Diese Seite steht derzeit nicht in Ihrer Sprache zur Verfügung. Mittels der
Übersetzungsfunktion
von Google kann Ihnen eine automatische Übersetzung angezeigt werden. Bitte beachten Sie jedoch, dass wir keinerlei Verantwortung für diese
Dienstleistung tragen und die Übersetzung auch nicht von uns geprüft wurde.
Wenn Sie weitere Unterstützung benötigen,
kontaktieren Sie uns bitte.
RLS encoders and Renishaw help place Dynisma in pole position
Background
For customers in elite motorsport and the automotive sector, Dynisma Ltd has pioneered a new class of motion generator, DMG-1, that accurately simulates motion cues in minute detail to provide a totally immersive driving experience. DMG-1 is also designed for vehicle dynamics testing and NVH (noise, vibration, and harshness) applications in automotive development.
Dynisma was founded by Ash Warne who previously ran the simulator teams at the F1 racing divisions of McLaren and then Ferrari. Dynisma's aim is to develop high performance driving simulators that deliver realistic vehicle motion cues to both championship winning F1 drivers and automotive engineers evaluating the ride of an upcoming passenger car before it has been built.
Ash Warne, Chief Engineer and CEO of Dynisma, introduces DMG-1:
"Our DMG-1 motion generator is used in automotive testing and motorsport. It is a technology that enables, for the first time, motorsport teams and automotive customers to carry out more realistic and higher fidelity tests than ever before. For example, the unique characteristics of this technology are its high bandwidth and very low latency; this means that our customers can put more information through their motion generator providing a more realistic and immersive scenario than they have ever been able to before."
The motion system of DMG-1 is split into two parts: a high frequency platform (HFP) which delivers high fidelity and high bandwidth motion, and a low-frequency platform (LFP) which enables larger movements. A visual system is synchronised with the motion system to provide visual cues to the driver.
Joshua Bell, Dynisma's DMG-1 Engineering Lead, explains:
"Integrated with the motion generator is the visual system. When the driver is sitting in the chassis, they are fully immersed in the world that they see. When they are driving around, they are feeling both the motion cues from the simulator and seeing the visual cues from the visual system too. The two systems work in lockstep with each other."
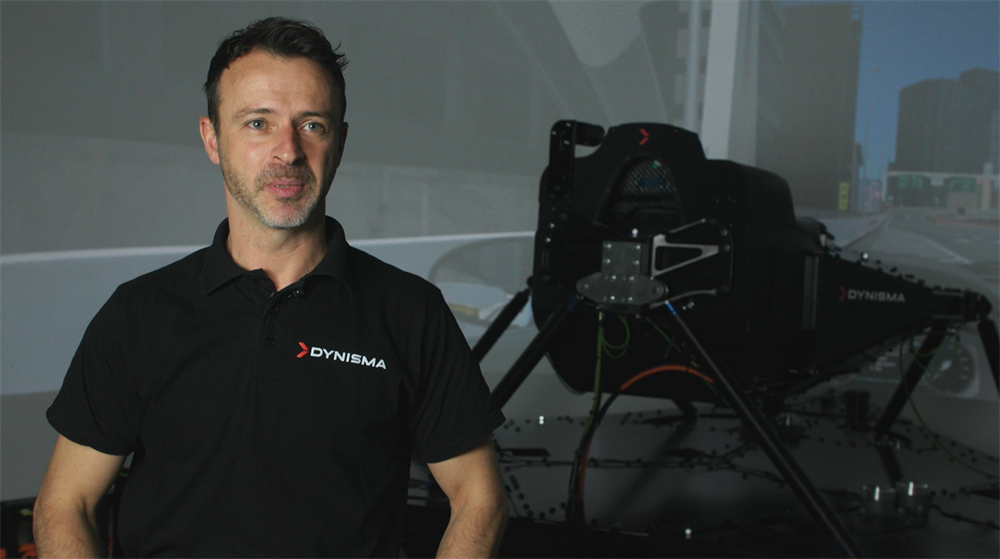
Ash Warne, Chief Engineer and CEO of Dynisma
Challenge
Low latency is also critically important, especially in motorsport, where a driver is trying to drive a racing car on the limit of grip. Latency is the delay between sending motion commands to the motion simulator and the actuation of the commanded motion. When the driver corrects for oversteer, they can only do so as quickly as the motion system provides feedback. The driver can drive the simulated car in a more accurate fashion because of low latency.
For example, in some simulators, where the latency is higher, extra understeer might have to be programmed into the vehicle model just to make the vehicle controllable. Low latency enables a fully correlated vehicle model to be used which gives the driver an accurate simulation of the real-world driving experience.
