Soluciones de inspección para optimizar los procesos de fabricación
La compañía Renishaw muestra cómo mejorar los procesos de mecanizado en el primero de una serie de cinco webinars divulgativos.
Barcelona, 19 de febrero de 2024. Renishaw, empresa especializada en sistemas de fabricación inteligente, medición y fabricación aditiva, ha impartido un webinar en el que ha mostrado, a más de noventa empresas interesadas, cómo las soluciones de inspección para máquina-herramienta pueden transformar un proceso de fabricación.
La presentación, titulada “Reglaje de herramientas, centraje e inspección de pieza en proceso”, se llevó a cabo el pasado 15 de febrero y es el primero de una serie de cinco webinars con los que Renishaw Ibérica quiere ofrecer un adelanto a su participación en la próxima Bienal Internacional de Máquina-Herramienta (BIEMH), que se celebrará del 3 al 7 de junio en Bilbao y en la que la multinacional dispondrá de un espacio de 132 m².
Impartido por Aitor López, Product Manager para máquina-herramienta de Renishaw Ibérica, el webinar se ha centrado en dos cuestiones: qué se puede conseguir con las soluciones de inspección para máquina-herramienta y cuándo se pueden utilizar los beneficios de estas soluciones en el proceso productivo. En relación con la primera cuestión, se ha explicado el funcionamiento y las ventajas asociadas de la sonda de inspección de pieza y también del sistema de medición de herramientas.
Soluciones de inspección para máquina-herramienta
La sonda de inspección de pieza es una solución que ayuda a determinar la posición y orientación de la pieza durante el reglaje, realiza la medición dimensional y de posición de puntos críticos, y verifica automáticamente la pieza, corrigiendo correctores de desgaste de la herramienta si hiciera falta. “Su uso evita procesos manuales en la alineación y en la actualización del cero pieza, lo que salva de errores humanos”, ha explicado Aitor López. “También evita el uso de utillajes complejos y la inspección posterior, lo que reduce tiempos muertos, permite una verificación inmediata al finalizar el mecanizado y genera informes automáticos del estado de la pieza”, ha agregado.
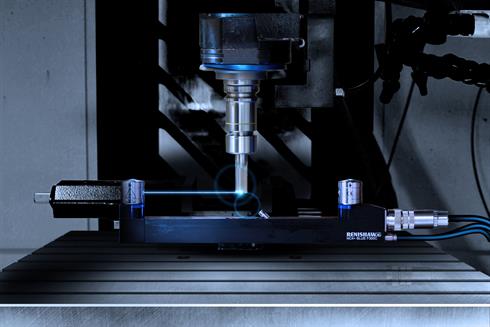
La otra solución de inspección que se ha destacado durante el webinar es el sistema de medición de herramientas, cuyo uso ayuda a determinar la longitud y el diámetro de la herramienta, además de a comprobar su perfil durante la preparación del trabajo. También verifica la rotura de esta en el ciclo de mecanizado y actualiza automáticamente sus correctores. Entre sus ventajas, se ha subrayado la posibilidad de medir la herramienta sin contacto, lo que evita dañar aquellas herramientas más delicadas o de pequeño diámetro, o la de hacerlo con el cabezal girando, lo que permite controlar la desviación causada por el salto del cabezal. Asimismo, un sistema de medición permite verificar la integridad de cada diente de la fresa o monitorizar y compensar la dilatación térmica de la máquina.
Así optimizan las soluciones de inspección un proceso de fabricación
“La respuesta a cuándo pueden utilizarse las ventajas de las soluciones de inspección en un proceso productivo es en todas las fases del ciclo de fabricación típico de una pieza mecanizada”, ha señalado Aitor López, con más de 16 años de experiencia en el sector. Estas fases a las que hace referencia son cuatro: previa al mecanizado (preventiva), justo antes del mecanizado (predictiva), durante el mecanizado (activa) y después del mecanizado (informativa). La etapa preventiva sería la base de la Productive Process Pyramid™, un proceso con el que la compañía proporciona un marco en el que identificar y controlar la variación de los procesos de mecanizado.
La fase previa al mecanizado presenta controles preventivos para la estabilidad del entorno (por ejemplo, la temperatura ambiente de un taller) y para la optimización de la condición de la máquina, con ventajas como la eliminación de los errores de máquina, la reducción de las paradas imprevistas y la producción de piezas correctas de forma uniforme. “De nada sirve poner a medir una sonda a 3.000 milímetros por minuto si luego la máquina tarda 30 milímetros en parar ese movimiento desde el punto de disparo y rompe el palpador durante el proceso”, ha valorado Aitor López con relación a algunas tecnologías del mercado que ofrecen grandes velocidades. En este sentido, Renishaw dispone de soluciones como el software Inspection Plus con tecnología SupaTouch, cuyo uso permite determinar automáticamente, sin depender de la experiencia de un técnico, la velocidad del palpado y de otros parámetros.
Reglaje de herramientas, centraje e inspección de pieza en proceso:
De nada sirve poner a medir una sonda a 3.000 milímetros por minuto si luego la máquina tarda 30 milímetros en parar ese movimiento desde el punto de disparo y rompe el palpador durante el proceso.
Una vez iniciado el mecanizado, se entra en una fase de controles activos como la medición durante el ciclo y la detección de roturas de la herramienta, lo que redunda en un aumento de las prestaciones y de la trazabilidad de los procesos, además de en una compensación de las condiciones ambientales. En consecuencia, también se incrementa la productividad y los beneficios. “Un ejemplo típico para una pieza unitaria con tolerancia estrecha sería realizar una pasada en semiacabado, medir el diámetro, corregir el error detectado y realizar una pasada de acabado final para obtener la tolerancia real”, ha explicado Aitor López, Product Manager para máquina-herramienta de Renishaw Ibérica.
La última fase viene después del mecanizado y está compuesta de controles informativos como el registro del proceso, la verificación en máquina y la generación de informes postproceso, con ventajas asociadas como la reducción de costes de inspección y de piezas desechadas o una mayor confianza en el proceso de fabricación. En este punto, Aitor López ha mostrado un caso real de la industria automotriz en el que se utilizó la sonda de escaneado en máquina con tecnología SPRINT™, adaptada a una fabricación en grandes series en la que el tiempo de ciclo es crítico.
Leer artículo anterior Volver al menu