KMT Lidköping el gigante de la energía verde rectifica con precisión micrométrica
Los aerogeneradores son muy llamativos y todos están de acuerdo en que cada vez son más demandados para la generación de energías renovables. La fabricación de enormes componentes, como los rodamientos, supone nuevos retos para la ingeniería, y KMT Lidköping los ha resuelto satisfactoriamente.
Con sede en Lidköping, en el centro de Suecia, la nueva máquina de rectificado en duro VTG4000 (rectificadora cilíndrica vertical) emplea una combinación de encóderes lineales y angulares ópticos Renishaw SiGNUM (obsoleto, actualización alternativa: encoder VIONiC con regla RTLC20 o encoder RESOLUTE con regla RTLA) para lograr la precisión necesaria, con robustos encóderes magnéticos Renishaw en los ejes expuestos de los cabezales de corte.
Eive Johansson, jefe de diseño de VTG de Lidköping, comenta “Nuestra mayor máquina ha llegado a albergar piezas de hasta 600 mm de diámetro, sin embargo, la VTG4000 puede manejar diámetros que superan los 4.000 mm, el tamaño de los rodamientos de las turbinas más grandes. El torneado en duro y el rectificado pueden ser muy exigentes, donde la precisión de posicionamiento es muy importante, ya que influye directamente en la calidad de los rodamientos acabados. Una máquina de tamaño estándar, con husillos a bolas en los ejes, puede mantener una desviación de forma de 3 µm, sin embargo, a pesar de la considerable diferencia en tamaño relativo, la VTG4000 ha demostrado una excepcional desviación de forma de menos de 1 µm, con una resolución de avance en pasos de 0,1 µm.”
El Sr. Johansson prosigue, “En el corazón de la máquina Lidköping se encuentran las guías lineales. La combinación de las guías hidrostáticas, las juntas de aire y los motores lineales crea un sistema rígido y preciso que no necesita mantenimiento. Para obtener rigidez dinámica se necesita una ganancia alta, y esa ganancia está vinculada a la calidad de las reglas del encóder. También supone una gran diferencia que los encóderes angulares lleven la escala integrada directamente en el anillo.”
La primera vez que vio los encóderes Renishaw SiGNUM fue en la feria EMO 2007 de Hannover, y a partir de ese momento se puso en marcha un riguroso proceso de pruebas en Lidköping. El Sr. Johansson afirma, “La elección de Renishaw fue fácil, comparamos las distintas reglas ensambladas en nuestra guía de referencia y compramos la que ofrecía el mejor rendimiento. También consideramos el hecho de que los encóderes pudieran suministrarse en longitud continua de al menos 4,5 m y SiGNUM ofrecía las mejores posibilidades. Los encóderes Renishaw son también más resistentes a la suciedad. Ahora, hemos instalado encóderes Renishaw en las cuatro guías lineales y, como esperábamos, no hemos tenido ningún problema.”
“La mesa giratoria sigue el mismo principio de diseño, con engranajes axiales y radiales hidrostáticos, juntas de aire y motores de par para la tracción. Realizamos los mismos análisis y elegimos los encóderes angulares Renishaw SiGNUM.”
La elección de Renishaw fue fácil, comparamos las distintas reglas ensambladas en nuestra guía de referencia y compramos la que ofrecía el mejor rendimiento. También consideramos el hecho de que los encóderes pudieran suministrarse en longitud continua de al menos 4,5 m y SiGNUM ofrecía las mejores posibilidades. Los encóderes Renishaw son también más resistentes a la suciedad. Ahora, hemos instalado encóderes Renishaw en las cuatro guías lineales y, como esperábamos, no hemos tenido ningún problema.
KMT Lidköping (Suecia)
Instalación del encóder
Todos los encóderes de Renishaw están equipados con un LED integral de instalación que agiliza el proceso y hace innecesario el uso de osciloscopios y otros complicados equipos de reglaje.
“Una de las principales características de los encóderes Renishaw es su facilidad de instalación”, comenta el Sr. Johansson. “Con la regla instalada y el cabezal de lectura colocado en una posición aproximada, las luces indicadoras muestran claramente si la alineación de los elementos es correcta para, a continuación, realizar los ajustes finales.”
La alta calidad aumenta la seguridad
Sería fácil presuponer que un aerogenerador se compone de un único rodamiento, pero en realidad tiene tres tipos distintos. Sorprendentemente, el paso de rodamientos en la base de las aspas es el más alto, hasta Ø4.000 mm en muchos aerogeneradores y, probablemente, lo más importante es que el paso de las aspas puede ser ajustado. Cuando está en funcionamiento, el paso debe ajustarse a la velocidad del viento, de lo contrario, la resistencia de las aspas podría hacerlas caer, por lo que es imprescindible utilizar unos rodamientos de alta calidad. Además, cuando la velocidad del viento es muy alta, generalmente más de 25 km/h, es necesario crear un mecanismo de parada para proteger las aspas. También juegan un papel importante los rodamientos del eje principal y los de ladeo, ya que permiten el giro de la turbina.