In automotive design, the simulation of an accurate full vehicle model is essential in representing the behaviour of the vehicle related to its dynamic system performance such as ride comfort and handling.
“Our technology's incredibly low latency is particularly useful when the driver needs to respond very rapidly to the stimuli that they get from the motion generator. The information that we provide through the motion generator is very dependent on the use case that our customer is evaluating. For example, automotive ride simulation is all about the vertical dynamics of the car as it goes over the bumps in the road, the cat's eyes, potholes, and rumble strips, and providing a very accurate representation to the driver and the passenger within the vehicle of those things,” says Ash Warne
Joshua Bell continues: “Latency is a key USP for us. The whole round-trip latency is important – any latency in our feedback is then going to feed through to the driver.”
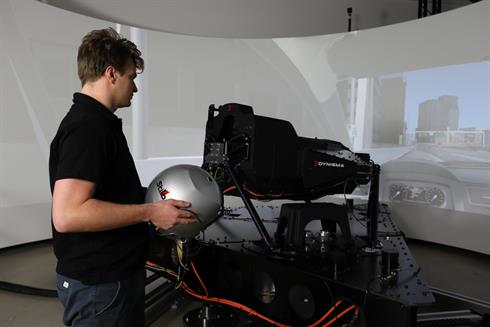
Joshua Bell, DMG-1 Engineering Lead of Dynisma
Solution
Dynisma selected the LA11 absolute magnetic linear encoder from Renishaw associate company RLS, to enable precise position control of the belt-driven actuators that drive the LFP responsible for large movements (excursions).
The LFP comprises three belt driven actuators (ground rails) arranged in a triangle, which interface with the tri-base of the HFP via three passive radial rails. The three ground rails enable motion with three degrees of freedom (longitudinal, lateral, yaw) over a large excursion. In contrast, the HFP employs six actuators to enable six degrees of freedom in a smaller motion envelope but with higher fidelity.
In particular, the electronics design of the LA11 absolute encoder provides short response and recovery times. The LA11 encoder also features communications interface options that enable dual output of both absolute position readings via serial communication and incremental position readings.
As Joshua Bell explains: “The LA11 encoders are all on the low-frequency platform. So, on our demonstrator system we have got six on the three ground rails, which are the ones that go radially outwards, and on the customer systems we have nine. The encoders output to Beckhoff safety slices which feed into our safety program where we monitor the position and velocity of the system. As a result, we can safely shut down any system that exceeds its safe performance envelope.”
