Cette page n'est pas disponible actuellement dans votre langue. Vous pouvez en afficher une traduction automatique avec l'outil Google Translate. Cependant nous déclinons toute responsabilité quant à ce service et nous ne contrôlons pas les résultats de la traduction.
Pour en savoir plus à ce sujet, contactez-nous.
Additives in Formula 1: technology of the future
Metal additive manufacturing is quickly becoming the technology of the future, but few people know the full extent of the opportunities it offers or the nature of the partnership - in this industry - between Renishaw and Scuderia Ferrari.
The item we are talking about is an exhaust manifold for F1 engines used for racing by Scuderia Ferrari. This is a continuously evolving part which is replaced after every race to benefit fully from all the advantages of research and also to minimise the risk of breakage. This component is subjected to both significant thermal and mechanical stresses and it comes into contact with extremely aggressive exhaust gases: this is why it is made of Inconel, a nickel-based alloy which proves extremely resistant to corrosion and high temperatures.
However, this is a relatively heavy material and difficult to machine owing to the removal of the swarf: the decision to use additive manufacturing made it possible to make a part that is on the whole extremely sturdy and light-weight thanks to the very limited thickness of the walls, something which would have been extremely difficult to achieve through mechanical machining. The need to produce pipes of the required thickness with the correct fluid dynamic shape and to incorporate auxiliary shapes, such as insertion points for sensors, would have made machining even more complex using traditional technology.
The only solution, aside from additive manufacturing, was casting, which, however, entailed considerably longer manufacturing times and near-zero flexibility, in the sense of the ability to adapt to research developments. In addition to development, even the ‘normal' routine needs different parts depending on the characteristics of the track on which the race is to be held: that means different moulds for different requirements and no possibility of change except with the creation of new moulds. Product development and the pursuit of improved performance lead to the conception of new solutions, which translate into changes in shape, with modifications (more or less evident) that still lead to different manufactured products which need to be produced and tested with a very quick turnaround time. The only technology capable of quickly producing finished parts from mathematical figures which differ each time is additive manufacturing: the only choice considering all these factors.
So in actual fact, additive manufacturing is not an alternative technology to mechanical machining, but rather an evolution of casting: complex parts can be produced without the need for moulds and without having to take into account the limitations of the passage of the molten mass due to its temperature and viscosity. Additive manufacturing and swarf removal machining are therefore complementary technologies, since the part produced using additive manufacturing subsequently needs to be machine-processed to achieve levels of finish and flatness that could not be obtained in any other way. This ‘complementarity' is particularly evident in this part where, in addition to the insertion of sensors mentioned earlier, grip points were incorporated into the part specifically to facilitate subsequent machining. Considering the shape of the part with very thin walls, the difficulty of machining the material and the need for absolute precision, this was the right solution for the subsequent finishing phases.
Essentially this part constitutes a concentration of all the aspects of a DfAM (Design for Additive Manufacturing), which includes the design of the main function of the part (optimising the flow of high temperature exhaust gases), of the auxiliary function (insertion of sensors) and of the process, such as the creation of grip points and references for subsequent mechanical machining.
A project that starts after the design
As we've seen, this is a complex part owing both to its conditions of use, to the material, and also to its particular design. In the case of Scuderia Ferrari, the design of the part is the sole responsibility of the team, which provides the maths, but how does one tackle all the issues linked to actual manufacturing?
The most significant steps were definitely the definition of the positioning of the part in the car, and the engineering of the related supports: indeed, a profound knowledge of the additive manufacturing process was required to achieve these steps. An additional challenge lay in the fact that the supports were under no circumstances to be fitted inside the gas passageways to avoid compromising the fluid dynamics.
Optimising the supports is extremely important because all the powder used to make the supports cannot be recovered and this affects the processing time in the machine as well as the amount of time it takes to remove it at the end of the task. At the same time, the supports have a very important function, which is to guarantee the geometric stability and define a path for the melt heat disposal.
