Las soluciones de refrigeración conformal de Renishaw aumentan la productividad del moldeado
Antecedentes
Los limpiadores de alta presión de Alfred Kärcher GmbH & Co.KG, con sus inconfundibles carcasas color amarillo fuerte, son un utensilio habitual en muchos hogares alemanes, y están aumentando su popularidad internacional. La potencia y fiabilidad del aparato anima a usar el “Kärcher” en las tareas de limpieza diaria, dentro y fuera de la casa.
Para atender la creciente demanda internacional, Kärcher fabrica millones de unidades de su limpiador compacto cada año. Solo del limpiador de presión básico K2, salen más de dos millones de unidades de la fábrica de Obersontheim cada año. Sin embargo, a pesar de este nivel de producción, no consiguen satisfacer la demanda internacional.
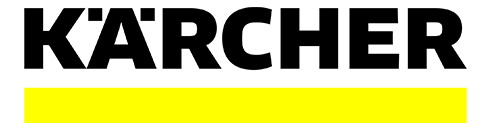
Retos
Una de las características más reconocibles de los limpiadores Kärcher es su carcasa de color amarillo fuerte. Esto también era uno de los principales cuellos de botella del proceso de fabricación. Por ejemplo, las carcasas del limpiador de la serie K2 se fabrican en seis máquinas de moldeado por inyección, con una capacidad de producción de 1.496 carcasas al día cada una. Esto no era suficiente para Kärcher, que cuenta con cuatro cadenas de montaje, con funcionamiento a tres turnos, y una capacidad de producción de 12.000 limpiadores de alta presión K2, ensamblados y empaquetados, al día.
Obviamente, una posibilidad sería añadir más máquinas de moldeado. Sin embargo, Leopold Hoffer, coordinador de moldeado de inyección en la fábrica de Kärcher en Obersontheim, opina que sería posible aumentar la productividad de los equipos existentes. “Nuestro objetivo era reducir la duración de los ciclos de los 52 segundos iniciales a entre 40 y 42 segundos”, explica. Para tratar de mejorar el tiempo de refrigeración de los moldes, se puso en contacto con LBC Engineering en Pliezhausen, empresa adquirida por Renishaw GmbH en mayo de 2013.
Los resultados han sido mejores de lo previsto. Renishaw nos suministró un paquete de mejoras completo, con un exhaustivo análisis y consideraciones sobre el molde utilizado para obtener los mejores resultados.
Kärcher (Alemania)
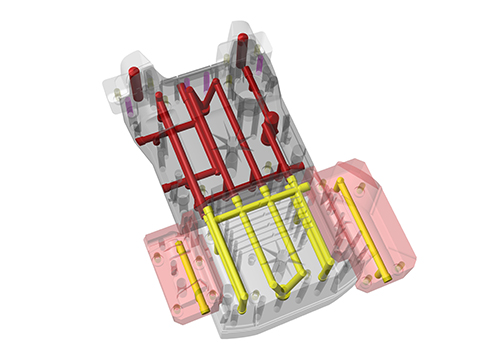
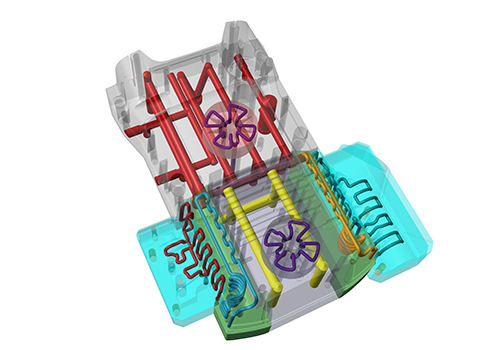
Solución
“La primera fase del proyecto consistía en obtener información de los moldes existentes para comprobar si el objetivo de Kärcher era factible”, puntualiza Carlo Hüsken, coordinador del proyecto de Renishaw. El proceso de diseño del moldeado por inyección existente utilizaba imágenes termográficas facilitadas por Kärcher, generadas en el software de simulación 3D-F Cadmould®. Se averiguó que la duración del ciclo era de 52 segundos, con un tiempo de refrigeración de 22 segundos, fundición a 220°C y extracción del molde a 100°C. La temperatura de la herramienta del molde se controlaba con agua a una temperatura de 35°C y un caudal de 10 litros por minuto. Los puntos de calor, detectados mediante termografía, también se modelaron, ya que estas áreas eran las responsables del aumento de la duración del ciclo y debían analizarse más detalladamente. Con estos datos, se completó una simulación de 20 ciclos, incluido un análisis de temperatura de las paredes.
Atendiendo a la sugerencia de Mr Hüsken, se mejoró el control de temperatura en el lado del inyector en la segunda simulación. La tuerca roscada de cobre berilio que ajusta la carcasa, se incluyó con refrigeración adicional, insertando dos canales de refrigeración convencional en el lado del inyector de la placa del molde.
A continuación, se ejecutaron dos simulaciones para evaluar las posibles mejoras mediante el uso de refrigeración conformal. La refrigeración del moldeado convencional se obtiene mediante una red de canales perforados. La perforación de los canales limita los tipos de geometría que pueden producirse y, aunque es adecuada para moldes sencillos, no proporciona la mejor refrigeración en modelos más complejos. La refrigeración conformal utiliza la fabricación aditiva metálica para producir la base del molde. La fabricación aditiva construye las bases en una serie de capas delgadas. La flexibilidad de este método permite incorporar canales de refrigeración con una complejidad prácticamente ilimitada. Generalmente, la refrigeración conformal se utiliza para mantener los canales a distancias iguales en el molde y, de este modo, conseguir una refrigeración más uniforme, o para concentrarse en áreas de puntos de calor conocidas donde es necesario acelerarla.
