Diese Seite steht derzeit nicht in Ihrer Sprache zur Verfügung. Mittels der
Übersetzungsfunktion
von Google kann Ihnen eine automatische Übersetzung angezeigt werden. Bitte beachten Sie jedoch, dass wir keinerlei Verantwortung für diese
Dienstleistung tragen und die Übersetzung auch nicht von uns geprüft wurde.
Wenn Sie weitere Unterstützung benötigen,
kontaktieren Sie uns bitte.
New ballbar technology 'just what the doctor ordered' for medical machine tools
Ballbars have been commonplace at precision machining operations for more than 20 years, but a Midwest-based medical device manufacturer is showing how the latest wireless ballbar technology makes a big difference in doing fast capability checks on small machines, as well as establishing a benchmark on machines' volumetric accuracy.
Wireless operation facilitates use in small machining envelopes, and allows fast checks with minimal interruption. Volumetric accuracy testing adds new dimension. Fort Wayne, Indiana, USA – Ballbar analysis is a proven method for determining machine tool capability, and is the most practical, convenient and comprehensive tool for assessing the contouring accuracy of CNC machines.
Nemcomed, a division of Avalign Technologies, is a full-service supplier of implants, instruments, cutting tools, speciality instruments, cases and trays for medical device OEMs. Avalign's strategy is to be a "one stop shop" for OEM providers to the orthopedic, spine and trauma sectors – aiming to supply everything a physician needs to perform implant procedures. Ensuring that machine tools and processes are capable of producing parts to spec is a goal shared by customers and the company's 450+ employees, as well as federal regulatory agencies. "Obviously, we have to meet FDA and ISO requirements," said Eric Arnold, Manufacturing Engineer at Nemcomed. "But we also have special customer requirements, as well a personal interest and pride, knowing that our products may end up in someone's body. As potential patients ourselves someday, we want to make the highest quality parts possible."
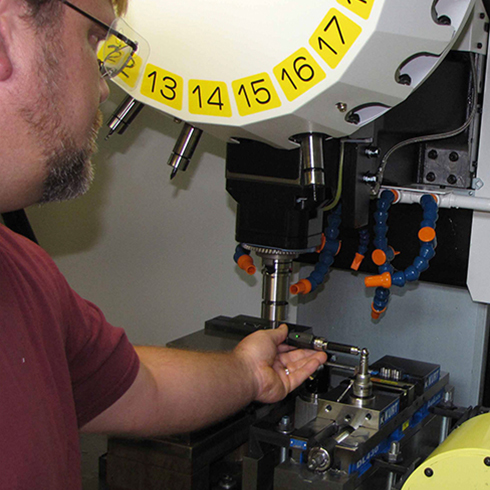
Regulatory environment and customer requirements
As a manufacturer of medical devices, Nemcomed must comply with both the FDA 21 CFR Part 820 Quality System Regulation and the ISO 13485 Medical Device Standard. To qualify machines, the company had been using a traditional wired QC10 ballbar from Renishaw. "We test the X-Y, Y-Z and X-Z planes and the QC10 required a setup for each, so our setup time was about 1.5 hours," said Arnold.
The company acquired Renishaw's new QC20-W wireless ballbar in 2010, which immediately had positive impact on part quality and the company's bottom line. The new ballbar retains the principle of using a CNC circular program and powerful software to quickly diagnose and quantify machine positioning errors including servo mismatch, stick-slip errors, backlash, repeatability, scale mismatch and machine geometry as well as providing an overall circularity error value. It also adds new capabilities. "The wireless ballbar requires just one setup – less than 15 minutes – for testing in all three planes," Arnold said. "More important, it doesn't disturb our production setup, so we don't have to re-set the machine when we go back to production mode. We remove the ballbar, insert a tool and get back to making parts in minutes."
Wireless operation is also ideal for Nemcomed's small machines, Arnold added. "Machine tool makers understand how much ‘lean operations' value floor space, so the new machine tools are designed with smaller footprints," he explained. "This results in less interior space to manoeuvre a wired ballbar, so wireless data transmission is a big advantage. Safety is also improved by the ability to fully close the doors on the machine during the tests."
