Generative Fertigung überquert die Ziellinie
Die Formula Student ist Europas bekanntester, studentischer Konstruktionswettbewerb im Motorsport, der bekannte Namen aus der Industrie, erfahrene Konstrukteure, Universitäten und Studierende aus ganz Europa zusammenbringt.
Das Ziel ist, einen Einsitzer zu entwerfen und zu bauen, der auf einer Rennstrecke fährt, die normalerweise der Formel 1 vorbehalten ist. Die Formula Student ist außerdem eine Veranstaltung, die ganz der Innovation gewidmet ist, insbesondere wenn es um neue Fertigungsverfahren und Design Engineering geht.
Für das Rennen der Formula Society of Automotive Engineers (FSAE) des Jahres 2015 entwickelte die Swansea University in enger Zusammenarbeit mit Renishaw, einem weltweit operierenden Engineering-Unternehmen mit einzigartigen Fähigkeiten rund um die generative Fertigung, ein neues Design für den Zwischenkühler ihres Rennwagens. Nach der Entwicklungsphase wurde er auf dem generativen Fertigungssystem AM250 von Renishaw gefertigt.
Die Geschichte der FSAE reicht zurück bis auf das Jahr 1981, ihrem Gründungsdatum in den USA. Im Laufe der Jahre erfreute sich der Wettbewerb bei Wissenschaftlern und Technikern aus der ganzen Welt zunehmender Beliebtheit. Jedes Jahr werden innovative Entwicklungen vorgestellt, die häufig neue Maßstäbe für den traditionellen Motorsport setzen.
Ein Einsatzbereich der generativen Fertigung
Swansea University Race Engineering ist eines der Formula Student-Teams, das diesen Wettbewerb seit 2001 durch Experimente mit neuen Designs und Technologien mit anführt. Das Team besteht aus Maschinenbau-Studierenden unterschiedlicher Disziplinen und Ausbildungsgrade, die Seite an Seite mit Fachleuten des Materials Advanced Characterisation Centre (MACH1) und des an der Swansea University basierten ASTUTE Projekts, das von der walisischen Regierung bzw. von dem Welsh European Funding Office finanziert wurde, zusammenarbeiten.
Das Team der Swansea University konzentriert sich auf die Entwicklung verschiedener Fahrzeugaspekte, einschließlich Aufhängung, Motor, Fahrwerk und Wärmeübertragung. Der Innovationsansatz der Studierenden ist simpel: Wenn Sie ein Fahrzeug zerlegen, jede Komponente optimieren und alle Teile dann wieder zusammenfügen, wird das Ganze besser als die Summe seiner Teile sein.
Eine der Komponenten, die in diesem Jahr eine gründliche Überarbeitung erfuhren, war der Zwischenkühler des Fahrzeugs. Das Ziel war eine Neugestaltung der Komponente, um sie leichter und kompakter als das Vorgängermodell zu machen.
Die Kombination dieser Faktoren sollte eine höhere Fahrzeuggeschwindigkeit ergeben. Um dieses Ziel zu erreichen, orientierte sich das Team an generativen Fertigungsverfahren, insbesondere der Metallpulverbett-Fusionstechnologie.
Für dieses pulverbettbasierte Schmelzverfahren wird ein hochleistungsfähiger Präzisionslaser eingesetzt, der feine metallische Pulver Schicht für Schicht verschmilzt und zu hochkomplexen Funktionsteilen formt. Die Konstruktion der Bauteile wird mithilfe eines rechnergestützen dreidimensionalen Konstruktionsverfahrens (CAD) optimiert. Die Komponenten selbst können aus verschiedensten Metallpulvern gefertigt werden. Sie werden in einer streng kontrollierten Inertgasatmosphäre in Schichtstärken von 20 μm bis 100 μm aufgeschmolzen.
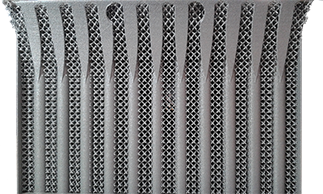
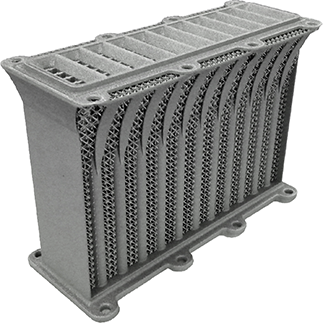
Weshalb ein Zwischenkühler?
