L'alignement laser accélère les contrôles d'assemblage de la machine-outil
La fiabilité et la précision ultime d'une machine-outil dépend en grande mesure du contrôle de l'alignement lors de son assemblage. Pour les machines-outils produites en grandes quantités, l'efficacité du procédé de contrôle d'alignement est primordiale. À la recherche d'une alternative aux techniques de mesure d'erreur traditionnelles,Hurco Manufacturing Ltd.(Hurco) a choisi le système laser d'alignement XK10 de Renishaw pour augmenter tant sa précision que sa cadence.
Contexte
Véritable pionnier dans l'application des technologies informatiques pour la conception de machines-outils, Hurco est un fournisseur international de machines à commande numérique. Fondée dans l’Indiana aux États-Unis en 1968, la société fabrique une gamme complète de produits comprenant des machines à CN 5 axes, des tours à CN multiaxes, des centres d'usinage verticaux et des centres de tournage.
Sa base de clientèle mondiale comprend des fabricants de moules et de matrices, d'outils de précision, des ateliers à façon indépendants, des fabricants spécialisés de production de petites séries et des constructeurs d'outils de fabrication métalliques. Le portefeuille de produits de la société comprend trois marques réputées : Hurco, Milltronics et Takumi.
Hurco Manufacturing a été créée à Taiwan en 1999 et est aujourd'hui responsable de la fabrication et de l'assemblage de la gamme complète des machines-outils Hurco. Pour s’assurer que les exigences de précision, de sécurité et de fiabilité des machines-outils sont respectées, un contrôle qualité strict est primordial à chaque étape du procédé de fabrication.
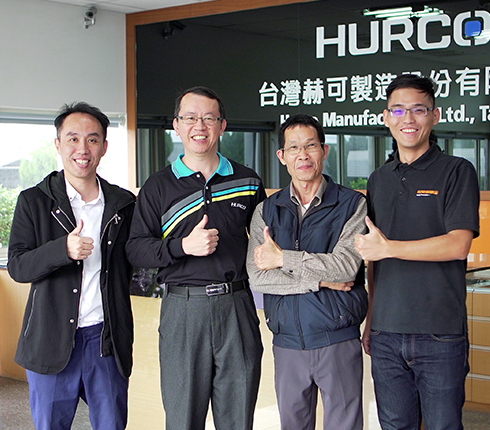
Hurco et les membres de l'équipe Renishaw
Défi
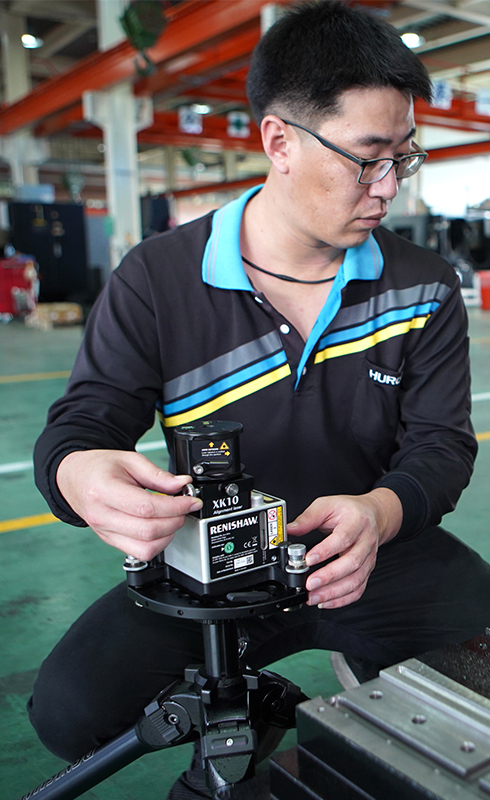
Hurco utilisant le système laser d’alignement XK10
Hurco produisant plus de 2.000 machines-outils chaque année, l’augmentation de l'efficacité de mesure représentait un facteur essentiel pour les procédés d'inspection et de vérification de la société. Non seulement l’alignement et la mesure de la machine devaient être très précis, mais ils devaient également gagner en rapidité.
