Additive Fertigungsverfahren – Optimiert für Wirbelsäulenimplantate
Renishaw, ein weltweit führendes Engineering Unternehmen, hat in Zusammenarbeit mit zwei innovativen Technologieunternehmen demonstriert, welche Möglichkeiten die metallbasierte additive Fertigung (AM) bietet, und zwar bei der Herstellung leichter Wirbelsäulenimplantate, die die mechanischen Eigenschaften des Knochens imitieren. Im Rahmen dieses Projekts hat IMR (Irish Manufacturing Research), ein Institut für Fertigungsforschung, eine Reihe repräsentativer Wirbelsäulenimplantate entwickelt und gefertigt. IMR hat diese Implantate mithilfe der Software von nTopology konstruiert und sie anschließend mit Renishaws additivem Fertigungssystem auf Metallbasis RenAM 500M angefertigt.
Hintergrund
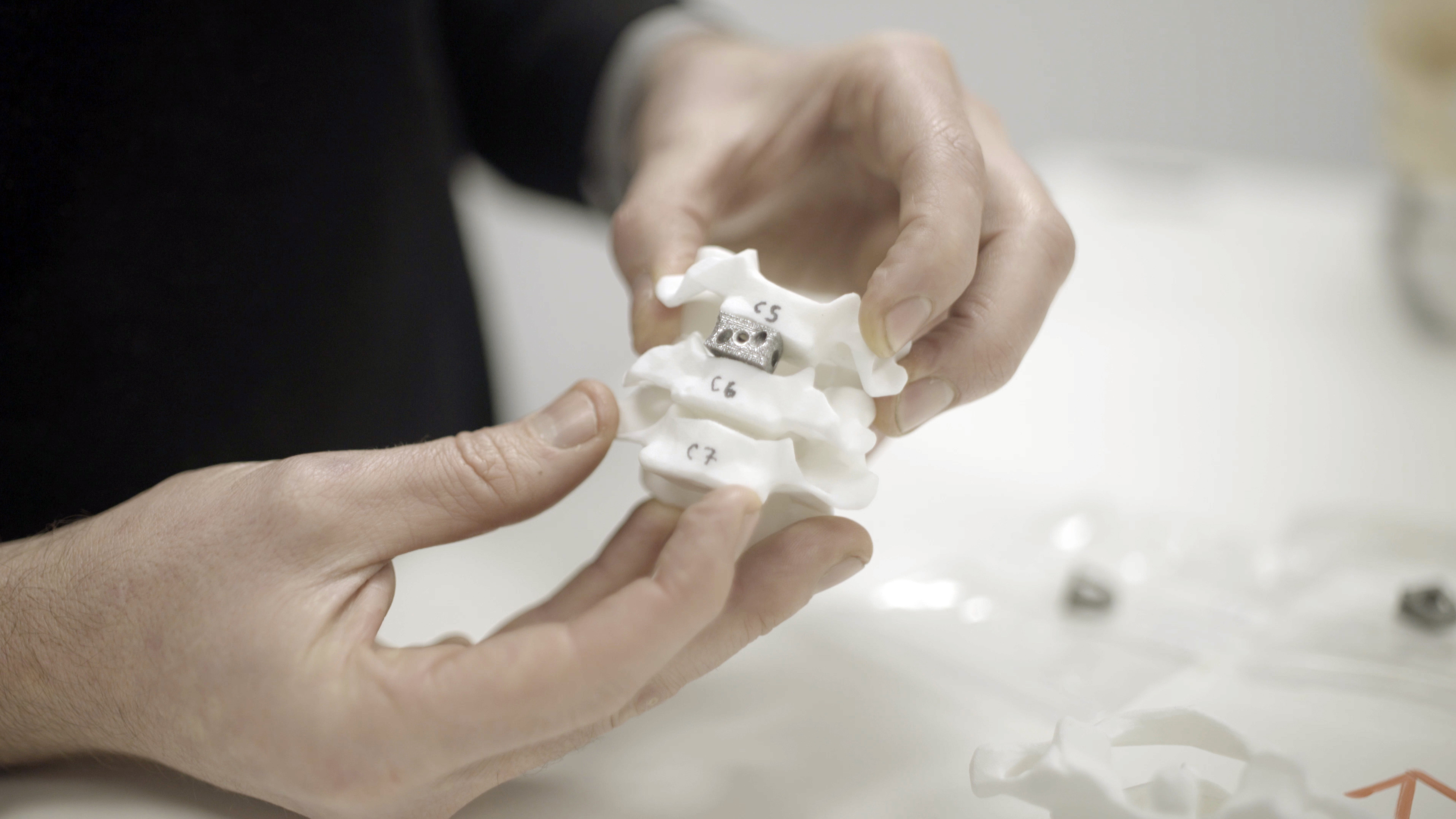
Das in Dublin ansässige IMR Institut bietet irischen Fertigungsunternehmen die Unterstützung, die sie brauchen, um sich auf die nächste Generation der digitalen Fertigung vorzubereiten. Die Medizingeräteherstellung ist ein wichtiger Wirtschaftszweig in Irland und IMR arbeitet mit verschiedenen Unternehmen zusammen, um zu erforschen, welche Möglichkeiten der 3D-Druck für die Medizintechnik eröffnet.
