Rapid prototyping expert uses Renishaw AM systems to develop hypersonic technology for aerospace
The development of spacecraft has always been reliant on new and advanced technologies. Additive manufacturing (AM), for example, gives aerospace engineers the design freedom and rapid prototyping capabilities required to develop new parts for satellites, while meeting the strict requirements of the aerospace industry. So, when aerospace venture capital startup Velontra looked to develop a hypersonic propulsion system for space applications, it turned to Innovative 3D Manufacturing, user of Renishaw's AM systems.
Background
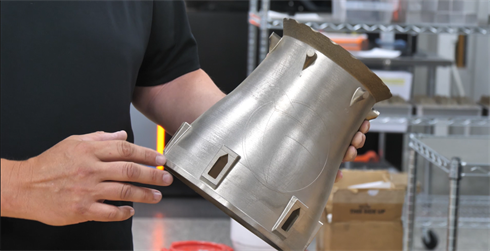
Innovative 3D Manufacturing, a rapid prototyping company founded in 2016, provides manufacturers, in a variety of industries ranging from aerospace to medical, with a range of expert prototyping services. By using AM, Innovative 3D Manufacturing can develop more complex components than what has traditionally been possible when using conventional methods, such as CNC machining. Using AM, the rapid prototyping specialist can also combine multiple components into one part, reducing the weight of the final product.
One of Innovative 3D Manufacturing's recent customers, Ohio-based Velontra, is a start-up in the aerospace market using innovative technologies to develop engines capable of hypersonic speeds. The company designs, prototypes and builds hypersonic propulsion systems for a range of applications, with the aim of accelerating development while reducing the cost of the propulsion design cycle. By making these advancements and developing new systems, such as its Bronco hypersonic engine for smaller vehicles, Velontra hopes to enable the space industry and other sectors to experience and benefit from affordable, unmanned supersonic vehicles.
Challenge
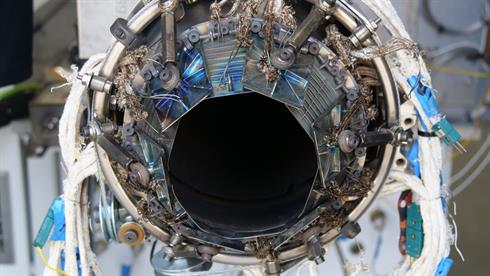
“Compact hypersonic propulsion systems are highly sought after by space companies, so, to remain competitive, we must develop parts quickly,” explained Joel Darin, CTO of Velontra. “In aerospace, we know that the best way to learn is by doing things, particularly if you want to be the first to launch a new technology.”
“Innovation also requires people to keep making iterations of an idea and testing it until it works. Take the Wright brothers — lots of other people across the world wanted to take the first successful flight. The brothers built a test tunnel to try their aircraft over and over again, which resulted in success. We take the same attitude when developing our products,” added Darin.
To successfully take the Bronco engine from concept to product, Velontra needed a way to produce rapid prototypes of its small and fast propulsion systems while also reducing resource use, meeting quality requirements and manufacturing tolerances, and keeping costs down. While the team understood the benefits of AM for this application, Velontra had no in-house expertise to develop a process in the intended timeline.
Solution
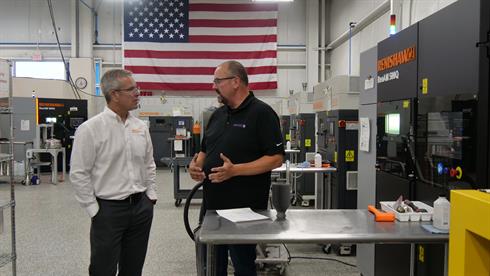
To develop AM components in partnership with a team experienced in AM, Velontra reached out to Innovative 3D Manufacturing. The prototyping expert recently upscaled its operations and is now operating four Renishaw RenAM 500Q multi-laser systems to improve productivity while continuing to deliver high quality parts for a range of customers, including Velontra.