Les inspections d'alignement au cours du procédé d'assemblage ont été effectuées par Hurco en utilisant un mélange d'outils de mesure traditionnels, des MMT et des équipements de calibration ultra-modernes. La société a depuis longtemps utilisé une gamme de solutions Renishaw, comprenant l'interféromètre à laser XL-80, le système Ballbar QC20-W et le calibre d’axe rotatif XR20-W.
La taille et l’échelle des composants moulés de machines-outils présentaient d'importantes restrictions pour les solutions MMT, tandis que les faiblesses inhérentes aux techniques de mesure traditionnelles risquaient de limiter les performances de fonctionnement. Wang Shun-Chien, vice-président de Hurco Manufacturing explique : « Par le passé, nous avons mesuré et aligné nos produits moulés en utilisant des machines à mesurer tridimensionnelles, mais les plus grandes dimensions de pièces moulées étaient toujours un facteur limitant et nécessitaient beaucoup de main-d'œuvre. »
Il poursuit : « Nous utilisions également des outils de contrôle d'erreur traditionnels tels que des carrés de granit, des comparateurs à cadran et des autocollimateurs pendant le procédé d'assemblage, mais ceux-ci n’étaient jamais assez efficaces et les résultats de mesure n’étaient pas suffisamment homogènes. »
« Quand nous avions besoin de mesurer le parallélisme de certaines grandes pièces moulées, si le carré de granit et le rail de guidage se situaient à une certaine distance, le comparateur à cadran devait être rallongé pour atteindre le granit, ce qui causait alors une amplification du résultat d’écart. »
Hurco s’est alors lui-même fixé le but d'identifier une solution d'alignement de machine-outil plus précise. Une qui nécessitait beaucoup moins de temps et de main-d'œuvre à paramétrer et à utiliser, et pouvant remplacer les méthodes de mesure traditionnelles.
Solution
Après des recherches et des tests approfondis, Hurco a choisi d'adopter le système laser d'alignement XK10 de Renishaw. Le système XK10 peut être appliqué sur des rails linéaires pour s’assurer qu'ils soient droits, carrés, plats, parallèles et à niveau, ainsi que pour évaluer la direction des broches et des mandrins, ainsi que la coaxialité des machines rotatives.
Solution de mesure numérique tout-en-un adaptée à une gamme de différentes machines-outils à commande numérique, le XK10 comprend une unité de sortie pour la transmission laser primaire ; des émetteurs et récepteurs sans fil ; une unité d'affichage portable et un kit de bridage. Un kit de parallélisme XK supplémentaire effectue les mesures de parallélisme.
La taille compacte, la connectivité sans fil et le bridage polyvalent signifient que le système XK10 peut être utilisé dans de nombreuses configurations différentes, permettant la détection et la mesure d’erreurs géométriques et rotationnelles sur tous types et toutes tailles de machine-outil.
L'unité d'affichage permet à l'opérateur de collecter, d'analyser et d’enregistrer les données de mesure. Elle fournit des instructions étape par étape pour chaque type de mesure, avec des graphiques intuitifs et des lectures en temps réel guidant l'opérateur à travers chaque étape du procédé de mesure.
Contrairement à un autocollimateur, lequel dépend du principe de la conversion des mesures angulaires en mesures linéaires, le système d'alignement laser XK10 prend des mesures linéaires directement, ce qui élimine l'erreur inhérente à la conversion. Plus important encore, tout bris de faisceau laser du XK10 lors de la capture de données ne nécessite pas de redémarrage complet, contrairement à une solution d’interféromètre laser.
En remplaçant différentes tailles de carrés de granit, le XK10 a également résolu le problème de l'espace de stockage limité et de logistique. Grâce à sa portabilité et à sa flexibilité, il est facile à emmener sur site, effectuant des mesures de précision en temps réel.