nTopology ist ein marktführendes Unternehmen im Bereich der generativen Konstruktion mit Sitz in New York. Es hat die Design- und Engineeringsoftware der nächsten Generation für die moderne Fertigung entwickelt. Die einzigartige Softwareplattform von nTopology ermöglicht die Erstellung komplexer, leistungsorientierter Konstruktionen, die vollen Nutzen aus den Möglichkeiten der additiven Fertigung ziehen.
Diese fortschrittlichen Designs können in Minuten statt in Stunden oder Tagen entwickelt werden. Die nTopology Plattform ermöglicht die Integration von Konstruktionsabläufen, Fertigungsprozessen und Informationen in der Software. Anwender können daher individuelle Arbeitsabläufe erstellen, die genau ihren Anforderungen entsprechen.
Wirbelsäulenimplantate werden benötigt, um die Zwischenwirbelhöhen bei verschiedenen Krankheitsbildern, wie unter anderem Bandscheibendegeneration, Bandscheibenvorfall, Spondylolisthese, Spinalstenose und Osteoporose, wiederherzustellen.
Dank der ganzen Unterstützung, die uns Renishaw während der Entwicklung der Wirbelsäulenimplantate und der Arbeit an anderen Projekten geboten hat, haben wir unsere Mitarbeiter auf den neuesten Wissensstand gebracht und uns gut im AM-Bereich etabliert.
Renishaw arbeitet unermüdlich mit uns daran, den AM-Prozess für die Herstellung von Wirbelsäulenimplantaten zu optimieren. Gemeinsam haben wir eine Reihe von Experimenten entwickelt, durch die wir die besten Parametereinstellungen für das Produkt erreicht haben. Infolgedessen haben wir den erforderlichen Aufwand für die Nachbearbeitung entscheidender Merkmale um das Zehnfache reduziert.
Irish Manufacturing Research (IMR) (Republik Irland)
Das Problem
Herkömmliche Fertigungsverfahren sind nicht in der Lage, Wirbelsäulenimplantate mit einer Gitterstruktur herzustellen, die sowohl eine großzügige Oberflächenstruktur zum Einwachsen der Osteoblasten in das Implantat bietet als auch die Fähigkeit, die mechanischen Eigenschaften eines Porenvolumens zu optimieren, um die benötigten Lastbedingungen zu erfüllen.
IMR hat AM auf Metallbasis als geeignetes Verfahren für die Fertigung von Gitterstrukturen identifiziert, die optimal für die Knocheneinheilung sind. Allerdings galt es auch, die Designsoftware und AM-Maschinen zu finden, die am besten für diesen Einsatzzweck geeignet sind.
„Die Möglichkeiten der AM-Hardware haben sich so schnell entwickelt, dass herkömmliche Konstruktionssysteme nicht mehr Schritt halten können“, erklärt Duann Scott, Leiter des Bereichs Geschäftsentwicklung und Partnerschaften bei nTopology. „nTopology wurde 2015 gegründet, und zwar auf die Erkenntnis des Gründers hin, dass es keine Software zur Konstruktion der komplexen Formen gab, die man mit AM-Verfahren herstellen konnte.
