Fabricante de bicicletas a medida adopta la fabricación aditiva de la mano de Optimus3D
Mantener la consistencia y la calidad de los componentes de una bicicleta de titanio fabricados a mano no es fácil, se necesita preparación, cuidado y tiempo. Angel Cycle Works retó a Optimus3D a crear una solución de fabricación aditiva metálica (FA) que permitiera producir parte de los soportes del tubo de la cadena en tiradas cortas conforme a un estándar de calidad perfectamente uniforme.
Historial
Optimus3D proporciona un servicio de fabricación aditiva completo a empresas de un amplio abanico de sectores industriales, como el aeroespacial, la automoción, la industria general y el sector médico. Ofrece una solución completa que incluye el diseño del componente, la producción de prototipos y en serie, post-proceso y metrología.
Con sede en el Parque tecnológico de Álava en Vitoria-Gasteiz, en el Norte de España, la empresa sirve a clientes internacionales y locales proporcionando acceso a la última generación de máquinas y software de impresión 3D. Su experiencia en fabricación aditiva les permite reducir la complejidad, el peso y el coste de los componentes, y aumentar la calidad y fiabilidad de las piezas.
La empresa española Angel Cycle Works fabrica cuadros y componentes de bicicleta reconocidos internacionalmente. Mediante la fabricación a mano de los cuadros y los componentes de titanio a medida, operan la tecnología de bicicletas más vanguardista, produciendo bicicletas de carretera de aventura, montaña y ciclocross.
Dedicados a la producción de componentes de alta calidad y resistencia, que dependen principalmente de la soldadura manual y la producción en tiradas cortas, en Angel Cycle Works estaban interesados en investigar la fabricación aditiva como alternativa, por lo que consultaron a Optimus3D en busca de una nueva solución.
Pablo Capellan, jefe de proyecto de Optimus 3D comenta, “Nuestra experiencia en fabricación aditiva se debe en gran medida a nuestro profundo conocimiento de fabricación e ingeniería inversa. Por consiguiente, podemos adaptar más rápidamente los requisitos del cliente al proceso de impresión 3D y utilizar el espectro completo de las prestaciones de FA”.
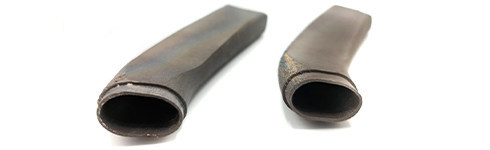
Componente de titanio del basculante impreso en 3D en el sistema RenAM 500S
Nuestro planteamiento es muy sencillo. Al fabricar el componente en horizontal, podemos reducir el tiempo de producción de la fabricación y ayudar a Angel Cycle Works a cumplir su presupuesto. También nos permitió detectar y gestionar mejor las deformaciones, ya que el componente del soporte de la cadena es largo y estrecho, con unas medidas de 35 x 20 x 115 mm”.
Optimus3D (España)
Comparación de parte del tubo de soporte de la cadena fabricado a mano con uno impreso en 3D componente
Objetivo
“Para Angel Cycle Works, la parte más complicada de fabricar el componente de titanio manualmente consiste principalmente en el propio metal. Sencillamente, no es uno de los materiales más fáciles con los que trabajar. Sobre todo, en la soldadura manual, ya que pueden producirse deformaciones en el componente, por lo que mantener las especificaciones reales del modelo CAD tridimensional puede ser verdaderamente difícil”.
Capellan continúa, “Dicho esto, incluso con la alternativa del proceso de fabricación aditiva, tanto si se construye el componente fundiendo el metal en capas o por deposición, el titanio sigue siendo un reto”.
Para producir el componente en serie, maximizar la productividad del proceso de fabricación aditiva era otro criterio fundamental para Optimus3D. Además de garantizar la precisión y fiabilidad total del componente, también era necesario asegurar que cada volumen de fabricación produjera el máximo número de piezas, para hacer el proceso lo más rentable posible.
