Cette page n'est pas disponible actuellement dans votre langue. Vous pouvez en afficher une traduction automatique avec l'outil Google Translate. Cependant nous déclinons toute responsabilité quant à ce service et nous ne contrôlons pas les résultats de la traduction.
Pour en savoir plus à ce sujet, contactez-nous.
Introduction to encoder systems
Position encoders are found in a wide range of applications and industries and feature a range of technical concepts and terminology.
This article aims to explain optical encoders in simple terms: it covers descriptions of what an encoder is, the different types of encoder, how they work and where they are used.
What is an encoder?
An encoder is an electromechanical device that converts information from one format or code into another. A position encoder, such as those made by Renishaw, converts linear or rotary motion into an electrical signal that provides information on position, speed, and direction of motion.
Position encoders can employ a range of different sensing technologies: Renishaw specialises in optical, inductive and laser encoder systems. RLS, a Renishaw associate company, specialises in magnetic encoders.
What is an inductive encoder?
An inductive absolute encoder is a type of position sensor that uses electromagnetic induction to measure the position or motion of an axis.
Inductive encoders offer robustness, contamination resistance, immunity to external magnetic fields and good accuracy.
Applications include gimbals, medical devices, general automation, UAVs, robots and servo motors.
To find out more, visit the Renishaw inductive encoder webpage.
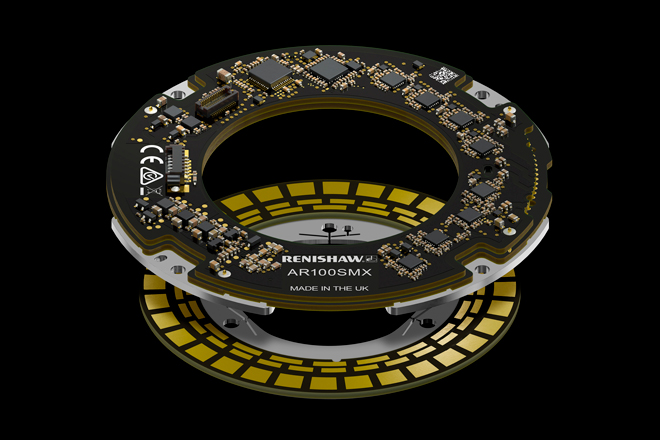
What is a magnetic encoder?
Magnetic encoder systems use a magnetised scale featuring a series of alternating magnetic poles. Motion along the scale is determined by a readhead that contains a sensor that detects the change in magnetic field as the readhead moves and converts this change into an electrical signal.
Magnetic encoders are often used in robotics (such as automated guided vehicles) and printing applications.
To find out more about magnetic encoder systems, visit the RLS website.
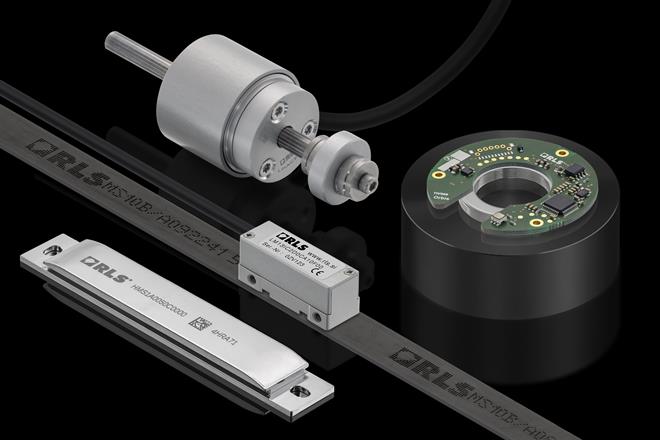
What is a laser encoder?
Laser encoder systems use the wavelength of a laser light as their measurement unit by detecting the path length difference between a fixed reference path and a variable measurement path. Laser encoders offer high accuracy position measurement with fine resolution.
Laser encoders are often used in the aerospace and marine industries as well as other specialist applications.
To find out more, visit the Renishaw laser encoder website pages.
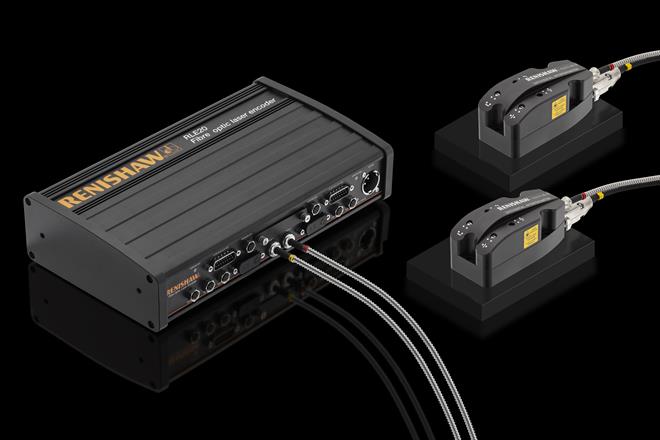
What is an optical encoder and how does it work?
