Messtaster mit Dehnmessstreifen: Höchste Antastgenauigkeit und Messleistung bei der Formmessung 5-Achsig gefräster Bauteile für die Luft und Raumfahrtindustrie.
Als Spezialist auf dem Gebiet der Streckziehbearbeitung von Bauteilen für die Luftfahrtindustrie gibt es in der Fertigung bei Triumph kaum Bauteile oder Umformwerkzeuge, die nicht eine parabolische, komplex gebogene oder konische Form aufweisen.
Eine Kernkompetenz des Unternehmens ist die schnelle, präzise Messung der Bearbeitungsschritte an diesen Bauteilen und wurde von der CAD/CAM-Abteilung entwickelt. Während der Messung verbleibt das Bauteil einfach in der Werkzeugmaschine aufgespannt. Es bedurfte jedoch eines RMP600 Messtasters mit Dehnmessstreifen, um die notwendige Antastgenauigkeit für eine beständige, hochpräzise Messung etwa von kleinen Bohrlochdurchmessern, Konturen und geometrischen Toleranzenzu erzielen. Ohne richtungsabhängige Antastunsicherheit (d. h. wahre dreidimensionale Schaltcharakteristik) und mit einer Wiederholgenauigkeit von 0,25 µm liefert der Dehnmessstreifen-Messtaster nach einer einmaligen Kalibrierroutine hohe Genauigkeit bei Auslenkung aus beliebiger Richtung.
Der RMP600 in Kombination mit der OMV Software von Renishaw verleiht der Zimmermann CNC-5-Achsen-Portalfräsmaschine des Unternehmens KMG-ähnliche Fähigkeiten, sodass komplexe Bauteile direkt ab der Maschine endabnahmefertig sind, wobei die Messergebnisse stets bei der Überprüfung durch andere Geräte innerhalb von 0,025 mm liegen. Demzufolge fallen Offline-Kontrollen der Arbeit auf einem echten KMG im Wesentlichen weg, wodurch das Unternehmen Produktionsverzögerungen, potenzielle Schäden und Genauigkeitsprobleme vermeidet, die normalerweise beim Umsetzen und erneuten Aufspannen hochwertiger Teile entstehen.
Die Kernkompetenz von Triumph Fabrications ist das Streckziehen von Blechen sowie extrudierten, Walzprofil- und Leichtplatten-Metallen für die Luftfahrtindustrie. Die Presskraft des Unternehmens reicht von 10 bis 750 Tonnen, wobei das Streckziehen von Gegenformen mithilfe von Bulldozer-Anbaugeräten mit 150 und 400 Tonnen auf eigenen Cyril-Bath-Pressen möglich ist. Das Unternehmen besitzt auch einzigartige Kompetenzen im Streckziehverfahren für die komplexe Einebenen- und Mehrebenen-Formung verschiedener Metalle.
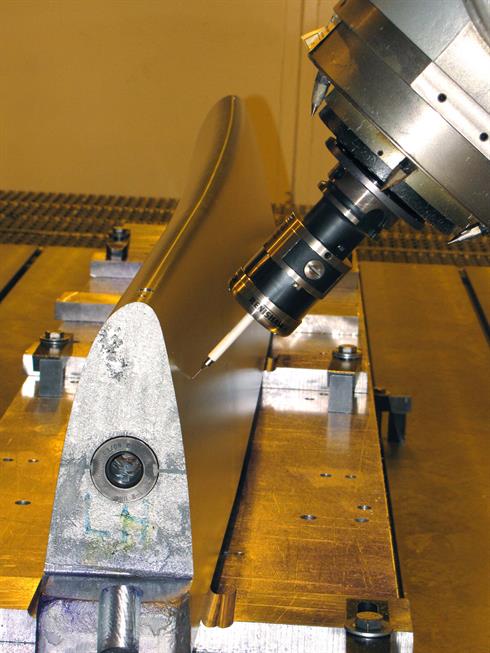
Die Kernkompetenz von Triumph Fabrications ist das Streckziehen von Blechen sowie extrudierten, Walzprofil- und Leichtplatten-Metallen für die Luftfahrtindustrie. Die Presskraft des Unternehmens reicht von 10 bis 750 Tonnen, wobei das Streckziehen von Gegenformen mithilfe von Bulldozer-Anbaugeräten mit 150 und 400 Tonnen auf eigenen Cyril-Bath-Pressen möglich ist. Das Unternehmen besitzt auch einzigartige Kompetenzen im Streckziehverfahren für die komplexe Einebenen- und Mehrebenen-Formung verschiedener Metalle.
