BiSS® serial interface support
What is the BiSS serial interface?
Renishaw supports BiSS (unidirectional) open serial interface for absolute encoders. BiSS is a high-speed serial interface, perfect for dynamic axes that require high acceleration, smooth velocity control, excellent bi-directional repeatability and dependable positional stability.
Renishaw absolute encoders are compatible with a wide range of industry-standard controllers, drives, DROs and PC counter cards.
Proprietary serial interface options for RESOLUTE™, EVOLUTE™ and FORTiS™ absolute encoders are also available.
Technical information
About RESOLUTE, EVOLUTE and FORTiS encoders
Renishaw RESOLUTE, EVOLUTE and FORTiS encoders use the BiSS C (unidirectional) serial interface.
RESOLUTE FS and FORTiS FS encoders, for applications requiring Functional Safety, use the BiSS Safety serial interface.
- Rotary encoders are single-turn (with 2n counts per revolution and no revolution counting).
- Linear encoders are available with a range of different resolutions (and maximum measuring lengths) as specified on the product data sheet.
Description of the BiSS C interface
BiSS C-mode (unidirectional) is a fast synchronous serial interface for acquiring position data from an encoder.
It is a master-slave interface. The master controls the timing of position acquisition and the data transmission speed,
and the encoder is the slave. The interface consists of two unidirectional differential pairs of lines:
- “MA” transmits position acquisition requests and timing information (clock) from master to encoder
- “SLO” transfers position data from encoder to master, synchronised to MA.
The diagram below shows the data transmitted.
Data format

Description of the BiSS Safety interface
BiSS Safety is a fast synchronous serial interface for acquiring position data from an encoder in applications requiring Functional Safety. RESOLUTE FS and FORTiS FS use BiSS Safety communications and are certified to the following Functional Safety standards:
- ISO 13849 Category 3 PLd
- IEC 61508 SIL2
- IEC 61800-5-2 SIL2
BiSS Safety is a master-slave interface. The master controls the timing of position acquisition and the data transmission speed, and the encoder is the slave. The interface consists of two unidirectional differential pairs of lines:
- “MA” transmits position acquisition requests and timing information (clock) from master to encoder.
- “SLO” transfers position data from encoder to master, synchronised to MA.
The diagram below shows the data transmitted.
The master-slave signal communication format is RS485 / RS422 differential line-driven.
Data format
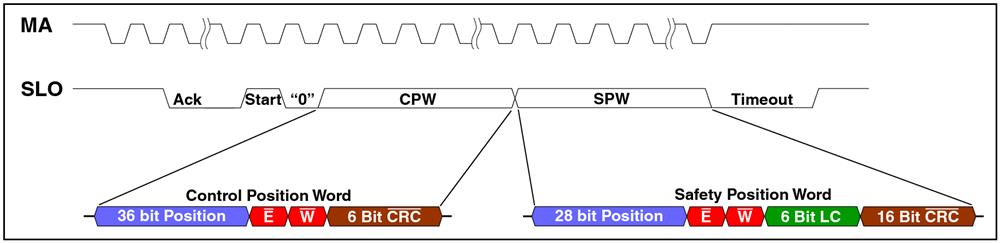
A typical request cycle proceeds as follows:
- When idle, the master holds MA high. The encoder indicates it is ready by holding SLO high.
- The master requests position acquisition by starting to transmit clock pulses on MA.
- The encoder responds by setting SLO low on the second rising edge on MA.
- After the “Ack” period is complete, the encoder transmits data to the master synchronised with the clock as shown in the diagrams above.
- When all data has been transferred, the master stops the clock and sets MA high.
- If the encoder is not yet ready for the next request cycle, it sets SLO low (the Timeout period).
- When the encoder is ready for the next request cycle, it indicates this to the master by setting SLO high.
RESOLUTE open absolute encoders with BiSS C and BiSS Safety
RESOLUTE variants | System options |
Standard | |
Ultra-high vacuum (UHV) | |
Extended Temperature Range (ETR) | Rotary (angle) rings |
Functional Safety (FS) |
EVOLUTE open absolute encoders with BiSS C
EVOLUTE variants | System options |
Standard |
FORTiS enclosed absolute encoders with BiSS C and BiSS Safety
FORTiS variants | Linear system options |
Standard | |
Functional Safety (FS) |