Equator™ 300 gauging system cuts the measurement time of automotive parts by up to 80%
Equator 300 system for flexible shop floor gauging and to radically improve measurement throughput. Being thermally ‘insensitive', the Equator system accurately gauges parts at very high speeds, regardless of environment and temperature changes on the shop floor.
Based in China, Fulin Precision Machining (Fulin P.M.) is a major manufacturer of precision parts for the automotive industry, specialising in the research, development, manufacture and sale of automotive engine systems. Parts produced range from traditional precision hydraulics, e.g., for internal combustion engine (ICE) and transmission parts, to the electromagnetic and electronic drives for electric and
hybrid vehicles. The company supplies some of the leading global automotive manufacturers including Audi, Volkswagen, General Motors, Renault, PSA, Toyota, Nissan, SAIC, GAC, BAIC, Changan Auto, Geely and Great Wall Motor.
Process control is critical
While the parts manufactured may vary in size and final application, all require the highest levels of machining accuracy to meet the strict standards of the automotive industry. Fulin P.M. has established its own, leading-edge testing centre, which is accredited by CNAS (China National Accreditation Service for Conformity Assessment), to inspect production parts for quality control and assurance.
Lyu Qijian, Deputy Manager of Fulin P.M. Testing Centre, explains that the testing centre is equipped with more than 1800 pieces of high-end manufacturing testing equipment. It boasts a range of testing, high-precision inspection and evaluation capabilities, and provides comprehensive and professional inspection on in-bound materials, precision manufactured-parts and finished products ready for delivery.
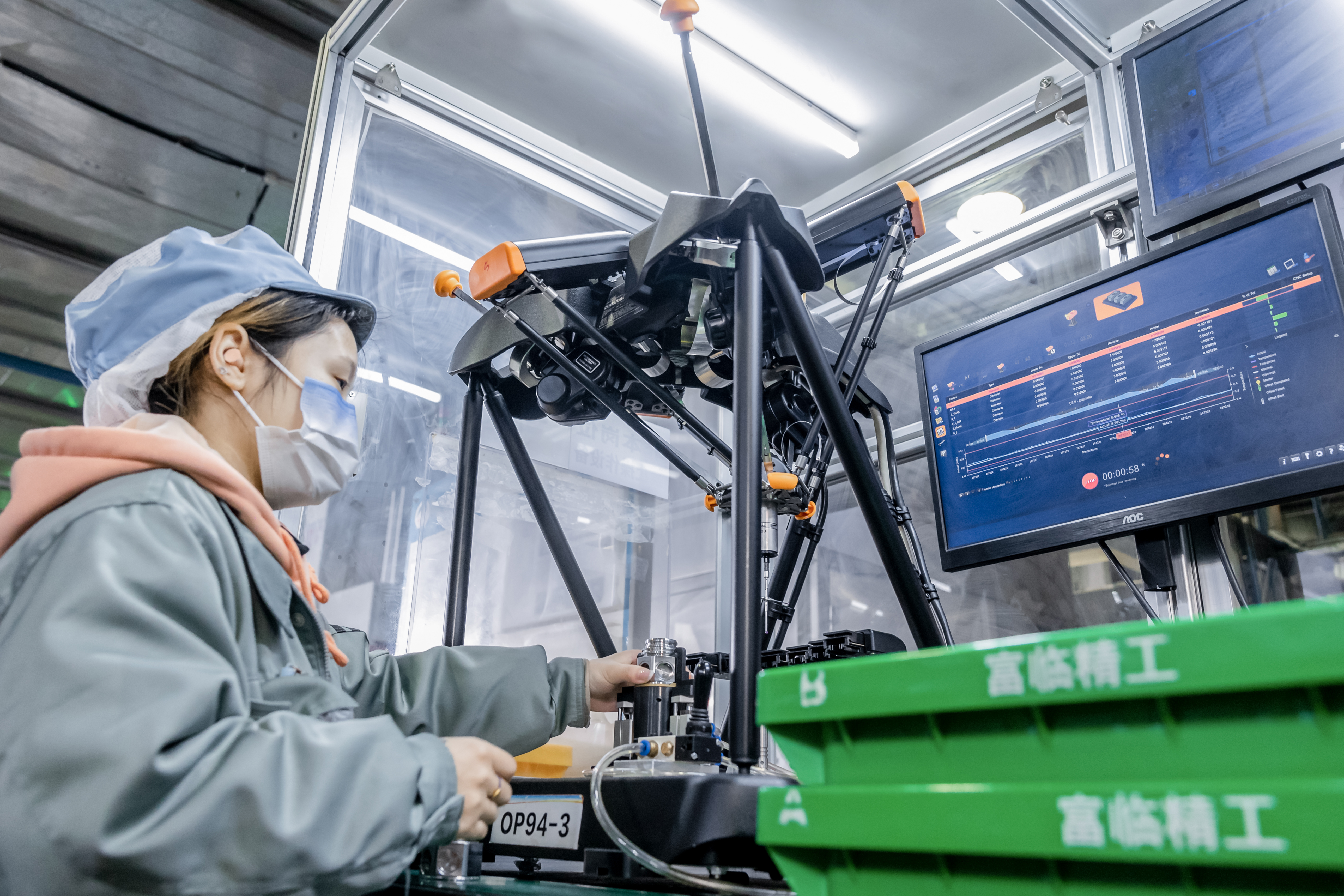
New gauging needed for high volume, multiple part batches
The scale of throughput is enormous. Every day, more than 80 skilled members of staff measure over 30,000 complex parts, and more than 1,000 batches. The Testing Centre needed to upgrade to a rapid and efficient inspection solution. Not only that, but any new system had to function consistently across the full range of widely varying
temperatures on the shop floor, and achieve a high level of accuracy with gauging system repeatability as small as 1 μm.
“In 2022, Fulin P.M. was developing a new part for an automotive engine. We had to go through hundreds of part features with strict tolerance requirements as low as 10 μm for some dimensions.
For the measuring device to gauge a 10 μm tolerance it needs to achieve 1 μm repeatability, and 100% inspection rather than sampling, explained Mr Lyu.
Such a large and complex task could not be completed using the laboratory Coordinate Measuring Machines (CMMs) and conventional manual inspection. Fulin P.M. needed a time- and cost-effective alternative. “We consulted several measurement solution providers and, after comprehensive comparison and assessment, selected the Equator 300 gauging system manufactured by Renishaw,” said Mr Lyu.
