Additive Fertigungsanwendungen
Sonderbeiträge
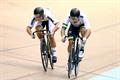
Bastion Advanced Engineering and Design (BAED) hat eine neue und innovative Produktpalette vorgestellt, die darauf abzielt, die Leistungs- und Wettbwerbsfähigkeit von Profisportlern auf der Radrennbahn weiter zu optimieren.
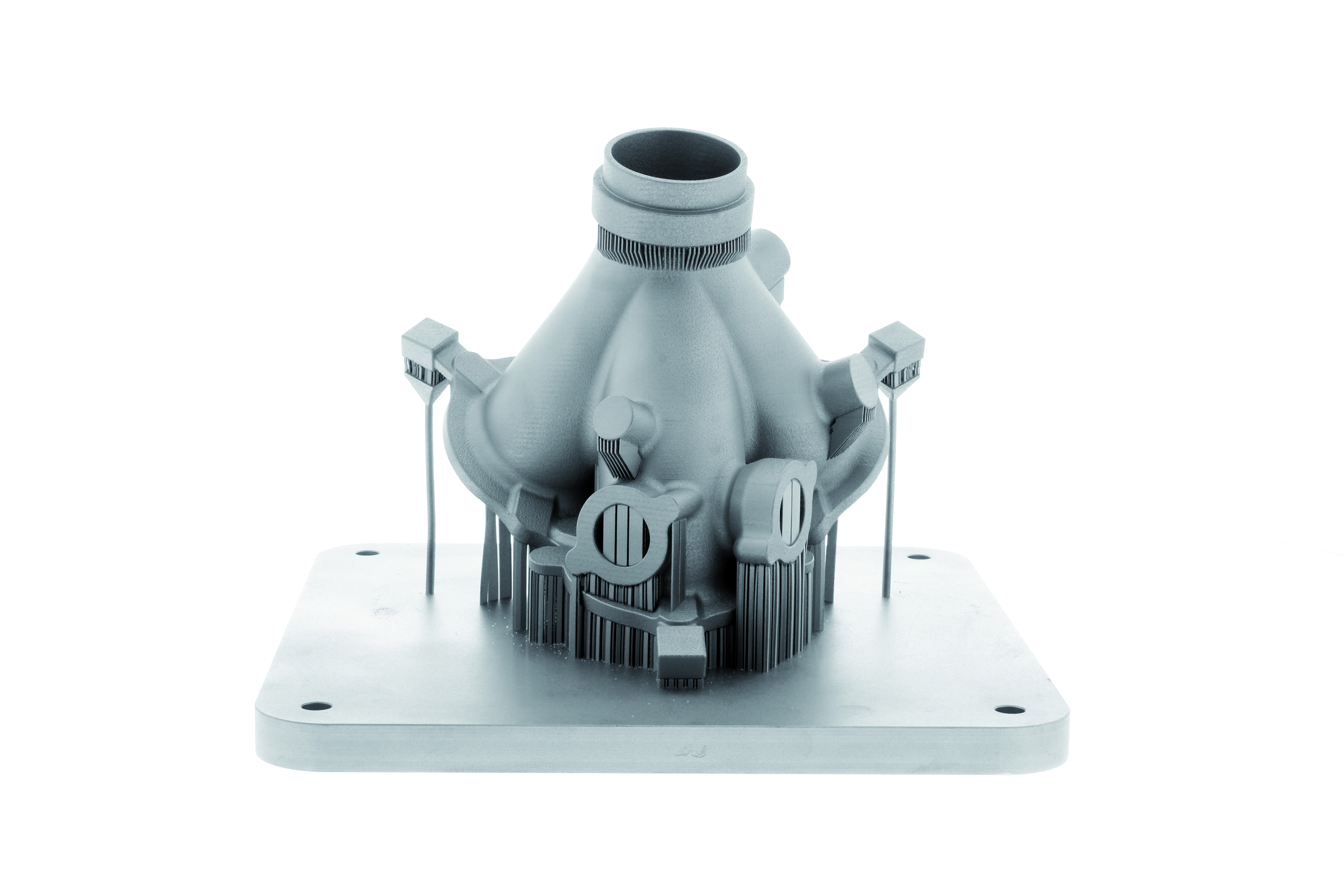
Die additive Fertigung auf Metallbasis wird schnell zur Technologie der Zukunft, aber nur wenige wissen, wie viele Möglichkeiten sie wirklich bietet, und wie sich die Partnerschaft – in dieser Branche – zwischen Renishaw und der Ferrari-Schmiede gestaltet.
