Genauigkeit ist alles
Die Präzisionstechnik für den Luft- und Raumfahrt und Automobilsektor erfordert einen proaktiven Ansatz für die Prüfung komplexer Bauteile. Der italienische Lohnfertigungsbetrieb R. Busi hat die strategische Entscheidung getroffen, auf 5-Achsen Koordinatenmessgeräte (KMG) umzustellen. Mithilfe der 5-Achsen Messköpfe von Renishaw konnte das Unternehmen die Prüfanforderungen für die zunehmend komplexen Werkstückdesigns erfüllen und die vorgegebenen Toleranzen und Wiederholgenauigkeiten liefern.
Hintergrund
R. Busi Officine Meccaniche di Precisione (Lohnfertigungsbetrieb für Präzisionsteile) wurde 1946 in der Provinz Pavia, Italien, von Raffaele Busi gegründet und fertigt Präzisionsteile aus Metall im Kundenauftrag.
Das Unternehmen, das auf den Werten einer Fertigung mit höchsten Qualitätsansprüchen aufgebaut wurde, ist heute strategischer Partner vieler bekannter nationaler und internationaler Marken aus unterschiedlichsten Branchen, insbesondere der Luft- und Raumfahrt und Automobilindustrie.
R. Busi operiert von einem 22 000 m² großen Standort in Mezzanino, Italien, aus. Im Werk befinden sich 40 Produktionsmaschinen, einschließlich Drehmaschinen, vertikale 5-Achsen Fräsmaschinen und horizontale 4-Achsen Bearbeitungszentren. Das Unternehmen beschäftigt 40 Fertigungsmitarbeiter, die in zwei Schichten arbeiten.
Es stellt sowohl Präzisionsteile in großen Losen als auch einmalige Prototypen für zahlreiche Kunden her. Es genießt besondere Anerkennung für seine Arbeit in der Luft- und Raumfahrtindustrie, wo sehr enge Toleranzen und eine hohe Wiederholgenauigkeit von entscheidender Bedeutung sind.
Gianmarco Ballerini, Technischer Leiter bei R. Busi, berichtet: „Wir sind enorm stolz auf die Präzisionsarbeit, die wir in technologisch fortgeschrittenen Sektoren wie der Luft- und Raumfahrt leisten. Davon abgesehen lassen sich einige unserer feinsten mechanischen Konstruktionsteile auf unsere frühesten Anfänge zurückverfolgen, wo wir die kleinsten der in Industrienähmaschinen verborgenen Komponenten produziert hatten. Die Toleranzen waren extrem eng und eine vollkommen makellose Ausführung wurde benötigt. Selbst damals war die Arbeit sehr anspruchsvoll.”
Die Werkstückprüfung und Qualitätskontrolle sind von wesentlicher Bedeutung für R. Busi und das Unternehmen musste sich schnell weiterentwickeln – von manuellen Messungen im Prozess, wo häufig im eigenen Hause entwickelte und hergestellte Präzisionswerkzeuge verwendet wurden, bis hin zum Einsatz von programmierbaren KMGs.
Im Rahmen seiner Philosophie der kontinuierlichen Verbesserung hat das Unternehmen beschlossen, den Schritt zu einer 5-Achsen KMG-gesteuerten Werkstückprüfung zu machen.
R. Busi (Italien)
Herausforderung
Jede Weiterentwicklung des Teileprüfprozesses musste in der Lage sein, die hochproduktiven Durchsatzraten zu unterstützen, die im Werk von R. Busi erzielt werden. Die Migration auf 5-Achsen KMGs durfte keine Störungen oder Engpässe im Betrieb verursachen.
Gleichzeitig musste die vom Unternehmen eingeführte 5-Achsen-Messtechnik die Flexibilität bieten, die für die Prüfung der unterschiedlichen, für eine Vielzahl verschiedener Bereiche der Industrie gefertigten Werkstücke benötigt wird.
Genauigkeit war natürlich ein absolut wichtiges Kriterium für die Wahl der 5-Achsen-Messlösung. Sie müsste die höchsten Standards der Luft- und Raumfahrt, wo eine 100%-ige Werkstückprüfung absolute Vorbedingung ist, erfüllen können.
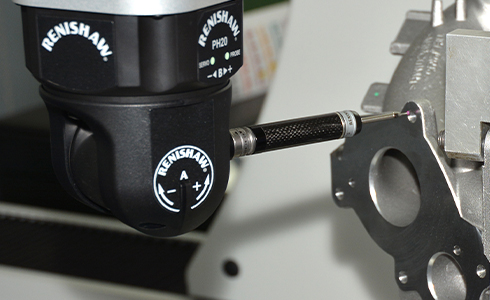
Renishaws PH20 KMG-Messkopf bei der Werkstückmessung bei R. Busi
Lösung
Zunächst veranlasste das Unternehmen die Nachrüstung eines bestehenden 3-Achsen KMGs mit einem Messkopf. Nachdem sich das System bewährt hatte, kamen zwei neue KMGs hinzu, beide mit einer Spezifikation, die von Anfang an die 5-Achsen-Messköpfe einschloss. Die REVO® und PH20 5-Achsen-Messsysteme wurde für den Einsatz spezifiziert.
