La alineación láser agiliza las comprobaciones del ensamblaje de la Máquina-Herramienta
La precisión y fiabilidad final de una Máquina-Herramienta dependen en gran medida de la comprobación de la alineación durante el ensamblaje. Para la producción de Máquinas-Herramienta en grandes cantidades, la fiabilidad del proceso de comprobación de la alineación es crucial. En busca de alternativas a las técnicas de medición de errores tradicionales, Hurco Manufacturing Ltd. (Hurco) eligió el sistema de alineación láser XK10 de Renishaw para aumentar la precisión y el rendimiento.
Historial
Como auténtico pionero en la aplicación de tecnologías informáticas para el diseño de Máquinas-Herramienta, Hurco es un proveedor internacional de máquinas CNC. Fundada en Indiana, EE. UU. en 1968, la empresa fabrica una extensa gama de productos como máquinas CNC de 5 ejes, tornos CNC multi-eje, centros de mecanizado vertical y centros de torneado.
Su base de clientes internacionales incluye empresas de herramientas de precisión, fabricantes de matrices y moldes, talleres independientes, fabricantes especializados con tiradas de producción cortas y herramientas de fabricación metálica para OEMs. La cartera de productos de la empresa incluye tres marcas muy conocidas: Hurco, Milltronics y Takumi.
Hurco Manufacturing se estableció en Taiwán en 1999 y es actualmente responsable de la fabricación y montaje de la gama completa de Máquinas-Herramienta de Hurco. Para garantizar que se cumplen los requisitos de precisión, seguridad y fiabilidad de la Máquina-Herramienta, es imprescindible un control estricto de cada paso del proceso de fabricación.
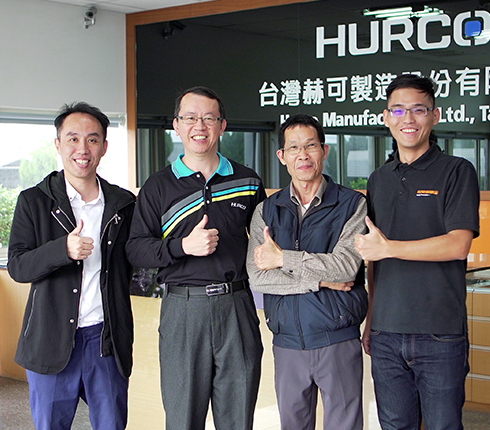
Integrantes del equipo de Hurco y Renishaw
Objetivo
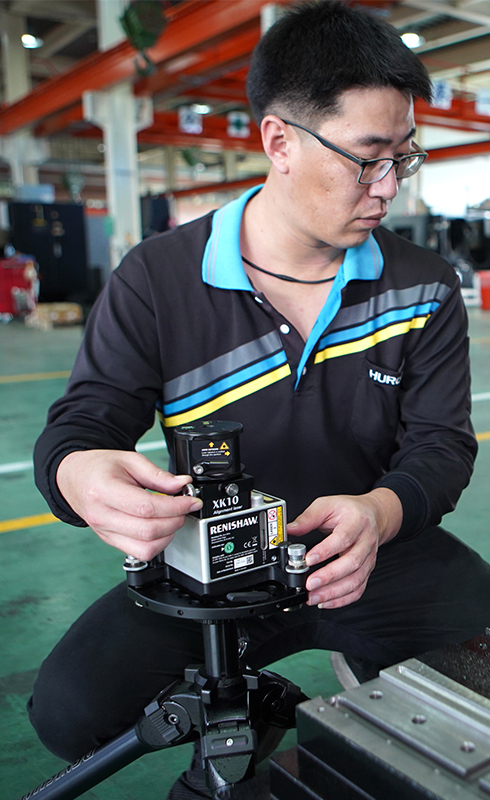
Hurco utilizando el sistema láser de alineación XK10
Puesto que Hurco produce más de 2 000 Máquinas-Herramienta cada año, el aumento de la eficiencia de medición era un factor crucial para los procesos de inspección y verificación de la empresa' No solo era necesaria una medición y alineación de alta precisión, también tenía que ser más rápida.