“The main requirement for DMG-1 was that we needed an encoder that gave absolute feedback and incremental feedback in the same readhead. We essentially wanted direct feedback to the safety system for both the position and velocity of the relevant axis; if we had to do that with an encoder that only gave us an absolute signal then we would need to fit a different encoder for an incremental signal which takes up more packaging space. The LA11 was ideal because it minimised our space requirements by producing both absolute and incremental signals from one readhead and scale tape,” Joshua Bell concludes.
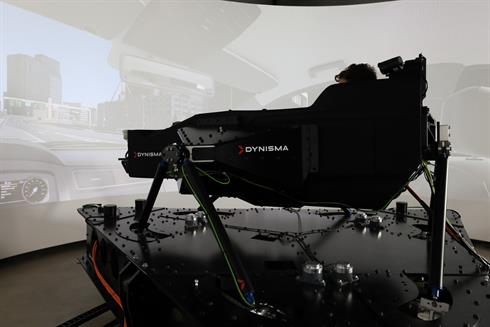
DMG-1 motion generator
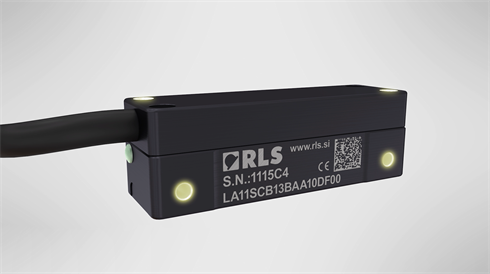
RLS' LA11 absolute magnetic linear encoder
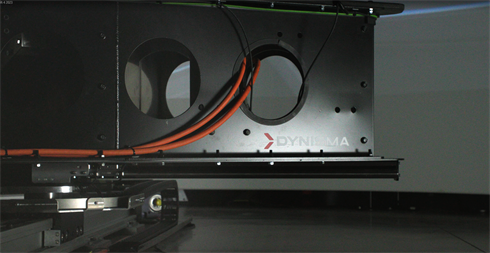
The LFP comprises three belt driven actuators (ground rails)
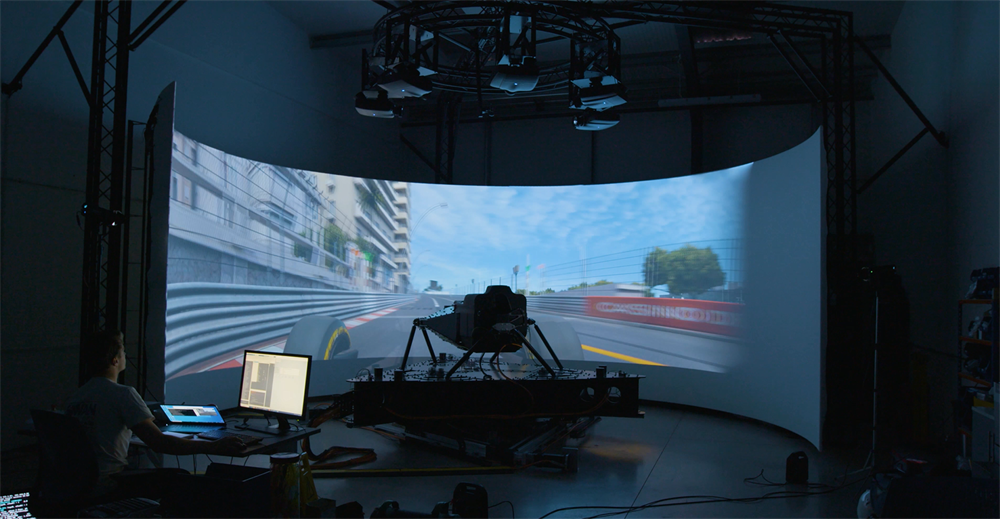
Results
“Initially we approached Renishaw for a specific requirement on a previous system where they recommended the RLS LA11 encoder. Since then, we realised it was also a great fit for DMG-1. We are delivering three DMG-1 systems to customers in the automotive and motorsport sector over the next 6 to 12 months and beyond that we have future orders in the pipeline, so we expect to continue that relationship with Renishaw and RLS,” says Joshua Bell.
For years, Renishaw and RLS have cultivated a working partnership with Dynisma through an extensive and diverse product offering backed by excellent technical and engineering support that has a material impact on customers' businesses.
Ash Warne continues: “Dynisma delivers projects across the world for our customers in both motorsport and automotive, in Europe, North America and beyond. So, there is already a strong market for new Dynisma products such as DMG-1. We have a very strong working relationship with Renishaw and RLS - their products match our requirements and use cases very well. We have also received excellent product selection help and technical support from both businesses. Dynisma is always focused on developing and expanding our product development roadmap, so we have plans to continue to develop our technology for years to come and we look forward to working with Renishaw and RLS on our future products.”
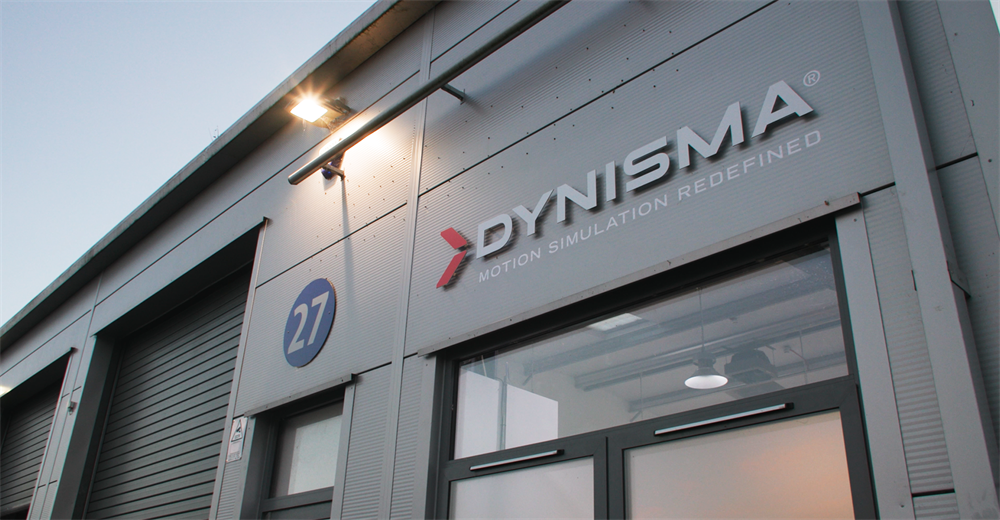