Ducati verlässt sich bei der Herstellung von einzigartigen Nockenwellen auf Werkzeugbrucherkennung
Bei Ducati hat man erkannt, dass die Komponentenbearbeitung der Desmodromik-Motoren sorgfältigst kontrolliert werden muss. Innerhalb eines Jahres werden verschiedene Werkzeuge x-mal verwendet, und jedes Mal besteht das Risiko, dass ein beschädigtes oder gebrochenes Werkzeug aus dem Magazin entnommen wird, was zu großen Problemen führen würde. Dank Renishaws berührungslosem Laser-Werkzeugkontrollsystem gehört dieses Problem der Vergangenheit an.
Die wichtigste Phase der Ducati Desmodromik Nockenwellenherstellung wird auf zwei Stama Bearbeitungszentren durchgeführt. Die Maschinen arbeiten ohne Unterbrechung das ganze Jahr hindurch und produzieren Nockenwellen für alle Ducati Motoren.
Fulvio Abbondi, Spezialist für Fertigungstechnik bei Ducati Motor: “Bei der Herstellung dieser Nockenwellen ist höchste Präzision gefordert. Der ziemlich aufwändige Bearbeitungsvorgang wird vollständig in unserem Betrieb durchgeführt. Hierbei handelt es sich um ein sehr teures Bauteil, welches aus einer speziellen Stahllegierung gefertigt wird, und schon vor der Bearbeitung auf der Werkzeugmaschine, nach dem Vordrehen, einen stolzen Preis hat“.
Ein Werkzeugbruch bei der Nockenwellenherstellung hätte deshalb schwerwiegende Folgen, und könnte z.B. zu Ausschuss, kostspieliger Nacharbeit und Zeitverschwendung führen. Außerdem könnten Beschädigungen an der Maschinenspindel verursacht werden, die sich, zusammengerechnet mit den Spezialwerkzeugen, auf mehrere tausend Euro belaufen würden.
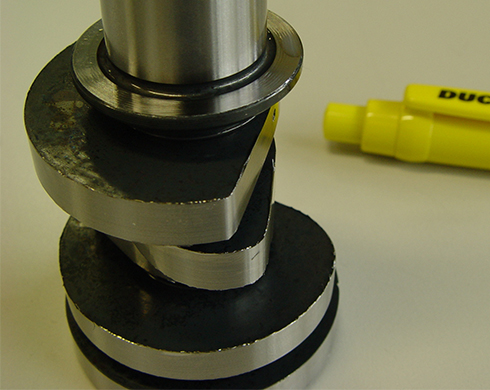
Unter Kontrolle
Abbondi über die Funktion der Werkzeugbruchkontrolle: „Es ist äußerst wichtig, die Fertigung auf der Maschine zu kontrollieren. Ein System kontrolliert das Werkzeug sofort nach der Aufnahme in der Spindel, d.h. kurz vor der eigentlichen Bearbeitung. Hierfür wird das Werkzeug in einer festgelegten Höhe in den Laserstrahl verfahren. Ist die Spitze beschädigt, und das Werkzeug ist z.B. nur noch 97 mm anstatt 100 mm lang, dann löst das Laserwerkzeugkontroll-System einen Alarm aus. Jedes Werkzeug hat natürlich seine eigene Länge, eigenen Durchmesser etc. Das System berücksichtigt dies sobald ein Werkzeug durch den Laserstrahl fährt“.
Er erklärt weiter: „Das NC4 ermöglicht es uns außerdem, kleine Werkzeuge, die wir zur Herstellung von Nuten und anderen Referenzpunkten an der Nocke verwenden und die für die Motorenfunktion unerlässlich sind, auf Bruch zu überprüfen. Ohne das Laserwerkzeugkontroll-System von Renishaw könnte die Maschine z. B. mit einer beschädigten Schneide arbeiten, was katastrophale Folgen hätte. Außerdem kann ein Maschinenbediener ohne Probleme beide Maschinen bedienen, da die Werkzeuge automatisch auf Bruch kontrolliert werden; er muss nur die Werkstücke aufspannen und sicherstellen, dass alles reibungslos läuft.“
Die Überwachung des Bearbeitungsprozesses ist entscheidend
Abbondi erklärt: "Zuerst haben wir ein System vom Werkzeugmaschinenhersteller installiert, mit welchem wir den vom Spindelmotor verwendeten Strom überwachen. Dieses System kontrolliert den Abnutzungsgrad der größeren Werkzeuge, die zum Bohren der tiefsten Löcher, bei denen Spannungen während der Bearbeitung sehr deutlich in Erscheinung treten, verwendet werden. Ein Anstieg des Drehmoments bedeutet, dass das Werkzeug verschlissen ist, woraufhin ein Alarm ausgelöst wird. Aber wir mussten auch in der Lage sein, schnell und zuverlässig Werkzeugbrüche an kleinsten Werkzeugen, die normalerweise mit herkömmlichen Werkzeugbrucherkennungs-Systemen nicht erkannt werden, zu erkennen.