Las simulaciones mostraron que prácticamente todas las áreas de puntos de calor podrían mejorarse mediante refrigeración conformal, y reducir la temperatura de las paredes hasta en un 70°C.
Por último, en un área sin espacio suficiente en el molde para incorporar la refrigeración conformal, Kärcher realizó unas mejoras inteligentes en el diseño del producto para atenuar el problema.
En base a los resultados de las simulaciones, Renishaw presentó un exhaustivo plan de mejoras a Kärcher. En este, se indicaba que era posible utilizar refrigeración conformal para mejorar el control de temperatura de los puntos de calor del molde y, por consiguiente, obtener una tasa de refrigeración más uniforme en un tiempo más reducido. Se propuso un diseño de molde modificado, con la incorporación de dos bases de fabricación aditiva para integrar refrigeración conformal en los puntos de calor identificados.
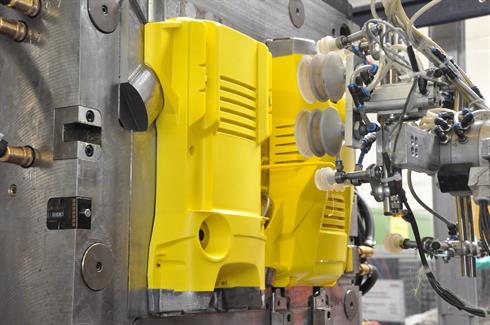
Resultados
Renishaw examinó los resultados del diseño del molde modificado mediante las imágenes termográficas proporcionadas. Los datos confirmaron que era posible reducir la temperatura de las paredes entre un 40°C y un 70°C. El tiempo de refrigeración se rebajó de 22 a 10 segundos, un 55% de reducción. Volker Neu, jefe del departamento de plásticos y tecnología de Kärcher, obtuvo las cifras que confirmaban que el nuevo diseño del molde, combinado con la realineación de determinados componentes periféricos (alimentación de material, sistemas de manejo, etc.), permitían rebajar la duración del ciclo de 52 a 37 segundos. En consecuencia, la capacidad diaria de una máquina podría aumentarse de 1.496 a 2.101 carcasas.
Después, Kärcher incorporó los cambios de diseño en los moldes restantes. Renishaw fabricó y suministró las conducciones híbridas de fabricación aditiva para estos moldes, con la colaboración activa de Mr. Hüsken para la fabricación del molde durante la fabricación de la herramienta.
Aunque escéptico al inicio del proyecto, Mr. Hoffer afirma, “Después de todo, los resultados han sido mejores de lo previsto. Renishaw nos suministró un paquete de mejoras completo, con un exhaustivo análisis y consideraciones sobre el molde utilizado para obtener los mejores resultados”.
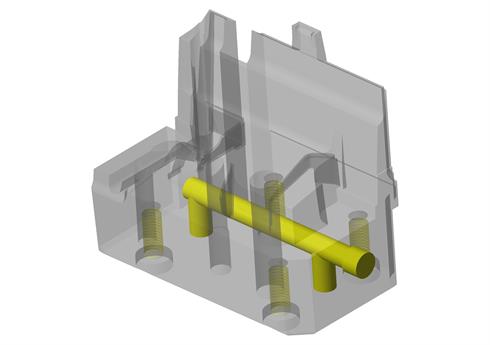
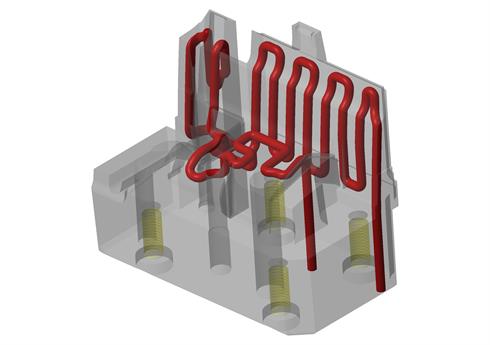
Renishaw siempre elabora sus soluciones para el cliente sobre una combinación de tecnologías. “En nuestro caso, esto suponía una combinación de tecnologías de refrigeración convencionales, bases de moldes específicas para el proyecto creadas con fabricación aditiva y soldadura fuerte”, añade. “A partir de estos ingredientes, obtuvimos la receta perfecta para la aplicación”.
En este proyecto, Mr. Hoffer ha adquirido unos conocimientos y experiencia importantes. “En adelante, prestaremos más atención a la refrigeración en la fase de diseño”, manifiesta. “Los cálculos de refrigeración van a ser una fase crucial en el diseño de cada molde en Kärcher. Con esta información, podemos decidir si aplicamos una decisión de refrigeración convencional o conformal”.
“La ayuda de Renishaw ha sido excelente. Para este proyecto, Renishaw ha sido la elección perfecta, además, la compañía será también el socio preferente para la supervisión de nuestros controles de temperatura en el futuro”, concluye Mr. Hoffer.
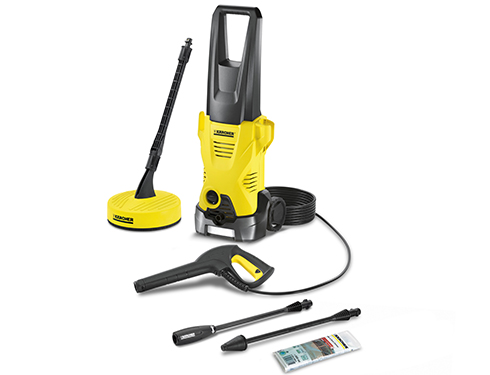
Imágenes: Creditos: Alfred Kärcher GmbH & Co.KG y Mr Gogoll