To achieve this, supporting structures were made to allow a reduced quantity of traditional supports to obtain the savings we discussed earlier. The supports made are very thin and, if they are very long, there may be a risk of distortions; what's more, they are often melted with parameters that make them less ‘dense' than the main part so as to allow simpler removal later, while retaining their function. The supporting structure on the other hand has a more significant cross-section and it is molten with the same parameters as the part in order to achieve a significantly higher robustness.
The advantages of this choice were many: the correct direction of the part and the use of these supporting structures made it possible to reduce the length and quantity of the supports, with the ensuing reduction in processing time. Based on what we have seen so far, it is necessary to specify that every part modification devised by the Scuderia Ferrari team makes it necessary to reassess the entire car-positioning project to optimise the situation depending on the modifications made. At this stage, intervention may be necessary to various extents, which essentially ‘adapt' what has already been made to the new design or, also, start from scratch with the positioning and the creation of the related supports and supporting structures. In any case, intervention is always required, with the modification, the addition or removal of supports, and this is irrespective of the extent of the part modification.
A multitude of ideas in a single part
3D printing is combined with a simple, easy and immediate concept, while this technology manages quickly to give body and shape to even very complex objects which would often not have been able to be made using traditional technologies. The manufacturing cycle required to produce these parts, which as we've seen may incorporate various functions, entails a profound knowledge of the process in order to achieve the goals that have been set during the design phase.
A typical example of 3D manufacturing is the production of a part in a single piece which would have needed to be produced in several pieces subsequently assembled together had traditional technologies been used. This makes for savings in the subsequent assembly phase, but it also leads to lighter weight, less complex management, fewer possibilities of breakages and improved mechanical characteristics.
This is what is already known; what often doesn't emerge is that the moment the complexity of a part increases, this makes room at design level to add ideas and functions. In addition to the insertion into this part of seats for sensors, as mentioned earlier, let's look at the bigger picture: if we recall how cars were built until the 1930s, we'll see that there was a chassis onto which the body, the engine, the suspension etc. were fixed (separate parts, specifically)… Then, at one point, the chassis