Renishaw supports Formule ETS with additive manufacturing project
Background
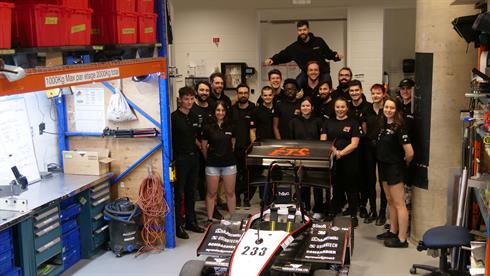
The Formula SAE competition, operated by SAE International, brings together over 600 teams from universities around the world. In the Formula SAE competition, teams compete by presenting a business plan to judges, describing their vehicle design philosophy, creating a project cost list, and by competing in races.
Based at the École de technologie supérieure university (ÉTS) in Montreal, Canada, Formule ETS is a Formula SAE team that has been competing in the combustion category of Formula SAE for more than three decades. In 2020, the team decided to enter the electric category instead, which would mean redesigning their vehicle to one with an electric powertrain.
“Formule ETS is a serious competitor in Formula SAE, we have been reaching the podium in the combustion category for years,” said Léa Tonini, Biomechanical Engineering Student at ÉTS and 2023-24 Co-Captain of Formule ETS. “When we made the decision to switch to an electric vehicle, we wanted to do so in a way that continued to push the boundaries of motorsports and maintained our leading position.”
The team built its first electric car, MANIC-20, over two years during the pandemic as a learning experience. They then optimised the car's design into a second iteration, named MANIC-22, for the 2022 season, which saw the team win first place in multiple competitions.
Challenge
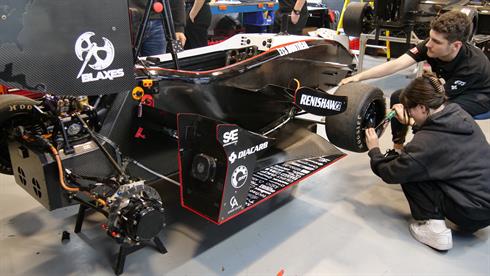
The main challenge was achieving our weight reduction target. Designing a car that weighed 400 lb overall would involve developing significantly lighter components for the MANIC-23 vehicle.
“After a successful 2022 season we wanted to build on our vehicle to create the best performing car in the history of the competition,” said Tommy Gélinas, Mechanical Engineering Student at ÉTS and team member involved in the powertrain design. “The main challenge was achieving our weight reduction target. Designing a car that weighed 400 lb overall would involve developing significantly lighter components for the MANIC-23 vehicle.” said Gélinas.
One key component selected for lightweighting was the uprights. These components connect several sub assemblies in the vehicle, enabling the transmission of wheel motion to the suspension arms and subsequently, to the shock absorbers. All four uprights in the vehicle house an electric motor, and act as supports for the planetary gear system contained in each wheel. Using AM for the uprights would enable the team to reduce the vehicle's unsprung mass, improving control over its dynamic behavior.
For previous vehicles, the uprights were machined from 7075-T6 aluminum on a 5-axis CNC milling machine. For the new vehicle, the team came up with an organic-type geometry that required a different manufacturing process.
“We identified that metal additive manufacturing would give us the design freedom to create lightweight parts without compromising the vehicle performance, while meeting the competition's compliance requirements. However, we could not initially find a partner capable of producing the new uprights,” said Gélinas.
Solution
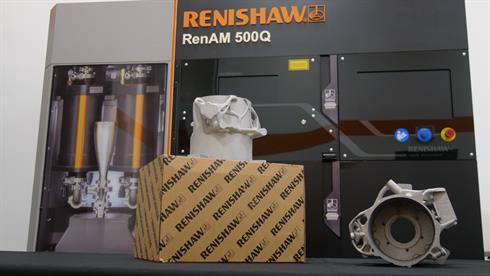
Renishaw gives full engineering support to Formule ETS by advising on design choices, assisting with topological optimisation, and manufacturing the final parts.
Having seen a previous partnership between Renishaw and a Formula Student team, the ÉTS team got in touch to ask if the company could help with the manufacture of the uprights. Renishaw stepped in to support Formule ETS by advising on design choices, assisting with topological optimisation, and manufacturing the final parts.
“The choice of material was a key decision during the development process,” said Carl Hamann, Technical Sales & Business Development Manager at Renishaw Canada. “We provided the Formule ETS team with technical information on powders, ranging from Young's modulus data to fatigue test results. Following the testing, the team opted for AlSi10Mg powder as it offered the required stiffness while being lightweight. The team was also able to optimise build time and support design using our QuantAM build preparation software.”
“From the outset, Renishaw showed a genuine interest in Formule ETS and the development of the new uprights,” added Gélinas. “The company's technical experts helped guide our design choices by giving valuable insight and advice, and we worked closely with the Renishaw team in Ontario throughout the project.”
Results
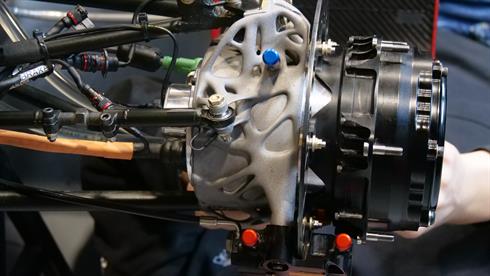
The development of the new uprights enabled the team to achieve a significant weight reduction for both the front and rear uprights - 30 per cent and 28 per cent respectively. This decreased the vehicle's unsprung mass, resulting in better control of the vehicle's dynamic behavior.
The team was able to meet the competition's compliance criteria by reducing camber compliance by 18 per cent for front uprights. Furthermore, the additive manufacturing of the uprights enabled the team to reduce upright material use by 45 per cent.
During its competition season in June 2023 with the MANIC-23 vehicle, the Formule ETS team won the North American Electric Formula SAE (FSAE) competition in Michigan, coming first out of 69 teams, and scoring 919 out of a possible 1,000 points.
The team also experienced success competing in European competitions, finishing in second place in the Croatian competition FSAE Alpe Adria. 2023 marked the first time since 2001 that Formule ETS has achieved second place on European ground. The European events also highlighted areas the vehicle could be further improved upon for future seasons.
“MANIC-23 is a significant leap in terms of power, precision, and compactness from our previous vehicle. With regards to the uprights, Renishaw was the cornerstone that enabled successful project completion, due to its technical expertise, production capabilities, and enthusiastic investment in our team and the innovation we are striving to achieve,” concluded Tonini.