Nach Ansicht des Leiters der CAD/CAM-Abteilung, Gary Medlock, ist das Messen auf der Maschine ausschlaggebend für die Zielsetzung des Unternehmens, Zykluszeiten zu verkürzen, Nacharbeit zu eliminieren und Fehler zu reduzieren, die sich durch das mehrfache Aufspannen eines Bauteils einschleichen können. „Wir messen lieber direkt bei der Bearbeitung, als das Bauteil zu einem KMG zu bringen“, so Medlock. „Es handelt sich zunächst einmal um hochwertige Bauteile und mit jedem Bearbeitungsvorgang auf der Zimmermann steigern wir den Wert. Bei Teilen wie dem Umformwerkzeug für eine Führungskante (in den beiliegenden Fotos zu sehen) würden wir sonst beinahe einen ganzen Tag durch das Abspannen, Messen und erneute Einrichten des Werkstücks verlieren; oder wir könnten das Bauteil komplett fertigstellen, dann prüfen und hoffen, dass keine Nacharbeit mehr nötig ist. Durch das Messen im Bearbeitungsprozess wird sichergestellt, dass jede einzelne Arbeitsphase den Spezifikationen entspricht, bevor wir weiter in das Bauteil investieren.“
Normalerweise sind auf der Fräsmaschine von Zimmermann bearbeitete Bauteile geformte, 0,635 mm bis 3,18 mm starke Blechteile, an denen Bohrungen und Ausschnitte vorzusehen sind. Diese Bauteile werden mit Vakuum gespannt. Bohrungen von 2,5 mm bis 9,5 mm – wie sie bei Flugzeugteilen typisch sind – werden gebohrt und mit einer Genauigkeit von 0,05 mm aufgerieben; die wahren Positionstoleranzen liegen bei 0,30 mm bis 0,71 mm. „Wir messen die Bohrlochgröße und wahre Position mit dem RMP600 Messtaster. Dabei verwenden wir einen 1-mm-Taster aus Hartmetall oder Edelstahl, eine 50-mm-Verlängerung und die Messmethode mit Zweifachantastung“, erklärt Medlock. „Wir bevorzugen die Hartmetallkugel, weil wir damit tief in die Bohrung gelangen. Wenn die Orientierung geschickt gewählt wird, kann mit dieser Kugel nahezu jede Messung durchgeführt werden. Die 50-mm-Verlängerung an einem RMP600 Messtaster hat keinen Genauigkeitsverlust zur Folge, gewährleistet ausreichend Abstand zwischen Messtaster und Werkstück zur Minimierung der Zusammenstoßgefahr und ist im Falle einer Kollision auch günstiger zu ersetzen. Wir führen Messungen mit Zweifachantastung aus, da wir die Kalibrierung mit derselben Geschwindigkeit ausgeführt haben, die wir auch in der Software verwenden, sodass sämtliche Zeiten und Winkel festgelegt sind.“
Die regelmäßige Genauigkeitsüberprüfung der Maschinen ist einer der Schlüssel zu dem von Triumph mit seinen Messergebnissen erzielten Erfolg und dem gewonnenen Vertrauen in die Ergebnisse. „Wir überprüfen die Genauigkeit der Maschine einmal im Jahr mit einem Laserinterfereometer und einem Kreisformmesssystem, sofern nicht ein größerer Defekt vorliegt“, meint Medlock. „Wir haben auch eine kleine Kalibrierkugel auf der Maschine, die wir wöchentlich kalibrieren, wobei wir die Maschine durch verschiedene bekannte Winkel rotieren und die Kugel mit dem Messtaster berühren. Die Ergebnisse werden in einem Balkendiagramm dargestellt, wobei die Daten bis zu zwei Jahre zurückgehen, sodass sich eine Trendentwicklung leicht erkennen lässt. Außerdem besitzen wir ein rückführbares Kalibriernormal mit Kegel, Kugel, Schlitzen und anderen Merkmalen, die wir messen, wann immer eine Komponente unseres QC-Programms abgeändert wird.“
Triumph besitzt zwei Portalfräsmaschinen von Zimmermann. Das neuere Modell FZ-30, Baujahr 2008, ist mit einer Siemens CNC-Steuerung 840D ausgestattet. Diese spezielle Maschine besitzt einen X-Y-Z Linearachsenbereich von 6 x 2,8 x 1,5 m, 110_ A-Achse und 360_ Z-Achse. Ihre Spindel erzeugt maximal 40 kW Leistung und 48 Nm Drehmoment bei einer Höchstgeschwindigkeit von 25.000 min-1. Das Werk selbst ist klimatisiert. „Diese Maschine besitzt eine volumetrische Genauigkeit von 0,1 mm, und bei einer großen, gut genutzten Werkzeugmaschine ist dies ohne Weiteres mit typischer KMG-Genauigkeit vergleichbar“, erklärt Medlock.
