Étalonnage, sans erreur, d'échelle linéaire par interféromètre laser
Pour obtenir constamment une précision de mesure inférieure au micron, un système automatisé d'étalonnage d'échelle linéaire, mis au point par le Standards and Calibration Laboratory (SCL) à Hong Kong, a fait de la correction automatique d'erreurs un critère essentiel de conception. Un interféromètre laser Renishaw XL-80 et un compensateur XC-80 ont été utilisés avec succès pour gérer les sources d'erreur d'Abbe, ainsi que les changements dans les conditions environnementales.
Contexte
Les échelles linéaires sont souvent utilisées sur les équipements de mesure très précise de longueur, y compris les comparateurs, les microscopes et les instruments de mesure, car elles permettent d'avoir un élément de comparaison précis pour mesurer les distances ou les déplacements avec précision.
Les échelles linéaires sont généralement en verre, des traits sont précisément gravés sur leur surface avec des traits parallèles équidistants perpendiculaires à l'axe de l’échelle linéaire. Pour mesurer et vérifier les distances entre les graduations d'échelle linéaire, des instruments de haute précision sont nécessaires.
Le Standards and Calibration Laboratory, faisant partie de la Innovation and Technology Commission de la région administrative spéciale de Hong Kong, est responsable de la formulation et du maintien des normes de référence de mesure physique pour la région de Hong Kong.
Ce laboratoire offre aux utilisateurs locaux des normes et des instruments de mesure des services d'étalonnage pour qu'ils puissent effectuer avec précision leurs mesures et pour qu'ils puissent correctement les corréler aux normes pertinentes.
SCL s'est fixé pour tâche de concevoir et de fabriquer un nouveau système automatisé d'étalonnage d'échelle linéaire capable d'atteindre une précision de mesure inférieure au micron. Et surtout, il devrait être en mesure de compenser automatiquement les erreurs Abbe causées par les moindres déplacements angulaires de l’équipement et par les variations des conditions environnementales.
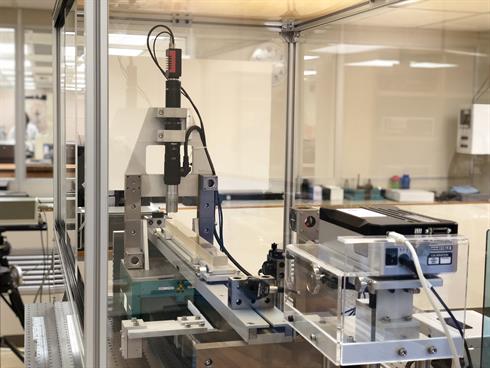
Défi
Décrit par Ernst Abbe de Zeiss en 1890, le principe d'Abbe a été appelé ‘le principe d'alignement’ et il dit : “Si les erreurs de parallaxe doivent être évitées, le système de mesure doit être placé dans le même axe que l'axe du déplacement (sens de la longueur) devant être mesuré sur la pièce à usiner.”
Une erreur Abbe est donc introduite lorsqu'un point à mesurer est séparé latéralement de l'axe de mesure, et lorsque le système de positionnement est soumis à un mouvement angulaire. Dans ce cas, le déplacement mesuré semble plus court ou plus long que le déplacement réel. La séparation spatiale entre le point mesuré et l'axe de mesure est appelée le décalage Abbe.
À titre d'illustration très simple, prenons le cas d'un pied à coulisse. Entre l'axe de l'échelle et l'axe de mesure (formé entre les mâchoires) il y a un décalage Abbe. Les problèmes concernant la rectitude, la rectangularité ou le ‘jeu’ du pied à coulisse conduiront tous à un déplacement angulaire dans les mâchoires, et donc à une erreur Abbe.
J.B. Bryan qui a décrit le principe d'Abbe comme “le premier principe de conception et de métrologie dimensionnelle d'une machine” l'a ainsi reformulé en termes de mécanique : “Le système de mesure de déplacement doit être aligné avec l'organe fonctionnel dont le déplacement est à mesurer. Si ceci n'est pas possible, soit les glissières qui transfèrent le déplacement ne doivent avoir aucun mouvement angulaire, soit les mesures du mouvement doivent être utilisées pour calculer les conséquences du décalage.”