Paolo Orlandi, Qualitätsleiter bei R. Busi, erklärt: „Wir verwendeten bereits Werkzeugmaschinen-Messtaster von Renishaw in unseren Fertigungsprozessen. Die Ausstattung eines speziellen Messraumes mit zugehöriger Technologie desselben Lieferanten war daher ein Schritt, der logisch und einfach zu treffen war.“
„Da unsere Fertigungsprozesse häufig ziemlich komplexe, maßgeschneiderte Werkstücke umfassen können, wünschten wir uns eine echte Veränderung zu einer Technik, die mehr Vorteile als ein einfaches 3-Achsen KMG bot. Etwas, das uns die von uns benötigte Genauigkeit, Flexibilität und Schnelligkeit bieten würde.“
Sergio Orlandi, Eigentümer von R. Busi
Schnelle schaltende Messung
Die einzigartige „Head Touch“-Methode (Kopfantastung) des PH20 5-Achsen-Messtastersystems ermöglicht R. Busi die Erfassung von Messpunkten durch Bewegungen des Messkopfes und nicht der KMG-Struktur. Infolgedessen können Messungen schneller und mit verbesserter Genauigkeit und Wiederholpräzision aufgenommen werden. Außerdem reduziert sich der Zeitaufwand für Indexierungen des Kopfes dank der 5-Achsen-Bewegung. Zusammen ergeben diese Faktoren typischerweise einen dreimal höheren Messdurchsatz im Vergleich zu herkömmlichen Systemen.
Darüber hinaus garantieren die unbegrenzten Positioniermöglichkeiten des PH20 einen optimalen Zugang zu Merkmalen bei minimalen Tastereinsatzwechseln. Da der für die Kopfrotation benötigte Platz um das Werkstück herum minimal ist, sind Messungen größerer Werkstücke auf dem KMG möglich. Der PH20 richtet sich automatisch zum Werkstück-Koordinatensystem aus und vermeidet somit Messtasterkollisionen und die Verwendung von genauen Spannvorrichtungen.
Der PH20 Schaltkopf wird mit dem in der Industrie bewährten TP20 Messtastersystem verwendet, das R. Busi eine große Auswahl an verschiedenen Antastkräften, Richtungsoptionen und Verlängerungen bietet. Die abnehmbaren TP20 Tastermodule bieten Kollisionsschutz und können unter Verwendung von Renishaws TCR20 Wechselmagazin automatisch gewechselt werden.
5-Achsen-Scanning
Für bestimmte Messungen nutzte R. Busi außerdem das REVO 5-Achsen-Messsystem von Renishaw. Das Unternehmen verwendet das REVO System bei bestimmten Prüfungen zur Form von Bohrungen und anderen Merkmalen, wo mehrere Oberflächendatenpunkte in einem Scandurchlauf ohne Einbußen bei der Messzeit erfasst werden.
Paolo Orlandi, Qualitätsleiter bei R. Busi, bei der Werkstückmessung mit 5-Achsen-Messtechnik
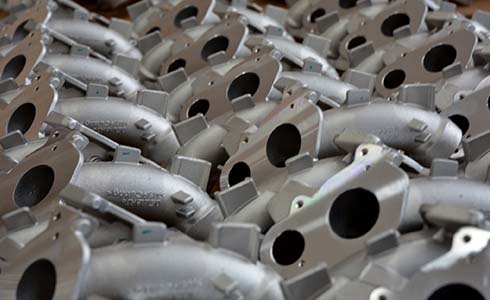
Beispiel für von R. Busi gefertigte Teile
Ergebnisse
Die Einführung der 5-Achsen-Messtechnik hatte weitreichende Auswirkungen auf Geschäftsentwicklung von R. Busi in der Präzisionsfertigung, wie Orlandi erläutert:
„Kurz gesagt bedeutet die Installation von drei 5-Achsen KMGs, die in einem speziellen Messraum arbeiten, nicht nur, dass wir extrem genaue Messungen erhalten, sondern auch, dass wir sie äußerst schnell erhalten. Indem wir die Messgeschwindigkeit drastisch erhöht und die Maschinenstillstandszeit deutlich reduziert haben, konnten wir einen bedeutenden Produktivitätsvorteil für unser Geschäft erzielen.”
„Mit den Messköpfen und Messtastern von Renishaw haben wir nun einfachen Zugang zu jedem erdenklichen Merkmal eines Werkstücks. Wir müssen somit weder spezielle Spannmittel für die Teilepositionierung konstruieren, noch benötigen wir Zugriff auf verschiedenste Tastereinsätze, die kategorisiert und ständig gewechselt werden müssen. Alles ist nun einfacher geworden.”
„Die Lernphase war ebenfalls sehr kurz, unterstützt von einer Software, die bedienerfreundlich ist und extrem genaue Ergebnisse liefert. Bei Bedarf steht uns außerdem ein Renishaw-Experte online zur Verfügung, der uns hilft, schnelle Lösungen zu finden, wenn teilespezifische Probleme auftreten.”
„Aufgrund der schieren Vielfalt und Komplexität der Werkstücke, die R. Busi messen muss, lassen sich all die erzielten Verbesserungen nicht genau in Zahlen ausdrücken. Was ich aber sagen kann ist, dass der Schritt von den herkömmlicheren Messverfahren zu 5-Achsen KMGs ein großer Erfolg war und dass ich nicht wieder zur alten Situation zurückkehren würde. Genauigkeit ist alles, was in unserem Geschäft zählt, und wir besitzen nun die Technologie, diese zukunftssicher zu liefern.”