„Mit Blick auf die herausragenden Fähigkeiten des RMP600 haben wir außerdem unter Beweis gestellt, dass wir den genauen Durchmesser kleinerer Bohrungen bis 0,098 Zoll (2,49 mm) mithilfe eines 1-mm-Tasters messen können.“
Triumph Fabrications (UK)
„Ohne den Messtaster müssten wir alternativ Bauteile zum KMG-Raum bringen, die Messung durchführen, sie anschließend wieder zurückbringen und einrichten“, so Medlock. „Wir müssten eine Prüfnut oder ein anderes Merkmal vorsehen, um sicherstellen zu können, dass jede Einrichtung der ersten entspricht. Das bedeutet höhere Kosten am Bauteil, ganz zu schweigen von einem verlorenen Tag für die Durchführung des gesamten Prüfzyklus.
Diese Verzögerungen und die Unsicherheit, die jede neue Einrichtung mit sich bringt, sind in einem schlanken Betrieb einfach inakzeptabel. Im Schnitt ist unser Messzyklus ungefähr gleich lang wie der Bearbeitungszyklus, allerdings ist dies ein sehr allgemeiner Mittelwert und bei manchen Bauteilen erfolgt die Prüfung sehr viel schneller, ganz nach Anzahl der Merkmale. Bei der Messung von Bohrungen beispielsweise veranschlagen wir pro Bohrung etwa 8 Sekunden.“
Ein weiterer Schlüssel zur Effizienz von Triumph ist die Programmierung von Modell und Geometrie. „Alle Merkmale müssen sich auf dem Bauteil befinden, wenn alles ordnungsgemäß laufen soll“, betont Medlock. „Wir starten normalerweise mit einer STEP-Datei, die zur Offline-Erstellung des Messprogramms in die OMV Software importiert wird. Die Software simuliert die Messroutine zwecks Kollisionserkennung und verfügt über eine „Auto-Orientierungs“-Funktion, dank derer der Messtaster automatisch in eine geeignete Messposition orientiert werden kann, ohne dass eine manuelle Eingabe des erforderlichen Winkels erforderlich ist. Merkmale lassen sich auf viele Arten messen – beispielsweise kann eine Bohrung als Kreis oder Zylinder gemessen werden.“
Das Messprogramm läuft auf der CNC zur Erfassung der Messdaten, die dann offline in der OMV Software mit KMG-ähnlichen Algorithmen ausgewertet werden. Die Software vergleicht die Messdaten mit der Map-/Modell-Datei und erstellt grafische und tabellarische Messprotokolle. Die Software protokolliert die Abweichungen von den Sollwerten und erstellt ein diesbezügliches Diagramm.
Ein Assistent für Form- und Lagetoleranzen in der OMV Software führt Programmierer durch den Prozess zur Erstellung standardisierter Berichtelemente basierend auf international anerkannten Symbolen, sodass ein Vergleich der Messergebnisse von der Maschine zur Fertigungszeichnung möglich ist. „Wir arbeiten derzeit mit Rechtwinkligkeit, Neigung, Oberflächenprofil und wahrer Position“, fügt Medlock hinzu.