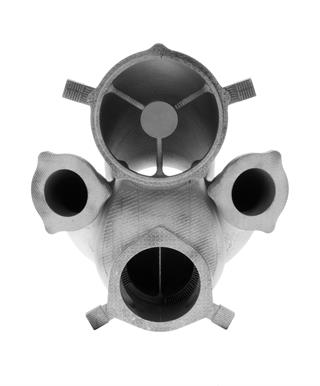
Ferrari ist eine Legende, die beliebteste italienische Marke der Welt, und im Zentrum dieses Mythos, der Rennsportabteilung, stehen zwei additive Fertigungssysteme von Renishaw.
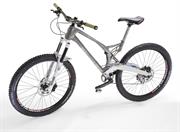
In den letzten Jahren ist die Nachfrage nach technisch hochentwickelten Fahrrädern explodiert, da sowohl Radprofis als auch „Prosumenten“ Leistungsvorteile anstrebten. Im Falle von Mountainbikes hat dies die Hersteller dazu veranlasst, modernste Werkstoffe und Konstruktionsverfahren aus der Luft- und Raumfahrt und Formel 1 einzusetzen.
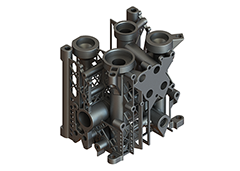
Renishaw unterstützte einen Kunden dabei, seinen hydraulischen Verteilerblock für die Anwendung mit additiven Fertigungsverfahren (AM-Konzept) neu zu gestalten. Das Hauptziel des Projektes bestand darin, die Masse der Komponente zu verringern, aber gleichzeitig ihre Robustheit zu wahren. Aufgrund der höheren Gestaltungsfreiheit des additiven Fertigungsverfahrens wurde außerdem eine Chance erkannt, den Wirkungsgrad der Durchflusswege zu erhöhen.

AM gibt Formenentwicklern die Freiheit, Werkzeuge mit komplexen internen Kühlkanälen zu gestalten. Sie lassen sich für eine optimierte Wärmeübertragung auslegen, die für eine schnelle, gleichmäßige Kühlwirkung sorgt. Das Ergebnis sind Einsparungen bei den Fertigungskosten durch kürzere Zykluszeiten, Reduzierung von Ausschuss und eine längere Lebensdauer der Formen sowie eine bessere Produktqualität.
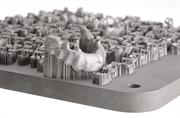
Zu oft geht es bei der „Konstruktion für AM-Konzepte“ darum, Methoden zur Herstellung von Produkten zu finden, die ganz und gar nicht für die additive Fertigung konzipiert wurden. Das heißt, häufig müssen einem Bauteil Stützkörper hinzugefügt werden, um einen erfolgreichen Aufbau zu gewährleisten. Stattdessen könnte der Einsatz von Stützkörpern vermieden oder reduziert werden, wenn die Bedingungen des AM-Prozesses bereits in der Anfangsphase des Bauteildesigns Berücksichtigung fänden. Macht man sich bereits im Vorfeld Gedanken, verbessern sich die Qualität und Beständigkeit des Teils. Es ist im Rahmen des Designprozesses vollständig unter Kontrolle, und nicht erst nachträglich.
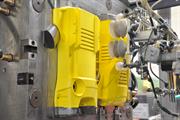
Spritzgussverfahren ermöglichen die Fertigung von komplexen, komplizierten Formteilen aus Kunststoff, häufig in größeren Produktionsläufen. In diesem Artikel untersuche ich, wie diese Techniken von der Alfred Kärcher GmbH & Co., dem weltweit führenden Anbieter von Reinigungssystemen, eingesetzt wurden, um die Produktion eines ihrer am besten verkäuflichen Hochdruckreiniger zu steigern.
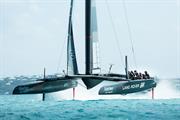
Land Rover BAR hat verstanden, welches Potenzial die additive Fertigung bietet, um Gewicht zu sparen und die Effizienz seines Hydrauliksystem zu optimieren. Einfach gesagt, wurde es den Bootsbauern damit möglich, eine perfekte Balance zwischen der Leistungsfähigkeit ihres Hydrauliksystems und der Energie, die für seinen Betrieb benötigt wird, herzustellen. Dies wiederum hilft der hart arbeitenden Besatzung, die das Hydrauliksystem bedient, Energie zu sparen und gleichzeitig die optimale Leistung aus dem Boot herauszuholen.