Turbolader und Zwischenkühler kommen im Automobilsektor zum Einsatz, um die einem Verbrennungsmotor zugeführte Luft zu verdichten. Dadurch kann pro Hub eine größere Kraftstoffmenge verbrannt werden, während das Verbrennungsluftverhältnis unverändert bleibt. Diese höhere Menge verbrannten Kraftstoffs bewirkt wiederum, dass der Kompressionsdruck im Zylinder steigt und mehr Energie an den Motor abgegeben wird. Im Wesentlichen tragen Turbolader und Zwischenkühler dazu bei, dass Fahrzeuge höhere Geschwindigkeiten als ohne diese Ausstattung erreichen.
Ein Turbolader besteht aus einer Turbine (Turbinenrad und Gehäuse), die an einen Verdichter und an das Abgasrohr des Motors angeschlossen ist. Das heiße Abgas strömt in das Turbinenrad, wodurch dieses sich dreht. Dadurch wird die dem Motor zugeführte Luft verdichtet – es entsteht der sogenannte Ladedruck. Eine unerwünschte Begleiterscheinung bei diesem Luftverdichtungsverfahren ist die höhere Temperatur der in den Motor strömenden Luft. Die heiße Luft nimmt mehr Volumen ein.
An diesem Punkt kommt der Zwischenkühler ins Spiel: Angebracht zwischen dem Verdichterauslass des Turboladers und dem Motoransaugkanal, entnimmt er der Luft die in den Motor strömt die Wärme und gibt sie an die Außenumgebung ab. Die Luft, die in den Motor strömt, wird dadurch noch weiter verdichtet und bewirkt eine höhere Leistungsabgabe.
Ohne Renishaws fortwährende Unterstützung wäre das Projekt nicht so ein Erfolg geworden. Die generative Fertigung ist ein komplexer Prozess. Es ist daher immer hilfreich, sich auf das technische Know-how von Experten zurückgreifen zu können, wenn Probleme zu bewältigen sind. Glücklicherweise war das Renishaw Team telefonisch immer erreichbar und unterstützte uns in der Konstruktions-, Test- und Fertigungsphase.
Swansea University (Großbritannien)
Anforderungen an das Bauteil
Natürlich ist die Einbauposition des Zwischenkühlers von wesentlicher Bedeutung, da er Luft aus der Umgebung ansaugen muss, um die in den Motor strömende Luft abzukühlen. Im Allgemeinen werden Zwischenkühler hinter dem vorderen Kühlergrill des Fahrzeugs angebracht. Aufgrund ihres Gewichts ist dies für einen Rennwagen aber nicht immer die optimale Wahl. Und in der Tat stellte die Einbaulage eine der Herausforderungen für den Formula Student Rennwagen der Swansea University dar. Der Zwischenkühler befindet sich hinter dem Fahrer, über dem Motor – in puncto Wärmeabgabe keine optimale Position.
Der neue hochleistungsfähige Wärmetauscher sollte eine ausgezeichnete Wärmeübertragung haben und einen niedrigen Druckverlust im gesamten System garantieren. Dank der größeren Gestaltungsfreiheit, die die generative Fertigung für die Konstruktion von Geometrien bietet, konnte das Team mit mehreren innovativen Designs zur Verbesserung des Luftflusses experimentieren. Interessanterweise ist das aktuelle Projekt – obwohl bereits früher generative Fertigungsverfahren in der Formel 1 eingesetzt wurden – aufgrund der besonderen Größenordnung und Strömungseigenschaften eines Zwischenkühlers einzigartig.
Konstruktionshürden meistern
Die größten Hürden, die für das Projekt zu nehmen waren, betrafen Konstruktion, Werkstoffe und Software. Das Team hatte die Zielsetzung, einen Ladedruck hoher Dichte für den Motor sicherzustellen und gleichzeitig einen guten Luftmassendurchsatz zu wahren. Dieser Zwischenkühler sollte außerdem so leicht wie möglich sein, um die Beschleunigung zu verbessern.
