Por el momento, esta página no está disponible en español. Puede obtener una traducción automática mediante la opción de traducción de Google.
No podemos responsabilizarnos de este servicio puesto que podemos no verificar los resultados de la traducción.
Si desea más información, póngase en contacto con nosotros.
Instron® equips its new ElectroPuls™ linear-torsion tester with advanced Renishaw encoders
Instron, headquartered in Massachusetts, USA, is a global market leader in the materials testing industry. It manufactures and services a comprehensive range of materials testing equipment and accessories for the research, industrial and academic sectors.
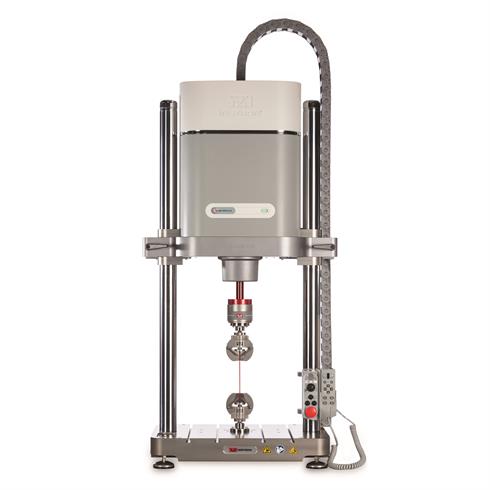
A variety of Instron systems test samples ranging from components for jet engines to medical syringes. Instron has just launched an advanced bi-axial variant of the ElectroPuls E3000 All-Electric test instrument. The E3000 is a compact table-top instrument comprising: a load frame, crosshead with combined linear/torsion actuator, Dynacell load cell and T-slot table for fixing samples.
The state-of-the-art ElectroPuls series includes the E1000, E3000 and E10000 fatigue test systems. These are suited for biomedical / biomechanical research applications and feature a wide dynamic performance range and low force characteristics. ElectroPuls is all-electric and utilises linear motor technology, which eliminates the need for ball / lead-screws and enables slow-speed static tests through to high-frequency dynamic tests at over 100 Hz.
The new E3000 linear-torsion is a smaller-scale equivalent of the E10000 linear-torsion system and includes a rotation axis with a standard range of ±135° as well as optional multi-turn capability for applications such as orthopaedic bone-screw testing. An ElectroPuls bi-axial linear-torsion test can be conducted on most materials and has found applications in testing inter-vertebral disc prostheses, various bio-materials, athletic footwear and elastomeric components.
The use of the RESOLUTE ring encoder for the rotary axis perfectly complements the linear encoder. It provides superior resolution, accuracy and mechanical simplicity over our previous belt driven, conventional rotary encoder.
Instron (USA)
An LVDT problem
ElectroPuls systems are intended for fatigue testing, which examines the behaviour of materials under fluctuating or cyclic loads in the elastic regime.
Conventional servo-hydraulic test instruments use a linear variable differential transformer (LVDT), a type of inductive absolute encoder, to determine the linear direction of travel and position of the actuator. ElectroPuls is driven by a linear synchronous motor and requires additional high-quality velocity feedback for precise dynamic control - due to the challenges of driving linear motors with lower inherent damping than traditional rotary designs. While suitable for position control, an LVDT suffers from relatively poor signal stability and cannot, therefore, produce accurate velocity measurements. An LVDT may also be susceptible to magnetic fields produced within a linear motor and exhibits increasing non-linearity over longer axes.
It is apparent that optical encoders, with intrinsically better signal stability and higher accuracy, are superior in this application. Instron decided that an absolute optical encoder, capable of providing absolute position information without homing, would be the best solution for their bi-axial systems. This offers several advantages over an earlier servo-mechanism using an optical linear incremental encoder in conjunction with an LVDT.
