Las soluciones de fabricación inteligente reducen a la mitad el tiempo de producción de los componentes de turbinas de gas
Doncasters Precision Castings – Deritend, es un fabricante líder de perfiles aerodinámicos de turbinas de gas industrial de fusión a la cera perdida y mecanizados. Estos perfiles aerodinámicos están fabricados en superaleaciones de níquel y cobalto.
La empresa está decidida a seguir creciendo y, para demostrar su compromiso, invierte en la mejora continua mediante el aumento de producción y el prototipado rápido. En consecuencia, ha experimentado un fuerte aumento en la demanda de sus servicios de mecanizado, que apoyan sus inversiones en empresas de fundición. Este aumento de la demanda ha supuesto una considerable inversión de más de 2 millones de euros en Máquinas-Herramienta Mazak y software de infraestructura y fabricación para mecanizar con éxito más de 14 nuevos productos.
Antecedentes
Antes de realizar la inversión en centros de mecanizado de cinco ejes Mazak, ya trabajaban en centros de mecanizado convencionales de tres ejes con sistemas de fijación de posición fija. Los procesos, además de lentos, exigían un alto nivel de cualificación a los operarios de la máquina. La duración de un ciclo típico de componentes de inyección, incluido el reglaje y el mecanizado, era de cuatro horas, por tanto, no se podía satisfacer el aumento de la demanda. Además, el uso de sistemas de fijación de posición fija se consideraba una tecnología obsoleta y una solución costosa por el equipo técnico. Por consiguiente, se decidió realizar una inversión importante en tecnología de mecanizado y se encargaron tres centros de mecanizado vertical Mazak VORTEX i-630V/6. Estas máquinas permitirían a Doncasters realizar los trabajos de mecanizado en sus instalaciones y facilitar a sus clientes una solución centralizada.
Como parte de la inversión, las máquinas se equiparon con sondas de alta precisión RMP600 de Renishaw, con tecnología de galgas de esfuerzo patentada RENGAGE™. Con un rendimiento inigualable por debajo de la micra cuando se aplica a formas 3D y contornos complejos, las sondas eran la solución idónea para el trabajo que se iba a realizar. No obstante, en las reuniones para la aplicación inicial, se acordó que sería necesario soporte adicional, por consiguiente, Renishaw se puso en contacto con su empresa filial de productos de software de metrología Metrology Software Products Ltd (MSP).
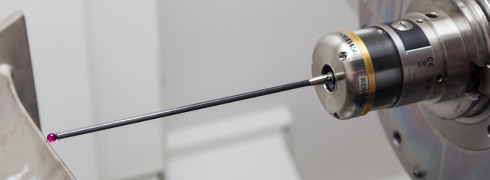
Retos
El objetivo consistía en mejorar el índice de piezas correctas a la primera y, de este modo, eliminar el potencial de errores y aumentar la productividad total. Ollie Macrow, director técnico de Doncasters, explica: “Cuando se trabaja con fundiciones de superaleaciones que cuestan miles de euros, tranquiliza saber que la pieza mecanizada va a ser correcta antes de cortar el metal. También se deben considerar los costes: aparte del precio de la fundición, también se pierde tiempo y, dado el material empleado, el coste relativamente alto de la herramienta. Además, determinados componentes no se pueden reutilizar, entonces, si no son correctos tras el mecanizado, pasan a material de desecho. Sabíamos que había que inspeccionar la pieza, pero nuestro reto era encontrar el modo de hacerlo correctamente sin fijaciones de posición fija”. Para agravar más el problema, la experiencia en inspección de la empresa era relativamente limitada, ya que únicamente se había aplicado para ajustes básicos y alineación de planos lisos sencillos, por lo que la ayuda de Renishaw era crucial.
Doncasters también quería prescindir de los costosos y lentos sistemas de fijación de posición fija. “Estos sistemas presentan numerosos inconvenientes: son caros; requieren un alto nivel de preparación del operario para colocar las piezas correctamente y, si una fijación se rompe, no es posible mecanizar la pieza porque no se puede alinear, por consiguiente, las fijaciones deben mantenerse en perfecto estado, lo que aumenta el tiempo y el coste. Nuestro reto consistía en reemplazar estas fijaciones por sistemas más sencillos de tipo modular y reducir la intervención humana en el proceso de reglaje”, comenta Ollie. También había que cumplir los objetivos de producción, por tanto, reducir los tiempos de reglaje era un punto a tener muy en cuenta al introducir las máquinas Mazak. Aunque la mayor parte del mecanizado se realizaba en nuestros talleres, todavía era necesario subcontratar algunas operaciones secundarias. No obstante, al aumentar la productividad, el objetivo es recuperar estas operaciones para realizarlas más adelante en nuestras instalaciones. “Esto tendrá un impacto positivo en nuestra productividad. Si podemos mecanizar en nuestros talleres, no tenemos que enviar las piezas fuera y esperar dos días hasta que las devuelvan”, explica Ollie.
Creo sinceramente que no podríamos estar mecanizando las piezas de fundición correctamente sin la ayuda de Renishaw y MSP. La ayuda que nos han brindado ha sido excelente; siempre están al teléfono cuando llamamos y nos visitan cuando es necesario.
