Bastion develops track bike components using additive manufacturing (AM)
Photo credit: Dianne Manson
This article has been reproduced with express authorisation of Bastion Cycles
Copyright © Bastion Cycles Pty Ltd.
Bastion Advanced Engineering and Design (BAED) have unveiled a new and innovative line-up of products targeted at further improving the performance and competitiveness of athletes on the track. Namely a stem, handlebar, and crank designed to work with the Argon 18 Electron Pro Track bikes used by several World Cup and Olympic teams, but most importantly for Bastion, Cycling Australia (CA). Bastion has worked very closely with CA to develop a suite of components aimed at improving the performance of their athletes through the innovative use of technology.
These high technology cycling components will be used in competition at the Glasgow Track Cycling World Cup by the Australian National team. Riders from CA have been testing the components for several months in Australia and some of the components have already appeared in competition, namely the Sprint Stem and Madison Bar. However, appearing for the first time in Glasgow is BAED's Titanium Crank.
Bastion Cycles, parent company to BAED, has been producing some of the finest road bicycles in the world since 2016. The company pioneered the use of 3D printing in bicycle manufacture and in January this year became the first bicycle company in the world to bring Titanium 3D printing in-house. The Titanium components in Bastion's bicycles are produced by Laser Powder Bed Fusion (LPBF) combined with filament wound Carbon Fibre tubes to achieve unparalleled customisation and performance.
Our ability to design, develop and produce custom components in-house has perfectly supported this collaborative effort with Cycling Australia. With direct input from CA driving the concept and requirements of the parts, we have leveraged the design and optimisation strategy behind our bicycles, to produce some truly amazing components. We are especially excited to showcase our knowhow in 3D printed Titanium on this suite of innovative products.
James Woolcock, Engineering Director, Bastion Cycles
Bastion's in-house Titanium print capability has enabled them to develop innovative components more quickly and expand beyond just framesets to stems, bars and cranks. They have been able to take the ideas and vision of Cycling Australia to improve the performance of their athletes and translate that efficiently into working prototypes for confirmation both on the track and in the wind tunnel.
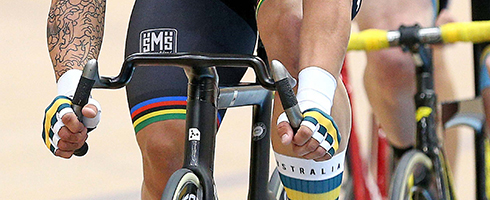
Photo credit: Dianne Manson
Working with likeminded partners to produce high performance solutions is critical if the Australian Cycling team is to meet its medal targets. In Bastion Cycles and the its Advanced Engineering team, we have found such a partner. The technology that Bastion brings to the tables allows them to iterate fast and effectively to the best possible solutions for the Australian Cycling team athletes. We are looking forward to using the new line up of Bastion produces in the up and coming World Cups and World Championships.
Andrew Warr, Performance Systems Manager, Cycling Australia
All three components are 3D printed in Titanium in-house at Bastion using their innovative structural designs incorporating variable wall thickness and internal structural lattice to create metallic structures that out-perform composites in strength to weight ratio.
Component Line-up
Sprint Stem - designed to bolt directly to the fork of the Argon 18 Electron Pro using the same 4 bolt system as the pursuit bars as opposed to the factory bolt on steerer and conventional stem. Available in lengths up to 160mm and effective angles between +17/- 17deg as well as several stack heights.
Madison Bars - the highly innovative double-drop bars are the first of their kind in the world. Developed specifically for use in track bunch events they offer several riding positions that improve control and stability as well as aerodynamic performance. Stem length, angle and bar width can be matched to the rider.
Track Crank - aerodynamically superior with class-leading stiffness. A large airfoil shape which seamlessly blends into the spider to which the chainrings attach. The crank spindle is also Titanium adding further stiffness compared to a conventional aluminium option. Effective crank lengths between 160 mm and 180 mm will be available.
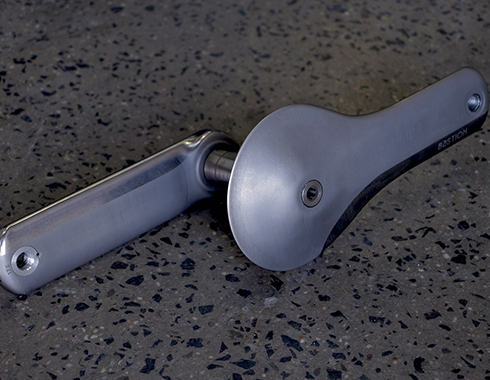
Photo credit: Bastion Cycles
Key Features
Rider Specific Geometry - The use of 3D printing means the size of the components can be tailored to the athlete. This results in a rider position optimised for both aerodynamics and power output. As each component can be made to order without moulds or tooling, otherwise unavailable size combinations are possible.
Aerodynamically Superior - Significant amounts of wind tunnel and real-world testing has confirmed the efficiency of the components and subsequent performance improvements.
Additive Manufacturing - 3D printed in Grade 5 Titanium Alloy (Ti6Al4V) the components utilise topology and structures unable to be manufactured using conventional subtractive methods such as CNC Machining. BAED are world leaders in utilising 3D printing in production parts with quality such that the components are finished naked without paint and are instantly recognisable by their metallic appearance.
High Stiffness to Weight - BAED's ability to manipulate the characteristics of the components by only adding material where it is needed result in parts that have very high stiffness to weight.
Durability Tested - All of the components have successfully passed significant bench durability testing prior to being tested on track by the athletes.
Collaboration with Cycling Australia - These components come straight from the vision of the engineering team at Cycling Australia and have been developed in close collaboration with their engineers and the athletes themselves. Cycling Australia have been pivotal in providing the concepts, initial aerodynamic profiles and confirming the resultant performance improvements both in the wind tunnel and on track.
UCI Approval for Tokyo 2020
In order to qualify to be ridden at the 2020 Tokyo Olympics, the components have already received comment and acceptance from the UCI where required, and have been or will be ridden during the Tissot UCI Track Cycling World Cup series by Cycling Australia before the end of 2019.
Read how Renishaw have helped Bastion Cycles take ownership of its metal AM capabilities www.renishaw.com/bastion.
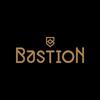
More information on Bastion Cycles and Bastion Advanced Engineering Design can be found at www.bastion-cycles.com and www.bastionadvanced.com.