Las inspecciones de alineación durante el proceso de ensamblaje se realizaban en Hurco con un conjunto de herramientas de medición tradicionales, CMM y equipos de calibración vanguardistas. La empresa ya estaba utilizando una serie de soluciones de Renishaw, como el interferómetro láser XL-80, el sistema ballbar QC20-W y el calibrador de ejes rotatorios XR20-W.
El tamaño y la escala de los componentes de fundición de la Máquina-Herramienta presentaba una serie de restricciones significativas para las soluciones de CMM, mientras que la debilidad inherente de las técnicas de medición tradicionales limitaba el rendimiento operativo. Wang Shun-Chien, vicepresidente de Hurco Manufacturing explica: “Hasta ahora, realizábamos la medición y alineación de los productos de fundición en máquinas de medición por coordenadas, pero las mayores dimensiones de las piezas de fundición siempre son un factor de limitación, por lo que exigían mucho trabajo”.
Y continúa, “También usábamos herramientas de verificación de errores tradicionales, como escuadras de granito, galgas comparadoras y autocolimadores durante el proceso de montaje, pero estas no tenían la eficacia necesaria, por lo que los resultados de medición eran demasiado inconsistentes”.
“Para medir el paralelismo de algunas piezas de fundición grandes, si la escuadra de granito y el raíl guía están separados, era necesario ampliar las galgas comparadoras para llegar al granito, lo que provocaría desviaciones durante la ampliación”.
Hurco se propuso encontrar una solución de alineación de herramientas más precisa. Una de ellas era reducir al mínimo las intensivas tareas manuales de configuración y uso, y cómo reemplazar los métodos de medición tradicionales.
Solución
Tras una intensa investigación y pruebas, Hurco eligió el sistema láser de alineación XK10 de Renishaw. El sistema se utiliza en raíles lineales para verificar la rectitud, la cuadratura, la planitud, el paralelismo y el nivel, y en los husillos o cabezales y en los platos, para verificar la dirección y la coaxialidad de las máquinas rotatorias.
Una solución de medición digital “todo en uno” adecuada para diferentes Máquinas-Herramienta CNC, el sistema XK10 se compone de una unidad emisora para la transmisión del láser principal; unidades de transmisor y receptor inalámbricas; una pantalla portátil y un kit de fijaciones. El kit de paralelismo XK es un accesorio adicional necesario para realizar mediciones de paralelismo.
El tamaño compacto de la unidad XK10, la conectividad inalámbrica y el juego de fijaciones versátiles permiten utilizar el sistema en varias configuraciones distintas y realizar detección y medición de errores geométricos y rotatorios en Máquinas'Herramienta de cualquier tipo y tamaño.
En la unidad de pantalla, el operario puede obtener, analizar y grabar datos de medición. Proporciona instrucciones paso a paso para cada tipo de medición, con gráficos intuitivos sencillos de entender y lecturas en tiempo real, que guían al operario por cada etapa del proceso de medición.
Al contrario que un autocolimador, que depende del principio de conversión de mediciones angulares en lineales, el sistema láser de alineación XK10 obtiene mediciones lineales directamente, por tanto, se evitan los errores de conversión inherentes. Lo más importante es que durante la captura de datos, no es necesario reiniciar el haz láser del XK10 completamente, al contrario que con una solución de interferómetro láser.
“Al sustituir las escuadras de granito de distintos tamaños, el sistema XK10 ha resuelto también los problemas de límite de espacio de almacenamiento y logística. Gracias a su flexibilidad y facilidad de transporte, es muy fácil trasladarlo a las instalaciones para realizar mediciones de alta precisión en tiempo real.