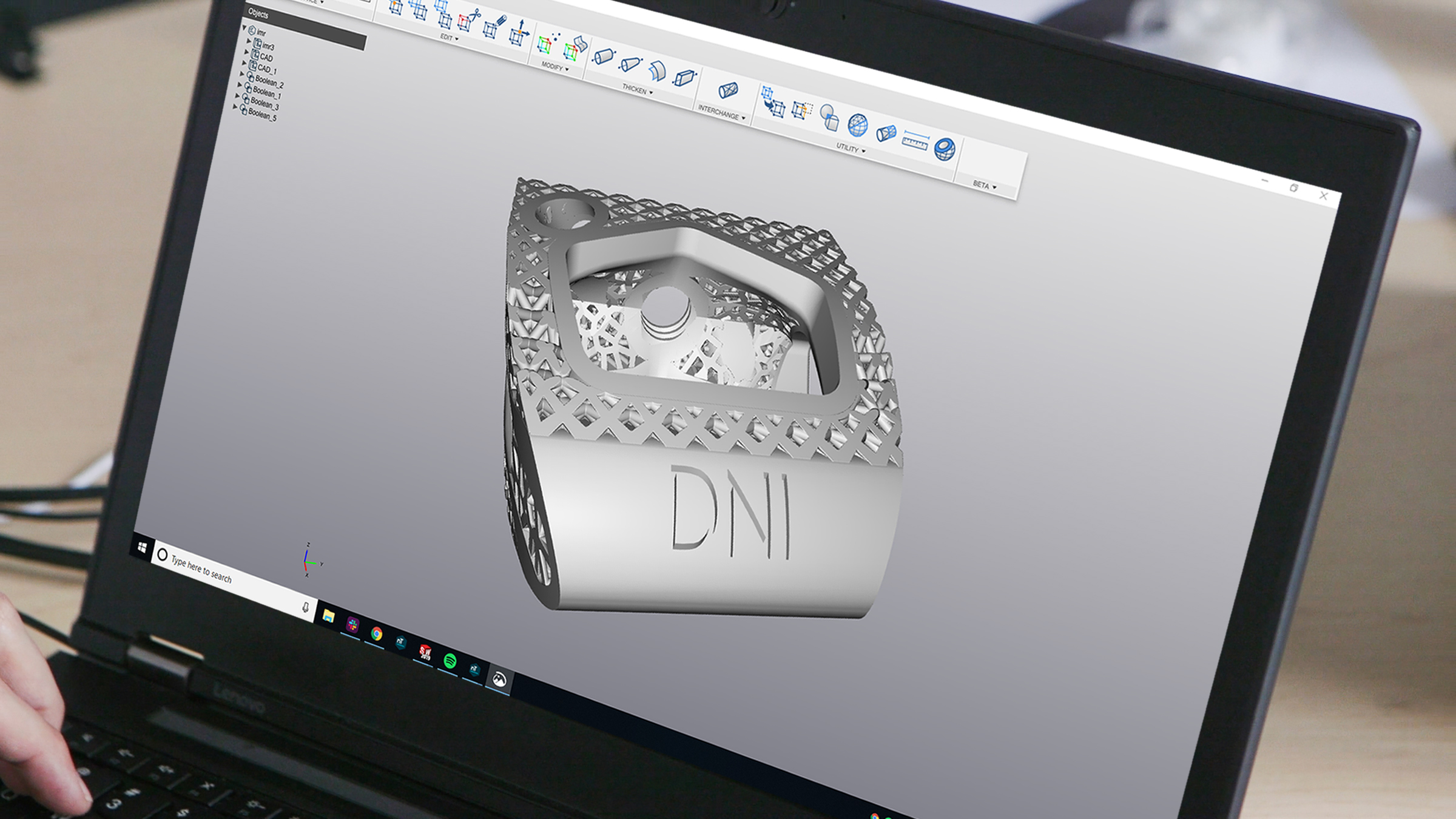
„Um einen nahtlosen AM-Arbeitsablauf von der Konstruktion bis zur Fertigung zu gewährleisten, bedarf es einer effektiven Kommunikation zwischen der Hardware und Designsoftware“, fährt Scott fort. „Ein einfacher Transfer von der Designsoftware zu einem AM-System ist für die Fertigung von Wirbelsäulenimplantaten besonders wichtig, da zwischengelagerte Prozessstufen und die Datenübertragung anfällig für Fehlerquellen und Abweichungen sind.“
Die Lösung
Renishaw, IMR und nTopology haben es mit vereinten Kräften und mittels AM geschafft, Halswirbelsäulen-Implantate mit integrierten Gitterstrukturen herzustellen. Der Projektname für den Implantattyp ist Anterior, Cervical, Interbody Device (Anteriores Halswirbelkörper-Zwischenelement) oder kurz ACID.