Doncasters Precision Castings – Deritend (Reino Unido)
Solución
Tras revisar el proyecto, el técnico de aplicaciones de Renishaw, reconoció que el software NC-PerfectPart y NC-Checker de MSP, combinado con la sonda RMP600, sería la mejor solución total para los requisitos de Doncasters. Esta combinación de hardware y software innovador permite identificar errores de colocación de la pieza y rendimiento geométrico de la máquina antes de empezar a mecanizar. El primer paso consiste en ‘asignar' la Máquina-Herramienta para evaluar por comparación. NC-Checker verifica el rendimiento de la sonda antes de iniciar las comprobaciones de cinco ejes en la Máquina-Herramienta. De este modo, todos los aspectos de rendimiento de inspección y mecanizado se definen conforme a las tolerancias antes del reglaje y mecanizado de la pieza. La verificación de máquina puede ejecutarse de forma periódica, ya que solo necesita unos pocos minutos para completarse. Con el tiempo, la máquina seguirá funcionando conforme a los parámetros definidos produciendo piezas exactas.
NC-PerfectPart resuelve los problemas creados por una alineación deficiente de la Máquina-Herramienta. Esta función es especialmente importante para componentes de forma libre, superficies complejas y para mecanizado de cinco ejes. El reglaje de estas piezas puede ser muy lento y muy difícil de conseguir de forma precisa y uniforme. Para superar estas dificultades, se inspecciona la pieza en la sonda RMP600 con un programa creado a partir del archivo CAD del componente.
En base a esta medición inicial, se crea una alineación para eliminar posibles errores de colocación de la pieza en la máquina. A continuación, se carga la alineación en el control de la máquina y se calculan automáticamente las compensaciones para generar un programa automático perfectamente alineado para la pieza. El reglaje es automático, por consiguiente, las fijaciones ya no son cruciales para el proceso, se eliminan los posibles errores de reglaje manual y el tiempo de reglaje necesario, incluso para los componentes más complejos, se reduce a minutos.
También se pueden considerar elementos como la condición del material, los sistemas de carga de palés y la temperatura durante la fase inicial del proceso de mecanizado, para reducir el riesgo de fabricar piezas incorrectas.
Después del mecanizado, NC-PerfectPart puede confirmar la precisión del componente terminado antes de retirarlo de la Máquina-Herramienta e inspeccionarlo en una MMC.
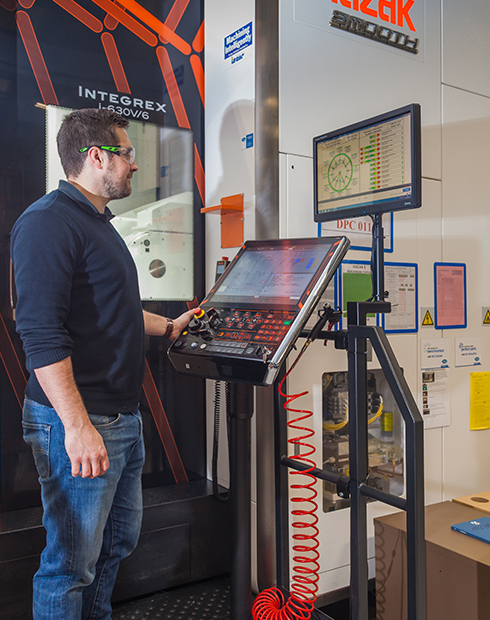
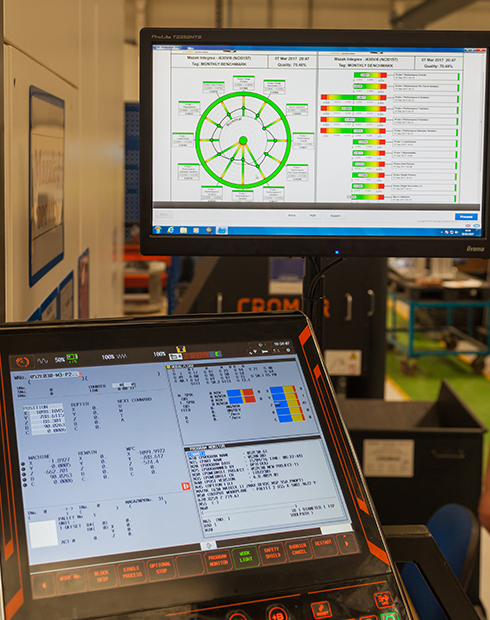
Resultados
Antes de instalar la sonda RMP600 y el software MSP, se empleaban cuatro horas en el reglaje y mecanizado de un inyector de turbina de gas industrial típico. Ahora, la misma pieza se puede inspeccionar, mecanizar y verificar en menos de dos horas, por consiguiente, Doncasters ha aumentado su productividad en un 50%. En componentes más complejos, el tiempo de mecanizado podría ser de hasta ocho horas, bajo la supervisión de un técnico altamente cualificado durante el proceso. Estas piezas se fabrican ahora en el mismo ciclo de dos horas que las piezas sencillas, lo que genera un ahorro de costes aún mayor. Mediante la colaboración con Renishaw y MSP, Doncasters ha mejorado sus sistemas de alineación para obtener unos resultados totales mejores; también se han mejorado la relación entre las mediciones en máquina, los resultados de MMC y los datos del sistema de exploración Bluelight.
Sobre este éxito, Ollie Macrow comenta: “Lo que ha ocurrido aquí es ciertamente una historia positiva, y nunca habríamos llegado hasta aquí sin la ayuda de Renishaw y MSP”.
Y continúa, “cuando decidimos comprar las máquinas, no reunimos con Mazak y nos preguntamos “¿Cómo lo vamos a hacer?” No creían que fuera posible con nuestros equipos actuales, entonces, se unieron Renishaw y MSP y nos facilitaron la solución que necesitábamos. Nuestros clientes nos felicitan por la considerable mejora de nuestra tasa de piezas correctas a la primera. Realmente siento que no estaríamos mecanizando las fundiciones con éxito sin la ayuda de Renishaw y MSP. El apoyo que recibimos de ellos es excelente; siempre disponibles al teléfono si llamamos, e “in situ” cuando los necesitamos.