Optical encoders are devices that use a light source and a photo-detector moving past scale lines to produce an electrical signal. This signal can be read by a control device (or controller) within a motion control system. Renishaw has more than thirty years of experience in the design, manufacture and support of high-performance optical encoders.
An optical encoder consists of two components: the scale and the readhead.
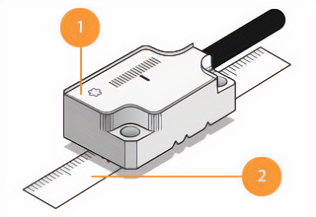
1: Readhead 2: Scale
The encoder scale
Optical encoder scales are marked with parallel dark lines, much like the markings on a conventional ruler. These lines, often called graduations, are ‘read' by an optical system inside the readhead to create electrical signals or images for further processing. The lines are accurately positioned on the scale material to ensure appropriate system measurement performance.
Optical encoder scales can take many forms, such as flexible linear, rigid linear, discs and rings. These different forms enable the measurement and control of different types of motion such as linear, full rotation, partial arc rotation, or a combination of these movements.
Optical encoder scales must be stable and robust and are commonly made from materials such as stainless steel or glass.
The encoder readhead
The readhead contains an optical system and electronics that generate an electrical output signal that describes the position and direction of motion of the readhead relative to the scale.
By means of signal processing and digital interpolation optical encoders can resolve movement down to one billionth of a metre (1 nm).
A nanometre is the radius of a DNA helix, the width of two glucose molecules or the wavelength of an X-ray.
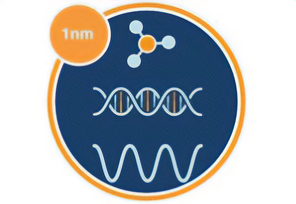
Types of optical encoder
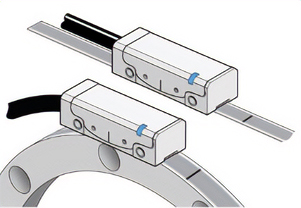
Open encoders
An open optical encoder features a scale and readhead that are separated by a small gap, known as the rideheight, and configured to measure linear, rotary or partial arc motion. Its non-contact design benefits from zero friction and no mechanical wear or hysteresis.
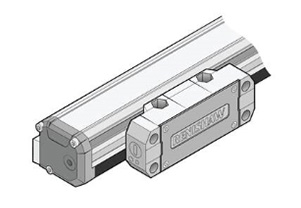
Enclosed encoders
In enclosed encoder systems, the scale and readhead are mounted in a sealed enclosure which protects the encoder from contamination with solid debris and ingress of fluids in harsh environments. For example, enclosed encoders are typically used on machine tools, where high accuracy and resistance to contamination from machining debris and cutting coolants are important.
Motion
Optical encoders can measure motion in various forms, depending on the type and structure of the machine motion being measured.
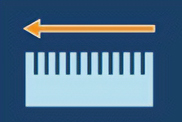
Linear
Linear encoders report position along a straight line and are used for X, Y or Z axes, such as in a Cartesian co-ordinate measuring machine (CMM).
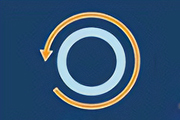
Rotary
Rotary encoders report angular position of a rotating part by means of a scale shaped like a ring or a disc. These encoders enable the control of rotary motion, such as in a rotary table or the joints of a robot.
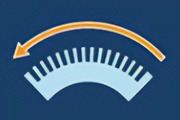
Partial arc
Some linear encoder scales are flexible and can be wrapped around a drum, shaft or curved surface of a machine to enable the control of rotary motion of less than one whole turn.
What are the differences between absolute and incremental encoders?
Incremental encoders can only detect motion relative to their current position or a known reference feature – the output position signal increments or decrements (depending on direction) position by one count at a time as the readhead moves relative to the scale.
Absolute encoders immediately decode their current position without any motion being required.
A key difference between the behaviours of incremental and absolute encoders is how they respond to a loss of power. If an absolute encoder loses power, the readhead will still be able to correctly report its current position when the power is restored, even if it moved during the power outage. Incremental encoders lose their position information during a power cut and require their datum position to be reacquired when power is restored.
Another key distinction is related to communication: absolute encoders feature two-way serial communication between the controller and readhead, whilst incremental encoders provide one-way communication via analogue or digital signals from readhead to controller.
Incremental position
The lines on an incremental scale are arranged in a simple evenly-spaced parallel pattern, like a ruler with no numbers. During the start-up procedure, a datum position is detected by reading a reference mark embedded within the incremental scale. The datum is a single fixed point anywhere along the axis of measurement that is used as the machine's point of reference and is sometimes described as the ‘home' position. All position information is relative to this datum.
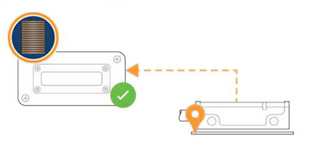
An incremental encoder commonly outputs its position information in the form of two analogue waveforms 90 degrees out of phase with each other, like a sine and cosine wave, or as two digital signals 90 degrees apart, known as quadrature. These signals can be interpreted by the controller to calculate the magnitude and direction of movement along the encoder scale.