Zunächst legte IMR einen Design-Space fest. Dann musste festgestellt werden, welche Möglichkeiten die additive Fertigung bietet, um bessere Ergebnisse für die Patienten zu erzielen. nTopology lieferte dann die Software, die man brauchte, um die komplexe Geometrie der Wirbelsäulenimplantate zu konstruieren. Das RenAM 500M-System von Renishaw wurde für die Herstellung der Implantate im AM-Verfahren verwendet.
IMR führte umfassende Forschungen aus, um die richtigen Proportionen für diesen bestimmten Anwendungsfall und die Lastbedingungen, denen die Implantate jeden Tag standhalten müssen, zu ermitteln. Dabei waren auch Extremsituationen wie Laufen oder Springen zu berücksichtigen. Diese Daten wurden mit den bekannten Eigenschaften von Knochenmaterial bei Patienten mit Krankheiten, die der Erfahrung nach Wirbelsäulenimplantate erforderlich machen würden, kombiniert. Anschließend arbeiteten die drei Unternehmen gemeinsam daran, die mechanischen Eigenschaften des Zwischenelements zu entwickeln, die sich weitgehend aus der Geometrie der in der Gitterstruktur verwendeten Elementarzellen ergeben. Das Ziel bestand darin, mechanische Eigenschaften zu erhalten, die denen des menschlichen Knochens möglichst nahekommen, sowie die zellulare Gitterstruktur für die Knocheneinheilung zu optimieren.