Hurco Manufacturing Ltd (Taïwan)
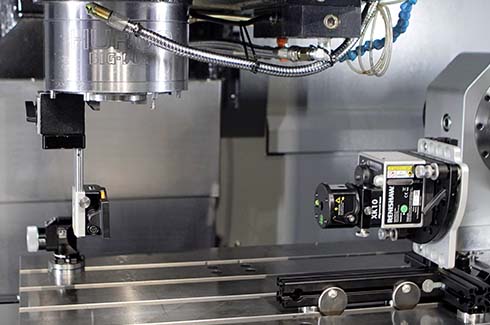
Solution de mesure numérique tout-en-un XK10
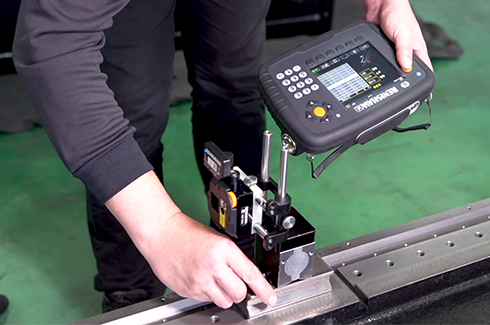
Unité d'affichage XK10 permettant de collecter, d'analyser et d’enregistrer les données de mesure
Résultats
Le système laser d'alignement XK10 a réussi à réduire de manière significative le temps nécessaire à Hurco pour mettre en œuvre un alignement de machines-outils de haute précision. Après avoir testé à plusieurs reprises le système XK10, ils ont constaté qu'il apportait une solution réellement capable de remplacer les méthodes traditionnelles.
M. Wang explique : « Selon une estimation prudente, je dirais que le système laser d'alignement XK10 de Renishaw a au moins doublé notre efficacité globale de mesure et notre procédé d'évaluation a prouvé que les résultats de mesure concordaient précisément avec ceux de machines à mesurer tridimensionnelles de haute précision.
Doté d’une large plage de mesure de 30 m, le système XK10 répond aux exigences de nombreuses grandes machines-outils. Le franchissement de la portée entre les rails de guidage pour les mesures de parallélisme est devenu facile, supprimant la nécessité de grands carrés de granit et évitant le risque d’écart de comparateurs à cadran hyper-rallongés.
M. Wang poursuit : « Le XK10 nous a particulièrement impressionnés en termes de mesure de parallélisme entre deux rails de mesure. Par rapport aux autocollimateurs, le paramétrage du XK10 pour de multiples mesures de rail est beaucoup plus simple. Nous alignons l'unité laser et tournons les faisceaux laser de 90° avec le kit de parallélisme XK. Ensuite, le système analyse automatiquement les données collectées et nous fournit des mesures de parallélisme entre les deux rails. Il n’y a pas plus simple. »
« En remplaçant différentes tailles de carrés de granit, le XK10 a également résolu le problème de l'espace de stockage limité et de logistique. Grâce à sa portabilité et à sa flexibilité, il est facile à emmener sur site, effectuant des mesures de précision en temps réel. Il est utilisé pour l'assemblage de machines-outils, la calibration et la maintenance, et en permettant une meilleure compréhension de l'état de chaque machine à commande numérique, les ressources peuvent être allouées plus efficacement. »
M. Wang ajoute : « Les rapports produits par le XK10 sont également très intuitifs, et par un choix de tableaux ou de graphiques, les clients peuvent déterminer très rapidement l'état d'une machine-outil lors d'un contrôle d'acceptation. »
« Maintenant que nous disposons du XK10, nous pouvons déterminer rapidement si la source d’écart est liée au procédé d’assemblage, plutôt qu’à l'usinage de la pièce ou à la rigidité de la pièce moulée. Et si nous découvrons des problèmes avec la précision de l'usinage de la pièce, nous pouvons réagir rapidement en vérifiant les machines à commande numérique et effectuer les ajustements nécessaires. Ce système nous a vraiment aidés à gagner en efficacité. »
Depuis sa fondation, Hurco a utilisé pratiquement tous les produits de calibration Renishaw, y compris l'interféromètre à laser XL-80, le système Ballbar QC20-W et le calibre d'axe rotatif XR20-W. M. Wang nous explique : « L'ajout du système XK10 a rendu notre arsenal d'instruments de mesure encore plus complet, nous apportant des instruments dédiés à l'assemblage des machines-outils, à la calibration et à la maintenance. Il nous permet également d'acquérir une meilleure compréhension de l'état de chaque machine à CN afin que nous puissions allouer nos ressources avec plus de souplesse. »