Todas las operaciones en una configuración
La máquina VTG4000 ha sido diseñada de forma que no sea necesario retirar el componente entre las operaciones de mecanizado, realizando el torneado y el rectificado con dos cabezales individuales. Los dos cabezales pueden configurarse según sea necesario, normalmente rectificado/torneado o torneado/rectificado. Esto significa que el eje x de la máquina, que lleva los dos cabezales al lado opuesto del componente, debe tener una longitud de 4,5 m, de forma que las herramientas de torneado y rectificado puedan tener acceso al exterior de la pieza.
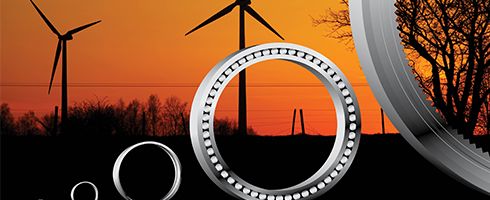
Máquinas diseñadas para maximizar el rendimiento
La máquina VTG4000 es de gran solidez y algunas de sus piezas pesan hasta 35 toneladas. Es por tanto muy resistente a la distorsión y a la variación térmica, con la asistencia de un minucioso control hidrostático de la temperatura del aceite y el refrigerante.
Henrik Jonsson, jefe de planta de Lidköping, explica con más detalle la construcción de la máquina: “las guías hidrostáticas, que venimos utilizando desde 1970, se utilizan para todos los ejes y el motor lineal. Esta combinación es más rápida, más precisa y permite una aceleración y deceleración mucho mayor. Si pensamos que es posible mover un eje rotatorio de 25.000 kg con un dedo, nos damos cuenta de la gran capacidad del sistema hidrostático.”
Otro factor crucial para la fabricación de estos enormes rodamientos es la condición térmica de la pieza de trabajo. Durante la producción, la pieza deberá aclimatarse a las condiciones de la fábrica durante un mínimo de 48 horas antes de cargarla en la máquina.
Funciones que mejoran la automatización de la máquina
Los sistemas de encóder magnético LM10 de Renishaw están equipados con ejes B en los cabezales de rectificado. Estos encóderes están expuestos a las condiciones más hostiles del entorno de trabajo, no obstante, con un diseño sin contacto, no óptico y sellado IP68, no pueden verse afectados por el refrigerante o la viruta. El encóder LM10 admite un recorrido máximo de 100 metros, con una alta velocidad de funcionamiento hasta 25 m/s (4 m/s a 1 µm de resolución), disponible en modelos de entrada digital o analógica, con una gama de resoluciones a elegir por el cliente.
La máquina utiliza también una sonda de contacto de transmisión de señal por radio Renishaw RMP60 para ajustar con precisión la pieza en el sistema de coordenadas de la máquina. Después de colocar la pieza en la mesa de la máquina VTG4000, la sonda RMP60 se carga en el cambiador de herramientas del mismo modo que una herramienta de corte y se utiliza para localizar la posición exacta de los principales elementos en cuestión de segundos. Con los datos obtenidos, se actualiza el sistema de coordenadas durante el ciclo para iniciar inmediatamente el mecanizado, con los datos precisos de la posición y las medias reales de la pieza.
Para automatizar otras tareas manuales potencialmente muy largas, pueden cambiarse los discos de rectificado mediante un cambiador de herramientas automático. Aunque es posible utilizar un disco de rectificado general para muchas tareas, a menudo es necesario cambiarlo por un disco para rectificado de caras, uno angular o un perfil a medida, también denominado ‘disco de forma’.
Adaptación satisfactoria a los nuevos retos
Al igual que los propios aerogeneradores, la VTG4000 es una máquina tan impresionante en cuanto a tamaño y capacidad que produce en el observador una sensación de sobrecogimiento. La fabricación de máquinas del tamaño de la VTG4000 supone, sin duda, un cambio significativo respecto a los trabajos anteriores de Lidköping, pero al integrar las tecnologías adecuadas, como los encóderes Renishaw, los retos se han cumplido satisfactoriamente.
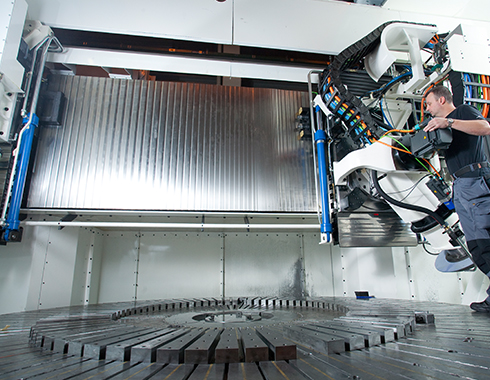