Surgical implants and instruments
Nemcomed manufactures approximately 1000 different parts – either implants or the tools used during implant procedures – and it supplies parts to the top orthopedic OEMs. The company makes implants for knees, hips, shoulders, wrists, elbows, fingers and the spine; tools include pliers, cutters and wire cutters. The implants are "family-sized," with five to six sizes of each part, and typical lot sizes are 30-40 pieces. Many of the implants have complex features, such as curved or spherical components.
The company also makes proprietary products, developed through internal R&D, and licenses them to customers. Its Flex-Shaft and Self-Retaining technologies, for example, are patented and used in a variety of applications, including spinal procedures and hip, shoulder and knee arthroplasties. The Flex-Shaft is applicable to surgical screwdrivers, taps and drills.
Parts are generally made of stainless steel, titanium or cobalt chrome, and start as bar stock or forgings (implants). Raw materials are processed through a cut-off cell, then move on to a mill or turning center, depending on complexity.
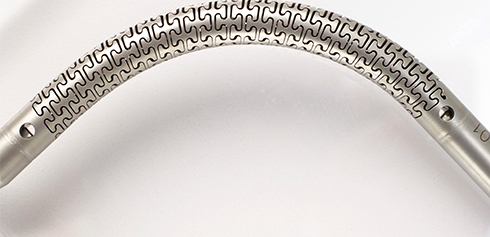
Speed with accuracy
"Shortly after receiving the new ballbar, we had a machine go out of spec so we tested it, as well as having the laser interferometer folks come in and test it," said Arnold. "Our results were identical, so we learned then the ballbar would allow us to test our CNC machines quickly and with an extraordinary level of confidence."
This ability to test quickly and accurately led to the acquisition of a large, quality-focused customer that required verification of machine calibration. "The expense of bringing in the laser interferometer for every machine would have made it cost-prohibitive to supply this customer with parts," Arnold explained. "We showed the customer the results of the ballbar and interferometer tests, and they agreed that ballbar testing would meet their verification requirements. Basically, the QC20-W paid for itself after testing just two machines."
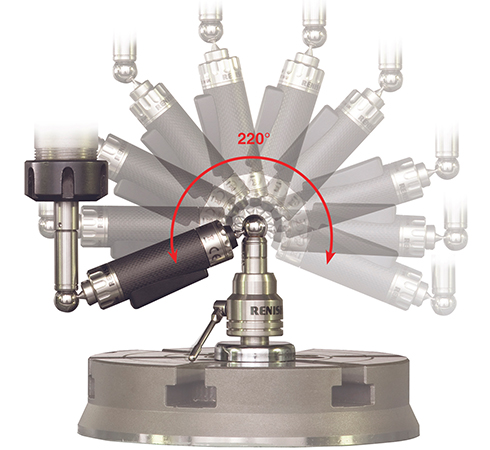
Volumetric testing provides new performance benchmark
The new ballbar design brings the unique advantage of testing in three orthogonal planes through a single reference point, with a single setup, which allows the accompanying software to produce a representative measurement of volumetric positioning accuracy by correlating all three. Arnold explained this benchmark of volumetric accuracy is valuable to Nemcomed because positioning errors can be compounded by simultaneous multi-axis motion during contouring. (Note: volumetric accuracy is also important with large machining volumes and parts, where tool path deviation is amplified across longer machine travels).
In August 2010, Nemcomed completed a 10,000-sq-ft addition to its Fort Wayne plant, to consolidate another plant's operations and add space for new machines: five new Citizen Swiss machines and a 5-axis Fanuc Robodrill to complement its lineup of Mori-Seiki and Mazak 5-axis mills, Fadal 3-axis mills, Brother and Fanuc wire EDMs, and a Samsung 3-axis lathe. The company uses the ballbar on 20 machines, including all of its CNC mills and wire EDM machines. Maintenance engineers monitor results in a predictive maintenance program, tracking a 3-month timeframe for early detection of errors for optimum efficiency in scheduling maintenance and repairs.
The ballbar comes with a system case with spaces for the most popular accessories making it easy to transport. "We can take it to any of our four global manufacturing facilities, set it up quickly and get the machine qualifications we need," Arnold said. "Knowing the machine's capability before it cuts parts allows us to minimize scrap and machine downtime. That gives us high part-quality and productivity while keeping manufacturing cost down. It's what Lean Manufacturing is all about – greater customer value." The company completed another 14,000-sq-ft. expansion in November, and as it continues to grow, Arnold said use of the ballbar will grow.