Anders als herkömmliche Messtaster für Werkzeugmaschinen muss der RMP600 mit Dehnmessstreifen nicht für jeden Vektor kalibriert werden, was eine erhebliche Zykluszeitverkürzung in einer 5-Achsen-Umgebung ermöglicht. „Wir messen aus allen Vektoren, da es sich um eine 5-Achsen-Anwendung handelt“, erklärt Medlock. „Aufgrund des besonderen Schaltsystems mit Dehnmessstreifen im RMP600 erhalten wir immer ein korrektes Messergebnis, – unabhängig davon, aus welcher Richtung wir mit dem Taster antasten. Das ist in einer 5-Achsen-Welt perfekt. Bei der Arbeit in fünf Achsen wird der Messtaster bisweilen in ungewöhnlichen Orientierungen eingesetzt und die Kugel kann aus praktisch jeder Richtung berührt werden. Wir haben überprüft, dass wir bei einer Messung mit dem RMP600 exakt dieselben Messergebnisse erhalten, wenn wir anschließend nochmals messen müssen. Mit Blick auf die herausragenden Fähigkeiten des RMP600 haben wir außerdem unter Beweis gestellt, dass wir den genauen Durchmesser kleinerer Bohrungen bis 0,098 Zoll (2,49 mm) mithilfe eines 1-mm-Tasters messen können.“Der RMP600 unterscheidet sich grundsätzlich von herkömmlichen Messtastern für Werkzeugmaschinen, denn der patentierte RENGAGE™ Antastmechanismus beseitigt die Antastunsicherheit, ein bei allen herkömmlichen, kinematisch schaltenden Messtastern typischerweise auftretender Fehler. Ist die Antastunsicherheit zu stark und groß genug, um sich auf die Messgenauigkeit auszuwirken, müssen Anwender für eine Kompensation durch Kalibrierung des Messtasters entlang jedes Messvektors sorgen. Dies setzt einen komplexen Kalibrierzyklus und die Verwaltung zahlreicher Messtasterkorrekturen voraus.
Beim RMP600 fällt dies alles weg. Dehnmessstreifen messen die auf den Taster ausgeübte Antastkraft und erzeugen einen Schaltpunkt bei Überschreitung des Schwellwertes für die Dehnbeanspruchung. Dadurch werden niedrige Auslösekräfte, eine geringere Tasterdurchbiegung, höchste Wiederholgenauigkeit (0,25 µm 2σ), keine Antastunsicherheit und eine tatsächlich dreidimensionale Schaltcharakteristik erzielt. Der RMP600 liefert eine bedeutend höhere Messleistung, insbesondere bei 3D-Flächen, bei denen viele Antastrichtungen verwendet werden, oder bei der Einrichtung, wenn Anfahrvektoren zum Werkstück möglicherweise nicht bekannt sind. Eine spezielle Logik im Messtaster verhindert unerwartete Auslösungen infolge von Stößen und Vibrationen durch Feststellung, ob die an den Messstreifen wahrgenommene Dehnbeanspruchung durch Kontakt mit der Bauteiloberfläche oder ein zufälliges Ereignis verursacht wurden.
„Natürlcih kann der Messtaster letzlich nur so genau sein wie die Maschine selbst“, betont Medlock. „Ausgehend von unserer Kenntnis über die Maschinenfähigkeit, den -zustand und die Kalibrierhistorie dieser Maschine kommt eine Prüfung auf dieser Maschine aus unserer Sicht einer KMG-Prüfung gleich. Die Maschine wird nach den grundsätzlich gleichen Vorgaben wie unsere KMGs getestet und kalibriert und ist problemlos in der Lage, eine Profilgenauigkeit des Bauteils von 0,38 mm zu liefern. Wir können unsere Messleistung durch Messung eines bekannten Kalibriernormals überprüfen, das sämtliche Merkmale aufweist, die wir bei unseren Bauteilen erwarten. Aufgrund der hohen Genauigkeit dieser Maschine und ihrer 5-Achsen-Fähigkeit hat sich der Messtaster mit Dehnmessstreifen für unsere Messanforderungen als bessere Wahl herausgestellt. Regelmäßige Überprüfungen mit anderen Messgeräten ergeben selten Abweichungen von mehr als einem Tausendstel Zoll, was unser Vertrauen stärkt und besonders effiziente Betriebsabläufe ermöglicht.“