„Das Design hatte entscheidenden Einfluss auf das Endprodukt, mehr noch sogar als der Werkstoff, etwas, womit wir ursprünglich nicht gerechnet hatten“, erklärt Dr. Nicholas Lavery, Leiter des Materials Advanced Characterisation Centre (MACH1) der Swansea University. „Auch wenn sich unsere Studierenden immer wieder ans Zeichenbrett setzen mussten, waren sie mit dem Endergebnis äußerst zufrieden. Interessant wird es auch, wenn unerwartete Ergebnisse eintreten; das bedeutet entweder, dass irgendetwas mit Ihren Berechnungen nicht stimmt oder Sie einer wichtigen Sache auf der Spur sind. Zum Glück war bei uns letzteres der Fall!”
Um die beste Alternative herauszufinden, testeten die Studierenden die vier wahrscheinlichsten Zwischenkühlerkonstruktionen (Kerndesigns). Die Konstruktionsgrundsätze und Fähigkeiten der verschiedenen Fertigungsverfahren wurden in den verschiedenen Durchläufen widergespiegelt. Das erste Kerndesign, das als Referenz verwendet wurde, war ein herkömmlich gefertigter Kern aus AlSi10Mg Aluminiumlegierung mit einer einfachen vertikalen Konstruktion auf der Umgebungsluftseite und einer Sinuswellenform auf der Ladedruckseite.
Die zweite Form wurde aus 316L Edelstahl mittels pulverbettbasiertem Schmelzverfahren hergestellt. Dieses Design war mit dem ersten identisch, wurde aber verwendet, um zu prüfen, wie die mit dem generativen Fertigungsverfahren geschaffene höhere Oberflächenrauheit auf die Wärmeübertragung und den Druckverlust wirkte.
Die wirklichen Vorteile der generativen Fertigung zeigten sich, als die Studierenden anfingen, mit der Gestaltungsfreiheit, die mit dieser Technologie einhergeht, zu experimentieren. Der dritte Zwischenkühler-Kern hatte eine Gitterstruktur aus dreidimensionalen Sternen, die ein Netz bilden – ein Design, das nur mit generativen Fertigungssystemen möglich wurde. Die Gitterstruktur wurde mit einer Software für generative Fertigungssysteme generiert und obwohl einige Probeläufe erforderlich waren wusste das Team, das sie mit diesem Produkt auf Erfolgskurs waren.
Der vierte und letzte Kern verwendete dieselbe sternförmige Gitterstruktur, die in dem Netzkern zum Einsatz kam. Der Querschnitt der Streben wurde hier jedoch verkleinert, was bedeutete, dass das Oberflächenvolumen und die Dichte sich erhöhten.
Trotz der Überlegenheit dieses Verfahren gegenüber dem Gießverfahren war die Oberflächenbeschaffenheit nicht so glatt wie die der maschinell hergestellten Oberfläche. Die Tests ergaben aber, dass die generativ gefertigten Zwischenkühler mit der höheren Oberflächenrauigkeit besser abschnitten als ihre konventionell gefertigten Pendants.
Dieses Ergebnis, entgegen aller Erwartungen, könnte auf ein besseres Luftgemisch, geänderte Strömungsbedingungen oder eine Kombination daraus zurückzuführen sein. Ein gutes Beispiel ist die Hautoberfläche eines Hais, die zwar rau, aber sehr effizient ist. Erst vor kurzem ist die Bionik, das Untersuchen und Übertragen von Phänomenen der Natur auf die Technik, zum Thema geworden. Generative Fertigungsverfahren könnten bei der Entwicklung und Erforschung neuartiger Formen eine Rolle spielen.
Material- und Softwareprobleme meistern
Nachdem die Studierenden das effizienteste Design gefunden hatten, rückte die Frage ins Rampenlicht, welches Material am Besten sei. Ursprünglich versuchten sie es mit Titan Ti6Al4V, das im Vergleich zu Stahl leichter ist, aber eine geringere Wärmeleitfähigkeit besitzt.
In diesem Stadium schaltete sich Renishaw ein und bot an, das Teil aus der Aluminiumlegierung AISi10Mg anzufertigen, einem Material, das aufgrund seiner hohen Wärmeleitfähigkeit und seines geringen Gewichts ideal wäre. Renishaw fertigte den Zwischenkühler anhand der studentischen Zeichnungen an.
