3D-Metalldruck sprengt die Grenzen in der Moto2™ Motorradrennserie durch eine unkonventionelle Innovation
In der hochoktanigen Welt des MotoGP™ Motorradrennsports können technische Verbesserungen viel bewirken. Das siegreiche Moto2-Team TransFIORmers setzt innovative generative Fertigungstechnologie (3D-Metalldruck) in einem unkonventionellen Vorderradaufhängungssystem ein und erzielt damit einen enormen Wettbewerbsvorteil.
Hintergrund
Bei der MotoGP Weltmeisterschaft eingesetzte Motorräder sind etwas Besonderes. Sie können im Handel nicht erworben und im öffentlichen Straßenverkehr nicht legal bewegt werden. Als Prototyp-Rennmotorräder werden sie spezialgefertigt, um die Konkurrenz abzuhängen und maximale Leistung auf der Rennstrecke zu erbringen.
Moto2, die zweite der drei MotoGP-Klassen, wurde 2010 geschaffen. Der offizielle Einheitsmotor ist ein 600-ccm-Viertaktmotor, der derzeit von Honda geliefert wird. Das französische Moto2-Team TransFIORmers mit Sitz in Perigueux, Südwestfrankreich, revolutioniert die Konstruktion der Vorderradaufhängung, um sich den Vorsprung vor der Konkurrenz zu sichern.
TransFIORmers wird vom früheren WM-Fahrer in der 250er-Kategorie, Christian Boudinot, angeführt und das unkonventionelle Aufhängungssystem des Teams wurde von der wegweisenden Arbeit des legendären französischen Motorradkonstrukteurs Claude Fior inspiriert.
Boudinots früherer Freund und Mentor, Fior, erkannte die durch die Isolierung der Vorderradaufhängung von den Lenkkräften erzielbaren Vorteile. Die Konstruktion löst Bremsnickprobleme und ermöglicht dadurch ein späteres Abbremsen in Kurven und ein kraftvolleres Herausbeschleunigen.
Anstelle der herkömmlicheren Teleskopgabelaufhängung verfügt das TransFIORmers Motorrad über ein starres Vorderradgabel-Aufhängungssystem, das vom Chassis mittels zweier Querlenker getrennt ist.
Um die Entwicklung seiner Konstruktion weiter voranzutreiben, wandte sich das TransFIORmers-Team an I3D Concept, einem weltweit führende Unternehmen für verfahrensgerechte Konstruktion und additive Fertigung auf Metallbasis.
Unter Einsatz des generativen Fertigungssystems AM250 von Renishaw arbeitete I3D Concept eng mit dem TransFIORmers-Team zusammen, um die Konstruktion der oberen Querlenkerkomponente zu optimieren, die in Verbindung mit einer weiteren, die Vorderradgabel mit dem Chassis verbindet und für die Lenkung des Motorrads ausschlaggebend ist.
Herausforderungen
Bei der Entwicklung neuer Komponenten in der Moto2-Entwicklung geht es vorrangig um eine Gewichtsreduktion. Insbesondere die Verringerung der ‚ungefederten Massen' des Motorrads ist ein zentraler Aspekt. Je geringer die ungefederten Massen sind, desto besser ist die Aufhängung im Hinblick auf Vibrationsmanagement und Reaktionsvermögen, sowohl beim Bremsen, als auch beim Beschleunigen.
Gleichermaßen entscheidend ist die Schnelligkeit, mit der die Konstruktion einer neuen Komponente abgeändert werden kann, sowie die für die Neufertigung benötigte Zeit. Die Erzielung von Perfektion in einem wettbewerbsintensiven Umfeld setzt eine schnelle und präzise Komponenteniteration voraus.
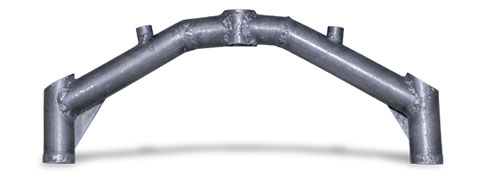
Ursprüngliche zwölfteilige Stahlkomponente
In einer auf hohe Zuverlässigkeit ausgerichteten Umgebung stellt die mechanische Festigkeit einen weiteren wesentlichen Aspekt dar. Die Querlenkerkomponente von TransFIORmers muss größtmögliche Steifigkeit gewährleisten und gleichzeitig erhebliche dynamische Lenkkräfte aufnehmen können.
„Um die Leistungsfähigkeit des Motorrads insgesamt zu verbessern, ist es extrem wichtig, dass das Gewicht aller hinter den Stoßdämpfern angeordneten Komponenten reduziert wird. Wird das Gewicht der Komponenten nicht optimiert, kann sich dies nachteilig auf Vibration sowie Brems- und Beschleunigungsvorgänge auswirken, weshalb die Gewichtsverringerung ein ganz entscheidender Aspekt ist,” erklärt Jérôme Aldeguer von TransFIORmers.