The Innovative 3D Manufacturing team uses its skills in designing for AM to develop parts including the propulsion system for the Bronco. The design process for this part involved considering optimal wall thickness, cavity design and flow paths. Innovative 3D Manufacturing then produced part iterations using the RenAM 500Q, orientating parts to use 100 per cent of the machine's build capacity.
As well as the propulsion system, Velontra has collaborated with Innovative 3D Manufacturing to prototype and produce other bespoke parts for the propulsion system, such as an additively manufactured ramjet prototype and afterburner hardware. By using AM, Velontra, in partnership with Innovative 3D Manufacturing, can develop complex yet lightweight parts, send designs to its partner and receive prototypes the next day, reducing development cycles.
“We've worked with Velontra since its inception to share our expertise on designing for AM in the aerospace industry,” said Chris Beck, Operations Manager and owner of Innovative 3D Manufacturing. “By helping Velontra to understand the importance of designing geometries for AM, choosing the optimal part thickness and selecting the right materials, Velontra's engineers have been able to develop and refine their propulsion system. By using the RenAM 500Q, a multi-laser metal AM system, we have been able to print prototypes at a much faster rate, while leveraging the machine's on-board sieving capabilities, making the entire process more efficient and reducing part turnaround.”
The RenAM 500Q is a laser powder bed fusion system that features four high-power 500 W lasers that can access the entire powder bed surface simultaneously, enabling users to make use of the entire build plate, thereby boosting productivity. The system also features automated powder and waste handling systems that enable consistent process quality, reduce operator intervention time, and ensure high standards of system safety.
By using AM technology we've been able to produce a propulsion system that is powerful, yet small, and anything but tame. We recently conducted tests of the Bronco using the wind tunnel at Purdue University, Indiana, and saw positive results. We plan to further our use of additive manufacturing to continue developing and improving the Bronco.
Joel Darin
CTO of Velontra
Results
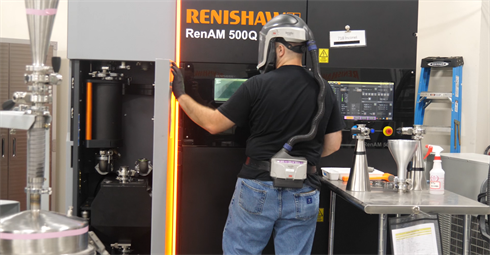
“By using AM technology we've been able to produce a propulsion system that is powerful, yet small, and anything but tame,” emphasised Darin. “We recently conducted tests of the Bronco using the wind tunnel at Purdue University, Indiana, and saw positive results. We plan to further our use of additive manufacturing to continue developing and improving the Bronco.”
Tests at Purdue University's wind tunnel simulated speeds of over Mach 4.5 and an altitude of 100,000 ft. Results demonstrated that the Bronco can deliver thrust at greater than Mach 5, over five times the speed of sound and, according to Velontra, this makes the engine the first of its kind.
“The Innovative 3D Manufacturing team have been an amazing collaborator as always. Chris and the team do all they can to deliver the quality parts we need as quickly as possible,” continued Darin. “On one occasion we sent a part design file on Monday afternoon, 24 hours later he drove to meet us halfway to deliver a part we needed — his support is incredible. We have also been impressed with the speed and quality of the Renishaw AM systems that the team uses to deliver quality parts, but at the affordable production cost we require to keep the costs of the propulsion system down.”
Velontra aims to integrate the Bronco hypersonic propulsion system into small vehicles to make them supersonic for commercial and industrial use. The company also plans to build an unmanned spaceplane that can be used as a platform for launching satellites.
With help from its Renishaw metal AM systems, Innovative 3D Manufacturing is maintaining its reputation for delivering high quality parts and meeting the deadlines of customers in a range of sectors. The on-board sieving and four laser system found in the RenAM 500Q is suited to production as well as prototyping, enabling Innovative 3D Manufacturing to take on manufacturing projects.