Nachdem die Konstruktionsparameter für die Implantate feststanden, erzeugte IMR die Designdateien unter Verwendung der nTop Plattform. nTopology und Renishaw haben eng zusammengearbeitet, um die Kompatibilität ihrer Produkte sicherzustellen, sodass ein Design nahtlos von der nTop Plattform zum RenAM 500M-System übertragen werden konnte.
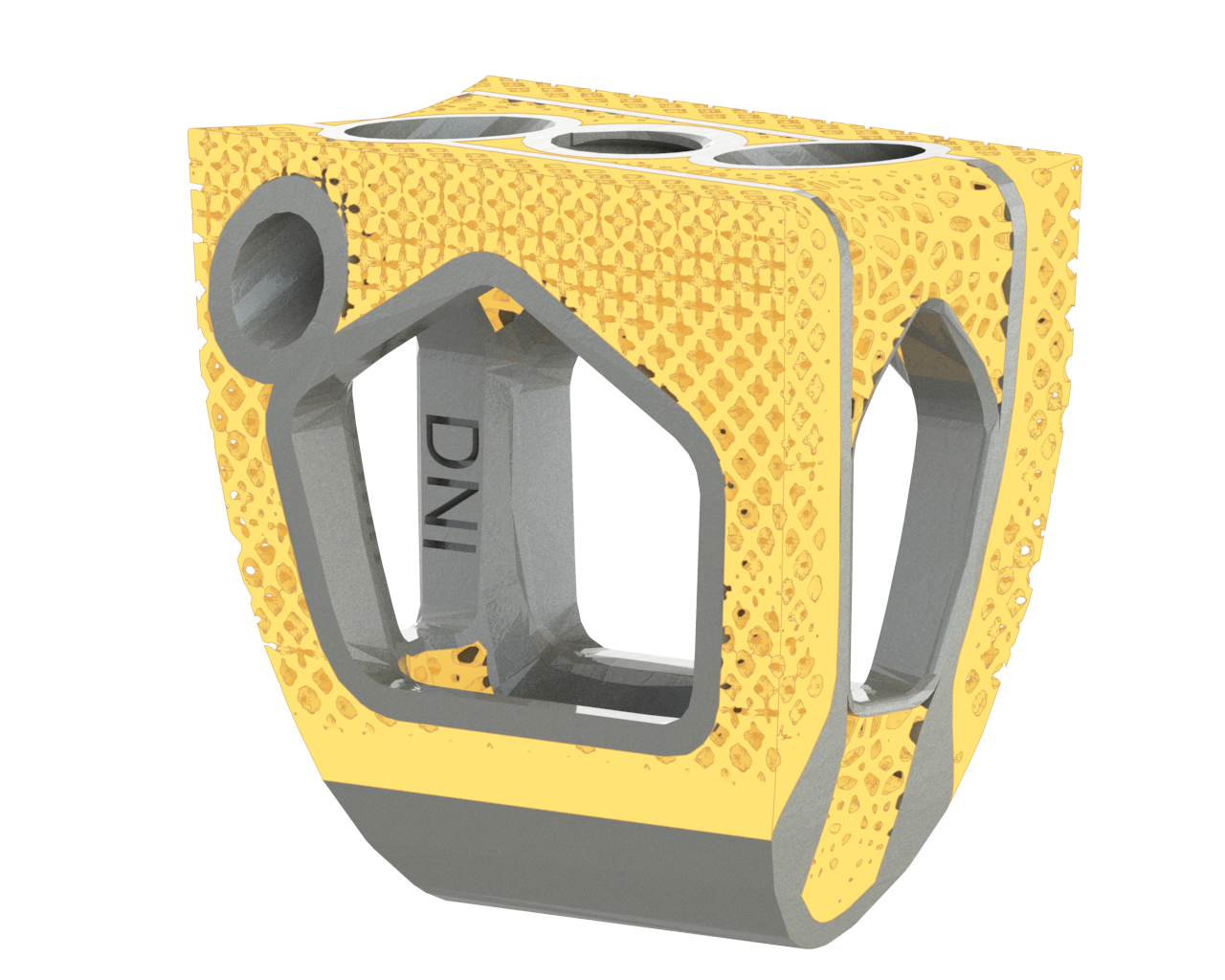
Das Unternehmen führte verschiedene Testreihen durch, um den Nachweis zu führen, dass das Produkt die wichtigsten Anforderungen der Standardspezifikation der US-amerikanischen Zulassungsbehörde für pharmazeutische Produkte FDA (Food and Drug Administration) erfüllte. Die chemischen Eigenschaften kamen auf den Prüfstand, um die Konformität mit den Anforderungen der ASTM F136 Norm, der Standardspezifikation für in orthopädischen Implantaten verwendetes dehn- und schmiedbares Titan „Grade 23“, beziehungsweise der ASTM F3302 Norm, der Standardspezifikation für die additive Herstellung von Titanlegierungen mithilfe des Pulverbettschmelzverfahrens, sicherzustellen. Die Kennzeichnung der mechanischen Eigenschaften der Porenstruktur erfolgte auf Grundlage der ISO 13314 Norm, eines Prüfverfahrens zur Bestimmung der Druckeigenschaften und Leistungsausfälle von metallisch zellularen Werkstoffen. Schließlich sicherten Tests die Konformität mit ASTM 1104 und ASTM 1147, den Standard-Prüfverfahren, die zeigen sollen, dass sich die zellularen Strukturen nicht von den massiven Oberflächen des Produkts abspalten.