Instron specified that the chosen absolute optical encoder be reliable, highly-accurate, compatible with BiSS® serial communications, easy to set-up and install and non-contacting to eliminate friction / wear and, hence, mechanical hysteresis error. Renishaw's RESOLUTE is the only absolute optical encoder to support ElectroPuls controllers and satisfy all other criteria - while offering linear resolutions of 1 nm and speeds beyond 20 m/s. This market-leading performance has resulted in RESOLUTE encoders being chosen for both axes on the E10000 and new E3000 test-frames.
Principal mechanical engineer for Instron ElectroPuls, at Instron's UK-based European headquarters, Mr Graham Mead, explains: “We have previously used an LVDT to provide the absolute position feedback needed to commutate a linear motor. In addition, an incremental optical encoder was employed to provide the measurement and control accuracy. With the RESOLUTE absolute linear encoder we are able to get all the functionality and accuracy from one device. The reduced assembly complexity and number of parts allows much simpler set-up and maintenance-free operation. The use of the RESOLUTE ring encoder for the rotary axis perfectly complements the linear encoder. It provides superior resolution, accuracy and mechanical simplicity over our previous belt driven, conventional rotary encoder.”
High performance solution
The ElectroPuls E3000 linear-torsion machine requires both linear and rotary absolute encoders for the linear and rotational axes respectively. Linear position is provided by a RESOLUTE readhead and an RTLA tape scale with ±5 µm/m accuracy and 5 nm resolution. Angular position is determined by another RESOLUTE reading a 115 mm diameter RESA ring, offering an impressive resolution of 0.019 arc second and an encoder accuracy of ±2.5 arc second.
Key features of RESOLUTE that enhance mechanical test performance include:
- Reliability: data from the encoder must be trustworthy. Sample tests, in many cases, cannot be repeated so it is essential that results are accurately measured. Failures such as miscounting are unacceptable because they lead to erroneous readings and potentially incorrect conclusions about a sample. RESOLUTE has high tolerance to dirt, scratches and grease that can cause other encoders to miscount. An independent position-checking algorithm also ensures that any potential problem is flagged long before it reaches the controller.
- Fine resolution and low noise (jitter): strain measurements on stiff samples demand position encoders with higher resolutions. Low jitter, of less than 10 nm RMS, improves displacement sensitivity and allows more information to be gleaned from the sample.
- High system accuracy and speed: The behaviour of dynamic materials-testing machines must be precisely controlled with either strain feedback from an encoder or stress feedback from a load cell. Standards body ASTM International tolerates a deviation of up to 2% of the maximum applied load before a test becomes invalid. Higher accuracy and excellent dynamic performance also permit more detailed analysis of samples at failure, contributing to the accuracy of drawn conclusions.
- Easy installation: RESOLUTE, as a single-track absolute optical encoder, allows far wider installation tolerances than traditional multi-track competitors. RESOLUTE's integral set-up LED further simplifies installation during test frame manufacture and servicing.
Pushing the limits of ElectroPuls
Instron knew of the limitations of LVDT technology and were waiting for a superior encoder solution to fulfil their needs. RESOLUTE with BiSS protocol offers Instron advanced capabilities that continue to support new developments in the ground-breaking ElectroPuls series. From evaluating the tensile strength of sutures to durability testing of fracture fixation devices, the ElectroPuls systems provide a uniquely versatile testing platform. Renishaw's close working relationship with Instron is mutually beneficial, and continues to drive future product innovation and development across both companies.
Customers interested in further information about the E3000 linear-torsion system should refer to Instron's main website.
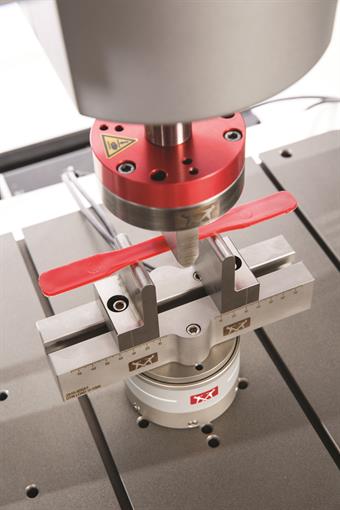