Herkömmliche, nicht berührungslose Erkennungssysteme haben gewisse Schwachstellen und eignen sich üblicherweise nicht für kleine Werkzeuge; das Werkzeug wird gegen einen 'Knopf' oder 'Stab' verfahren und aktiviert so das System. Hierbei besteht außerdem die Gefahr, dass gerade dieser Kontakt das Werkzeug beschädigen könnte. Deshalb kann dieser Arbeitsvorgang nur bei einer niedrigen Drehzahl durchgeführt werden, womit der Prozess verlangsamt und die Zykluszeit um einiges verlängert wird. Das System muss oftmals innerhalb des Arbeitsbereichs installiert werden, wobei es wertvollen Raum in Anspruch nimmt und möglicherweise sogar Kollisionsgefahr verursacht, ganz zu Schweigen von der schlechten Zuverlässigkeit, da sich diese Systeme schnell verklemmen. Deshalb wurde das Laserwerkzeugkontroll-System von Renishaw eingeführt, um diese herkömmlichen Kontrollsysteme zu ersetzen.
Kontrolle mit Licht
Verbesserungen in der Lasertechnologie haben zu der Entwicklung von berührungslosen Brucherkennungssystemen geführt, die in der Lage sind auch kleinere Werkzeuge sicher zu kontrollieren. Ein Laserstrahl verläuft zwischen einem Sender und einem Empfänger, die auf dem Maschinentisch oder auf gegenüberliegenden Seiten davon befestigt sind. Der Laserstrahl befindet sich innerhalb des Arbeitsbereiches. Sobald das Werkzeug in den Strahl eintritt, verringert sich die vom Empfänger erfasste Lichtmenge, wodurch ein Triggerpuls erzeugt wird. Wird keine Verringerung der Lichtmenge festgestellt, löst das System ein Werkzeugbruchsignal aus.
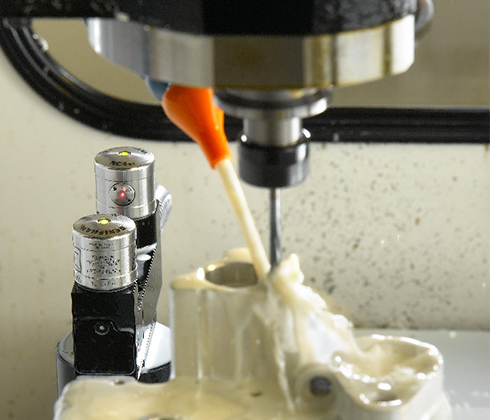
Das Desmodromik-System
Die große Mehrheit der Motorenhersteller verwendet für die Schließung der (Ein- und Auslass-) Ventile in ihren Motoren Ventilfedern, die das Ventil von der Arbeitsstellung wieder in die Ruhestellung bringen. Die einzige Ausnahme ist Ducati, wo man mit einem eher unkonventionellen Desmodromik-System großartig „fährt“. Die Desmodromik-Ventilsteuerung bietet eine bessere Zuverlässigkeit der Motoren bei hoher Geschwindigkeit, da keine Probleme bezüglich der Federträgheit bestehen und die Betriebsreibung um ca. 30% verringert wird. Theoretisch kann der Motor ohne Probleme 20.000 min-1 und mehr erreichen.
Die Desmodromik setzt ein mechanisches System zur Schließung der Ventile ein. Ein Konzept, welches ursprünglich aus Amerika stammt, aber dann wegen der hohen Kosten nicht weiter verfolgt wurde. Der berühmte Hersteller aus Bologna hatte ganz andere Pläne und baute 1972 die Desmodromik-Ventilsteuerung in seine Zweizylinder-Motoren ein. Diese erfolgreiche Technologie wird nun seit Jahrzehnten eingesetzt. Die Ventile werden durch einen speziellen Nocken und nicht mit einer einfachen Feder geschlossen, wodurch eine exakte Verbindung zwischen dem Ventil und seiner Position entsteht. Der Begriff ist übrigens dem Griechischen „desmòs“ abgeleitet und bedeutet soviel wie „Verbindung“.
Das Desmodromik-System erschwert jedoch das Design und die Herstellung einiger Bauteile, wie z.B. der Nockenwelle, erheblich. Die Nocke selber hat nicht die herkömmliche Nockenform, sondern arbeitet mit besonderen „Heberampen“. Diese Form wurde bis ins kleinste Detail von Ducatis Design Team durchdacht, um die benötigte Beschleunigungs- und Geschwindigkeitsleistung zu erreichen. Präzision ist das A und O! Das „Spiel“ zwischen Schaft und Nocke wird von Hand während der Montage eingestellt und ist ein äußerst schwieriger Arbeitsvorgang. Abbondi: „Ein hydraulischer Spielausgleich wie bei Autos ist hier nicht möglich. Wir verwenden je einen Nocken oben und unten, die beide mit höchster Präzision eingestellt werden müssen“.