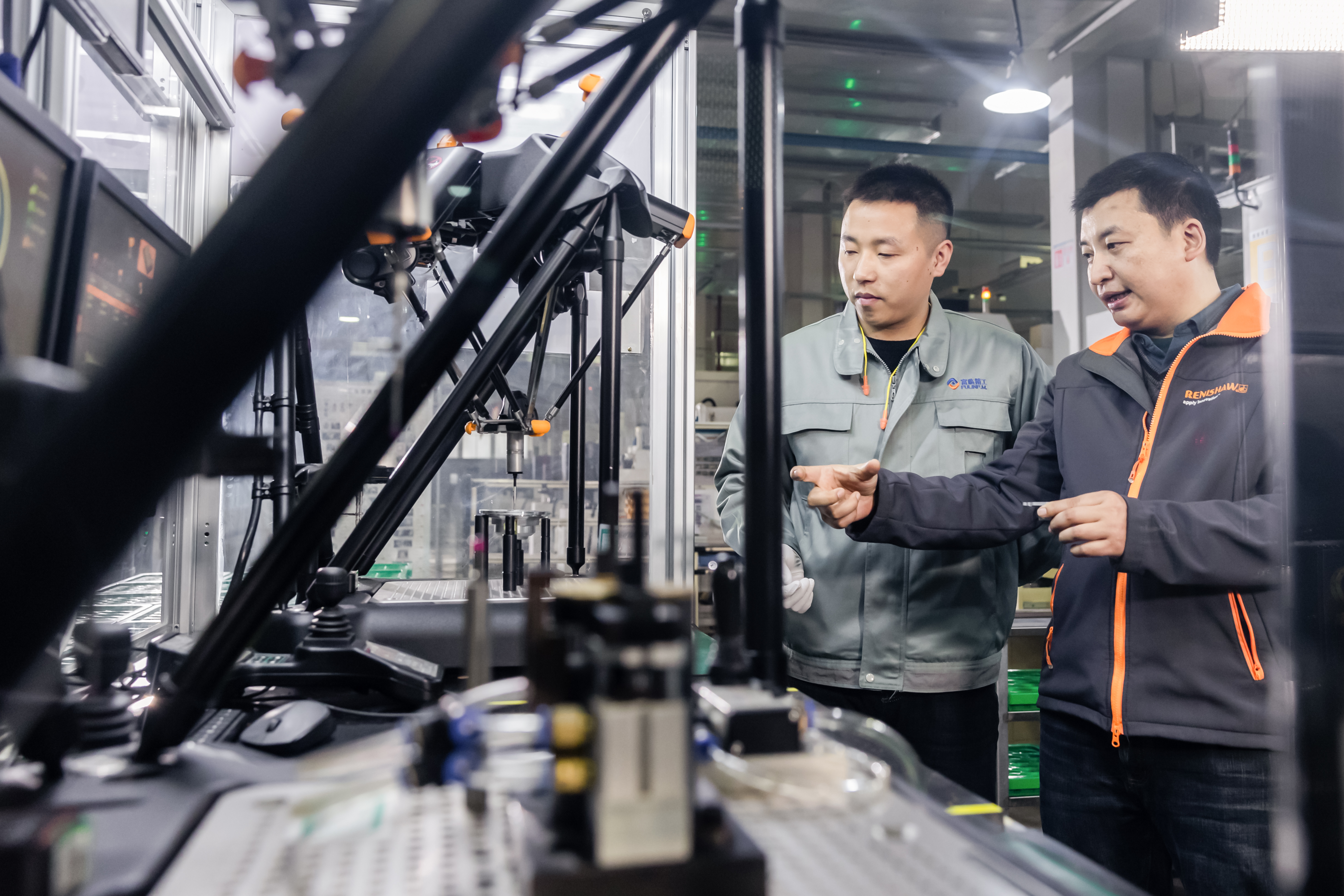
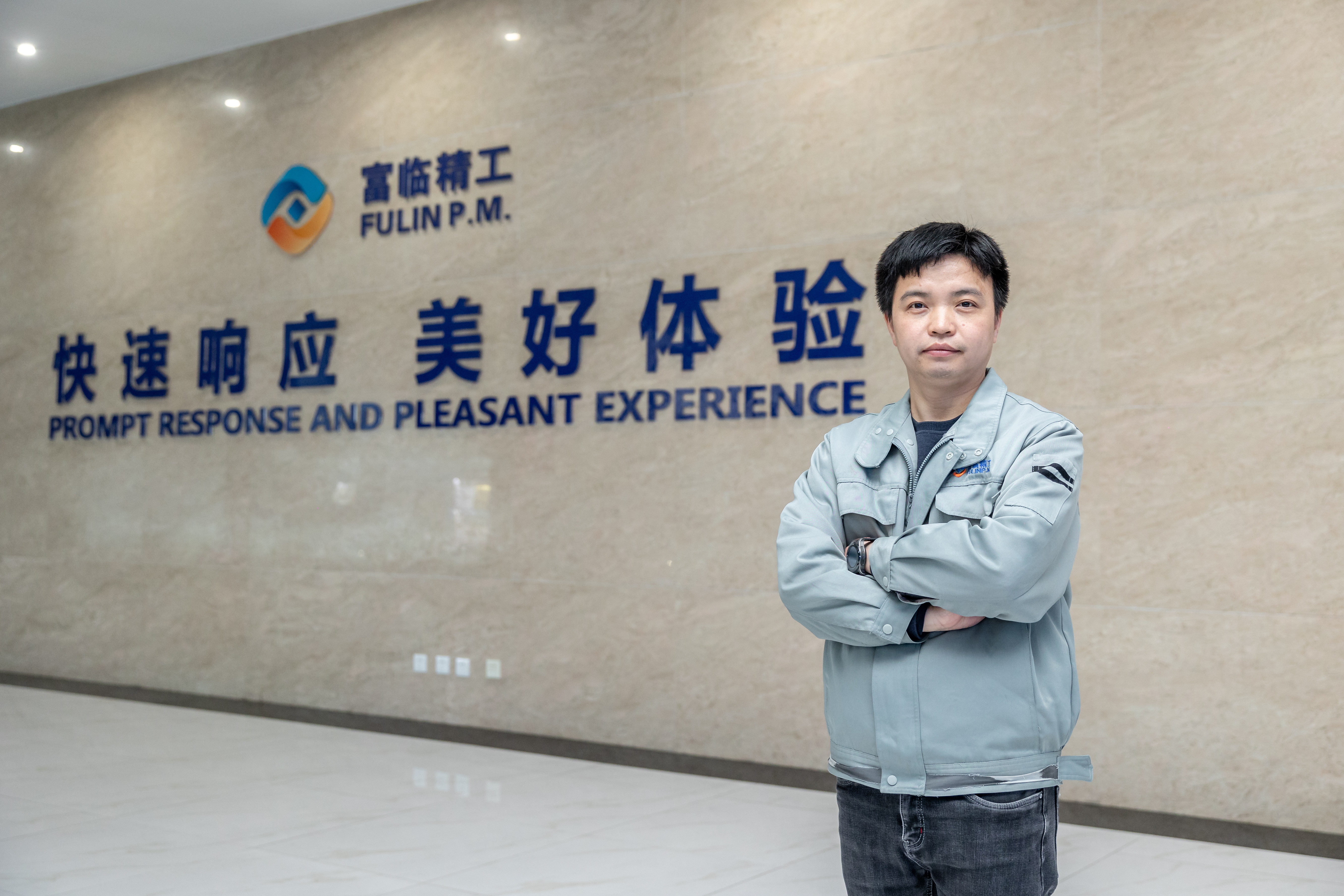
Lyu Qijian, Deputy Manager of Fulin P.M. Testing Centre (China)
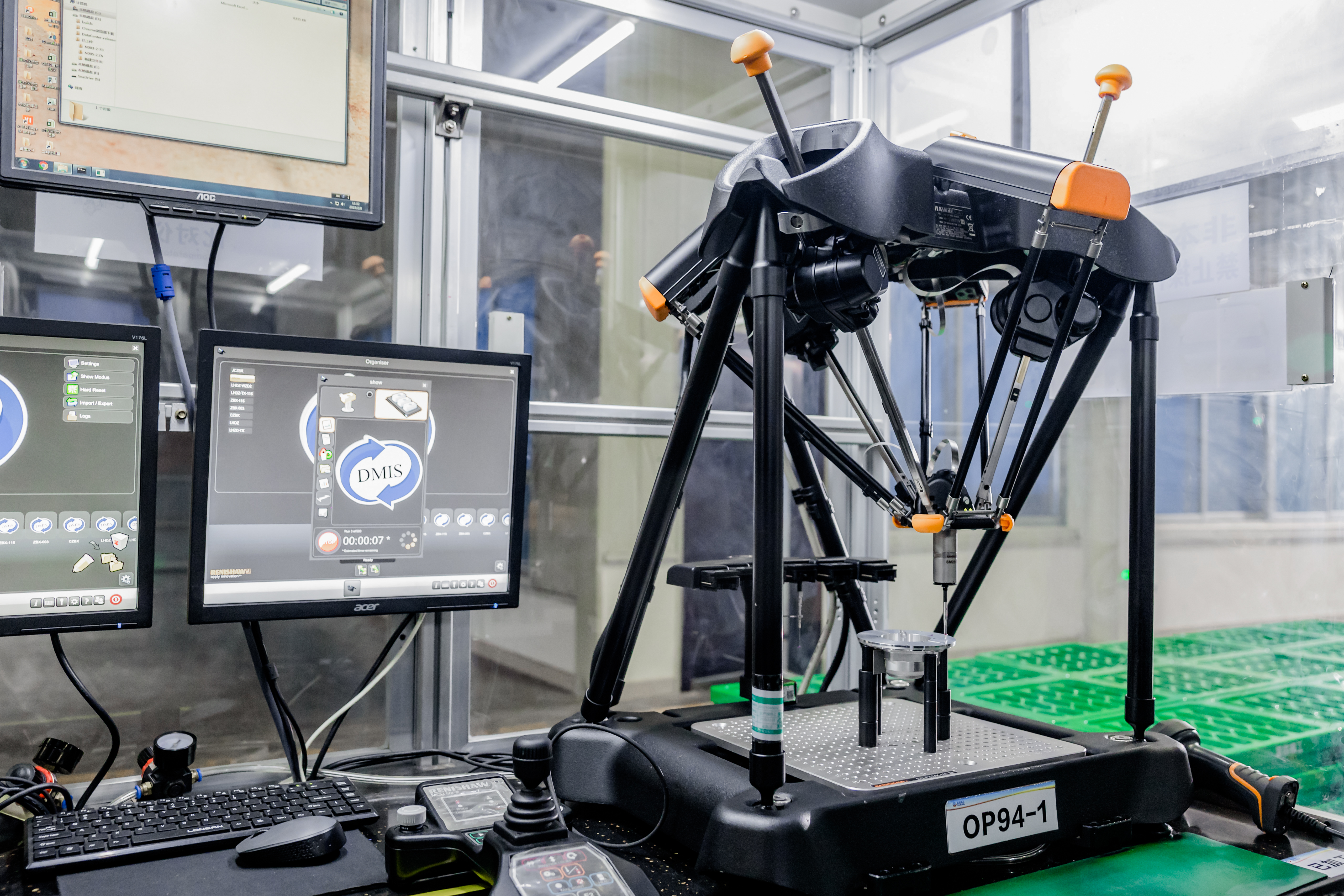
Currently, 13 Equator 300 systems are deployed on the shop floor at the Fulin facility
Gauging accuracy across a wide temperature range
Renishaw's Equator 300 gauging system is unique in being able to meet stringent measurement, reporting and tracking requirements for accuracy and repeatability. By employing a master part and using a compare process, it is thermally ‘insensitive', enabling it to operate reliably in an environment which ranges from 5 - 50 °C with a humidity of up to 80%. Its structure, using a parallel kinematic mechanism, allows for improved repeatability, reduced inertial effects, and lower power consumption when compared to the traditional Cartesian structures used for machine tools and CMMs.
It's adoption has significantly improved measurement efficiency at Fulin P.M. “Before, our operators had to take the parts to the designated CMMs in the laboratories; now, our production lines feature Equator 300 inspection stations, improving our inspection routes, shortening material turnaround time and time for temperature stabilisation, and eliminating quality risks arising from transport,” says Mr Lyu. “The time to measure the automotive engine part has been slashed by 80%, with the Equator 300 taking just one minute, compared to six minutes for a CMM to measure the same part.”