disappeared: the body, which had obviously been restyled and redesigned, became the self-supporting chassis itself and it started to include functions that it hadn't had beforehand. This potential gradually expanded in time, both in terms of the car body, as well as all the other subsets which were similarly redesigned. Perhaps it is also the name given to this process that simplifies the concept too much and deceives the potential user: digital casting would be closer to reality.
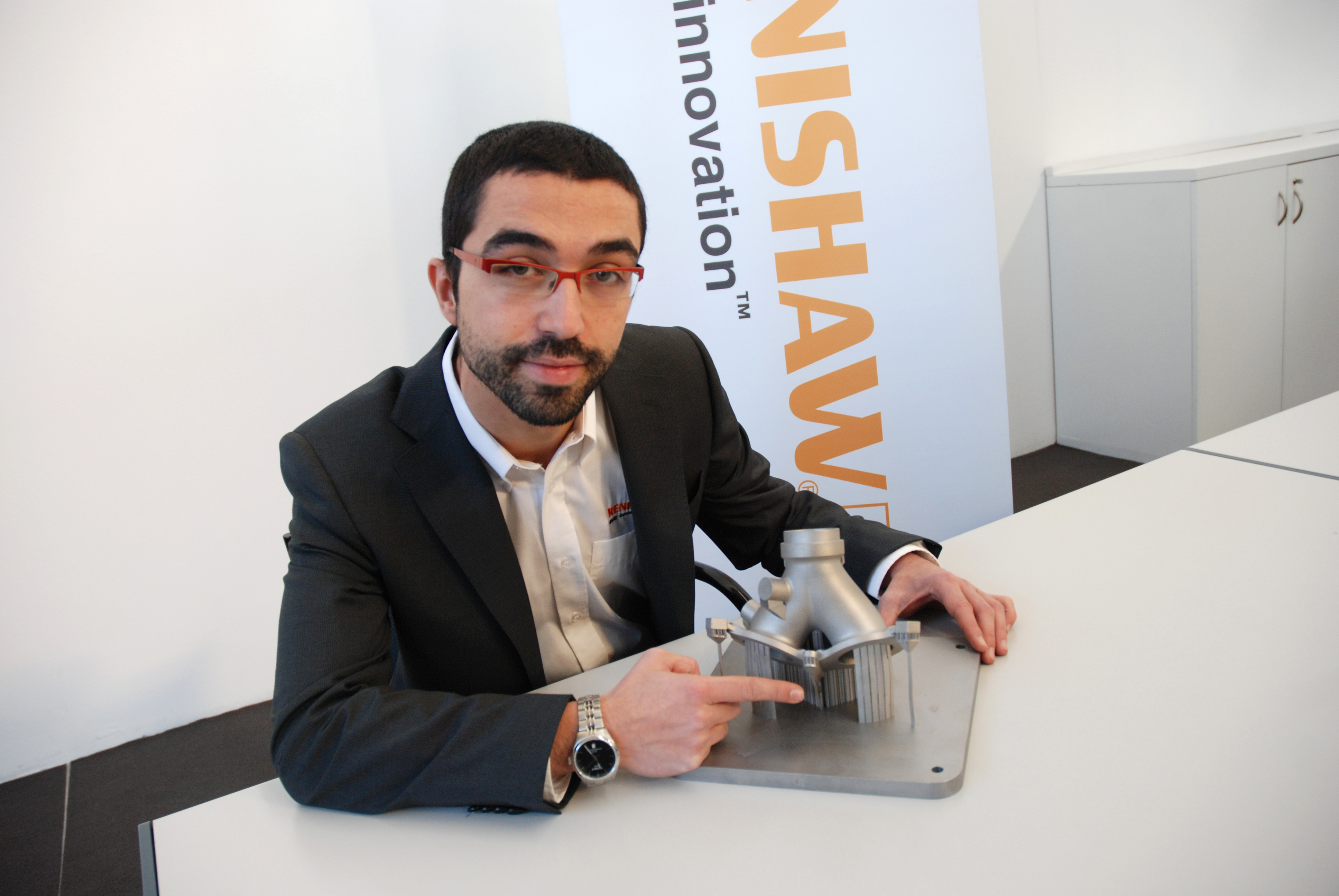
The racing industry was one of the first sectors to catch on to the specific advantages of additive technology. By specific advantages we mean that moment when, in a given sector, a reason, a factor emerges, making that technology become explosive. In practice, what happens is that at one stage, what is known as potential turns into a clear advantage, which could be time-related or linked to design freedom as in the case of racing, aerospace or medical, but it could also be merely economical, which is what is happening in many other industries. Since this sector entails complex shapes, weight reduction, single pieces as an alternative to assembled pieces, characteristics which cannot be achieved using traditional technologies, the potential of additive manufacturing is clear. Clearly each sector will have to turn this potential into objective advantages. When the performance levels required are extreme, designers are more sensitive to new potential, but the growth of this technology will make additive manufacturing increasingly accessible to various sectors.
Metal 3D printing in Formula 1
Racing fans appreciate the emotional aspect of races, with cars overtaking at the thrilling speed of 300 km per hour, the skill of the entire team that performs miracles, such as changing 4 tyres in just 2 seconds… then, behind it all, there are many, many other people who work with passion and dedication, who are committed to finding the perfect modification, the ideal improvement that will allow the driver to go that tiny bit faster on each lap, giving him an advantage, albeit a minimal one. This search is an exhaustive one, perhaps the most exhaustive there is in the world, comparable only to the space industry. In this search everything, and I really mean everything, is constantly up for debate, with a view to pursuing continuous improvement. In this context, additive manufacturing makes it possible to do away with the casting moulds and the tooling for mechanical machining, there remains only the design idea that is turned into a mechanical part.
For more information, visit www.renishaw.com/amguide
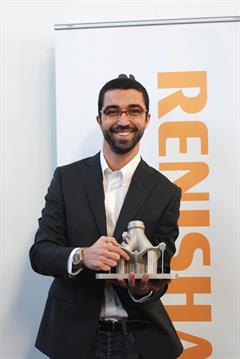
Downloads
If you would like to republish this article, only text and images used within the article can be published. Any questions can be directed to Renishaw's Additive Manufacturing marketing team, by emailing additive@renishaw.com.