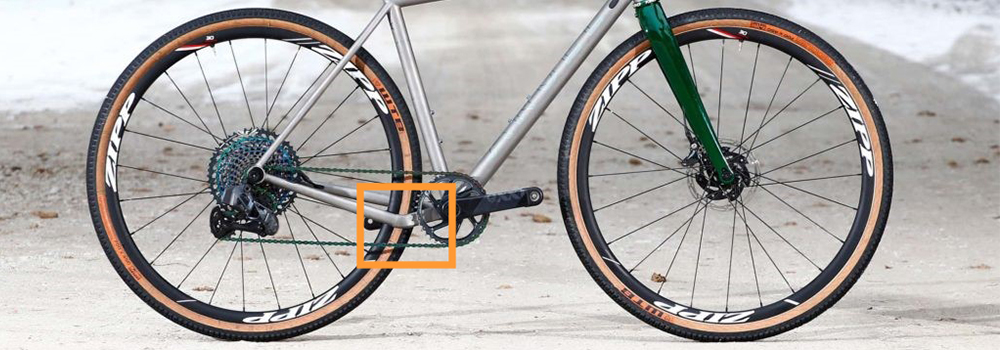
El recuadro resaltado en naranja muestra la posición del componente de titanioimpreso en 3D
Solución
Optimus3D propuso utilizar el sistema Renishaw de un láser de fabricación aditiva RenAM 500S. Diseñado expresamente para la construcción de componentes metálicos en un entorno de producción, usando la tecnología de fusión en lecho de polvo (también llamado fusión por láser), el sistema dispone de un amplio volumen de construcción de 250 x 250 x 350 mm.
Para el componente de bicicleta de Angel Cycle Works, es importante el uso de fabricación en atmósfera inerte de Renishaw (una cámara de vacío rellena con gas argón de alta pureza) que garantiza un entorno de construcción de muy alta calidad para todos los metales cualificados, incluido el titanio Ti6AI4V, el polvo metálico utilizado en este caso.
Teniendo en cuenta la estructura y las dimensiones del componente, la fabricación en orientación vertical parecía la opción obvia, y generalmente óptima. No obstante, conociendo el potencial problema de deformación y la necesidad de conseguir la máxima productividad, Optimus3D decidió construir la pieza en posición horizontal.
Capellán explica, Nuestro planteamiento es muy sencillo. Al fabricar el componente en horizontal, podemos reducir el tiempo de producción de la fabricación y ayudar a Angel Cycle Works a cumplir su presupuesto. También nos permitió detectar y gestionar mejor las deformaciones, ya que el componente del soporte de la cadena es largo y estrecho, con unas medidas de 35 x 20 x 115 mm”.
Como esperábamos, al fabricar el componente horizontalmente, directamente desde el archivo CAD, se generó una distorsión inaceptable de 0,375 mm en la parte más vulnerable. Para corregir este error, en colaboración con los ingenieros de Renishaw, llegamos a una práctica solución basada en la simulación de elemento finito.
Alex Garcia, ingeniero de aplicaciones de Renishaw, explica, Mediante el software de otro fabricante Simufact Additive, pudimos simular perfectamente el proceso de fusión de capas de polvo del sistema RenAM 500S. De este modo, pudimos determinar un factor de compensación preciso para "pre-distorsionar" el diseño del componente.
Análisis mediante el software Simufact del componente de titanio soporte construido en fabricación aditiva.
Resultados
Mediante la fabricación aditiva metálica, Angel Cycle Works puede producir los componentes de titanio de la bicicleta, que antes fabricaba manualmente, con un alto nivel de consistencia, características de peso y resistencia mejoradas, y en cantidades que permiten atender mejor la demanda de los clientes.
Aunque puede parecer contrario a la lógica más común, la decisión de Optimus3D de construir los componentes en posición horizontal, empleando el software de simulación para ajustar el diseño para la fabricación, ha conseguido reducir el peor caso de deformación de 0,375 a 0,086 mm, perfectamente dentro de la tolerancia del componente de 100 µm.
Esta innovadora solución de fabricación aditiva metálica supone que cada fabricación de la máquina RenAM 500S es capaz de imprimir hasta 50 piezas idénticas de una sola vez, con un tiempo de preparación mínimo. El coste de los componentes se ha reducido espectacularmente y se han agilizado las operaciones de la cadena de suministros.
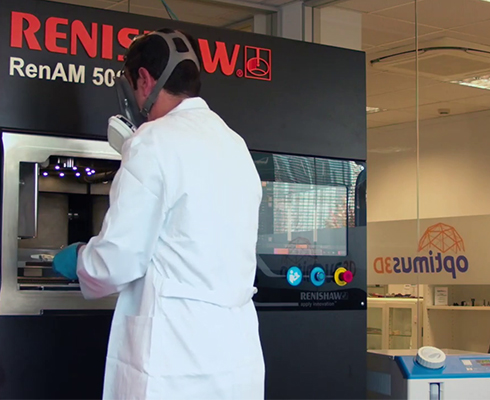
Sistema RenAM 500S de Renishaw en la fábrica de Optimus3D en el Parque tecnológico de Álava en el Norte de España