Equator 300 has improved inspection routes and shop floor efficiency
Currently, 13 Equator 300 systems are deployed to control manufacturing processes on the shop floor at the Fulin P.M. facility. After identifying the QR code on each batch of manufactured parts, the Equator 300 gauges the parts and tracks each one throughout the entire process from manufacture to delivery. As a result, Fulin P.M. is able to ensure not only quality of manufacture, but also product marking and traceability, which conform to the strict requirements demanded in
the ISO-TS16949 Automotive Quality Management System.
In doing so, another efficiency has been realised. Due to the flexibility of the system, operators can rapidly switch between part measurement programs as requirements change. This eliminates the cost of investing in new inspection equipment.
The high efficiency rate realised by the Equator 300 systems in use at Fulin P.M has led to 100% on-site gauging at the point of manufacture.
“Based on the data collected from 100% inspection, we can implement Statistical Process Control (SPC) to analyse on-site quality and process capability, along with Quality Risk Management (QRM). With the Equator 300 gauging system, we are fully confident that our parts meet the high standards for quality and reliability,” said Mr Lyu.
Partners for service and support
Fulin P.M. and Renishaw have maintained a close cooperative relationship since 2015. This partnership has resulted in Fulin P.M. continuously optimising its measurement technology, using Renishaw's machine tool probes for in-line measurement on the production line and Renishaw's XL-80 laser interferometer for machine calibration.
“Renishaw is very responsive in service and technological support,” said Mr Lyu. “Renishaw's engineers took time at the start of the Equator
project to help inspectors operate the gauging systems, providing advice on applications, even during the height of the pandemic.”
As the automotive industry transitions from conventional internal combustion engines (ICE) to electric and hybrid models, the Fulin P.M. Testing Centre is also adapting to this rapid change by implementing Intelligent Process Control (IPC) software. Fulin has also introduced the Equator 500 system to its automated inspection processes to cope with the increased demand on inspecting bigger parts at faster speeds. The Equator 500 system, which was launched by Renishaw in 2018, is designed for larger part gauging with a measuring volume of up to 500 mm in diameter and up to 400 mm in height. IPC software connects the Equator system to the machine tool controller to create an integrated closed-loop solution using gauging data to calculate cutting tool offset updates. This minimises human intervention and tool wear errors, while increasing process efficiency.