e l'impatto in termini di risparmio di tempo e costo della qualità è estremamente soddisfacente.
SJ: Inevitabilmente , la prima domanda che un operatore si pone è: "Come posso lavorare questo pezzo?" Tuttavia, se si impara a prendere in considerazione l'opportunità di verificare il componente o l'elemento, è possibile trovare soluzioni alternative e spesso più efficaci. Ad esempio, si può scoprire che il processo può essere ottimizzato cambiando l'orientamento o utilizzando fissaggi diversi. Trovare un modo per effettuare verifiche durante il ciclo e ottenere la conferma che un pezzo o una dimensione che potrebbero apparire problematici sono in realtà corretti ancora prima di aprire lo sportello della macchina rappresenta un vantaggio importante.
Dave Miles
Qualifica: Compliance Engineering Manager
Sede Renishaw: Stonehouse e Miskin
Dal 1973, anno della sua fondazione, Renishaw ha costantemente ampliato e diversificato il suo portafoglio di prodotti. Lavorando per oltre 20 anni nel campo dei servizi produttivi mi sono trovato a risolvere molti problemi. È piacevole essere circondato da un team di persone motivate e sempre pronte a superare i propri limiti per migliorare i processi produttivi.
Steve Roberts
Qualifica: Machine Shop Manager
Sede Renishaw: Stonehouse e Miskin
"Negli oltre 30 anni trascorsi in Renishaw, ho assistito a una straordinaria trasformazione dei servizi produttivi". Abbiamo aperto nuove sedi e siamo diventati leader del settore, con stabilimenti e strutture di primissimo livello. Per me è un privilegio e un onore risolvere i problemi che si presentano quotidianamente insieme a un team di tecnici così preparati e motivati. Ogni giorno ci impegniamo al massimo per consegnare gli ordini nei tempi previsti e per trovare nuove opportunità per ampliare e approfondire le nostre conoscenze tecniche".
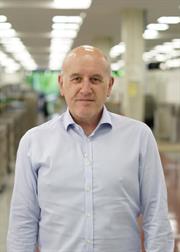
Sedi Renishaw di Miskin e Stonehouse
Le nostre attività
- Molti processi di lavorazione, fra cui: sistema RAMTIC (Renishaw Automated Milling, Turning and Inspection Centre) per la lavorazione di componenti prismatici; macchine di fresatura/tornitura per lavorazioni singole di pezzi di medie dimensioni; torni a fantina mobile per la tornitura di pezzi piccoli e diverse macchine per la produzione di piccoli lotti.
- Processi di ispezione, come ad esempio: sistemi di ispezione in-process e soluzioni di ispezione su CMM completamente automatiche.
- Operazioni di finitura: anodizzazione, sbavature e incisioni laser, processi di molatura per la realizzazione di utensili da taglio e taglio laser.
- Impianti di assemblaggio per stili, prodotti di lavorazione additiva ed encoder, oltre alle linee di assemblaggio automatiche per il montaggio delle elettroniche (Miskin).
Cosa produciamo
- La lavorazione dei pezzi di tutti i prodotti Renishaw è ripartita fra i due stabilimenti di Stonehouse e Miskin, dove si adottano processi simili, per garantire una maggiore flessibilità e una migliore gestione delle emergenze.
- Dai pezzi per le sonde più piccole, come TP20 e OMP40, fino ai prodotti più grandi, come ad esempio la testa del sistema di misura a 5 assi REVO® e il sistema di lavorazione additiva RenAM 500Q.
I prodotti Renishaw che usiamo
- Nelle nostre piattaforme di lavoro usiamo le sonde Renishaw per il presetting utensili, l'impostazione dei pezzi e l'ispezione dei componenti. I prodotti che utilizziamo con maggiore frequenza sono OMP40, OMP400, RMP60, RLP40, NC4, TS27R, MP250 e una serie di bracci di presetting utensile.
- Per la calibrazione della macchina e la base del processo ricorriamo a diversi sistemi di calibrazione Renishaw, fra cui ballbar QC20-W, sistema laser XL-80 AxiSet™.
- Le ispezioni del componente finale vengono eseguite con calibri Equator™ oppure mediante CMM che utilizzano sonde come PH10, SP25, TP20 e il software MODUS.
Miskin, Galles
Concetti per le Smart Factory del futuro, realizzabili con la tecnologia di oggi
Area: 40.000 m2
Addetti: 550
Stonehouse, Inghilterra
Uno degli stabilimenti manifatturieri più efficienti di tutto il Regno Unito
Area: 9.000 m2
Addetti: 220