Hurco Manufacturing Ltd. (Taiwán)
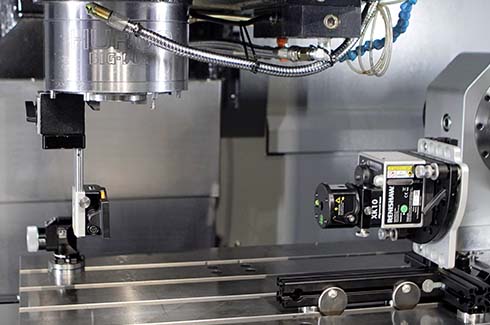
Solución de medición digital multifunción XK10
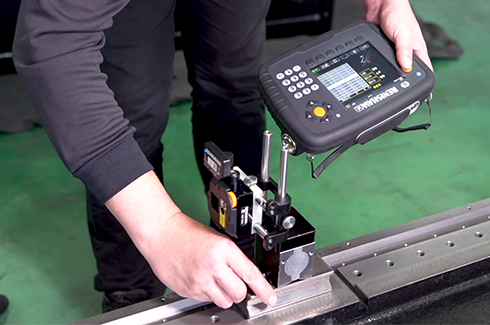
La unidad de pantalla del sistema XK10 obtiene, analiza y graba datos de medición
Resultados
El sistema de alineación láser XK10 ha ayudado a reducir considerablemente el tiempo que Hurco necesita para implantar la alineación de Máquinas-Herramienta de alta precisión. Tras varias pruebas con el sistema XK10, comprobaron que era una solución realmente capaz de reemplazar a los métodos tradicionales.
El Sr. Wang comenta, “Como estimación conservadora, diría que el sistema XK10 ha doblado al menos nuestra eficiencia de medición general y nuestro sistema de evaluación de procesos ha demostrado que los resultados de medición son iguales a los de una máquina de medición por coordenadas de alta precisión."
Con un amplio alcance de medición de 30 m, el XK10 cumple los requisitos de muchas Máquinas-Herramienta de gran tamaño. El cálculo de la separación entre los raíles guía para mediciones de paralelismo es ahora muy sencillo, ya que no se necesitan grandes escuadras de granito y se evita el riesgo de desviación de las galgas comparadoras ampliadas excesivamente.
El Sr. Wang prosigue, “El sistema XK10 nos ha impresionado especialmente en la medición de paralelismo entre dos raíles. Comparado con los autocolimadores, el reglaje del sistema XK10 para la medición de varios raíles es mucho más fácil. Alineamos la unidad láser y giramos los rayos láser 90° con el kit de paralelismo XK. A continuación, el sistema analiza automáticamente los datos obtenidos y genera las mediciones de paralelismo entre los dos raíles. No puede ser más fácil."
“Al sustituir las escuadras de granito de distintos tamaños, el sistema XK10 ha resuelto también los problemas de espacio limitado y logística. Gracias a su flexibilidad y facilidad de transporte, es muy fácil trasladarlo a las instalaciones para realizar mediciones de alta precisión en tiempo real. Se utiliza para el montaje de Máquinas-Herramienta, calibración y mantenimiento, y permite conocer el estado de cada máquina CNC para asignar los recursos más eficazmente”.
El Sr. Wang añade, "Los informes generados por el sistema XK10 son muy intuitivos y, mediante una serie de tablas o gráficos, el cliente puede conocer rápidamente el estado de una Máquina-Herramienta durante una inspección de aceptación".
"En el sistema XK10, puede determinar rápidamente si el origen de la desviación está relacionado con el proceso de ensamblaje, en vez del mecanizado de la pieza o la rigidez de la pieza de fundición. Si se detecta algún error de precisión en el mecanizado de la pieza de trabajo, puede corregirlo rápidamente verificando las máquinas CNC para hacer los ajustes necesarios. Nos ha ayudado enormemente a aumentar la eficiencia”.
Desde su creación, Hurco ha utilizado prácticamente todos los productos de calibración de Renishaw, incluido el interferómetro láser XL-80, el sistema de ballbar QC20-W y el calibrador de ejes rotatorios XR20-W. El Sr. Wang explica: “La incorporación del sistema XK10 ha ampliado aún más nuestro arsenal de dispositivos de medición y nos proporciona dispositivos para montaje, calibración y mantenimiento de Máquina-Herramienta. También nos permite conocer mejor el estado de cada máquina CNC para asignar los recursos con más flexibilidad”.