Aufgrund ihres großen Datenvolumens war die Handhabung der Zeichnungen eigentlich einer der komplexesten Aspekte des Projekts. Jedoch nur mit den CAD-Funktionen konnten die Gitterstrukturen so angeordnet werden, dass der maximale Wärmewirkungsgrad erzielt wurde, der die Leistungsfähigkeit des Zwischenkühlers steigerte.
„Ohne Renishaws fortwährende Unterstützung wäre dieses Projekt nicht so ein Erfolg geworden“, fügt Lavery hinzu. „Die generative Fertigung ist ein komplexer Prozess. Es ist daher immer hilfreich, sich an einen Experten wenden zu können, wenn Hindernisse zu bewältigen sind. Glücklicherweise war das Renishaw Team telefonisch immer erreichbar und unterstützte uns in der Konstruktions-, Test- und Fertigungsphase.”
„Die Zusammenarbeit mit Renishaw ist eine fantastische Gelegenheit für die Studierenden“, bemerkt Davide Deganello, Berater der Fakultät für das Swansea FS Team. „Dadurch können wir die Verbindungen zwischen der Swansea University, ihren Studierenden und der Industrie stärken.“
Das Projekt zeigt eindeutig die Vorteile und Chancen, die sich aus generativ gefertigten Zwischenkühlern zur Verwendung im Automobilsektor und Motorsport ergeben. Beide Branchen gehen immer mehr dazu über, kleinere Motoren mit Turboladertechnik einzusetzen, da sie den Kohlendioxidausstoß verringern, gleichzeitig aber höhere Leistung bringen.
Tatsächlich hat die Formel 1 unlängst eine der größten Veränderungen ihrer Geschichte erfahren, als 2014 das Reglement von den klassischen Motoren mit 2,4 l Hubraum auf einen Turbomotor mit 1,6 l Hubraum und kleinem Elektromotor für zusätzliche Leistung geändert wurde.
Bekanntermaßen haben die stets neuen Anforderungen an Rennwagen dazu geführt, revolutionäre Neuerungen in der Automobiltechnik, wie „intelligentere“ Reifen, Karbonchassis und Traktionssteuerung, zu initiieren.
Wer kann da nicht sagen, dass generativ gefertigte Teile der Automobilindustrie nicht die nächste große Veränderung bringen?
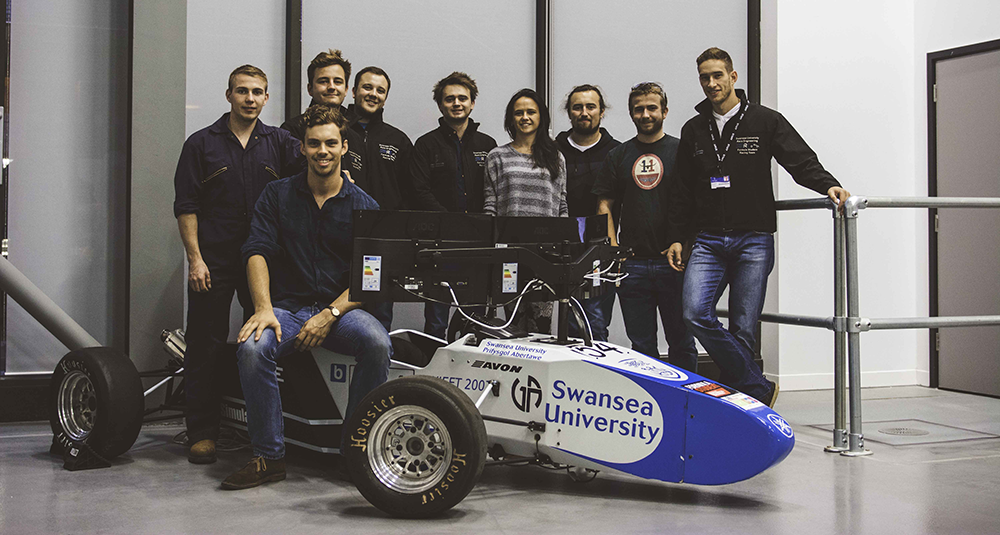