TONiC™ incremental encoder system with RESM20 rotary (angle) ring
Features
- Readhead size: 35 x 13.5 x 10 mm
- Resolutions to 1 nm
- Speed up to 3 673 rpm
- Ultra-low Sub-Divisional Error (SDE): typically < ±30 nm
- Vacuum and Functional Safety variants available
- Optical IN-TRAC™ reference mark
Benefits
- Low profile ring with large internal diameter for easy integration
- Super-compact encoder readhead with dynamic signal conditioning for improved motion control
- High dirt immunity
- Diagnostic kit to assist challenging installations and aid system optimisation
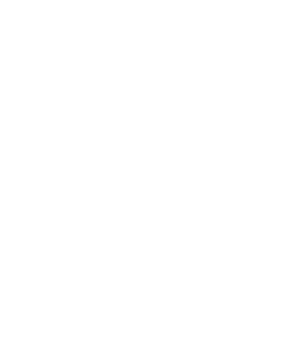
What is TONiC?
The TONiC™ series is a compact, non-contact incremental encoder system that offers speeds up to 10 m/s and, when combined with the Ti interface, resolutions down to 1 nm for both linear and rotary applications. Advanced filtering optics within the readhead give TONiC very low jitter, resulting in excellent positional stability and smoother velocity control. This makes TONiC the ideal encoder for applications where movement must be tightly controlled.
The TONiC encoder gives exceptional signal stability with low Sub-Divisional Error (SDE) of typically <±30 nm to help realise superior motion control performance.
TONiC encoders also feature an integrated setup LED for intuitive and efficient installation.
What is RESM20 ring?
RESM20 is a one-piece stainless steel ring with 20 µm pitch graduations marked directly on the periphery, featuring the IN-TRAC™ optical reference mark. Two versions are available in a wide range of sizes (Ø52 mm to Ø550 mm). ‘A' section rings, which offer an impressive installed accuracy and feature a taper mount system which reduces the need for highly toleranced machined parts and eliminates eccentricity. ‘B' section thin rings, which are low inertia and mass, are also available. Both 'A' and 'B' section rings have a large internal diameter for flexible integration. The non-contact format eliminates backlash, shaft wind-up (torsion) and other mechanical hysteresis errors that are inherent in traditional enclosed encoders.
Why choose this encoder system ?
Dirt immunity
High tolerance to dirt, scratches and greasy fingerprints and speeds of 10m/s mean that TONiC is ideal for more challenging applications. Furthermore, the non-contact RESM operates without friction or wear ensuring excellent reliability.
Exceptional metrology
The TONiC encoder features Renishaw's market-proven filtering optics and advanced signal processing. Auto Gain Control (AGC) and Auto Offset Control (AOC) technologies reduce analogue signal noise and digital jitter within the readhead.
TONiC encoders deliver exceptionally low signal output jitter of <±0.5 nm RMS and low Sub-Divisional Error (SDE) of <±30 nm, enabling systems to hold position better and generate less heat in linear motor applications. Low jitter also enables smoother velocity control in high-precision applications operating at low speeds.
Flexible configuration
The TONiC series offers a variety of external interfaces that can be configured to meet the speed and resolution requirements of the application. With late-stage integration and configuration of the external interface, one versatile TONiC readhead offers many options for end user customisation.
TONiC interface options enable digital, analogue, or dual output of both digital and analogue signals. The TD (dual resolution) interface offers selectable dual-resolution output, and a DPI interface is also available for wide-format printing applications. The flexibility of TONiC encoder configuration allows OEMs to benefit from superior motion control and high throughput in a wide range of applications.
Interface options
TD (dual resolution) interface
- Selectable dual-resolutions quadrature output.
- Ideal for applications that require high speed movement combined with finer precision motion.
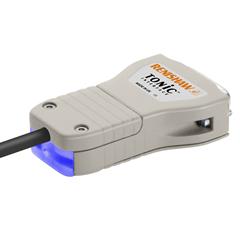
DOP (dual output) interface
- Provides simultaneous digital quadrature and 1 Vpp signals.
- Designed for applications requiring one or more operations to be synchronised with a motion axis.
DSi (Dual Signal interface)
- Renishaw's DSi combines the incremental signals from two TONiC readheads on a RESM20 ring (REST20 ring for partial rotation applications) to compensate for the effect of bearing wander and eliminates odd error harmonics, including eccentricity to give total l installed accuracy of typically ±2.0 arc second.
Optional diagnostic kit
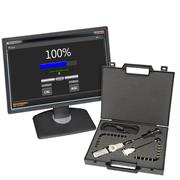
TONiC diagnostic software can be used to optimise the installation of TONiC encoders and provide a quick and comprehensive system calibration. The software must be used in conjunction with the TONiC diagnostic hardware which can be purchased from Renishaw using part number A-9411-0011. The hardware is connected to the PC via the USB cable (provided in the kit) or in-line with the customers' electronics.
Find out all about the TONiC diagnostic kit.
Technical specifications
Measuring standard | RESM20: one-piece low profile stainless steel ring. Standard ‘A' section with tapered internal diameter or low inertia ‘B' section rings available Also available for partial rotation applications as REST20 |
Readhead size (LxHxW) | 35 mm x 13.5 mm x 10 mm |
Scale pitch | 20 μm |
Coefficient of thermal expansion at 20 °C | 15.5 ±0.5 μm/m/°C |
Ring outer diameter | 52 mm to 550 mm. For larger custom sizes, contact Renishaw |
Line count | 8 192 to 86 400 (depending on ring size) |
Reference mark | RESM20: single IN-TRAC reference mark ring REST20: two reference mark ring for partial rotation applications |
Typical installed accuracy* | ±12.7 to ±1.9 arc seconds (depending on ring diameter) |
Maximum speed Analogue Digital | (See data sheet for details) 3 673 rpm at -3 dB (on 52 mm RESM20) 3 673 rpm (5 μm resolution TONiC on 52 mm RESM20) |
Sub-Divisional Error (SDE) | Typically < ±30 nm |
Dynamic signal control | Real time signal conditioning including Auto Gain Control (AGC) and Auto Offset Control (AOC) for optimised performance during operation |
Incremental signals Analogue Digital | (See data sheet for details of angular resolutions) 1 Vpp (20 μm period) Resolutions from 5 μm to 1 nm |
Electrical connection | 0.5 m, 1 m, 1.5 m, 3 m, 5 m and 10 m cable lengths with mini connector (connects direct to TONiC interface) |
Power supply | 5 V ±10%, < 100 mA (analogue system), < 200 mA (digital systems) (unterminated) |
Vibration (operating) | 100 m/s2 max @ 55 Hz to 2 000 Hz |
Shock (non-operating) | 1 000 m/s2, 6 ms, ½ sine |
Operating temperature (system) | 0 °C to +70 °C |
Sealing | Readhead: IP40 Interface: IP20 |
* 'Typical' installations are a result of graduation and installation errors combining and, to some magnitude, cancelling.
Refer to data sheets for full details.