Dank der Gewichtsverringerung, die durch die additive Fertigung bei unserer Querlenkerkomponente erzielt werden konnte, ließen sich das übliche Gewichtsverlagerungsphänomen und darüber hinaus die mit dem ‚Bremsnicken‘ verbundenen Probleme umgehen. Nicht nur das: Mithilfe dieses Verfahrens konnten wir ein Bauteil konstruieren, das nicht nur leichter, sondern gleichzeitig auch viel steifer ist.
TransFIORmers (Frankreich)
Lösung
Die ursprüngliche Querlenkerkomponente von TransFIORmers war aus Stahl handgefertigt, wobei sich die Baugruppe aus zwölf getrennt gefertigten und verschweißten Bauteilen zusammensetzte. I3D Concept konstruierte aus der Vielzahl an Kompnonenten ein einzelnes Bauteil und reduzierte dadurch erheblich die Montagezeit.
Das Unternehmen stellte den 3D-gedruckten Querlenker aus Metall mit dem generativen Fertigungssystem AM250 von Renishaw her: zuerst der Prototypenbau aus rostfreiem Stahl und anschließend die Fertigung eines leichteren Bauteils aus Titan.
Der Schlüssel zum neuen 3D-Bauteildesign war ein iterativer Prozess der topologischen Optimierung, bei dem die Querlenkerkonzeption innerhalb enger räumlicher Konstruktionsgrenzen schrittweise in der Software rationalisiert wurde, um einer Reihe von vordefinierten Belastungsbedingungen der Vordergabel standzuhalten.
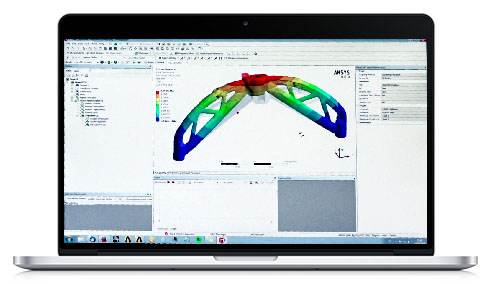
CAD-Entwicklung der generativ gefertigten Titankomponente
Nach Prüfung des finalen Bauteildesigns mithilfe digitaler CAD-Software, wurde die Bauprozessvorbereitungsdatei vor dem anschließenden Export an das generative Fertigungssystem erstellt.
Innerhalb der CAD-Software konnte I3D Concept feststellen, ob die Parameter zweckmäßig vorgegeben waren oder ob sie auf die Eigenschaften des speziellen Metallpulvers und die komplexen Zielgeometrien des Querlenkers von TransFIORmers abgestimmt werden mussten.
Vor allem aber konnte I3D Concept mithilfe der dedizierten Steuerungssoftware Optical Control System (OCS) des AM250 Systems die Lasersteuerung sehr präzise kontrollieren, wodurch sich Genauigkeit, Merkmaldefinition und Oberflächengüte verbessern ließen.
Ergebnisse
Dank der Anwendung der generativen Fertigung bei der Moto2-Rennmaschinenkonstruktion ist es dem TransFIORmers-Team gelungen, das Gewicht der zentralen Querlenkerkomponente an der Vorderradaufhängung um erhebliche 40 % zu reduzieren. Beim Vergleich der einteiligen Titankomponente mit der ursprünglich geschweißten Stahlkomponente lässt sich eine Gewichtseinsparung von 600 g erreichen.
3D-gedruckte einteilige Titankomponente
Der 3D-Metalldruck bot dem TransFIORmers-Team auch eine wesentlich genauere Kontrolle über die allgemeinen und spezifischen Werkstücktoleranzen, sowie die Flexibilität, die Querlenkergeometrien sehr schnell an bestimmte Chassis- und Kinematikanforderungen iterativ anzupassen.
„Dank der Gewichtsverringerung, die durch die additive Fertigung bei unserer Querlenkerkomponente erzielt werden konnte, ließen sich das übliche Gewichtsverlagerungsphänomen und darüber hinaus die mit dem ‚Bremsnicken‘ verbundenen Probleme umgehen. Aber nicht nur das: Mithilfe dieses Verfahrens konnten wir ein Bauteil konstruieren, das nicht nur leichter, sondern gleichzeitig auch viel steifer ist,” erläutert Jérôme Aldeguer vom TransFIORmers-Team.
Mit einer ultimativen Zugfestigkeit von mehr als 1100 MPa bei der additiven Fertigung und einer fast perfekten Dichte von 99,7 % ergab die verwendete Titanlegierung Ti6AI4V einen grundlegend neuen Querlenker, der eine sehr viel größere Steifigkeit als die ursprüngliche mehrteilige, handmontierte Stahlkomponente bietet.
Dank der generativen Fertigung erwies sich die Entwicklung des Prototyp-Querlenkers vom TransFIORmers-Team als hocheffizienter und kostengünstiger Prozess. Zu hohe Herstellkosten für die Teilebearbeitung und die Montagezeit wurden beseitigt, während die Iterationsschritte in der Konstruktion und die Bauteilfertigung um ein Vielfaches beschleunigt wurden.
Im Juni 2016 gewann das Team sein allererstes Moto2 GP-Rennen bei der Spanischen Meisterschaft (FIM CEV) in Barcelona.