„Um die Machbarkeit nachzuweisen, bauten wir Prüflinge auf der RenAM 500M und führten zerstörende Prüfungen daran durch”, erklärt Sean McConnell, Leitender Forschungsingenieur bei IMR. „Wir haben die Tests durchgeführt, um sicherzustellen, dass die Implantate tatsächlich die gewünschten chemischen, metallurgischen und mechanischen Eigenschaften besitzen.“
Ergebnisse
Diese Machbarkeitsstudie hat gezeigt, dass die additive Fertigung geeignet ist, Wirbelsäulenimplantate mit Eigenschaften herzustellen, die mit herkömmlichen Fertigungsverfahren unmöglich zu verwirklichen sind. Das RenAM 500M-System wurde sowohl für die Herstellung der Prototypen als auch der endgültigen Implantate verwendet. Das Verfahren musste daher nicht an unterschiedliche Maschinen angepasst werden. Dieser vereinfachte Prozessablauf wird zu einer erheblichen Zeit- und Kostenersparnis bei Medizingeräteherstellern beitragen.
„Vor zwei Jahren war AM bei IMR gar nicht existent“, erklärt McConnell. „Dank der ganzen Unterstützung, die uns Renishaw während der Entwicklung der Wirbelsäulenimplantate und der Arbeit an anderen Projekten geboten hat, haben wir unsere Mitarbeiter auf den neuesten Wissensstand gebracht und uns gut im AM-Bereich etabliert.
Wir konnten das neue, von Renishaw gewonnene Wissen über additive Fertigungsverfahren an unsere Kunden weitergeben“, fügt McConnell hinzu. „Wir arbeiten nun mit Unternehmen zusammen, die zunächst die Risiken gefürchtet hatten, die mit mangelnden AM-Kenntnissen verbunden sind, nun aber Vertrauen beim Einsatz von AM-Systemen gewinnen.
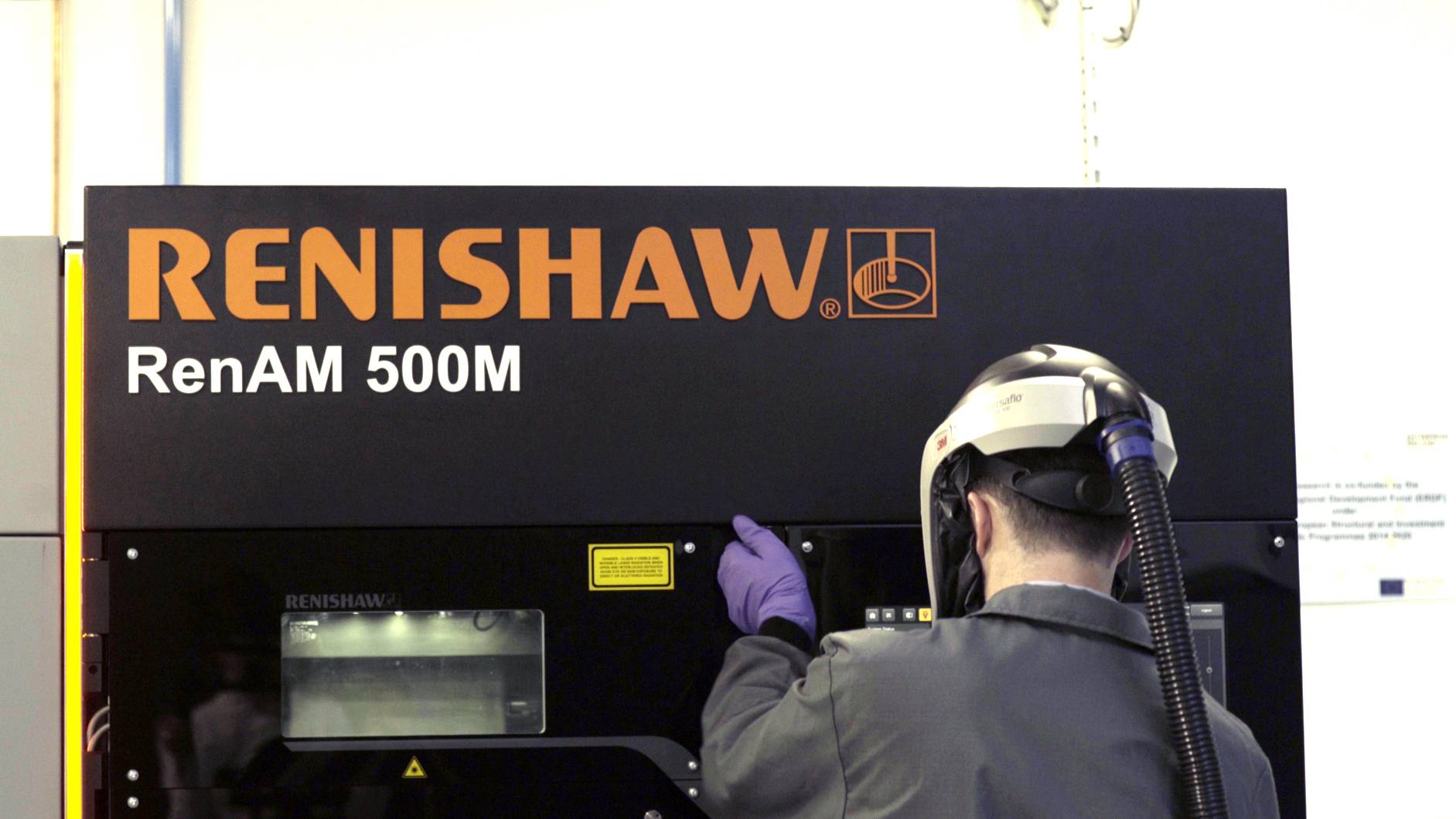
„Renishaw arbeitet unermüdlich mit uns daran, den AM-Prozess für die Herstellung von Wirbelsäulenimplantaten zu optimieren“, fährt McConnell fort. „Gemeinsam haben wir eine Reihe von Experimenten entwickelt, durch die wir die besten Parametereinstellungen für das Produkt erzielt haben. Wir konnten den erforderlichen Aufwand für die Nachbearbeitung entscheidender Merkmale daher um das Zehnfache reduzieren.”