Incremental encoder scale can be manufactured in long lengths for large-scale installations or cut-to-length to suit any axis length.
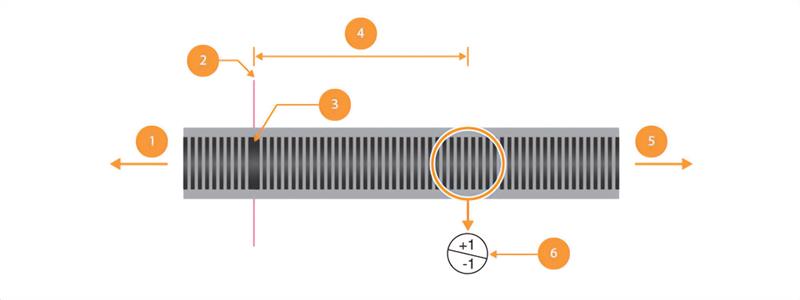
1: Direction of decreasing count, 2: Datum position, 3: Reference mark, 4: Controller position = number of counts from datum, 5: Direction of increasing count, 6: Incremental count change
Absolute position
In an absolute encoder system, specific position information is coded within all sections of the scale, like a ruler with numbers. These specific positions are defined by sets of parallel lines with some of the lines missing, rather like a barcode. This non-repeating pattern allows the readhead to find its position immediately on start-up.
The controller will periodically request position information from the readhead, which then captures a snapshot of the scale and decodes the image into a specific position, which is then reported back to the controller via a serial communications protocol.
A range of industry-standard communications protocols are available, often associated with specific machine controller manufacturers.
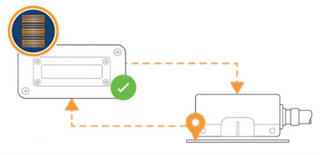
Absolute scales rely on short unique patterns (or words) of lines and spaces to identify position. As these words have a finite number of possible arrangements, absolute encoders scales will have a maximum measuring length. In the case of Renishaw's RESOLUTE™ absolute encoder system, this maximum measuring length is 21 metres.
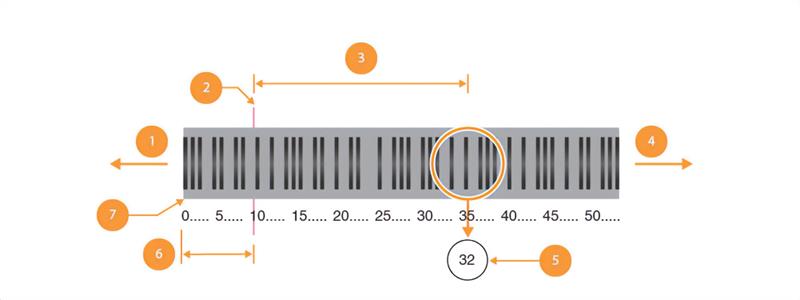
1: Direction of decreasing position, 2: Datum position, 3: Controller position = readhead position - numerical offset, 4: Direction of increasing position, 5: Absolute position, 6: Numerical offset of datum position, 7: Position 'Zero'
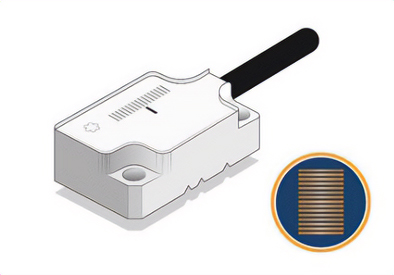
Where would I use an incremental encoder?
Incremental encoders are used in a wide variety of motion control applications such as factory automation, co-ordinate measuring machines (CMMs) and semiconductor manufacturing equipment. Incremental encoders enable accurate position measurement at fine resolutions and at high scanning speeds.
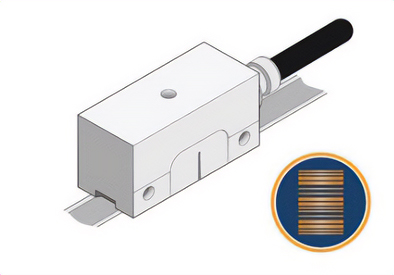
Where would I use an absolute encoder?
Absolute encoders are well-suited to machines that need to retain position information through power cycle events. Applications include surgical robots and machines where homing cycles to a fixed reference mark are not desirable.
Where are optical encoders used?
Optical encoders are versatile position measurement devices used in a wide range of applications for measuring and controlling linear or rotary motion.
They are used in many industries and applications such as metrology, semiconductor manufacture, robotics, automation, machine tools and scientific research.
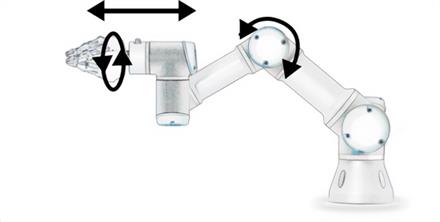
Watch our webinar on-demand
The introduction to encoder systems webinar aims to describe in simple terms what an encoder does.
It will explain the role of the scale and readhead, the different types of encoder available, how they work and where they are used.
Register to watch it on-demand.