En termes simples, la mesure de la précision des graduations sur une échelle linéaire est effectuée en mesurant la distance entre une ligne de référence (généralement la position zéro) et la graduation cible. Les technologies d'analyse et de correction d'image doivent alors être appliquées afin que le système puisse calculer et modifier les positions de lecture de l'échelle linéaire, et puisse ainsi diminuer l'erreur Abbe.
Cependant, lorsqu'on utilise réellement de tels systèmes, il faut aussi tenir compte des influences du monde réel et des autres incertitudes dans la conception. Pour cette raison, il est essentiel d'incorporer un facteur de compensation pour les erreurs causées par divers facteurs environnementaux et humains. Dans ce cas, SCL était situé au 35ème étage d'un immeuble de 48 étages, et pour cette raison il fallait tenir compte des vibrations provoquées par le vent et par la circulation.
Automatisation
En réponse à une intervention de l'opérateur, le support coulissant se déplace sur une position par défaut pour mesurer la ligne cible. Une fois à l'arrêt, l'interféromètre laser lit les données de position et l'appareil photo prend des images de l'échelle graduée.
Les images sont ensuite analysées afin d'obtenir la position actuelle (en utilisant la distance à partir de la position zéro jusqu'à la valeur de pixels équivalente affichée). La position est comparée à la position réelle calculée, et le système compense alors la différence en donnant des instructions au support coulissant pour qu'il se positionne avec une très grande précision.
Ensuite, l'interféromètre relève une autre mesure des données de position. Le processus entier est répété plusieurs fois jusqu'à ce que l'erreur soit inférieure à la distance spécifiée de pixel et jusqu'à ce que la position finale de la ligne soit obtenue.
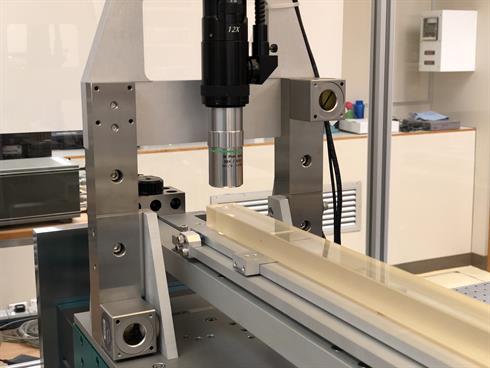
Source laser stabilisée avec précision
La conception du système utilise l'interféromètre laser Renishaw XL-80 pour compenser les erreurs Abbe dans le système de mesure, concernant tout déplacement angulaire subi pendant l'installation. Ceci peut concerner la linéarité du support coulissant, le placement de l'échelle linéaire ou la position du réflecteur, par exemple.
Avec une longueur d'onde nominale de 633 nm, l'interféromètre garantit une précision de mesure linéaire de ±0,5 ppm grâce à une source laser stabilisée avec précision et grâce à une compensation précise des facteurs environnementaux. On peut prendre des mesures avec une fréquence d’échantillonnage maximum de 50 kHz, à une vitesse linéaire maximale de 4 m/s et avec une résolution linéaire de 1 nm, même à la vitesse maximale. Toutes les options de mesure sont basées sur des mesures interférométriques, ce qui donne une plus grande confiance dans l'exactitude des données enregistrées.
L'interféromètre utilise une configuration de mesure linéaire classique. Le faisceau laser est divisé en deux faisceaux, lorsqu'il traverse le séparateur de faisceau S, un faisceau formant le faisceau de référence qui traverse la lentille de transfert T et le réflecteur R pour revenir dans la sonde de la source laser, et l'autre faisceau traverse les lentilles T1, T2 et T3 et le réflecteur R pour former un faisceau permettant de mesurer le changement de longueur.
Dans le système SCL, le XL-80 a été utilisé avec le compensateur XC-80. Les conditions environnementales sont mesurées à l'aide de capteurs internes pour la pression de l'air et l'humidité, avec des précisions respectives de 1 mbar et de 6 %, et également à l'aide de trois capteurs de température de matériaux et un capteur de température d'air, ayant respectivement des précisions de 0,1 °C et 0,2 °C.