„IMR ist maßgeblich daran beteiligt, die irische Industrie mit modernster Fertigungstechnik auszustatten“, erklärt Ed Littlewood, Marketing Manager des Geschäftsbereichs „Medizinische und zahnmedizinische Produkte“ bei Renishaw. „Die Konstruktionserfahrung und Forschungsintensität des Unternehmens ermöglichten die Herstellung repräsentativer Wirbelsäulenimplantate, die das Wandlungspotenzial der additiven Fertigung im Gesundheitswesen verdeutlichen.“
Ebenso, wie diese Studie gezeigt hat, dass mittels additiver Fertigung Wirbelsäulenimplantate hergestellt werden können, demonstriert sie, dass es durch Einbeziehung des „Designs for additive manufacturing“ (DfAM), d. h. generativer Konstruktionsverfahren, in den frühen Prozessstufen möglich ist, vermehrt auf Stützkonstruktionen zu verzichten und die Endbearbeitung zu reduzieren.
„Dank des Wirbelsäulenimplantat-Projekts haben wir ein Verständnis für die Medizingeräteherstellung und Möglichkeiten von AM-Systemen gewonnen“, erklärt Scott. „Auf dieser Grundlage konnten wir unsere Designsoftware so entwickeln, dass sie zum treibenden Faktor für den Einsatz modernster Technik in der Medizingeräteherstellung wurde.
Wir haben viel ausprobiert und aus Fehlern gelernt, bis wir die Software auf die Anforderungen des RenAM 500M-Systems abgestimmt haben”, fügt Scott hinzu. „Die Techniker von Renishaw haben aber dafür gesorgt, dass der gesamte Prozess reibungslos und effektiv abgelaufen ist. Projekte wie diese dauern normalerweise mehrere Jahre. Der ausgezeichneten Zusammenarbeit zwischen nTopology, Renishaw und IMR ist es jedoch zu verdanken, dass wir diese Studie in nur wenigen Monaten abschließen konnten.
„Wir werden weiterhin eng mit Renishaw zusammenarbeiten, um anderen Unternehmen den Zugang zur AM-Technologie zu eröffnen. Wir möchten eine breitere Zusammenarbeit in der modernen Fertigungsindustrie fördern“, bemerkt Scott abschließend.