Solution
La configuration du système de mesure de SCL est illustrée à la figure 1. Il utilise une méthode de déplacement dans laquelle l'appareil de mesure se déplace sur un portique au-dessus d'une échelle linéaire fixe pour mesurer la distance entre une position zéro et une graduation de l'échelle linéaire. L'ensemble est monté sur une table amortissant les vibrations, soutenue par un coussin d'air, et pour mieux régler la température, une enceinte est utilisée.
La mesure est effectuée par un microscope haute résolution, une mono-caméra CCD et un algorithme logiciel de comptage des pixels, montés sur un support coulissant sur coussin d'air, et entraînés par un moteur piézoélectrique CA/CC (courant alternatif/continu). Le support coulissant du système permet d'obtenir une linéarité de 0,9 µm pour un déplacement mesuré de 800 mm et une répétabilité de 20 nm. Le roulis, le tangage et le lacet maximum sont chacun de ±0,5 seconde d'arc.
Pour compenser toute erreur Abbe, le système SCL adopte alors une approche s'appuyant sur une réflexion de J.B. Bryan. Au lieu d'utiliser les données de mouvement angulaire pour calculer une valeur de compensation, il utilise un faisceau laser symétrique des deux côtés de l'axe de mesure. De cette façon, tout mouvement angulaire détecté, qui conduit soit à une augmentation, soit à une diminution de la mesure à cause de l'erreur d'Abbe, peut être automatiquement compensé.
Résultats
SCL a développé avec succès un système automatisé d'étalonnage d'échelle linéaire de très grande précision. Pouvant être utilisé sur des échelles linéaires de longueur maximum 750 mm, le système a une incertitude de mesure de seulement 0,15 nm - 0,41 nm.
Lors des essais du système, une échelle en verre de 500 mm étalonnée par le Korean Institute of Standards and Science (KRISS) a été utilisée comme un artefact pour valider le système d'étalonnage. Au total, 23 distances entre les graduations de l'échelle et le zéro ont été sélectionnées comme mesurandes.
Les résultats de mesures ont été comparés aux valeurs obtenues à partir de KRISS. Les différences entre les valeurs mesurées étaient toutes inférieures aux incertitudes concernant les mesures individuelles et bien inférieures au taux d'erreur normalisé de 0,7.
Dans le système, la racine quadratique de l'erreur Abbe, causée par 5 secondes d'arc dans les mouvements de tangage et de lacet du support coulissant du microscope pour une distance de 100 mm peut être calculée et est égale à 3,4 µm. Une analyse approfondie a montré qu'en intégrant l'interféromètre XL-80, ce taux d'erreur Abbe pouvait être réduit de 95 %.
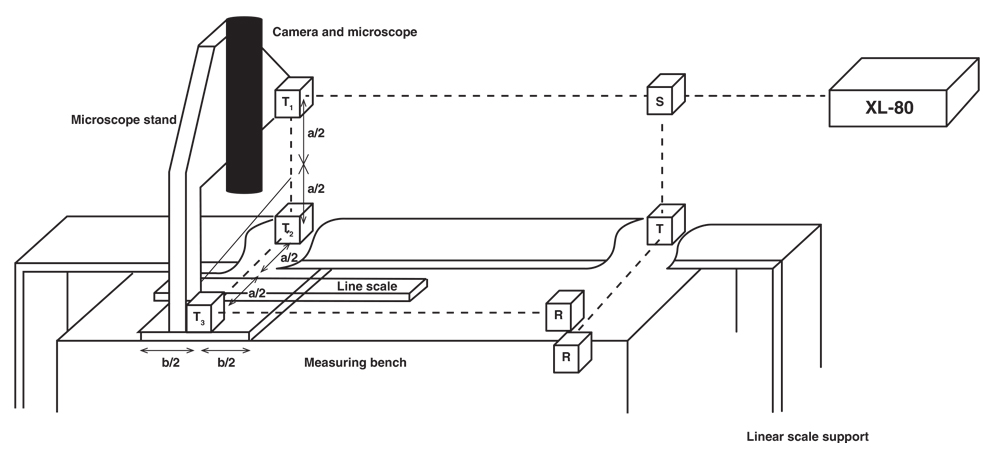